평면 밀링
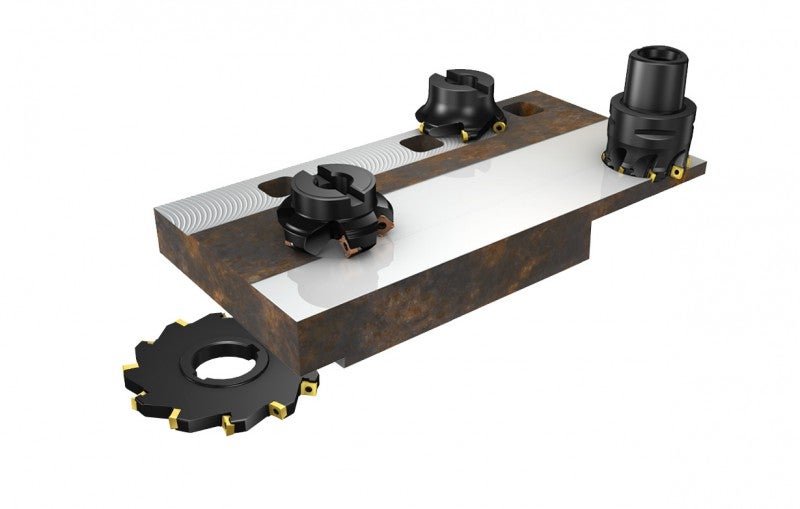
평면 밀링 가공에 포함되는 작업
- 일반 평면 밀링 가공
- 고이송 밀링 가공
- 중절삭 평면 밀링 가공
- 와이퍼 인서트를 사용한 정삭
일반 평면 밀링 가공
성공적인 평면 밀링 가공이란?
평면 밀링 가공은 가장 일반적인 밀링 작업이고 다양한 공구를 사용해 수행할 수 있습니다. 절입각이 45º인 커터가 가장 많이 사용되지만, 특정 조건에서는 원형 인서트 커터, 사각 직각 커터, 사이드 및 평면 밀링 커터도 사용됩니다. 작업의 생산성을 극대화할 수 있는 커터를 선택하십시오(아래의 공구 선택 정보 참조).
공구 선택
평면 밀링 커터 개요
아래의 다이어그램에는 커터 공구별 절입 깊이(ap), 날당 이송(fz) 등의 적용 영역이 나와 있습니다.
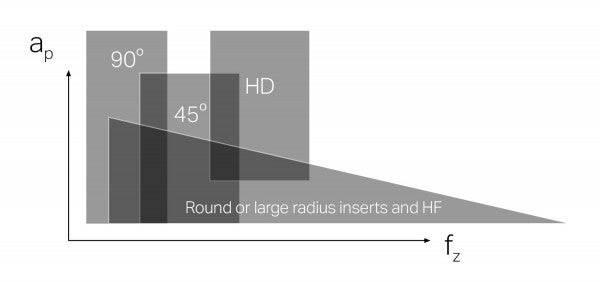
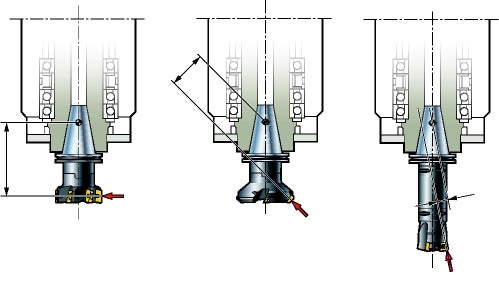
절입각별로 발생하는 절삭 부하의 방향
10° - 65° 평면 및 플런지 밀링 커터
평면 밀링 가공에서는 기본적으로 다양한 커터가 사용되지만, 절입각이 매우 작아서 플런지 밀링에 적합한 커터도 사용됩니다.
