Thread turning tool setup
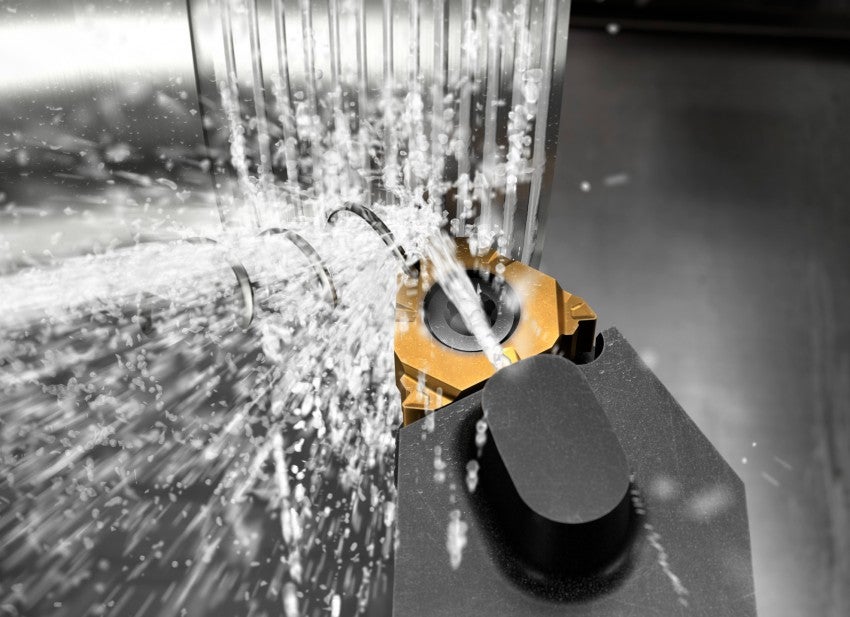
The tool setup has a strong influence on the thread quality and effectiveness of threading. The number one rule is to use as short an overhang as possible.
Upside-down tool holders for external thread turning
In many operations, it is beneficial to use a tool holder in an upside-down position (drop-head holder) to help remove chips more effectively. Drop-head tool holders are specially developed for upside-down thread turning and allow the correct center height to be maintained, without having to change the tool holding in the turret or using a Y-axis.
![]() |
|||
Conventional tool holder | Drop-head tool holder |
Tool holding for internal thread turning
Since the radial forces are much higher than the axial forces when thread turning, the overhang generally needs to be shorter than in general turning operations.
For internal turning operations, this is even more important to consider as the overhangs are usually longer, and especially for internal thread turning, as the higher radial forces increase the risk of tool bend out and vibrations.
The choice of boring bar has a strong influence on the effectiveness of internal threading. Four main types can be used, depending on the overhang length and required level of stability.
Steel boring bars
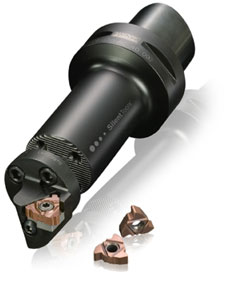
- Maximum 2–3 × bore diameter overhang
- Bar diameter 10–40 mm (0.4–1.5 inch)
Carbide boring bars
- Maximum 5 × bore diameter overhang
- Bar diameter 16 mm (0.63 inch)
Steel damped boring bars (Silent Tools™)
- To be used together with CoroTurn® SL cutting heads
- Maximum 5 × bore diameter overhang
- Bar diameter 40, 50, 60 mm (1.5, 2.0, and 2.4 inch)
- Can also be used for parting and grooving operations
Carbide boring bars
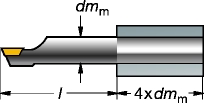
- To be used together with CoroTurn® SL cutting heads
- Maximum 5 × bore diameter overhang
- Bar diameter 16, 20, and 25 mm (0.63, 0.75, and 1.0 inch)
Boring bar deflection is influenced by the boring bar material, diameter (dmm), overhang, and cutting forces. The recommended clamping length in a boring bar holder with a sleeve is 4 × bar diameter.
Maintenance of thread turning tools
Establishing a routine for tool maintenance in the work shop will prevent problems and save money.
Check the insert seat
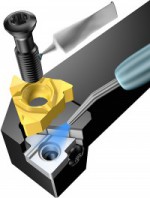
It is important to ensure that the insert seat has not been damaged during machining or handling. Make sure the insert seat is free from dust or metal chips that are produced when machining. If necessary, clean the insert seat with compressed air.
Torque wrench
To get the best performance out of screw-clamp tool holders, a torque wrench should be used to correctly tighten the insert. Use the recommended torque (TQ) for each tool holder.
- Torque that is too high will negatively affect the performance of the tool, and can cause insert and screw breakage
- Torque that is too low will cause insert movement and vibrations, and degrade the cutting result
Clamping screws
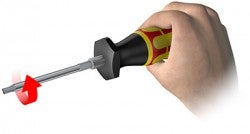
Apply sufficient screw lubrication to prevent the screw from seizing. Lubricant should be applied to the screw thread as well as the screw head face. Replace worn or damaged screws.
