Precision coolant advantages for machining aerospace materials
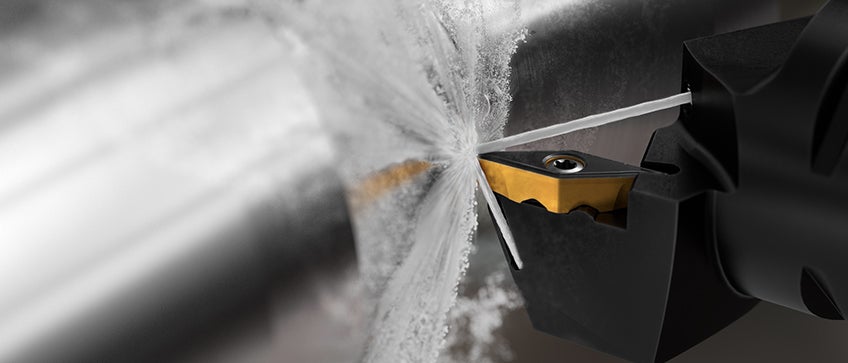
The role of coolants in machining aerospace parts has undergone something of an evolution. For many years, machine shops have used coolants by directing tubes that flood the machining zone, particularly on materials that require coolant to be machined. Nowadays, coolant can be applied with high precision into the machining zone, offering new advantages. Access to this technology has been broadened thanks to the higher coolant supply capacity of many CNC machines, as well as by new tooling concepts.
Making a difference
For coolant to be effective and make a difference, it needs to be applied as high precision jets, in sufficient volume and correctly directed. Simply having a stream of coolant or even flooding the machining zone with coolant is not enough. On the other hand, professional application of high precision coolant can make a distinct difference as regards:
- chip formation,
- heat distribution
- smearing of workpiece material on the cutting edge,
- surface integrity,
- tool wear.
These basic machining factors in turn affect manufacturing in terms of the improvement objectives to achieve higher competitiveness:
- productivity,
- tool life,
- chip control and chip evacuation,
- component quality.
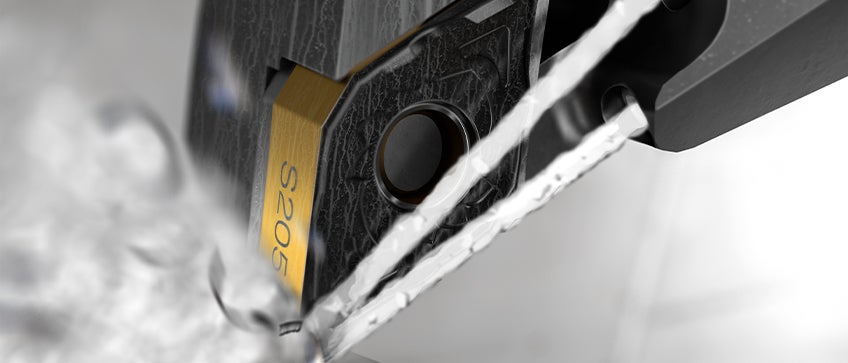
When applied correctly, precision coolant maximizes output, increases process security and improves tool performance and component quality. The positive effects start at low coolant pressure, however more demanding materials can be successfully machined at higher pressures.
The application of precision coolant can make a difference to machining in general, especially for stainless steel and low-carbon steel. But it is when machining more demanding materials, such as heat-resistant super alloys and titanium alloys, that the practice makes a dramatic difference. Significantly, a number of recent developments have made high precision coolant even more interesting and more readily available.
Jetbreak pioneered the concept
During the 1980s and 1990s, Sandvik Coromant developed the first version of Jetbreak, a high pressure coolant system. Research led to the integration of coolant jets precisely directed at ultra-high pressure (100–1000 bar) in cutting tools used to machine materials with high demands on machinability and chip control. The coolant jets forced their way in, forming a fluid wedge between the chip and the cutting edge. The contact length was shortened, with a temperature reduction in the machining zone. Another interesting observation was how the curl of the chip could be influenced, improving the control of the chip and in some cases even leading to chip breakage.