45° 커터
- 일반 작업에서는 우선 추천
- 긴 오버행과 약한 셋업에서 진동 감소
- 칩이 얇아지는 효과로 생산성 향상
90° 커터
- 얇은 박판 가공물
- 지그가 약한 가공물
- 90° 형태가 필요한 경우
원형 인서트 및 대형 반경 커터
원형 인서트 커터는 많은 용도로 사용할 수 있으며, 램핑 기능이 우수하고, 까다로운 평면 밀링과 프로파일 작업 모두에서 사용됩니다.
- 일반용 커터
- 강도가 가장 높은 절삭날
- 인서트당 많은 절삭 날
- 내열 합금인 ISO S에 적합
- 부드러운 절삭 수행
방법 선택 - 예
평면 밀링 가공
![]() | ||||||
![]() | ||||||
25-65° 절입각 | 90° 절입각 | 10° 절입각 | ||||
장점 + 높은 생산성 + 평면 밀링에 최적화 + 여러날 인서트 옵션 단점 – 적당한 절입 깊이 | 장점 + 다양한 작업에서 사용할 수 있는 다목적 커터 + 축 방향 부하 낮음 + 인서트 크기에 비해 상대적으로 큰 절입 깊이 단점 – 생산성 저하 | 장점 + 높은 생산성 + 매우 높은 이송 + 축 방향 절삭력 방향(스핀들 안정성 측면에서 효과적) 단점 – 절입 깊이가 얕음 | ||||
높은 생산성 기본 선택 | 다용도 혼합 생산 | 높은 생산성 문제 해결 |
적용 방법
표면의 단속 평면 밀링 가공
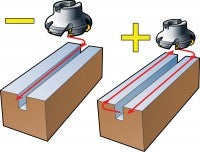
단속 시 밀링 중단
- 가능하면 단속(홀 또는 슬롯) 시에는 밀링을 중단하십시오. 이러한 단속 절삭은 여러번에 절입부와 불리한 진출부를 발생시키므로 공구의 절삭날이 처리하기 어렵습니다.
- 또는 단속이 포함되는 가공물 영역에서 추천 이송 속도를 50% 줄여 진출부에서 칩 두께를 얇게 유지하십시오.
벽이 얇고 휘는 부분의 평면 밀링 가공
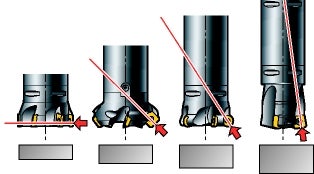
- 가공물과 지그의 안정성을 고려하여 주 절삭 부하의 방향을 정하십시오.
- 축 방향으로 약한 가공물을 밀링 가공할 때 절삭 부하의 대부분을 반경 방향으로 유도하는 90° 직각 밀링 커터를 사용하십시오.
- 또는 경절삭 평면 밀링 커터를 사용하십시오.
- 축 방향의 힘을 최소화하기 위해 0.5-2 mm보다 얕은 축 방향 절입 깊이는 사용하지 마십시오.
- 절삭날 수의 최소화를 위해 코스 피치 커터를 사용하십시오.
- 날카로운 포지티브(- L) 날을 사용하여 절삭 부하를 최소화하십시오.
- 문제가 발생할 경우 비균등 피치 커터를 사용하십시오.
평면 밀링 커터를 사용하여 얇은 부분의 엣지 가공
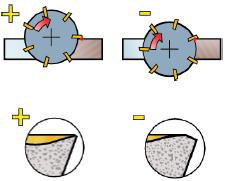
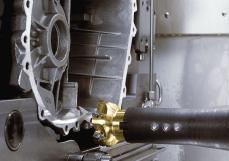
- 얇은 부분의 모서리에서 평면 밀링 가공을 위해 커터를 중앙에서 벗어나게 배치하십시오. 절삭이 부드러워지고 절삭 부하가 벽을 따라 더욱 균일하게 전달되면서 진동의 위험이 줄어듭니다.
- 절삭면에 항상 한개 이상의 인서트를 유지하는 커터 피치를 선택하십시오.
- 최대한 가벼운 인서트 형상을 사용하십시오(중절삭 대신 경절삭, 또는 강력절삭 대신 중절삭 사용).
