홀 및 캐비티/포켓의 밀링 가공
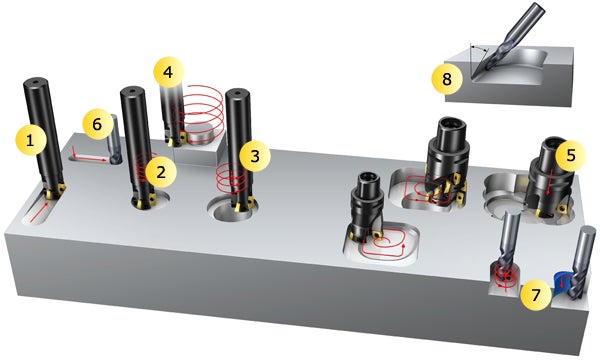
- 2축 선형 램핑 가공
- 원호 램핑 가공
- 홀 확대
- 원호 외경 밀링 가공 또는 램핑 가공
- 플런지 밀링 가공
- 펙 밀링 가공
- 슬라이싱 방법
- 예각 포켓 또는 각도
홀 밀링 가공: 홀 생성
- 솔리드 가공물에서 홀 생성
- 홀 또는 캐비티 확대
- 캐비티 또는 포켓 생성/확대
솔리드 가공물에서 홀 생성
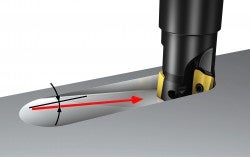
선형 램핑 가공
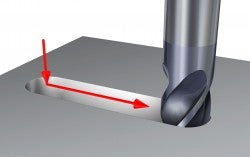
펙 밀링 가공
슬롯 생성
홀의 밀링 가공 때 선형 램핑 가공(2축 동시)이 펙 밀링 가공보다 항상 선호되는 방법입니다.
펙 밀링 가공은 대안적인 홀 밀링 가공 방법이지만, 때때로 긴 칩을 생성하고 커터에 바람직하지 않은 절삭 부하를 발생시킵니다.홀 또는 캐비티 생성
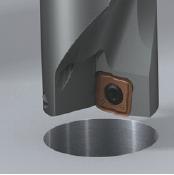
드릴링 가공
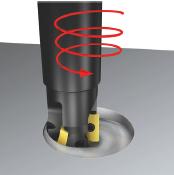
원호 램핑 가공
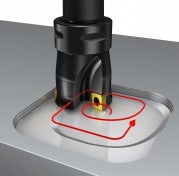
캐비티 램핑 가공
드릴링 가공은 홀을 생성하는 전통적이고 가장 빠른 가공법이지만, 일부 소재에서는 칩 브레이킹이 문제가 될 수 있고 유연성이 부족해서 다양한 직경과 원형이 아닌 모양을 가공하는 데 어려움이 있습니다.
원호 램핑 가공(3축 동시)은 홀을 드릴링하는 것보다 생산성이 떨어지지만, 다음과 같은 경우에 좋은 대안이 될 수 있습니다.
- 기계 동력이 부족할 때 대직경 홀의 가공
- 소규모 연속 생산. 직경이 25 mm보다 큰 경우의 일반 원칙: 최대 약 500개의 홀을 연속 가공할 때 밀링 가공이 비용 효율적임
- 다양한 홀 크기를 가공할 때
- 여러 종류의 드릴 크기를 보관하기에는 공구 매거진 공간이 제한적인 경우
- 막힌 홀의 생산, 평면 홈이 필요할 때
- 연성, 벽이 얇은 가공물
- 단속 절삭
- 칩 브레이킹과 칩 배출 문제 때문에 드릴링하기 어려운 소재
- 절삭유를 사용하지 않는 경우
- 캐비티/포켓을 밀링 가공할 때("원형이 아닌 홀")
방법 선택 - 예
캐비티/포켓 생성
![]() | ||||||
![]() | ||||||
드릴링 및 원호 밀링 가공 ![]() ![]() | 드릴링 및 플런지 밀링 가공 ![]() ![]() | 원호 램핑 가공 ![]() | ||||
장점 + 원형이 아닌 홀에서 높은 칩 제거율 + 우주 항공 프레임 티타늄 구조물 부품에 우선 추천 단점 – 안정적인 기계 필요 – 칩 배출 – 수평 기계 – 신중한 프로그래밍 필요 | 장점 + 긴 오버행에서 발생하는 문제 해결 + 구형/다축 스핀들 장비에 적합한 간단한 프로그래밍 단점 – 낮은 칩 제거율 | 장점 + 공구 수 감소(드릴 불필요) + 유연성(다양한 크기 가공) + 절삭유 불필요 = 개방형 기계에 적합 + 모든 기계 유형과 구성에 적합 단점 – 큰 캐비티에서 생산성이 떨어짐 | ||||
포켓을 위한 기본 선택 | 긴 오버행에서 발생하는 문제 해결 | 3D 동공을 위한 기본 선택 |
홀 또는 캐비티 확대
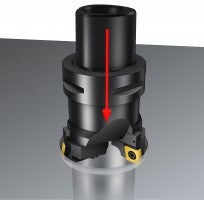
보링 가공
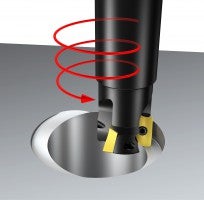
원호 램핑 가공
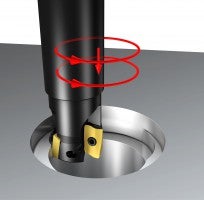
원호 밀링 가공
홀 확대
일반적으로 보링 가공은 드릴링 가공과 같은 이유로 가장 빠른 가공법이지만, 때때로 홀 밀링 가공이 좋은 대안이 될 수 있습니다. 사용할 수 있는 두 가지 대안적인 밀링 가공법은 원호 램핑 가공(3축)과 원호 밀링 가공(2축)입니다. 원호 램핑 가공은 홀이 최대 ap보다 더 깊거나 진동에 민감한 작업에서 선호됩니다. 또한 램핑 가공 시, 특히 긴 오버행에서 홀의 진원도/동심도가 개선됩니다. 원호 램핑 가공과 원호 밀링 가공 모두에서 밀링 커터를 원호 경로로 이동하는 대신 가공물을 회전할 때 진원도가 개선됩니다.캐비티 확대
내경 직각 밀링 가공 및 플런지 밀링 가공에는 시작 홀이 필요하고 솔리드 블록으로 직접 캐비티를 램핑 가공하는 방법과 비교해야 합니다.
- 램핑 가공(3축)은 공구가 하나만 필요하고 3D 모양을 가공할 수 있어 프로파일 밀링 가공에 적합하다는 장점이 있습니다. 고이송 기술(light and fast)을 적용할 경우 절삭력이 진동 문제를 최소화하는 유리한 방향으로 향하게됩니다.
- 플런지 밀링 가공은 오버행이 길거나 깊은 캐비티에서 발생하는 문제를 해결합니다.
- 내경 직각 밀링 가공은 플런지 밀링 가공보다 더 많은 프로그래밍이 필요하지만, 더 빠릅니다.
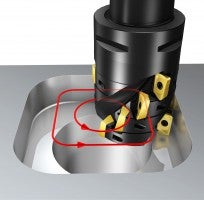
내경 직각 밀링 가공
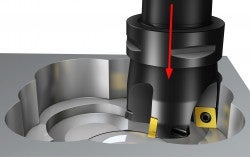
플런지 밀링 가공
잔삭(남은 스톡) 밀링 가공
캐비티 황삭 가공이 완료된 후 특히 코너에 스톡이 남아 있는 경우가 종종 있습니다. 작은 커터를 사용한 플런지 밀링 가공은 정삭된 모양에 더 근접하기 위한 한 방법입니다. 슬라이싱(light and fast)은 코너 밀링 가공에 사용되는 또 다른 기술입니다. 트로코이드 밀링 가공은 슬롯, 포켓 등의 밀링 가공에 사용되는 슬라이싱 기술의 한 유형입니다.
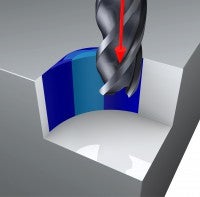
코너의 플런지 가공
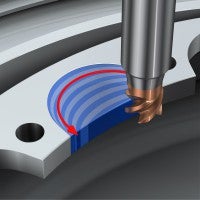
슬라이싱 기술 – light and fast
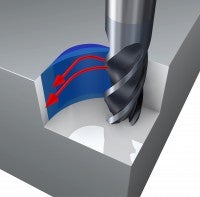
코너의 슬라이싱
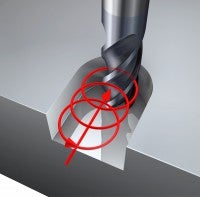
트로코이드
캐비티 또는 포켓의 생성/확대 방법
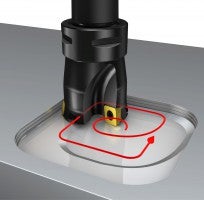
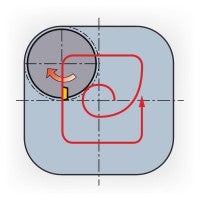