In a number of special tool applications, Jetbreak became the solution for machining materials with poor machinability and/or troublesome chips. A lot was learnt about the effects of coolant-pressure distribution and coolant nozzle size. A variable chip former was achieved by varying the jet data, making it possible to guide stringy chips in a desired direction and even improve the length of chips. Limited installations were undertaken to solve these problems, particularly in the oil, aerospace and ball bearing industries. However, Jetbreak needed a dedicated installation with special tool holders, mainly for use in vertical turning machines.
High precision coolant as standard
The coolant on many modern CNC machines is supplied at a pressure of 70 to 100 bar, either as standard or optionally with suitable tanks and pumps. This is sufficient to incorporate high precision coolant, which makes a noticeable difference to performance and results on more commonly used machining centers, turning centers, vertical lathes and multi-task machines. Standard equipment is sufficient with easy channeling of coolant to where the jet is applied.
Modular tools are essential for high-precision coolant machining, partly to ensure quick tool changes for minimizing machine stoppages, but also to efficiently secure coolant connections and channels from the machine to the cutting edge. The Coromant Capto® modular quick-change tooling system was the basis for the development of Jetbreak, and has become the basis for new standard high-precision coolant tooling. This system is ideal as a modular platform and designed with an internal coolant supply, making it effective for high-precision coolant supply. It is an established ISO standard and optional system on many CNC machines with stationary and rotating tools.
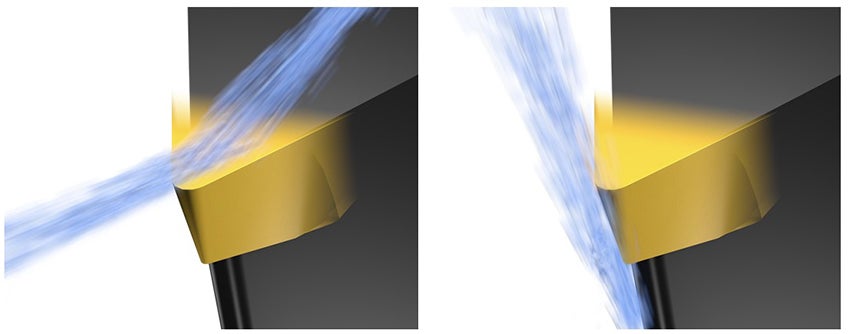
High-precision direction of over coolant towards the cutting zone improves chip control and process security. Under coolant increases tool life and productivity, especially in applications that generate a lot of heat in the insert.
A milling cutter with high-precision through-coolant and equipped with nozzles positioned and directed depending upon the tool type and the intended application. Channels are connected to the machine tool or extra pump equipment to supply coolant at a pressure of around 70 bar. This supply is widely available today, and although the pressure involved is not ultra-high, the scope is certainly sufficient for a marked improvement in performance and results. The concept makes good use of a resource that many machine shops either already have, or can invest in for the future.
Precision coolant for turning
Turning tools with precision coolant are equipped to provide precise coolant jets with laminar parallel flow. The jets create a hydraulic wedge between the insert and the chip, affecting the chip form and flow and reducing the temperature in the machining area. The use of nozzles mounted close to the cutting edge and precisely projecting the high-velocity jets, forces the chip off the insert face and cools and breaks the chips into shorter lengths, helping to evacuate them.
Benefits in finishing operations have been obtained even at lower pressures, down to 10 bar in materials including steel, stainless steel, aluminum, as well as titanium and heat-resistant super alloys. In addition to higher security thanks to better chip control, precision coolant can offer considerable improvements in tool life and potential for higher cutting speeds. Applying precision coolant can increase the tool life by up to 50%.
The cutting speed affects the temperature – and therefore tool wear – more than any other factor. Increasing the cutting speed in titanium outside the more limited machinability window dramatically reduces the tool life. However, when the feed is increased on a similar scale, the typical reduction in tool life is smaller. This often makes the feed an attractive route to an improved metal removal rate, with a low effect on tool life. However, high feed is not always an option in these machines because of higher cutting forces, as well as the effect on chip control.