- 벽이 얇은 가공물의 진동을 최소화하려면 작은 인서트 반경과 짧은 평행 랜드를 선택하십시오.
- 낮은 절삭 조건, 작은 절입 깊이, ap, 낮은 날당 이송, fz을 사용하십시오.
적용 체크 리스트 및 힌트
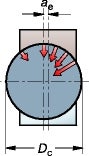
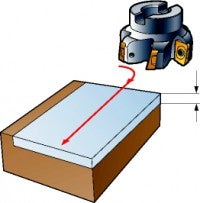
롤 인(roll in) 진입
- 기계 안정성, 스핀들 크기 및 유형(수직 또는 수평), 사용 가능 동력 고려하십시오.
- 공작물보다 20~50% 큰 커터 직경을 사용하십시오.
- 최적의 이송을 위한 커터 위치 설정 시 최대 칩 두께를 고려하십시오.
- 출구에서 가장 얇은 칩을 생성할 수 있도록 커터를 중심에서 벗어나게 위치시키십시오.
- 양호한 칩 형성, 즉 두꺼운 칩에서 얇은 칩으로 하향 밀링 적용
- 부드러운 진입을 위해 커터를 롤인 또는 이송을 줄여 절입이 이루워지도록 프로그래밍하십시요.
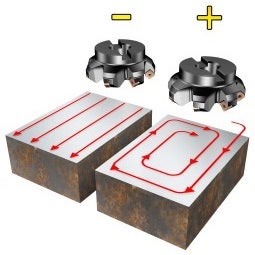
커터 맞물림을 유지하십시오.
- 양호한 칩 형성, 즉 두꺼운 칩에서 얇은 칩으로 하향 밀링 적용
- 공구 프로그래밍을 통한 진입 및 진출 방지
- 가능한 가공물을 자주 진입 및 진출하는 것을 피해야합니다. 절삭날에 바람직하지 않은 응력이 생기거나 드웰 및 채터 성향이 발생할 수 있습니다. 여러번 평행 패스를 수행하는 대신 밀링 커터를 완전 접촉 상태로 유지하는 공구 경로를 프로그래밍하는 것이 좋습니다. 방향을 변경할 때는 커터 맞물림이 지속되도록 작은 반경 방향 공구 경로를 포함하십시오.
고이송 밀링 가공
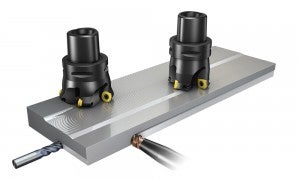
성공적인 고이송 밀링 가공이란? 알루미늄을 가공할 때, 그리고 CBN 또는 세라믹 인서트로 주철을 가공할 때 분당 1000 m 이상의 절삭 속도를 사용할 수 있으며, 이 경우 테이블 이송값이 크게 증가합니다. 이러한 가공을 고속 가공(HSM)이라고 합니다.
회주철과 같은 짧은 치핑 소재를 밀링 가공할 경우 엑스트라 크로스 피치가 적용된 평면 밀링 커터를 이용하여 테이블 이송을 높일 수 있습니다. 일반적으로 절삭 속도가 낮은 HRSA 소재에서는 엑스트라 크로스 피치를 사용하면 테이블 이송이 높아집니다.
절입각이 작은 커터를 사용하거나 원형 인서트 커터를 사용하면 칩을 얇게 만드는 효과가 있어서 매우 빠른 날당 이송(4 mm/날 까지)으로 평면 밀링 가공이 가능합니다. 절입 깊이가 2.8 mm 미만으로 제한되더라도 극대화된 이송은 생산성이 높은 밀링 방법입니다. 특정 커터 컨셉은 작은 축 방향 절입 깊이에서 최대한의 고이송 밀링을 위해 최적화되었습니다. 작은 절입각은 가볍고 빠른 고이송을 적용하기 위해 필요한 전제 조건입니다.