두 가지 전략이 있습니다.1. 원호 램핑 가공(3축) – 작은 ap
절입각이 작은 커터를 사용하십시오. 원형 인서트 커터는 또 다른 대안입니다.
이 "light and fast" 기술은 뛰어난 금속 제거율을 제공하고 안정성이 떨어지는 기계(ISO 40 기준)와 동공에 프로파일 가공된 모양이 있을 때(예: 금형) 우선 추천됩니다.
주의: 낮은 절입 각도의 효과가 손실될 수 있기 때문에 90° 직각에 대한 가공은 하지 마십시요(예: 절입 깊이가 급격히 증가).
절삭 매개 변수:
- 최대 커터 직경 = 1.5 x 가공물 코너 반경
- 깊이까지 원호 램핑 가공 – 반시계 방향
- 다음 절삭으로 롤인(roll in) 형태로 진입
- 반경 방향 절삭 – 최대 ae = 70% DC
- 원형 인서트 커터 25% iC의 경우 축 방향 절삭
- 코너의 공구 경로 반경 = DC
- 코너 이송 감소
2. 원호 밀링 가공(2축) – 큰 ap
홀을 드릴링한 후 직각 엔드밀이나 롱에지 커터로 변경하십시오. 일반적인 적용 영역은 우주 항공 프레임 – 티타늄 가공입니다.적용 정보
칩의 재절삭/칩 걸림을 방지하려면 칩 배출이 양호해야 합니다.
- 수평 스핀들(ISO 50)이 선호됩니다.
- 고압 절삭유 또는 압축 공기 및 공구 관통 절삭유
- DC가 홀 직경의 75%보다 크면 안 됩니다. 큰 축 방향 절삭을 사용하십시오(최대 ae = 2 x DC).
드릴링한 홀에 원호 경로로 진입해야 합니다.
- 반경 방향 맞물림을 제어하십시오(최대 ae = DC의 30%).
코너에서 진동을 최소화하고 생산성을 극대화할 수 있도록 반경 방향 맞물림을 제어하십시오.
- 코너에서 가능한 한 가장 큰 반경, 나선형 프로그래밍을 사용하십시오.
- 1.5 x 코너 반경보다 크지 않은 상태에서 가능한 한 가장 큰 DC와 완전한 잔삭 밀링을 개별적으로 사용하십시오.
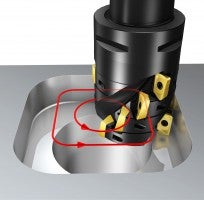
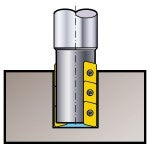

