How have tools developed to provide advantages?
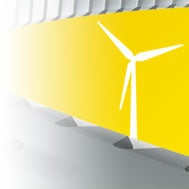
And what does it mean for manufacturing wind power components?
Components for wind power equipment are very varied in size, design, material and what needs to be machined. This means that they stand to gain broadly from the regular developments that are made to cutting tools and machining methods.
Status quo for too many years, not taking advantage of available new concepts that lead to continuous improvements, means a measurable drop in competitiveness. Here are a couple of examples.
The tool material
reliability
The tool material forms the front-line of all cutting tools, affects not only durability and of the process but also the productivity. The cutting data and tool-life possible with an edge, based on wear resistance and strength, determines cycle times, machine stoppages, versatility and in so doing the capacity and delivery capability of the machine shop.
The absolute majority of indexable inserts today are coated, which means that developments in this area have a huge influence on performance. Considerable development of the two main coating processes and materials have been made for grades to complement each other as never before.
New PVD-grades have been introduced where the coating process actually lower any tensile stresses in the material by countering with compressive stresses. This is done through a new high-impact treatment process, resulting in the edge-line of sharper cutting edges being stronger and safer. This, for example, has a huge benefit on endmilling operations where entry and exit to cut is often challenging.
New CVD coatings with less inherent stress and post-coating treatment of inserts have made thicker, more wear resistant inserts possible. This has above all benefitted operations that present a higher risk of breakdown from heat and chemical loads. Coating layers can be made thicker - without sacrificing insert toughness. The result is that inserts can machine at higher cutting speeds and still last longer, with better predictability. This has made rough milling and turning more productive today.
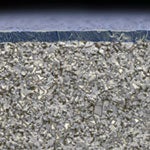
PVD
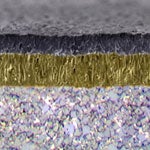
CVD
Toolholding
Toolholding is the link between cutting edge and machine, and a key-factor for high performance and results. This is an area where several developments have taken place as regards interface between insert and toolholder and tool to spindle.
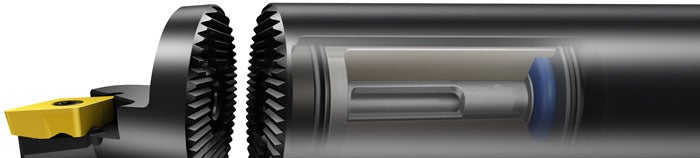
An intermediate area in the actual toolholder, involving minimal exchangeable cutting heads, has revolutionized the availability of tools dedicated and optimized for a large variety of turning operations, especially internal ones. This modularity has been made possible through the development of a new serrated interface (SL) between head and tool adapter.
The development of SL-system has added proven rationality to machining on vertical turning machines, lathes and multi-task machines, where the coupling means access to performing almost any operation with no compromise in performance.