내경 선삭 가공
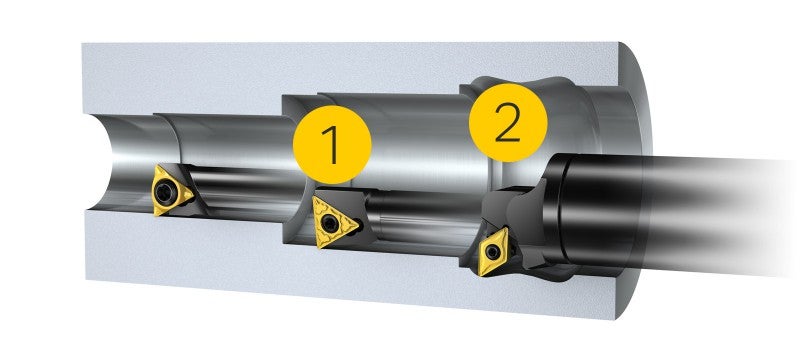
내경 선삭 가공은 가공물의 내경을 가공합니다. 긴 오버행과 칩 배출의 어려움은 내경 선삭 가공의 대표적인 문제입니다. 오버행이 길면 편향과 진동 문제가 모두 발생할 수 있습니다. 진동과 칩 배출 불량으로 인서트 파손이 발생할 수 있습니다. 또한 칩 배출 문제는 표면 조도 불량의 원인이 될 수도 있습니다.
내경 선삭 가공의 기본 적용 영역은 축 방향 선삭 가공(1)과 프로파일 선삭 가공(2)입니다.
축 방향 선삭 가공
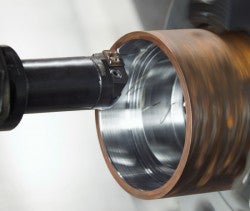
공구 선택이 가공물의 홀 직경과 길이(홀 깊이와 오버행)에 의해 큰 제약을 받습니다. 일반적인 규칙은 가장 짧은 오버행과 가능한 가장 큰 공구 크기를 가진 공구를 선택하는 것입니다.
작업에 맞는 올바른 공구를 선택해 올바르게 적용하고 적합하게 클램핑하면 공구 편향과 진동을 최소화할 수 있습니다.
인서트 모양
내경 선삭 가공에서는 네거티브 인서트에 비해 절삭 부하가 낮은 포지티브 기본 형상 인서트를 사용하는 것이 유리합니다. 작은 노즈 각도뿐만 아니라 작은 노즈 반경도 절삭력 감소에 기여합니다.
절입각
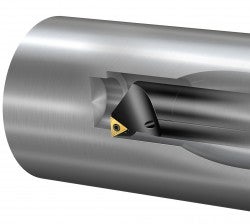
절입각은 축 방향 및 반경 방향 부하의 방향과 크기에 영향을 줍니다. 큰 절입각(작은 리드각)은 큰 축 방향 절삭 부하를, 작은 절입각(큰 리드각)은 큰 반경 방향 절삭 부하를 발생시킵니다. 90°(0°의 리드각)에 가깝고 75°(15°의 리드각) 이상인 절입각이 권장됩니다.
공구 홀더
가공물에 가공할 직각이 있으면 절입각이 91–95°(-1 ~ -5°의 리드각)인 공구를 선택하십시오. 삼각형 또는 D- 스타일(55°) 인서트를 사용할 것을 권장합니다.
더 강한 날이 필요하면 C- 스타일(80°) 인서트를 선택하십시오.
가공할 직각이 없고 조건이 안정적이면 75°의 절입각(15°의 리드각)에서 사각형 인서트를 사용해 생산성을 높이십시오.축 방향 선삭 가공용 공구
프로파일 선삭 가공
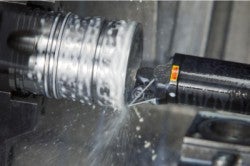
내경 프로파일 가공에서는 공구가 반경 방향 절삭 부하와 탄젠셜 절삭 부하 모두에 노출됩니다. 반경 방향 절삭 부하는 공구를 가공물로부터 멀리 편향시키고 탄젠셜 부하는 공구를 중심선으로부터 멀어지게 아래로 누릅니다.
소직경 홀을 보링 가공할 때는 공구와 홀 안쪽벽 사이의 접촉을 피할 수 있도록 인서트 여유각이 충분히 커야 합니다.
인서트 모양
프로파일 선삭 가공에서는 절입 깊이, 이송 및 속도에 따라 절삭이 변할 수 있습니다. 인서트의 가장 적합한 노즈 각은 강성, 비용 효율성 및 접근성을 위해 선택해야 합니다. 가장 자주 사용되는 노즈 각은 55°와 35°입니다.
절입각
절입각과 인서트 노즈 반경은 모두 접근성을 위해 중요한 요소입니다. 가장 적합한 카피 각도를 선택하려면 가공물 프로파일을 분석해야 합니다.
가공물과 인서트 사이에 최소 2°의 여유각을 유지해야 합니다. 그러나 표면 조도 및 공구 수명과 관련된 이유로 최소 7°를 권장합니다.
공구 홀더
우선 추천은 절입각이 93°(-3°의 리드각)인 공구와 D- 스타일(55°) 인서트입니다. 더 큰 램핑 각도가 필요하면 V- 스타일(35°) 인서트를 사용하십시오.
단면을 프로파일 가공하거나 코너 릴리프를 만들려면 절입각이 107–117°(-17 ~ -27°의 리드각)인 홀더를 선택하십시오.
역방향 보링 가공을 위한, 특히 반대 방향으로 직각을 가공하도록 설계된 공구가 있습니다.
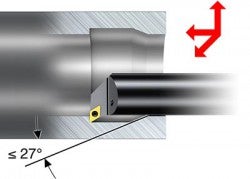

외경 선삭 가공
외경 선삭 가공은 가공물의 외경을 가공합니다. 외경 선삭 가공이 가장 잘 알려지고 일반적으로 사용되는 공정 중 하나이기 때문에 칩 컨트롤, 공정... chevron_right
램핑 가공: 2축 선형 및 원호
성공적인 램핑 가공이란? 선형 램핑 가공 은 막힌 슬롯/포켓/캐비티을 가공할 때 가공물에 접근하는 효율적이고 일반적으로 사용되는 방법이며, 드릴이... chevron_right
태핑 가공 팁
나사 태핑 방법 태핑 작업의 성공은 최종 제품의 품질에 영향을 미치는 모든 요소에 의해 결정됩니다. 다음에 유의해 효율적인 나사 태핑 가공을 수행하십시오. 가공물... chevron_right
밀링
밀링 가공에서 성공적인 결과를 평가할 때는 공정 및 가공물 형상, 황삭 가공과 정삭 가공, 생산성 요구사항 대 가공물 품질(예: 치수 정확도, 기하학적... chevron_right