직각 밀링
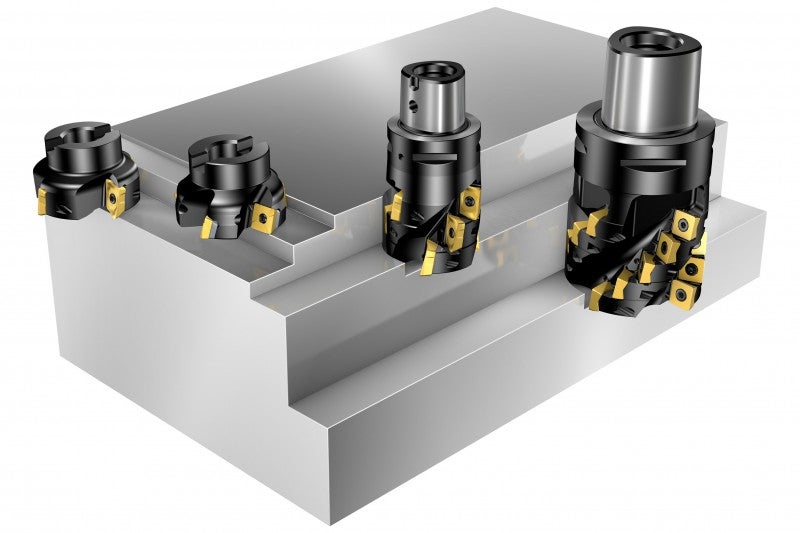
직각 밀링에 포함되는 작업은 다음과 같습니다.
- 직각/평면 밀링 가공
- 엣지 원주 밀링 가공
- 얇은 편향 벽의 직각 밀링 가공
직각/평면 밀링 가공
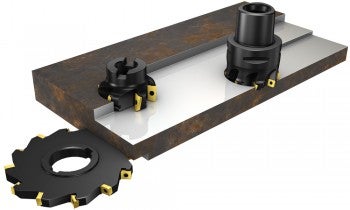
성공적인 직각/평면 밀링 가공이란?
직각 밀링에서는 두 개의 면을 동시에 가공하므로 평면 밀링과 함께 원주 밀링이 필요합니다. 진정한 90도 직각을 달성하는 것이 가장 중요한 요구사항 중 하나입니다. 직각 밀링은 전통적인 사각 직각 커터와 엔드 밀링 커터, 롱에지 커터, 사이드 및 평면 밀링 커터를 사용해 처리할 수 있습니다. 이와 같이 다양한 옵션으로 인해 최적의 선택을 하기 위하여 작업 요구사항을 신중하게 고려해야 합니다.
공구 선택
직각 밀링 커터
일반적으로 전통적인 디자인의 직각 평면 밀링 커터는 '정확한' 90도인 얕은 직각을 밀링할 수 있습니다. 많은 직각 평면 밀링 커터는 범용 커터이며, 홀을 만드는데 유용하게 사용될 수 있습니다. 축 방향으로 편향된면을 밀링 가공할 때 또는 수직면에 근접하게 밀링 가공할 때 직각 밀링 커터를 사용하면 효과적입니다.
엔드 밀링 커터
인서트 교환형 및 솔리드 초경 엔드밀은 접근성이 요구되는 직각에서 좋은 솔루션입니다.
롱에지 밀링 커터
일반적으로 롱에지 커터는 깊은 직각을 밀링 가공할 때 사용됩니다.
적용 방법
얕은 직각 밀링 가공
이 작업은 자주 사용되며, 일반적으로 직각 평면 밀링 및 엔드밀 커터로 처리합니다. 얕은 절삭에서는 반경이 더욱 큰 절삭이 가능합니다. 대부분의 경우, 특히 가공물에 가해지는 축 방향 압력이 제한적이고, 수직면 또는 지그 부분 근처에 접근해야 할 때 이러한 커터를 평면 밀링 커터 대신 사용할 수 있습니다. 오버사이즈 직각 커터 옵션을 이용하면 깊게 위치한 얕은 직각을 밀링 가공할 때 최적의 접근이 가능합니다.
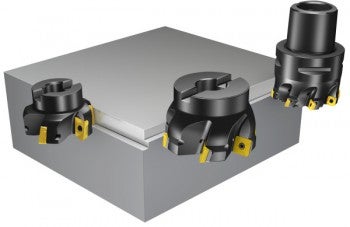
깊은 직각의 밀링 가공
직각 평면 밀링 커터와 엔드밀 커터를 이용해 패스를 반복하십시오. 패스 사이의 스캘럽과 이전 날 등의 표면 에러를 최소화하려면 정확한 90º 직각을 생성할 수 있는 고정밀 커터가 절대적으로 필요합니다. 직각 깊이가 절삭날 길이의 75%보다 얕으면 수직 표면의 품질이 우수하여 추가 정삭이 필요하지 않습니다.
롱에지 밀링 커터를 단일 패스에서 이용하십시오.
롱에지 커터는 더욱 깊고 크며 무거운 직각 밀링 작업에 적합한 솔루션입니다. 이 제품은 금속 제거 능력이 탁월하며, 일반적으로 표면 거칠기가 높은 이송에서 사이드 밀링을 특징으로하기 때문에 황삭 밀링 가공에서 사용됩니다.