공구 선택
고이송 커터 | 원형 인서트 커터 | 중삭 HF | ||||
최대 절입 깊이(ap), mm | 1.2 - 2 | 1.3 | 1.3 | 10 | 7/8 | 2.8 |
커터 직경 (Dc), mm | 25 - 160 | 10 - 25 | 4 - 20 | 25 - 160 | 10 - 42 / 25 - 125 | 63 - 160 |
소재 | ![]() | ![]() | ![]() | ![]() | ![]() | ![]() |
고이송 커터:
- 절입각 10°를 적용하여 생산성이 높은 고이송 평면 밀링 커터를 사용하면 날당 이송 fz 매우 높아집니다.
- 작은 절입 깊이 ap에서도 빠른 이송
- 고경도강의 고속 가공을 위한 최적화된 고정밀 공구
- 극대화된 이송률에서 윤곽 및 비대칭 형상의 황삭에서 준정삭까지 가공
주의: 원형 인서트 및 반경 방향 커터의 경우 고이송 밀링을 위해 ap 값이 항상 추천 최대값보다 훨씬 낮게 유지해야 합니다.
원형 인서트 커터:
- 감소된 축 방향 절삭에서 증가된 얇은 칩 효과
- 부드러운 절삭 수행
- 거칠거나 또는 가벼운 조건을 위한 범용 커터
적용 방법
절입각이 작은 커터
절입각이 매우 작은 커터를 사용하면 ap가 작을 때의 얇은 칩 효과 때문에 이송 fz을 크게 증가할 수 있습니다.
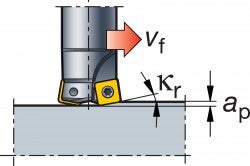
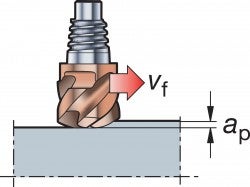
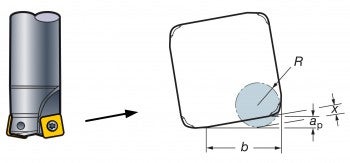
iC | 치수, mm | 절삭되지 않은 소재 | ||
iC | R | b | ap | x |
9 | 2.5 | 7.05 | 1.2 | 0.79 |
14 | 3.5 | 12.0 | 2.0 | 1.48 |
절입각이 작아지면 최대 칩 두께가 크게 줄어듭니다. 따라서 인서트에 대한 과부하 없이 매우 높은 이송을 사용할 수 있습니다.
주의: 낮은 절입 각도의 긍정적인 효과가 손실될 수 있기 때문에 90° 직각에 대한 가공은 하지마십시요. 즉, 절삭 깊이가 급격히 증가합니다.
항상 그렇듯이 특정 조건에 따라 이송 속도를 줄이고 적용해야하며 진동을 방지해야 합니다. 이로 인해 인서트가 손상될 수 있습니다.
원형 인서트 커터
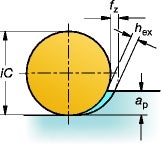
칩 두께 hex는 원형 인서트와 절입 깊이 ap에 따라 달라집니다. 원형 인서트 커터로 고이송 밀링 기술을 사용할 때, 절입 깊이는 낮게 유지되어야합니다. (최대 인서트 직경, iC의 10% 이내로 절입 깊이를 유지해야 하며, 그렇지 않으면 칩이 얇아지는 효과가 반감되어 이송을 줄여야합니다(그림 참조).
주의: 원형 인서트 커터를 사용할 때는 벽/직각에 접근하면서 절입 깊이가 갑자기 깊어지므로 이송률을 낮춰야 합니다.
일반 황삭을 위한 강력한 인서트
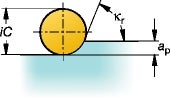
원형 인서트, 칩 부하, 절입각은 절입 깊이에 따라 달라집니다. 절입 깊이가 인서트 직경, iC의 25% 이내일 때 최상의 결과를 얻을 수 있습니다.
중절삭 평면 밀링 가공
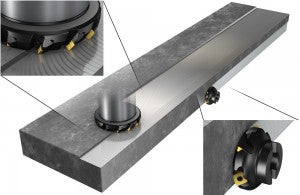
성공적인 중절삭 평면 밀링 가공이란?
