Consultancy services
Do you use tried-and-tested methods for identifying production bottlenecks? And what's your team's approach to unblocking them? How does digitalization affect the way you carry out changes and improvements?
Whether you're mostly digital or halfway there — you are in charge of realizing your full potential. And that's where we can help.
Lean manufacturing consultancy services
The consultancy process
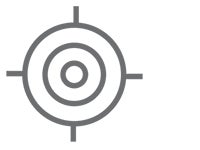
Identify pain points
It starts with identifying your pain points, e.g. productivity, long set-up times or lack of transparency in production.
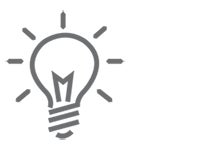
Choose way of working
We evaluate your needs and select a proven method to support you in reaching your targets.
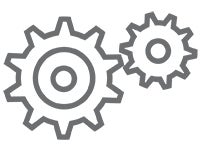
Perform analysis
In-depth analysis of your shopfloor or organization, together with workshops and meetings result in actions for improvement.
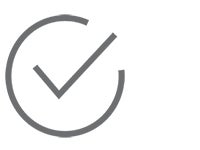
Implement improvements
Our services cover the implementation phases, where results are being realized. Standardization is key for staying ahead in the long-run.
Take the first step!
If you are interested in becoming better tomorrow than you are today or have questions about our services, please let us know by sending a message to one of our Lean Specialists.
Register in less than a minute and unwind with a 50-minute learning session on important KPIs and ways of working in the world’s largest insert manufacturing plant. Sandvik Coromant uses Lean principles to constantly drive productivity improvements, so this summary is a great way to understand how we approach change.
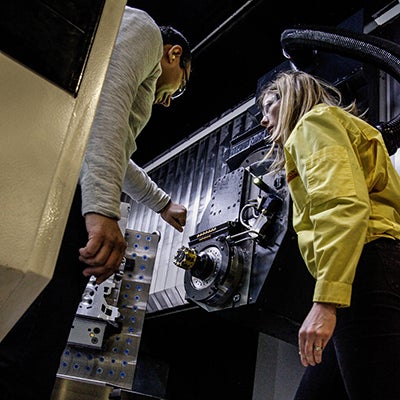
Find bottlenecks
Lean assessment project analyses your product value chain from start to finish. What are the core problems that hold back your productivity – producing bad parts, utilizing poor layout, need to rework, machine downtime, instable production, or bad planning? Our Account Manager and Lean Specialist will conduct a bottleneck analysis at your location and investigate your production organization, set-up processes, teamwork, and other topics with you. With an in-depth understanding of your issues, the next informed steps can be taken.
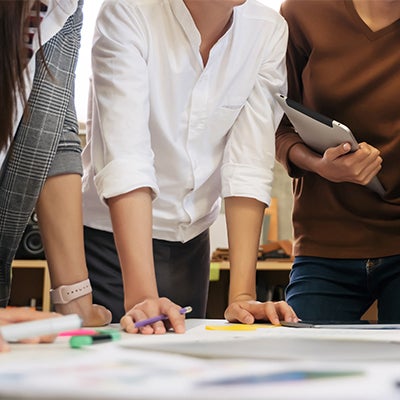
Establish changes
Lean methodology aims to optimize your organization’s energy and resources to increase productivity and generate more value for your customer. The Improvement implementation workshops facilitated by Sandvik Coromant are two different ways of achieving this:
- The SMED workshop follows a proven way of working where key people from your production work together to simplify and streamline a process to reduce waste. The name SMED – Single Minute Exchange of Die – indicates the ambition to diminish the time spent in a changeover.
- The 5S workshop includes teaching the theory of Sort, Set in order, Shine, Standardize and Sustain. The two-day session will generate findings and actions, as well as standards, to sustain productivity improvement.
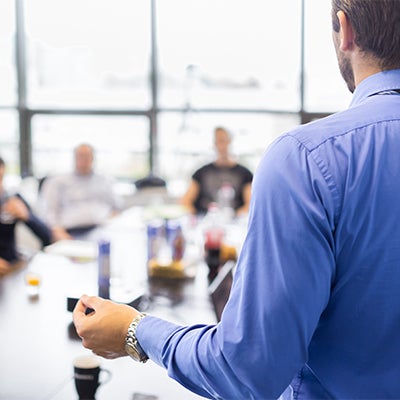
Identify potential
Not everything has to be a huge commitment. The Lean improvement pre-studies aim to get you quickly started on identifying gaps and improvement potential. Expected outcome from the pre-studies includes a solid foundation for evaluating the next steps and clear priorities for your company going forward.
