턴 밀링 가공
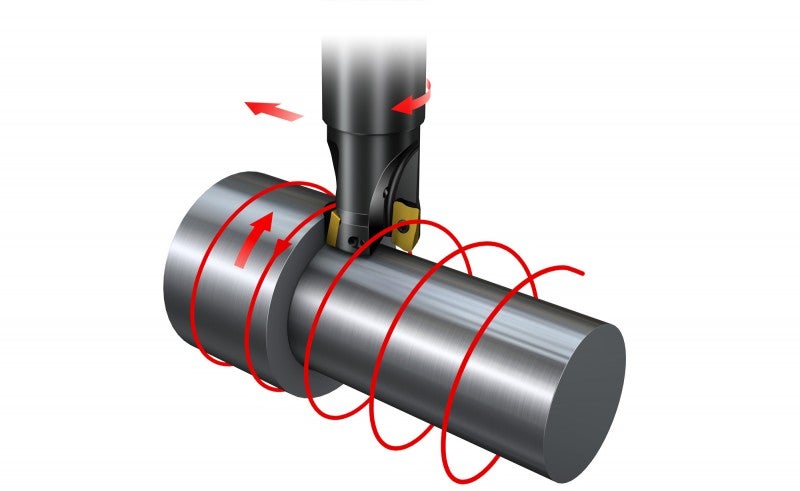
성공적인 턴 밀링 가공이란?
턴 밀링 가공은 센터를 중심으로 가공물을 회전시키면서 곡면을 밀링 가공하는 것으로 정의됩니다.
기존의 밀링 또는 선삭 작업과 크게 다른 편심 형태나 모양을 턴 밀링으로 가공할 수 있습니다. 이 방법은 금속 제거율과 칩 컨트롤이 탁월합니다.
- 원통형 표면은 회전 중에 반경 방향으로 밀링 커터를 이송할 때만 가공할 수 있습니다.
- 커터를 두 방향으로 동시에 이동하면 편심 표면을 가공할 수 있습니다(예: 샤프트의 캠).
- 2축 이상에서 이동하려면 램핑 가공 기능이 있는 공구가 필요합니다.
- 원추형 모양을 가공하려면 5축이 필요합니다.
- 복잡한 프로파일(예: 터빈 블레이드)의 턴 밀링 가공에는 5축 또는 4축(가공물에 2축 또는 3축, 공구에 1축 또는 2축)에서 동시 이동이 필요합니다.
- 가공물이 회전하는 동시에 커터를 2축 이상에서 이송하면 터빈 블레이드 같은 가공물을 생산할 수 있습니다.
턴 밀링 가공 공정의 선택
평면 턴 밀링 가공 – 4/5축
외경 가공을 위한 주요 방법
+ 짧은 공구 연장부
+ 작은 공구 직경/낮은 토크
+ 외경/가는 가공물
+ 프로파일 가공
− 자연스러운 원통형 표면이 아님
− 내경
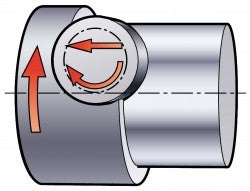
원주 턴 밀링 가공 – 3/4축
원호 보간과 동일한 원리이지만(내경 / 외경), 턴 밀링 가공에서는 가공물과 커터가 모두 회전합니다.
주로 내경에 사용
+ 내경 가공
+ 원통형 표면
+ 좁은 슬롯
+ 나사 밀링 가공
+ 진원도
− 프로파일 가공
− 대직경/높은 토크
− 긴 오버행
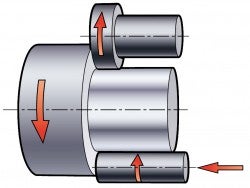
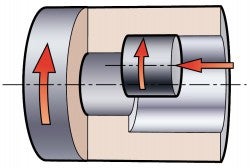
턴 밀링 가공 적용 방법
커터 위치 - 직사각형 인서트/와이퍼
커터 위치
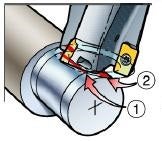
절삭 폭
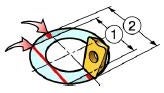
1 = 1차 절삭
2 = 2차 절삭
평면 턴 밀링 가공에서는 가공물의 원통형 부분을 가공하기 위해 하나의 와이퍼 인서트를 사용해 커터와 가공 표면 사이에 직선 접촉면을 생성합니다.