중절삭 평면 밀링 어플리케이션은 대형 갠트리 밀 및 강력한 밀링 기계 또는 머시닝 센터에 무거운 단조물 또는 열간 압연 소재 블랭크, 주조물 및 용접 구조물의 거친 밀링을 포함합니다. 많은 량의 소재를 제거하면서 고온 및 높은 절삭 부하가 발생하여 밀링 인서트에 특정 요구사항이 발생합니다.
- 전체 절입 깊이에서 메인 날에 가해지는 무거운 부하
- 절입 깊이가 0에 가까워지면서 코너 부위에 마멸 마모
중절삭 밀링 커터를 사용할 경우 최적의 절입각은 60º입니다. 이 디자인의 장점은 다음과 같습니다.
- 우수한 절삭 능력, 상대적으로 절삭력 및 칩을 얇게하는 효과가있어 고이송 가능
- 디자인의 축 방향 여유 덕분에 인서트는 평행한 페럴 랜드를 갖게되어 양호한 표면 조도 처리 가능
공구 선택
중절삭 평면 밀링 커터 | ||||
절입각(κr), mm | 60° | 45° | 90° | 원형 인서트 |
최대 절입 깊이(ap), mm | 13/18 | 10 | 15.7 | 12.5 |
커터 직경 (Dc), mm | 160 - 500 | 80 - 250 | 40 - 200 | 66 - 200 |
소재 | ![]() | ![]() | ![]() | ![]() |
60° 중절삭 밀링 커터
- 효율적인 공구 핸들링을 위해 디자인되어 유지보수 시간이 짧고, 안정적이며, 신속한 인서트 인덱싱이 가능
- 고르지 않은 물결 모양의 금속 표면도 쉽게 제거 및 가공할 수 있도록 최대 18mm까지 절삭 가능
- 높은 생산성(날당 이송률 0.4 – 0.7 mm)
- 여유 있는 평행 랜드가 적용되어 준정삭 결과 향상
- 작은 절입 깊이에서 문질러진 표면에 견딜 수 있는 튼튼한 인서트 코너
- 매우 까다로운 절삭에서 안전을 위한 커터 강도
45-90° 중형 밀링 커터
- 가장 가벼운 절삭 능력을 제공하는 중형 평면 밀링 커터
- 0.2 – 0.6 mm의 이송 범위에서 6-8 mm 깊이의 절입 가능
- 대형 머시닝 센터의 까다로운 조건에 적합
- 와이퍼 인서트와 함께 사용하여 밀링 가공에서 표면 조도 개선
- 중형 평면 및 직각 밀링에서 우선 추천
대형 원형 인서트 커터
- 표피 제거와 단속과 같은 거친 밀링 조건에서 튼튼한 날이 있는 중형 커터 둥근 인서트 형상은 부드러운 절삭 작용을 제공
- 양호한 조건에서 8개의 절삭 날을 사용할 수 있음
- 최대 절입 깊이는 10 mm. 최대 추천 칩 두께는 인서트 형상 및 절입 깊이에 따라 날당 최대 0.55 mm 까지 다양
적용 방법
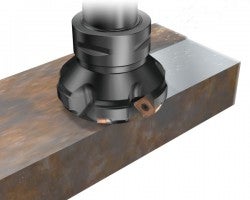
중절삭 작업에서는 대직경의 큰 인서트 커터가 사용됨. 절삭 속도는 표준이지만, 높은 ap 및 fz와 큰 ae가 결합하여 생산성이 매우 높음
절삭 진입
일반적으로 중절삭 밀링 가공에서 흔히 볼 수있는 까다로운 조건으로 인하여 절삭 부위로 진입하는 것이 항상 중요합니다.
- 가능하면 롤인 진입이 가능하도록 공구 경로를 프로그래밍하십시오.
- 그렇지 않으면 커터가 완전히 맞물릴 때까지 이송을 줄이십시오.