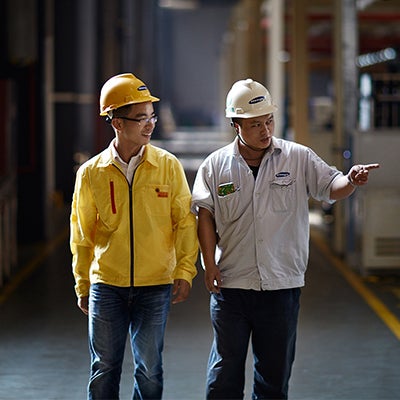
Customized support
A project together with us is a good opportunity to get the full potential out of your production, equipment, and staff. The Consultancy project will contain a combination of activities tailored to deliver the highest degree of output for you, for example:
- 5S workshops and implementation
- SMED workshops and implementation
- Data analysis and sharing best practice
- Kaizen whiteboard design and staff training
- Metal cutting tool optimization including CNC programming, supported by the industry’s top specialists
- Visual management
- Shopfloor Management enablement
- Value stream mapping (VSM)
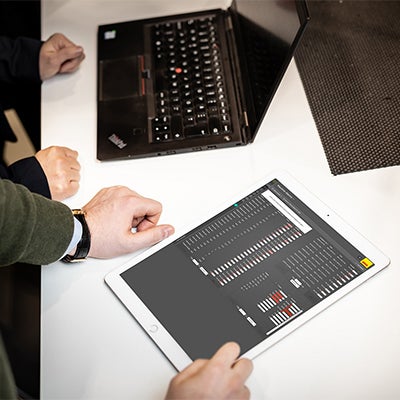
Data-driven machining
Remote machine monitoring is a service that brings productivity increase to your production cell or machine. By finding and then analysing your pain points over a period of time, you will be able to do data-based improvements on key areas of your production. When Sandvik Coromant analyses your machining data, remotely and on-site, we will be able to propose pin-pointed and fact-based improvements for a complete cell down to the very tool. Together we turn data into value, freeing more time for you to focus on your core business.
We start with identifying your pain points, the areas of your production to zoom in on. Then we install machine monitoring solutions to bring insights to your production processes.
With remote access to your processes, we will conduct an in-depth analysis, which we will break down, interpret and discuss during weekly meetings. Together with our combined expertise and observations, we will complete a detailed report catered to your specific situation and requirements.
Then, based on the result from the analysis, we recommend improvement activities to help resolve identified pain points.
In the final stage it is time to implement the improvements. We will monitor the performance continuously, with monthly reports and proactive suggestions to ensure the full realization of your monetary and productivity goals.
References
Ask us about our client consultancy projects.
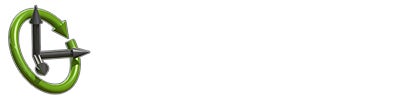
3D TechDraw
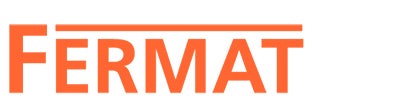
Fermat
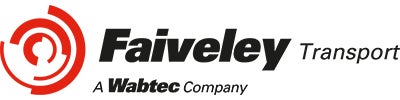
Faiveley Transport

PartnerTech Karlskoga
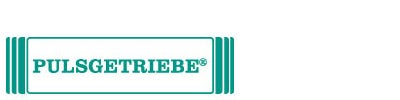
Pulsgetriebe
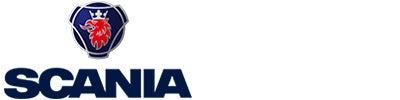
Scania
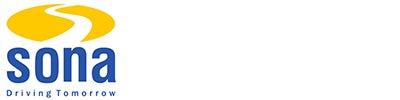
Sona
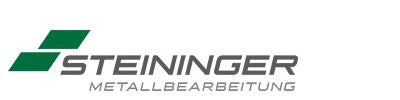
Steininger
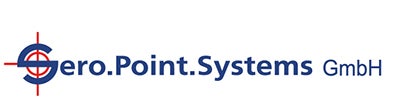
Zero Point Systems
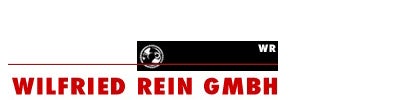
Wilfried Rein
Availability of offer
Sandvik Coromant consultancy services are available in the countries marked with yellow colour in the map below.