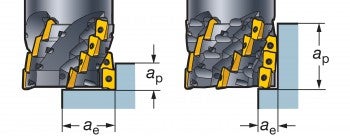
이 커터를 사용할 경우 충족해야 하는 요건은 다음과 같습니다.
- 안정성
- 스핀들 조건
- 칩 배출
- 홀딩 공구
- 출력
반경 방향 부하는 많은 부하를 만들어 까다로운 사이드 밀링 작업입니다.
짧아진 롱에지 커터는 다음과 같은 조건에 적합합니다.
- 반경이 크지만 얕은 직각
- 깊이가 직경과 동일하여 기계 한계를 보완하는 전체 슬롯 가공
길어진 모델은 다음과 같은 조건에 적합합니다.
- 반경 방향 깊이가 적당한 직각 밀링 가공
- 강력하면서 안정적인 기계에서 엣지 가공
깊은 위치의 직각 밀링 가공
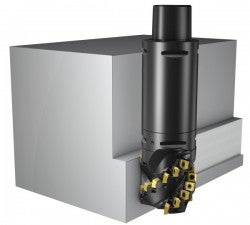
오버사이즈 직각 커터 옵션을 이용하면 깊게 위치한 얕은 직각을 밀링 가공할 때 최적의 접근이 가능합니다. 훨씬 더 깊은 위치의 직각을 가공할 때는 Coromant Capto 커플링과 확장 옵션을 사용하십시오. 롱에지 커터는 직각의 위치가 더욱 깊은 오버사이즈 모델에서도 사용할 수 있습니다. 하지만 반경 방향 절입 깊이는 더욱 제한됩니다.
적용 체크리스트 및 힌트
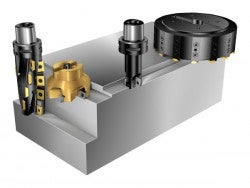
- 하향 밀링이 항상 첫 번째 방법이며, 90° 절입각 때문에 직각 밀링에서 특히 중요합니다.
- 가능하면 지그의 지지점 방향으로 절삭 부하를 전달하는 방식으로 가공을 진행해야 합니다. 따라서 일부 경우에는 상향 밀링이 효과적입니다.
- 커터 피치 선택은 기계 공구, 가공물 및 클램핑, 가공물 소재 등 전체 시스템의 안정성에 따라 달라집니다.
- ISO 40 기계 및 소형 기계에서는 안정성이 제한되므로 코스 피치 커터를 사용하는 것이 좋습니다.
- 코스 피치 커터는 정육면체 지그 위에 올린 가공물을 가공할 때도 추천합니다.
- 가공물에서 커터의 위치는 매우 중요하며 특히 주의해서 정해야 합니다.
- Dc/ae가 10보다 큰 경우 최상의 결과를 얻고 가장자리 파손을 방지하려면 hex 값에 따라 이송 fz을 조정해야 합니다.
- 직각 깊이가 절삭날 길이의 75%보다 얕으면 수직 표면의 품질이 우수하여 추가 정삭이 필요하지 않습니다.
- 평면 밀링보다 인성이 많은 초경 인서트 재종을 선택하십시요.
- 롱에지 커터를 사용할 경우 조건이 까다롭기 때문에, 인성이 더욱 많은 재종이 필요할 수 있습니다.
- 절삭이 깊어질수록 진동을 피하기 위해 더 낮은 절삭 속도를 선택하는 것이 중요합니다.
- 진동이 발생하면 vc를 낮추고 fz를 높인 다음, 권장 hex 값을 확인하십시오.
- 선택한 절삭 조건에서 기계 출력이 충분해야 합니다.
홀딩 공구
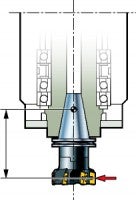
- 롱에지 커터를 이용해 많은 절삭을 할 때는 가공할 때 요구되는 출력에 특히 주의하십시오.
- 공구 장착은 50 mm보다 작은 커터의 밀링 가공 결과에 가장 큰 영향을 미치는 요소입니다.
- 절입 깊이가 깊을수록 커플링의 크기와 안정성이 더욱 중요합니다. 왜냐하면 직각 평면 밀링 커터를 사용할 때 반경 방향 부하가 상당하기 때문입니다.
- 모든 종류의 커터에서 안정성을 극대화하고 편향을 최소화하는 Coromant Capto 커플링을 사용하십시오. 이 방법은 길거나 연장된 툴링에서 특히 중요합니다.
롤인 진입
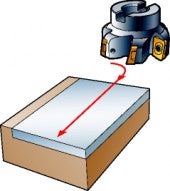
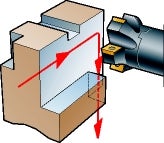
- 특히 직각 밀링 가공할 때 절삭 부위에 부드럽게 진입하는 것은 진동을 방지하고 공구 수명을 연장하는 데 도움이 됩니다.