커터 위치 및 크기
넓은 표면을 밀링 가공하기 위해 여러 번의 패스가 필요한 중절삭 밀링에서는 다음과 같은 추천사항을 따르는 것이 중요합니다.
- 커터 위치 및 맞물림
- 공작 기계 용량 대비 커터 크기
- 불리한 진출을 피하기 위한 공구 경로
고온 관찰
까다로운 중절삭 밀링에서는 온도가 크게 상승합니다. 마그네틱 테이블을 사용하여 가공물을 고정할 때는 발생하는 칩의 많은 양이 커터 주변에 자주 남아있는 경우가 많습니다. 이로 인해 칩의 단속 또는 부분적인 칩 배출과 재절삭이 발생하면서 공구 수명에 악영향을 주게 됩니다. 이를 방지하려면 작업 영역에 칩을 깨끗하게 치우십시오. 절입 깊이를 깊게 하여 표면 접촉점을 인서트의 강한 모서리에 가깝게 이동시키면서 약한 인서트 코너가 스킨 및 스케일과 마찰하면서 마모되지 않게 하십시오.
주의: 커터에서 인서트를 인덱싱할 때는 열에 의한 화상을 피하기 위해 장갑을 착용하십시오.
와이퍼 인서트를 사용한 정삭
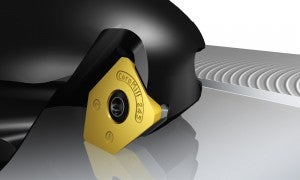
평면 밀링 가공에서 표면 조도를 높이는 방법
표준 인서트와 하나 이상의 와이퍼 인서트를 함께 사용하면 표면 조도를 크게 높일 수 있습니다. 와이퍼 인서트는 고이송 엑스트라 크로스 피치의 큰 직경 커터에서 회전당 이송(fn)이 높을 때 성능이 극대화됩니다.
우수한 표면 품질을 유지하면서 회전당 이송을 약 4배 늘릴 수 있습니다. 일반적으로 와이퍼 인서트는 우수한 표면 품질을 위해 소재를 평면 밀링 가공할 때 사용할 수 있으며, 열악한 조건에서도 사용 가능합니다.
공구 선택
커터 | ||||||
절입각(Kr), mm | 45° | 45° | 65° | 90° | 25° | 90° |
최대 절입 깊이(ap), mm | 6 | 10 | 6 | 10 | 0.9 | 8.1 |
커터 직경 (Dc), mm | 40 - 250 | 32 - 250 | 40 - 250 | 40 - 200 | 80 - 250 | 125 - 500 |
표면 조도(Ra) | < 1.0 | < 1.0 | < 1.0 | < 1.0 | < 1.0 | < 1.0 |
소재 | ![]() | ![]() | ![]() | ![]() | ![]() | ![]() |
와이퍼 날 인서트는 다양한 길이(Bs)로 제공되며, 각 인서트에 우승수 및 좌승수 버전이 있습니다. 대부분의 가공물 소재에서 재종을 사용할 수 있습니다. 조정식 인서트 시트는 커터 개념이 정삭용 커터를 위해 특별히 개발되거나 또는 카세트 솔루션을 제공할 때 특정 인서트 시트에 공통적으로 사용됩니다.
적용 방법
대형 평면 밀링 커터가 사용되는 정삭 작업에서 이송 fz은 일반적으로 낮게 유지되어야 합니다. 하지만 와이퍼 인서트가 장착된 커터를 사용하면 표면 품질을 유지하면서도 이송률을 2~3배 높일 수 있습니다.
고이송 경면 정삭
표면 거칠기 | ||
![]() | 이송 fn | |
fn1 <= 0.8 * bs1 | fn2 <= 0.6 * bs2 |
A : 표준 인서트만
B : 와이퍼 인서트 1개 사용
C : fn = 회전당 이송
bs1 | bs2 | |
![]() |
- 표준 인서트에서 fn이 평행 랜드 길이 Bs의 80%를 초과하면 와이퍼 절삭 날이 표면 품질을 향상됩니다.
