How to apply coolant in parting and grooving
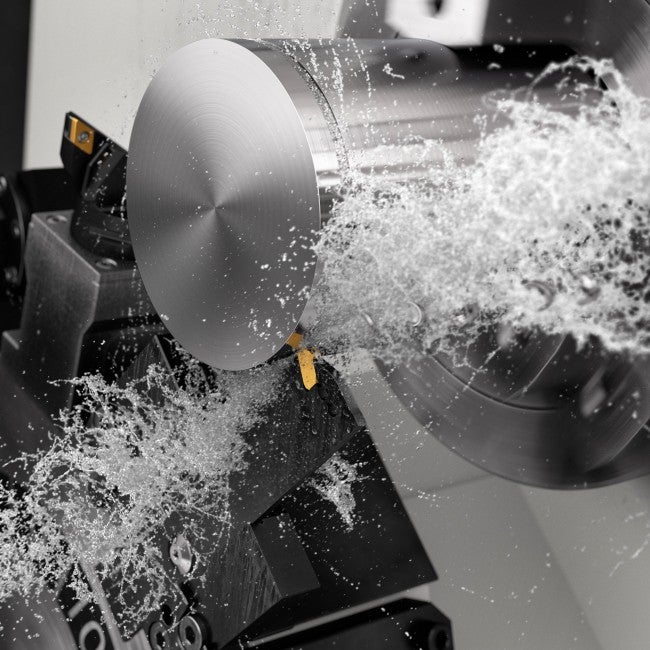
The use of coolant and lubrication has a large impact on process security in parting and grooving. If applied correctly, it reduces temperature at the cutting zone and improves chip evacuation.
Internal versus external coolant
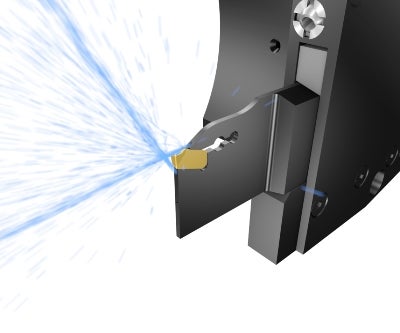
When external coolant is applied in parting and grooving, the amount of coolant that actually gets into the groove, especially with deep grooves, is very small. Therefore, the coolant effect is minor. With internal coolant delivered with precision, the coolant jets access the cutting edge even in deep grooves.
Advantages with precision coolant
- Higher cutting data, or the ability to use a tougher carbide grade
- Improved chip control and surface finish
- Longer tool life
Over or under coolant? Or both?
Depending on the machining conditions, you can choose to apply tools with internal over- or under-coolant. Sometimes you just need one, but you get the best effect when using both at the same time.
The effects of over-coolant
Over-coolant improves chip control, which is the key to longer tool life and fewer machine stoppages. Coolant from above and can also reduce edge build-up.
The effects of under-coolant
Under-coolant reduces temperature and flank wear at the same time. It also improves chip evacuation. Reduced temperature allows for the use of softer insert grades with potentially improved tool life and cutting data. When used in combination with tougher insert grades, it results in a more predictable and secure machining process. Under coolant is beneficial in long cuts where temperature is often a limiting factor.
The Impact of Coolant on Different Materials
The coolant effect is greatest when machining materials with low thermal conductivity, such as stainless steels and heat-resistant super alloys. Coolant also has a large impact on smearing materials such as low carbon steels, aluminum, and duplex stainless steels.
Different materials’ unique properties regarding machinability
Recommendations
Using the right amount of pressure
To put it in simple terms, the more coolant pressure you add, the better the tool life and chip control. There are, however, exceptions. In some cases, tool life can be reduced when using pressures above 100 bar (1450 psi). Low coolant pressure can improve tool life and chip control to some extent, while coolant pressure in the range of 30–80 bar (435–1160 psi) will significantly improve both.
Avoid temperatures that are too low and edge build-up
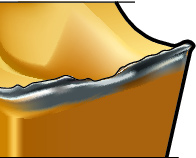
Temperatures that are too low can cause built-up edges on the insert
Temperatures that are too low risk decreasing tool life, especially when machining in stainless steels. This will lead to a built-up edge (BUE) area. If this occurs, you may need to increase the temperature. This is best done by:
- Increasing feed and speed. When using internal coolant, increase the cutting speed by 30 to 50 percent
- If a built-up edge occurs when parting-off to center, switch off the coolant after the machine’s RPM limit is reached
Precision coolant advantages for machining aerospace materials
The role of coolants in machining aerospace parts has undergone something of an evolution.... chevron_right
Parting and grooving
In parting and grooving, process security and productivity are two important aspects.... chevron_right
Internal grooving
Long overhangs and poor chip evacuation are two of the challenges with internal grooving.... chevron_right
Coolant aspects
In some cases, it may be beneficial, from environmental and cost perspectives, to... chevron_right