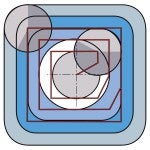

작은 코너 반경
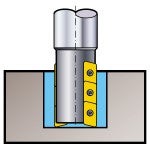

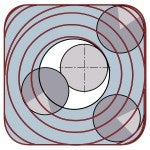

나선형 몰프 프로그래밍
슬라이싱 방법
슬라이싱과 트로코이드 밀링 가공은 원래 고경도 강, ISO H 및 HRSA 소재, ISO S 같은 난삭재의 황삭 및 준황삭 가공을 위해 개발되었지만,... chevron_right
평면 밀링
평면 밀링 가공에 포함되는 작업 일반 평면 밀링 가공 고이송 밀링 가공 중절삭 평면 밀링 가공 와이퍼 인서트를 사용한 정삭 일반 평면 밀링... chevron_right
선삭에서 가공물의 품질을 높이는 방법
선삭 가공물의 품질을 높이려면 칩 컨트롤이 고려해야 할 가장 중요한 요소 중 하나입니다. 올바른 절삭 조건을 선택하고 좋은 부품 품질을 위한 적용... chevron_right
다양한 소재의 밀링 가공
강의 밀링 가공 강의 가공성은 합금 성분, 열처리 및 제조 공정(단조, 주조 등)에 따라 달라집니다. 연성의 저탄소강은 가공물의 구성인선과 버... chevron_right