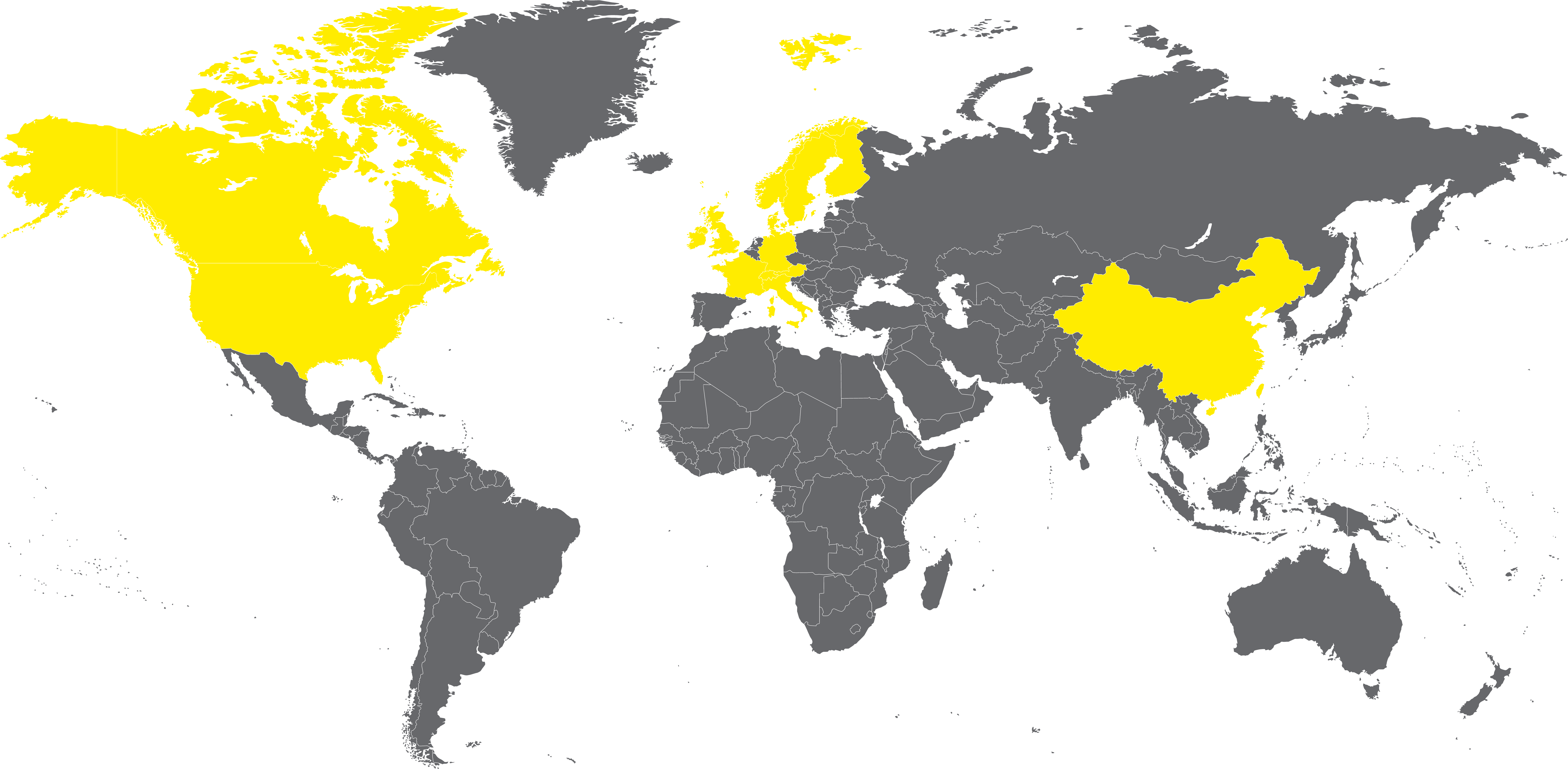