Overhang
For an optimal tool setup, use a tool holder with as short an overhang as possible to avoid vibration. We recommend to use a sub-spindle or tailstock for support, if available.
Long overhangs are most common for internal thread turning. When machining with long overhangs, it is especially important to mount the bar correctly to ensure enough clamping contact. Recommended clamping length is 2.5–5 × bar diameter (D), depending on boring bar design. This will result in a stable tool setup.
For best performance of the boring bar, the contact, design, and dimensional tolerance between tool and tool holder are important factors. The best stability is obtained with a holder that completely encases the bar. A V-type bar holder and cylindrical holder with screws are not recommended.
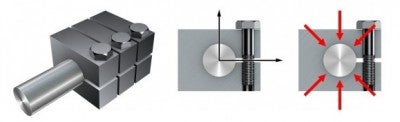
Holder that completely encases the bar

V-type bar holder
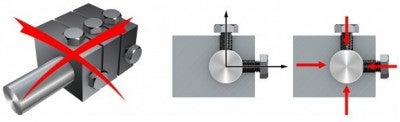
Cylindrical holder with screws
Cylindrical boring bars and adapters can be clamped in split sleeves. Large boring bars and adapters can be clamped using two split bearing caps.
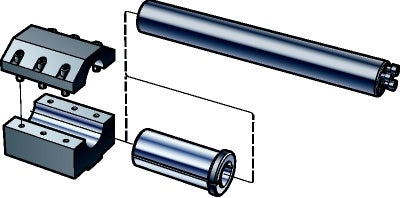
Tool assembled with split sleeve
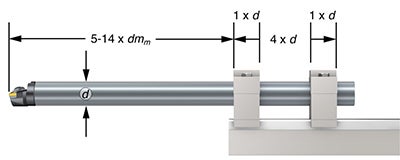
Tool fixed in two split bearing caps
Tool holding
Coromant Capto® is a modular, quick change tooling concept, which, when directly integrated into the spindle, increases stability and versatility in, for example, multi-task machines, machining centers with turning capability, and vertical lathes.
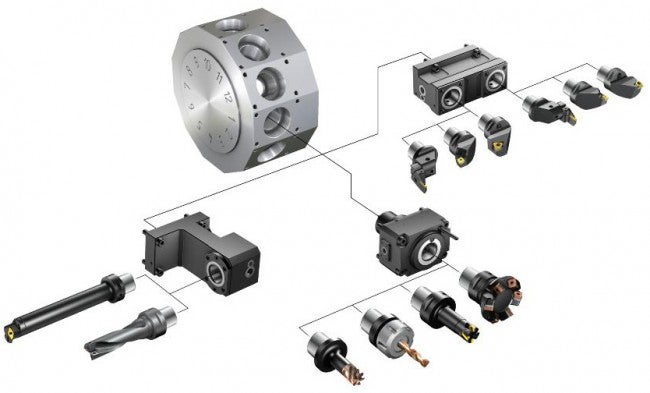
Silent Tools™ adapters are designed to minimize vibration through a dampener inside the tool. The majority of Silent Tools™ customers use these tools for long overhangs. However, even with shorter overhangs (3 × D), large productivity increases and surface quality improvements are to be gained.
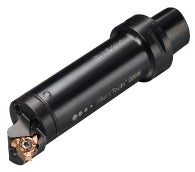
EasyFix™ sleeves are a setup time-reducing solution for cylindrical adapters. A spring plunger mounted in the sleeve clicks into a groove in the bar to guarantee the correct center height. EasyFix™ sleeves are designed for high coolant pressure.
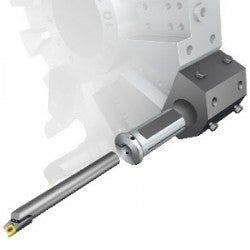
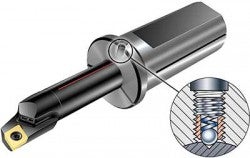
CoroTurn® SL is a modular system of adapters with exchangeable cutting heads that allows you to create a wide range of tool combinations from a small inventory.
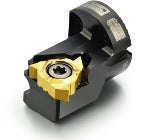
The QS™ holding system is a quick change tool holder to maximize effective production time in sliding head machines.

Tool Setup
Good quality in parting-off and grooving is mainly dependent on the tool system and... keyboard_arrow_right
Tool set-up
Good quality in turning is mainly dependent upon the tool system and how it is used... keyboard_arrow_right
Silent Tools for milling
Many components and machine tools require long tool assemblies to reach down in large... keyboard_arrow_right
Coromant Capto®
Coromant Capto is a modular quick change tooling concept offering three systems in... keyboard_arrow_right