Our moments
Being part of the Mont Blanc tunnel excavation, setting up grinding stations and setting a world record—it’s all these moments, big and small, short and long, that make up the history of a company. Here are a few of ours.
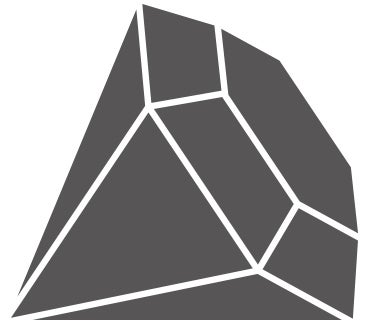
In the late 1930s, cemented carbide became scarce in Sweden. Production Manager Carl Sebardt took the initiative to collaborate with the Swedish Cooperative Association’s Luma factory, which, at that time, was manufacturing cemented carbide for military use.
In 1942, Sandvik and Luma signed a 10-year agreement that more or less transferred the exclusive rights of processing cemented carbide for civilian production from Luma to Sandvik.
Sebardt later chose to name the carbide Coromant; a combination of the words “diamant,” which is the Swedish word for “diamond,” and “corona,” which, at that time, was the name of Sandvik’s high-speed steel. And the rest is history!
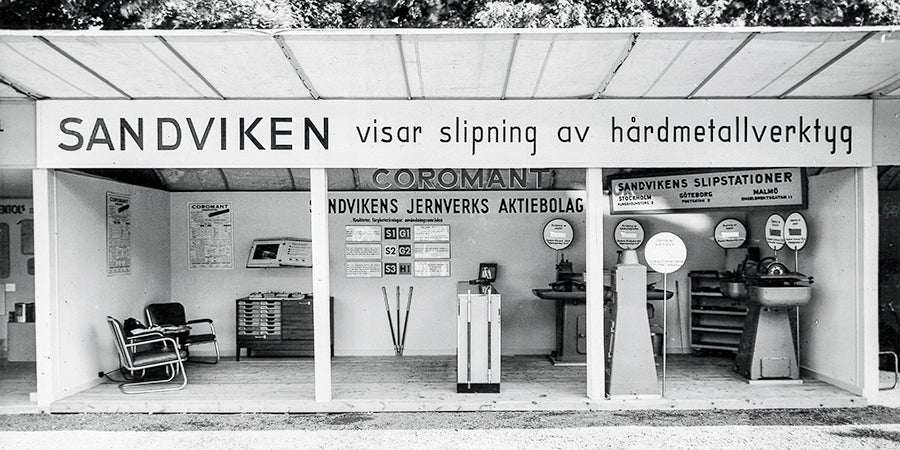
Grinding our way to the top
Early on, Sandvik Coromant was able to determine that tool renewal was vital to customers’ production. Unfortunately, however, when a carbide insert was reground by the customer, it no longer performed as well as it used to. Believing that customers should have access to first class grinding equipment operated by specially trained personnel, the company, in 1944, set up its first grinding stations. Here, customers could have their tools repaired and reground, while staff members attended training in the maintenance of cemented carbide tools.
Consequently, customers’ tool costs were reduced, and their productivity increased, and Sandvik Coromant became an early favorite in the industry.
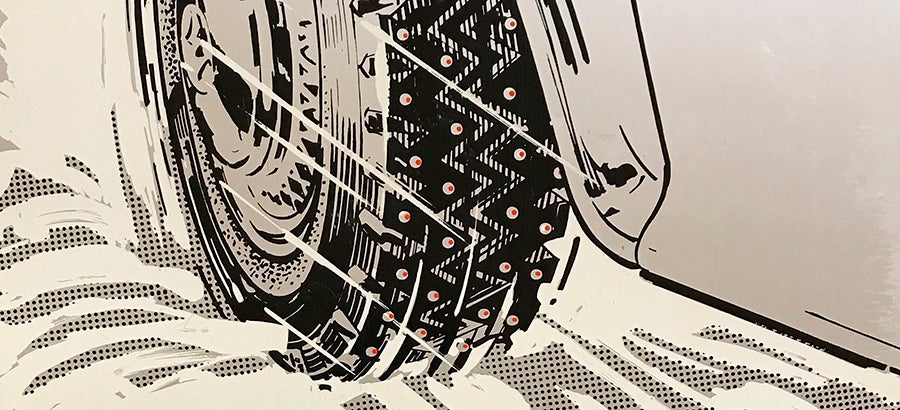
Gripping for pole position
At Sandvik Coromant, we take great pride in the innovative thinking and extensive research that has been a vital part of our company since day one. Sandvik studs (in Swedish, “Sandvikbrodden”) were, of course, no exception. It took the Wear Parts department several years to develop a cemented carbide of a quality that could withstand the strains of time, and had the right wear resistance. The end result was Sandvikbrodden, a popular stud that greatly contributed to increasing the safety on Swedish roads.
The quality of the studs was put to the test many times. On one occasion, a car producer decided to find out how the studs would behave on the tires of a truck weighing 29 tonnes. Some 30,000 kilometers (18,641 miles) later, the tires were finished, but the Sandvikbrodden were not. Out of a total of 552 studs, 448 were still in excellent condition.
