Solutions for cost-effective and high-quality machining of aerospace wings
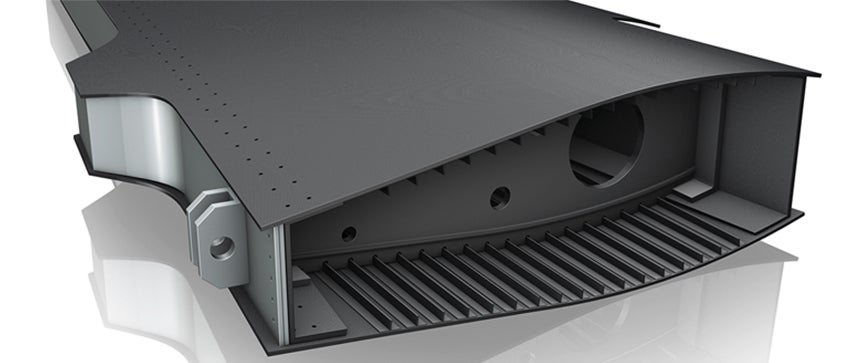
The main challenges for machining these types of structural components are hole making, edging and surface machining.
Tooling solutions for aerospace wings
Composite solutions – product offer for composite machining
Machining solutions dedicated to specific composite materials as well as operations and demands are becoming an increasingly important competitive factor.
More information
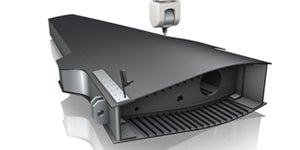
CoroDrill® 863 with -O geometry – solid carbide drills for high-quality hole making and longer tool life in composites
Hole making in CFRP (carbon fiber reinforced polymer composite) – facts and demands
- Minimal delamination of fibers
- Good surface finish and dimensions
- Unidirectional or woven layers
- High rate of material removal
Solutions
- CoroDrill® 863 with -O geometry, standard diameter range 3–9.5 mm (0.118–0.374 inch)
- Drill depth 3–10 × drill diameter
Benefits
- Enhanced tool life – more feet of composite material drilled
- Minimal delamination
- Excellent hole finish and tolerance
Cutting data
- Visit CoroPlus® ToolGuide for precise cutting data suggestions
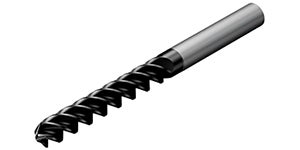
CoroMill® Century – surface machining of carbon fiber
Facts and demands
- Primary structure carbon fiber
- Minimal splintering of fibers and delamination
- Good surface finish and dimensions
Solutions
- CoroMill® Century with PCD inserts
- Cutter: R590-04C3-11M
- Inserts: R590-1105H-PS2-NL CD10
Cutting data
- Visit CoroPlus® ToolGuide for precise cutting data suggestions
Learn more about CoroMill® Century light cutting face mill for high-speed finishing
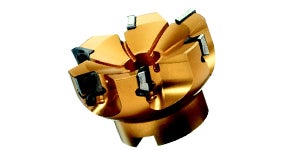
CoroMill® 390 – Sturtz milling: profiling of carbon fiber
Facts and demands
- Tilting of tool 2–10 degrees – high rpm and feed rate
- Primary structure carbon fiber
- Hand-held pneumatic machine design
- 2D and 3D feature solutions
- Good surface finish and dimensions
Solutions
- CoroMill® 390
- Cutter: R390-032A32-11H
- CD10 PCD inserts (3 mm (0.118 inch) modified radii)
Cutting data
- Visit CoroPlus® ToolGuide for precise cutting data suggestions
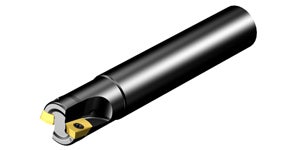
Ball-end scanning vs Sturtz
32 mm (1.260 inch) diameter tools used with the same cutting data.
32 mm ball | 32 mm Sturtz | |
Surface speed, m/min (ft/min) | 2,011 (6598) | 2,011 (6598) |
RPM | 20,000 | 20,000 |
Feed/tooth, mm/min (in/tooth) | 0.12 (0.005) | 0.12 (0.005) |
Table feed, mm/min (in/min) | 12,000 (472.441) | 12,000 (472.441) |
No. of flutes | 5 | 5 |
Step over, mm (in) | 3.52 (0.139) | 11 (0.433) |
Pass/sq meter | 284 | 91 |
Time for 1 sq meter | 23.7 | 7.6 |
Over 3 times faster generation of surface |
Smaller ball-end tools are typically used, resulting in even greater productivity when switching to Sturtz techniques.
Vertical tails
The main challenges for machining these types of structural components are hole making,... chevron_right
Wing ribs
There are several types of aluminum components on an airplane such as spars, skins... chevron_right
Central wing box
The central wing box, made out of several types of composite materials and commonly... chevron_right
Turbine blade
Blade machining moves to a new level Competitive manufacturing blades for steam... chevron_right