The hardest there is
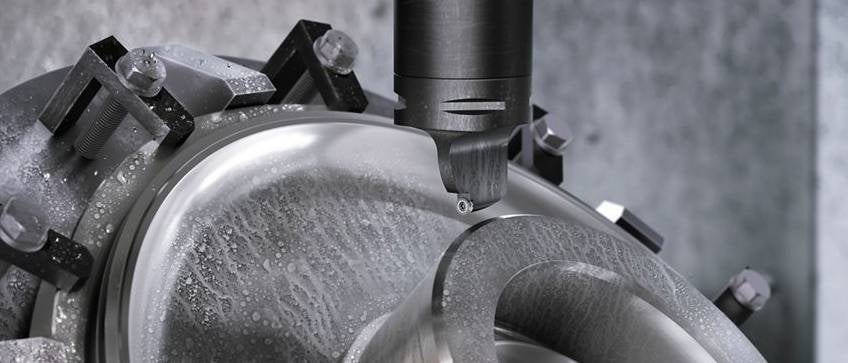
The aerospace industry is one of the most technically demanding fields out there, and components for aircraft engines are among the most difficult to manufacture. Manufacturers can take advantage of the latest processing knowledge and the best possible tools when machining each component. Here are some examples involving seven of the most important components of an aerospace engine.
Turbine disk
CoroTurn® SL70: Complex turning made easy
The flexible modular CoroTurn SL70 tooling system equipped with round inserts can be used for roughing and finishing of typical profiling and pocketing features. The SL70 system is perfect for turbine disks, which have complex features in difficult-to-manufacture alloys, often with profiled pockets and various difficult clearance requirements.
Fan disk
Get the right angle with CoroCut® angled inserts
Fan disks are made of titanium and have grooves and tulip grooves that must be machined. CoroCut angled inserts are formed to reach difficult-to-access grooves. They come in a variety of standard shapes so special tools are not needed.
Turbine casing
Ceramic turn milling for high-speed machining
When machining the turbine casing, you need to remove large quantities of challenging materials (Inconel and Waspaloy, for example) through a rough milling process. Ceramic turn milling inserts offer opportunities to run at 20 to 30 times the speed of carbide, although at lower feed rates, which results in high productivity gains
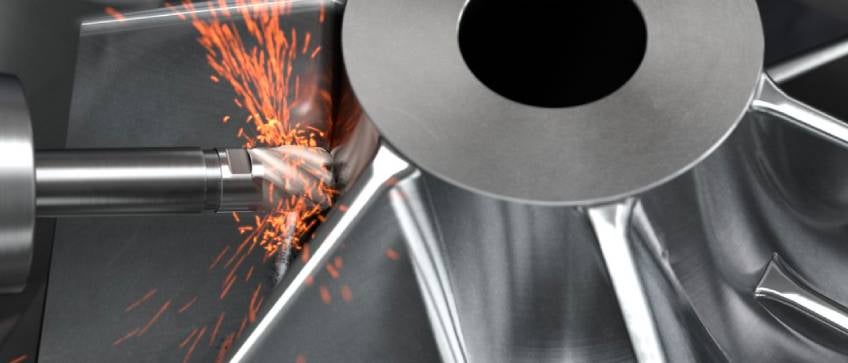
Fan casing
Stay cool with precision coolant
Successfully machining fan casings made of titanium requires the cutting temperature to be kept low. Sandvik Coromant's precision coolant systems are designed to hit the exact spot where the coolant is most usable, which results in good chip control, longer tool life and increased productivity.
Spool
Damped blades: When stability is everything
One of the challenges in manufacturing a spool is its deep internal chambers. To manufacture these chambers, typically up to 150 millimeters deep, you need a long, slender tool. With the Coromant Capto® coupling system, damped blades offer a stable solution that minimizes vibration, which means the depth of cut can be four times greater than without damping.
Shaft
Silent Tools™: Quiet, please!
The length and internal features of a shaft make it the perfect challenge for Silent Tools damped bars. The boring bar program is available for diameters of up to 250 millimeters and overhangs of up to 14 times the diameter, which is outside the parameters for conventional tools.
Blisk
Secure flexibility with CoroMill® Plura conical ball nose end mills
Flank milling (high axial depth of cut) is the fastest option when milling a component. The standard program of conical ball nose end mills is specifically designed for this operation, offering excellent stability combined with reach.
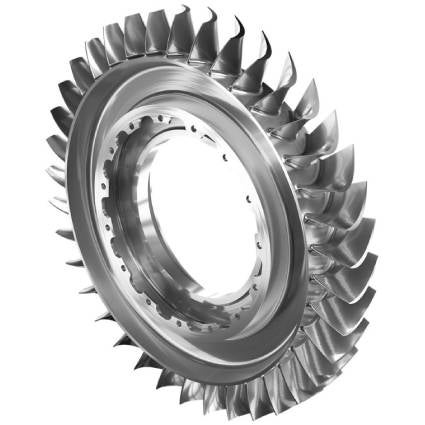
Blisk
CoroMill® 316: Balanced productivity
When manufacturing blades on a disk or blisk, an optimal method for roughing is point milling. CoroMill 316 ball nose exchangeable cutting heads offer a great balance of productivity and economy.
For further information, please visit www.aeroknowledge.com.