When production was at its peak, we manufactured 15 million studs per week.
An Italian job and a French connection
In 1965, the distance between Paris and Rome was shortened by 150 kilometers (93 miles) thanks to the new Mont Blanc tunnel inaugurated by French President Charles de Gaulle and Italian President Giuseppe Saragat. It was the longest highway tunnel of the time.
The tunnel took more than six years to finish and involved tunneling through the Mont Blanc Massif, a mountain range in the Alps that includes some of the highest peaks in Western Europe. When completed, the tunnel connected the towns of Chamonix, France and Courmayeur, Italy.
The project involved a cooperation between Sandvik and Atlas Copco—and rock drills made of Sandvik Coromant cemented carbide.
Productivity on wheels
Food trucks, buses for blood donations and even libraries on wheels are a common sight in urban and rural landscapes. Sandvik Coromant has been part of the rolling fleet of service vehicles on the streets since the 1960s, when the Corovan was introduced to the Japanese market. The minivan is a product display stand on wheels; a platform from which sales representatives can present much of the Sandvik Coromant product range. It is also used for local marketing events.
“The sales engineers have to get to the customers anyway,” says Sandvik Coromant representative Mitsuhiro Kokubo. “Bringing the van generates a kind of ‘event atmosphere,’ even for routine visits.”
“This is a different kind of PR.” “What a vast range of tools!” “Isn’t this great!” These are typical customer remarks when sales representatives from Sandvik Coromant Japan roll up in the Corovan. Customers enjoy the opportunity to see the products “in real life” rather than in a brochure or online.
“I appreciate the fact that I can touch and feel the products and check the variety of tools here at my own facilities,” says Fumihiko Andoh, assistant manager of Oguchi Production Department Parts Machining – 2 in Aichi, Japan.
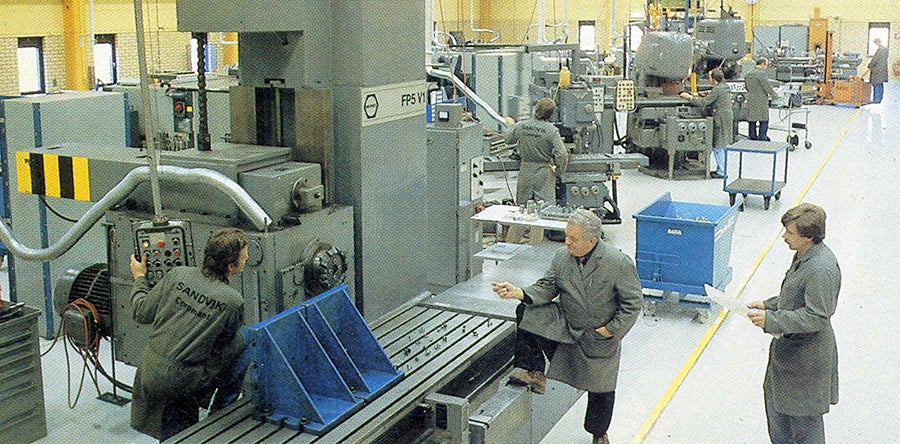
One-of-a-kind solution for a one-of-a-kind workforce
Desperate times call for desperate measures? Not necessarily. In the winter of 1992/1993, when the Sandvik Coromant warehouse in Gimo, Sweden fell on hard times, the company arrived at a unique solution. The warehouse had received instructions to reduce operations and dismiss 185 employees, but the local management came up with the idea of sharing the available jobs among the employees, resulting in the creation of a four-day workweek schedule—a solution that was gladly received by a great majority of the workforce.
The new four-day workweek was supposed to remain in effect until 1995, but it was canceled in the summer of 1994 when the economy improved sufficiently and employees could go back to working five days a week.
Chileans in the coal mine
On August 5, 2010, the San Jose gold and copper mine in Chile collapsed, trapping 33 miners underground. The trapped men were able to move to an underground emergency shelter where there was a small supply of canned food and 10 bottles of water, which could be supplemented by the thousands of liters of water that had been stored to keep the machine engines cool. Although not precisely drinking water, it was drinkable enough.
After 17 days, a drill from the surface finally broke through, enabling communication between the trapped miners and the rescuers at ground level. The first note, attached to the drill bit read, “We are well in the refuge, the 33.”
Sandvik Coromant’s CoroDrill® 800 Ejector system was essential in the construction of the drill that cleared the 2,000-foot (610-meter) path down to the trapped miners, creating a lifeline for food and water supplies. Finally, 52 days later, a new hole could be drilled that was wide enough for a rescue capsule to be sent down, and the trapped miners brought up, all in relatively good health. The entire ordeal, from collapse to rescue, lasted 69 days.
Millions of people around the world watched the rescue, which was achieved with a combination of engineering know how, strong morale and unyielding faith.