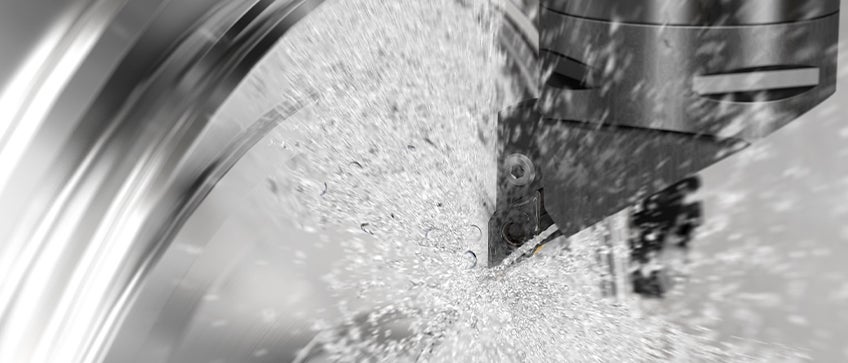
Turning a HRSA turbine disk. Precision coolant can play a vital role in ISO S machining.
The effect of precision coolant can therefore be to boost performance by way of higher cutting speeds, without the usual rise in temperature and reduction in tool life. There is a clear cooling effect, without the higher cutting forces from higher feeds. For ISO S classified materials, a 20% increase in the cutting speed can be achieved while maintaining the same cutting length.
Internal turning is also an area where precision coolant can play an important role in helping to ensure good chip formation, as well as improving shearing properties in demanding materials such as titanium. This means the concept increases security and offers a longer tool life in boring operations. When machining relatively large, deep holes with boring bars, such as on landing gear components, modular tooling at both the front and rear of the tool can be advantageous. The ability to change the small cutting head on the clamped bar means quick, easy and accurate changing, adding considerable flexibility for various cuts in a single set-up. The CoroTurn SL combines damped boring bars with serrated locking of heads for boring larger holes with depths of ten times the diameter, and is also equipped with a precision coolant system.
Variations in the component surface integrity are affected by the temperature and forces generated during machining. Coolant plays an important role in controlling the temperature and, consequently, precision coolant has been shown to provide a more reliable surface result. Tool nozzles are aimed directly at the part of the insert in contact with the finished surface. Since the nozzles are non-adjustable, many of the variables are eliminated, resulting in a more secure and consistent machining process.
Optimization of correctly classified operations
With the ability to force a fluid wedge into the machining area, especially in operations classified as medium to finish turning, the chip thickness is more controllable and the fluid wedge easier to apply than in roughing operations.
The application of high precision coolant machining should not be seen as a way to compensate for shortcomings due to other application factors such as unsuitable inserts, instability, incorrect cutting data, etc. Precision coolant is an optimizer when operations are correctly classified. The concept offers the potential for shorter cycle times, improved component quality consistency and higher process security in turning and milling.
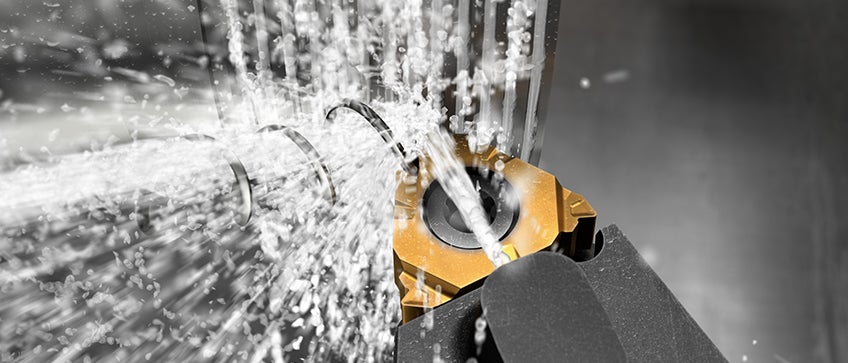
Thread turning with precision coolant.
The need to optimize various machining operations, especially when chip formation and the effects of demanding materials are major factors, make precision coolant an attractive option. The growing number of multi-task machines, along with a new generation of vertical turning machines, has highlighted the benefits of machining with precision coolant, especially in terms of chip control. The disturbance due to chip accumulation is critical, as these machines are increasingly used by machine shops producing aerospace components in demanding materials.