밀링된 표면이 볼록하기 때문에 와이퍼 랜드가 평평해야 합니다. 커터 폭 전체를 커버하려면 공구를 최소 2개의 오프셋과 함께 위치해야 합니다. 먼저 최초 가공물 회전 중 Ew1이었다가 2차 절삭을 위해 Ew2로 이동합니다.
커터 위치 - 원형 인서트/비 와이퍼
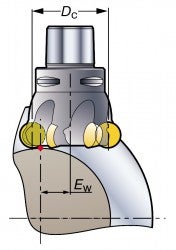
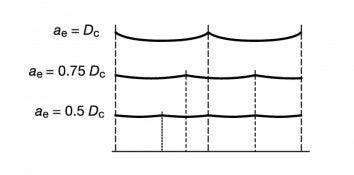
턴 밀링 가공에서 최대한 평평한 표면을 가공하려면 절삭 폭 ae가 유효 커터 직경 DC의 40% 미만인 소직경 커터가 최적입니다.
그러나 생산성을 극대화하려면 ae를 증가시켜야 합니다. 이는 다음을 증가시키면 가능합니다.
- 커터 직경
- 반경 방향 맞물림의 비율 – ae/DC
허용 가능한 파형 높이에 도달하려면 커터가 중심으로부터 오프셋되어야 합니다. 오프셋의 양은 ae에 따라 다르고 ae/DC의 도표에서 확인할 수 있습니다.
오프셋과 절삭 폭
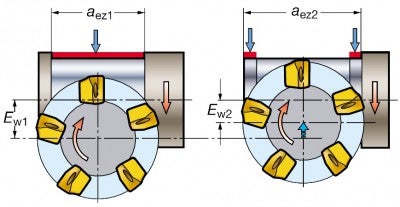
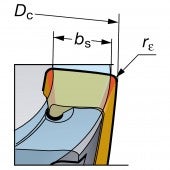
와이퍼 폭
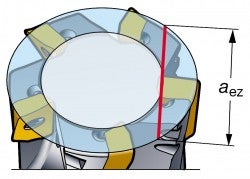
절삭 폭
커터 직경보다 넓은 표면을 밀링 가공하려면 최초 위치를 유지한 다음 축 방향으로 필요 길이까지 커터를 이동해야 합니다. 그러나 회전당 aez1의 80%를 넘으면 안 됩니다. 90° 직각이 필요할 경우 커터를 두 번째 위치 Ew2로 이동해야 합니다.
인피드 원리
턴 밀링 가공 중에 밀링 공구는 반경 방향으로 공작물로 이송되어야 합니다. 공작물 회전 속도는 인서트의 권장 이송/날과 일치해야 합니다. 커터는 축 방향으로 이송되어야 합니다.
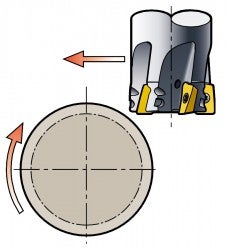
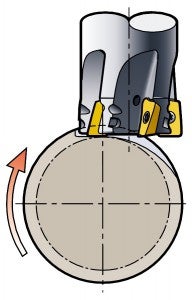
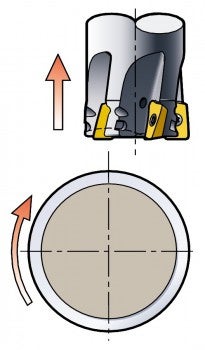
커터 경로 및 칩 형성
밀링 가공에서 올바른 커터 경로와 칩 형성은 안정적인 절삭날과 향상된 공구 수명을 위해 중요한 요소입니다. 반경 방향에서 밀링 커터의 각 절삭날은... chevron_right
램핑 가공: 2축 선형 및 원호
성공적인 램핑 가공이란? 선형 램핑 가공 은 막힌 슬롯/포켓/캐비티을 가공할 때 가공물에 접근하는 효율적이고 일반적으로 사용되는 방법이며, 드릴이... chevron_right
내경 선삭 가공
내경 선삭 가공은 가공물의 내경을 가공합니다. 긴 오버행과 칩 배출의 어려움은 내경 선삭 가공의 대표적인 문제입니다. 오버행이 길면 편향과 진동... chevron_right
스텝 및 챔퍼 드릴링
챔퍼 드릴링 스텝 드릴링 또는 스텝 및 챔퍼 드릴링 챔퍼 드릴링 챔퍼 홀이란? 가공되는 모든 홀들 중 상당수는 챔퍼가 필요하거나 적어도 디버링이... chevron_right