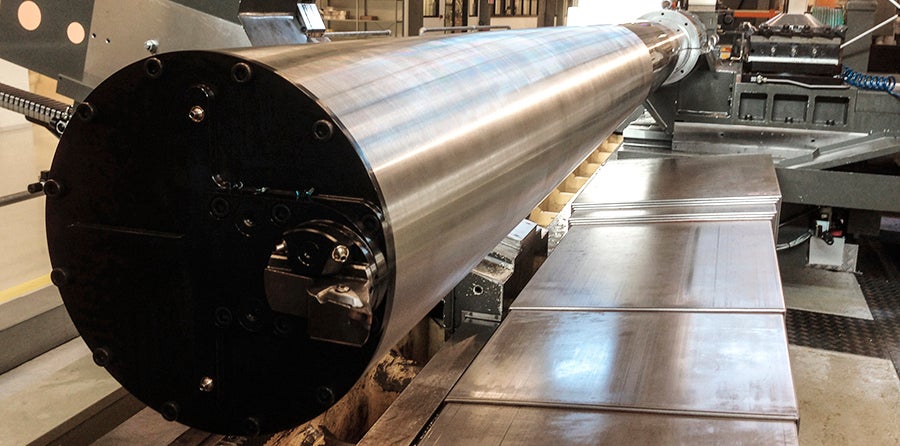
Record-breaking boring bar
In 2015, a milestone was achieved, and a world record was broken, thanks to the close collaboration, careful design and comprehensive solutions of two companies. The achievement took place at Gurutzpe Turning Solutions, in the province of Guípuzcoa, in the Basque country of northern Spain.
“Some years ago, we took part in the BIMU trade fair in Italy, where we came into contact with a company in Saudi Arabia, and that company became very interested in the potential of our lathes,” recalls Oscar Anitua, marketing manager at Gurutzpe. “They wanted to visit our plants, and that gave us the opportunity to show our capabilities in technology and design. They were so pleased with what they saw that they ordered a 65-foot (20-meter) long lathe.” It was on that lathe that the world’s biggest reinforced Silent Tools™ anti-vibration boring bar, produced by Sandvik Coromant, was mounted.
Jon Arregi, a machine specialist at Sandvik Coromant says:
“When Sandvik Coromant Ibérica received the order, we contacted Sandvik Coromant’s department for vibration-free machining in Trondheim regarding the construction and manufacturing of the Silent Tools™ anti-vibration boring bar with capacity for a maximum length of 165 inches (4,200 millimeters), 14 times the bar’s diameter of 11.8 inches (300 millimeters). The cooperation between Sandvik Coromant’s department in Trondheim and Gurutzpe also extended to the design of the clamp for the machine.”
The production of the boring bar took four months, and, when it was finished, it was 240 inches (6,090 millimeters) long—a new world record in the premium class.
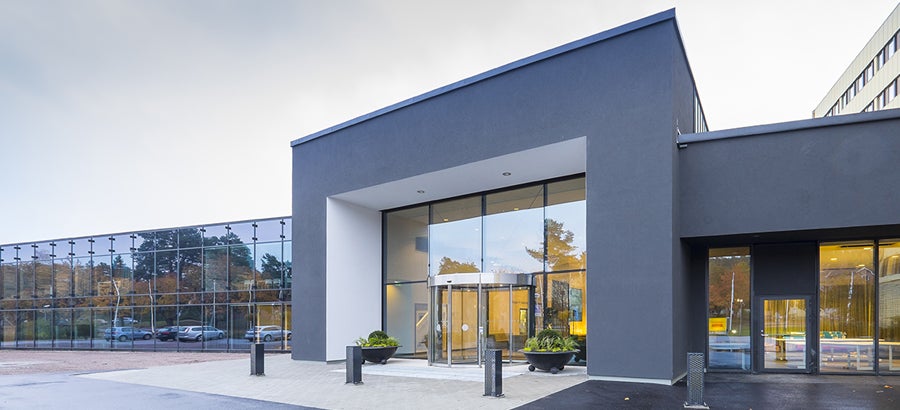
Sandvik Coromant Center
In October 2014, after two years of construction, Sandvik Coromant opened its flagship Sandvik Coromant Center in Sandviken, Sweden. In November of the same year, the company opened a similar center in Langfang, China. Senior Project Manager Bertil Isaksson said at the time that Sandvik Coromant envisions these centers to be global meeting places for the industry.
“We would like to show that Sandvik Coromant is a part of the manufacturing industry of the future,” he said. “Visiting customers will get a feel for what will happen in their line of business. They will also get an understanding of what Sandvik Coromant can offer as a partner.”
“We are clear on what we want our visitors to remember when they leave,” Isaksson says. “From a technical perspective, they can become familiar with our new products and get solutions to their productivity challenges. If the challenges are advanced, we can help them with our application knowledge. I can guarantee that we have a solution that will meet their needs.”
The centers are part of a network of Sandvik Coromant centers around the world, and know how gained at one center can easily be shared at the other centers. Klas Forsström, Sandvik Coromant's president at the time of the opening of the Sandvik Coromant Center in Sandviken, commented on the investment: “We have created a world-class meeting place that we are convinced is needed by the manufacturing industry,” Forsström said. “It is a center for everyone who is interested in productivity gains, cutting-edge research innovations and the future of global manufacturing.”