Solutions for cost effective and high-quality machining of aerospace spool
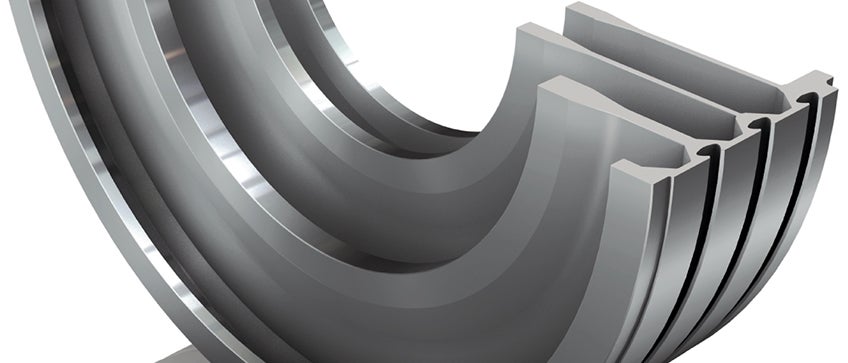
The two challenging features of this component are the deep internal chambers and external blade tulip grooves.
A combination of engineered solutions and methodology with optimized grades are the key to success.
Tooling solutions for machining of aerospace spools
Grades optimized for turning of aged nickel-based HRSA
Turning grades GC1205 and GC1210 provide secure and reliable machining with excellent flank and notch wear resistance. A combination of a hard substrate and PVD coating allows for a significant increase in cutting speed (GC1205) and tool life (GC1210).
- GC1205: Finishing grade for machined surfaces. For last stage machining and intermediate stage machining applications
- GC1210: Mainly used in intermediate stage machining applications. Complements GC1205 when more toughness is required
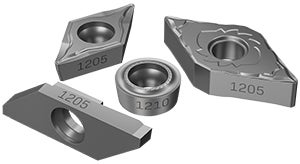
CoroCut® angled inserts to fit any groove shape
Designed specifically for reaching difficult-to-access grooves and pockets in complex components. To complement the standard CoroCut 90 degree program, blanks are available in 90,45 degree and T-shape for more specialist requirements.
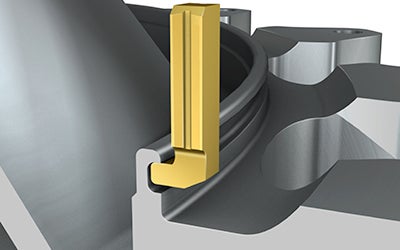
Dampened blades with Coromant Capto®
To machine deep internal chambers typically up to 150 mm, long, slender tools are required. The challenges are a tendency for vibration and removal of the chips from the groove.
Turning one of the most challenging features into a secure process has been achieved by:
- An oval serration blade system for optimal stability and accessibility. The 100-mm high blade allows for the best coolant delivery to assist in chip removal
- For blades longer than 4x width of the blade, a patented dampening device is part of the design. This allows depth of cut to be 4 times greater than without dampening
- A trochoidal turning technique combined with ceramic grade CC6160, 6220 or 6230 reduces the number of machining passes required
A secure process with more than double the productivity
Read more about the Coromant Capto® system
![]() Without dampening | ![]() |
![]() Same cutting conditions with dampening |
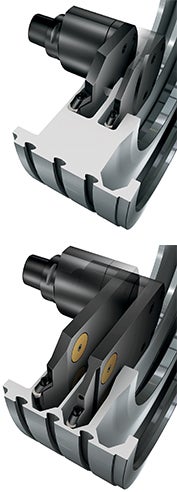
Ceramic turning
Ceramic grades CC6220 and CC6230 are designed specifically for the challenges of new HRSA materials, where whisker ceramics and SiAlONs fall short, and are capable of higher cutting speeds, which helps reduce cost per component. For high metal removal rates in pocketing and profiling applications, choose grade CC6160. For more demanding HRSA surfaces, choose the tougher grade CC6165.
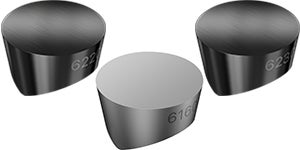
RCMX turning inserts for intermediate to finishing
The carbide RCMX insert fits in same insert pocket as ceramic, reducing number of tools required and the set-up time. The geometry provides low cutting force and good chip control.
- S05F for HRSA or H13A for titanium
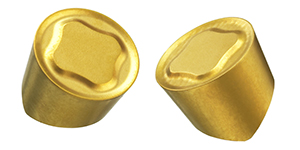
RCGX turning inserts for finishing to super-finishing
Round insert with V-shape bottom providing improved surface quality. Low cutting forces thanks to the smooth geometry.
- S05F for HRSA or H13A for titanium
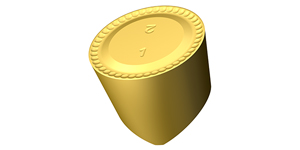
CB7014 high-speed CBN turning solution for nickel-based alloys
Finish turning of aerospace components involves challenging operations performed in demanding ISO S materials. Using CBN inserts allows for increased cutting speeds and improved productivity while maintaining good surface integrity on the component. CBN inserts optimized for high speed finishing of nickel-based heat resistant super alloys are now available as a stocked standard solution.
CoroTurn® 107 with rail interface for profiling and pocketing in HRSA materials
For finishing in HRSA components with relatively open features, the positive, screw-mounted CBN insert is optimal. With up to 12 insert indexes, it will boost your productivity in HRSA materials. The rail interface ensures mounting security, offers process security and increases reliability and tool life for your profiling and pocketing operations.
Fan discs
Made from titanium, this component has internal chambers to be bored and large tulip... chevron_right
Turbine disc
Aerospace turbines must withstand extreme temperatures and pressure differences.... chevron_right
Fan casings
The machinability of titanium is low; however, unlike with nickel alloys, ceramic... chevron_right
Grooving solutions
Groove machining on power components requires versatile, rigid tools suitable for... chevron_right