- 인서트가 많은 대직경 커터를 사용할 때는 회전당 이송 fn이 증가할 때 표면 품질을 유지하기 위한 와이퍼 인서트를 반드시 사용해야 합니다.
- 스핀들 경사도, 커터 크기, 장착 및 설정 정확도에 따라 커터의 축 방향 런아웃이 가공면의 파상도에 영향을 줍니다. 크라운 와이퍼 랜드를 사용하면 평평한 표면을 만들 수 있습니다. 회전당 이송은 와이퍼 랜드의 60%로 제한됩니다.
- 와이퍼 랜드는 고정 인서트 시트가 있는 커터에 장착하면 밀링 인서트 아래로 약 0.05 mm정도 돌출합니다. 카세트 디자인 커터의 경우 와이퍼 절삭 날을 항상 이 위치로 매우 정확하게 조정할 수 있습니다. 돌출부는 기존 인서트보다 더 큰 부하를 와이퍼 인서트에 가하며, 이를 통해 진동이 발생할 수 있습니다. 따라서 와이퍼는 적당한 절입 깊이와 제한된 수로 경절삭 가공에서 사용해야 합니다.
- 축 방향의 부하를 제한하고 진동의 위험을 줄이려면 절입 깊이를 얕게 하십시오. 정삭 작업 때 추천 축 방향 절입 깊이는 0.5–1.0 mm입니다.
- 와이퍼 인서트를 장착할 때는 긴 절삭날을 올바르게 배치하려면 특별한 주의가 필요합니다.
예:
- 인서트에서 평행 랜드 Bs의 폭은 1.5 mm입니다.
- 커터에 인서트가 10개 있으며, 날당 이송 fz은 0.3 mm입니다. 따라서 회전당 이송 fn은 평행 랜드 길이의 두 배인 3 mm입니다.
- 표면 조도의 품질을 높이려면 회전당 이송이 1.5 mm의 80%인 1.2 mm 이하여야 합니다.
- 이에 따른 와이퍼 인서트는 평행 랜드의 폭이 약 8 mm입니다.
- 결과: 회전당 이송은 1.2 mm에서 8 mm의 60%인 4.8 mm로 증가할 수 있습니다.
주의: 기계 출력과 같은 다른 제한사항도 고려해야 합니다.
적용 체크 리스트 및 힌트
'경면 정삭'을 위한 힌트:
- 표면의 광택을 높이기 위해 고속 절삭 및 서멧 인서트를 사용하십시오.
- ISO M 및 S 소재의 점착성을 위해 절삭유 또는 오일 미스트를 사용하십시오.
- 날이 날카롭고 ap가 0.5–0.8 mm인 PVD 코팅 인서트에서는 표면 조도가 극대화됩니다.
- 작업 인서트로 사용하는 와이퍼 인서트는 가급적이면 동일한 재종을 사용하십시오.
홈 또는 슬롯 밀링 가공
일반적으로 홈 또는 슬롯 밀링 가공에서는 엔드밀 가공보다 사이드 및 평면 밀링을 선호합니다. 슬롯 또는 홈은 짧거나 길거나, 닫혀 있거나 열려... chevron_right
슬라이싱 방법
슬라이싱과 트로코이드 밀링 가공은 원래 고경도 강, ISO H 및 HRSA 소재, ISO S 같은 난삭재의 황삭 및 준황삭 가공을 위해 개발되었지만,... chevron_right
선삭에서 가공물의 품질을 높이는 방법
선삭 가공물의 품질을 높이려면 칩 컨트롤이 고려해야 할 가장 중요한 요소 중 하나입니다. 올바른 절삭 조건을 선택하고 좋은 부품 품질을 위한 적용... chevron_right
직각 밀링
직각 밀링에 포함되는 작업은 다음과 같습니다. 직각/평면 밀링 가공 엣지 원주 밀링 가공 얇은 편향 벽의 직각 밀링 가공 직각/평면 밀링... chevron_right