- 커터가 롤인 형태로 진입하도록 프로그래밍하십시오. 진출부의 칩 두께는 항상 0이어야 합니다. 이를 통해 이송 증가와 공구 수명 연장이 가능합니다.
- 이 방법은 절삭의 급격한 변화를 피하기 때문에 외부 코너를 밀링하는 작업에 가장 적합합니다.
- 연속 절삭에서 커터를 맞물림 상태로 유지하십시오.
사이드 밀링 커터 및 평면 밀링 커터를 사용한 직각 밀링 가공
사이드 밀링 커터와 평면 밀링 커터는 직각 밀링에서도 사용되며, 특히 형상이 폭이 좁고 반경이 넓은 경우에 사용됩니다. 일반적으로 이 커터는 뒷쪽 면 직각 및 평면을 백 페이싱 가공할 때 유일한 해결책입니다.
우승수 | 좌승수 |
![]() |
외곽 엣지 밀링 가공
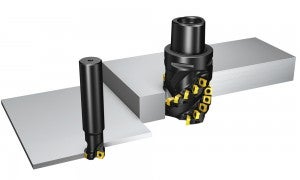
성공적인 외곽 엣지 밀링 가공이란?
엣지 가공은 윤곽 가공 공구 패스에서 적용되는 사이드 밀링 작업입니다. 사이드 밀링 및 엣지 가공은 외곽 밀링 가공의 옵션입니다.
공구 선택
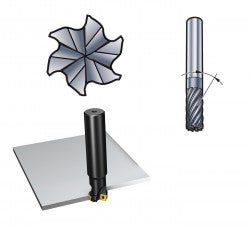
- 얇은 엣지는 일반적으로 엔드 밀링 커터에 의해 생성되지만, 더 깊거나 두꺼운 엣지는 반복되는 '직각 밀링' 패스를 사용하는 엔드밀 또는 단일 패스에서 롱에지 커터에 의해 생성됩니다.
- 깊이가 직경의 두 배인 직각은 롱에지 밀링 커터 또는 솔리드 초경 커터를 이용해 가공됩니다. 이러한 깊은 직각 또는 두꺼운 가공물 엣지의 경우 반경 0.5배의 절입 깊이가 권장됩니다.
- 사이드 및 평면 밀링 커터는 엣지 가공 또는 외곽 밀링 가공에서도 사용할 수 있습니다.
- 예를 들어 헬릭스가 크면 절삭에서 날의 개수가 충분하며, 반경 방향 절입 깊이가 얕으면 엣지 가공이 매끄럽게 이루어집니다.
- 크로스 피치 또는 엑스트라 크로스 피치 커터는 엣지 가공에 특히 적합합니다. 이는 90º 엔드밀을 사용하여 더욱 얇거나 얕은 엣지 직각을 가공할 때도 마찬가지입니다.
적용 방법
표면 형상 – 반경 방향으로 생성됨
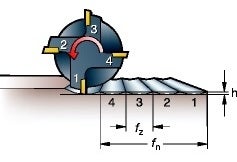
커터에 런아웃이 없으면 교두 높이 h가
동등하게 높아지며, 다음 공식을 이용해 계산할 수 있습니다.
프로파일 깊이/ 교두 높이
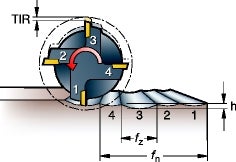
커터에서 런아웃이 발생하면 날당 이송 fz,
뒤이어 교두 높이 h가 TIR에 따라 달라집니다.
![]() | |
fz | fz 런아웃 |
앞서 설명한 것처럼, 표면 형상과 상승 성향은 특히 반경 방향 절입 깊이가 얕을 때 이송 속도를 제한할 수 있습니다.
프로파일 밀링을 위해 엔드밀의 측면을 사용하면 일련의 '교두'가 생성됩니다. 교구의 높이인 - h는 다음 조건에 의해 정해집니다.
- 커터 직경, Dc
- 날당 이송, fz
- 런아웃 공구 표시기 판독값(TIR)
인서트 교환형 커터는 항상 솔리드 초경 커터보다 TIR이 높습니다. 또한 커터 직경이 클수록 날 수가 많아져서 교두의 고점과 저점 사이가 멀어집니다.
최상의 표면 조도를 얻으려면 다음과 같이 하십시오.
- 솔리드 초경 커터를 사용하십시오.
- Coromant Capto 커플링과 함께 고정밀 파워 척을 사용하십시오.
- 최대한 짧은 오버행을 사용하십시오.
권장 이송(hex 무시):
- 인서트 교환형 커터, 시작값 fz = 0.15 mm/tooth
- 솔리드 초경 커터, 시작값 fz = 0.10 mm/tooth
주의: 커터의 잘못된 런아웃으로 인해 절삭날 하나에서만 표면이 생성되면 표면 품질이 최악 수준으로 떨어집니다.
적용 체크 리스트 및 힌트
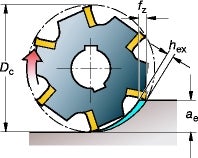
- 외곽 밀링에서는 최적의 날당 이송 fz을 찾는 것이 가장 중요한 요인 중 하나입니다.
- 이송값 fz가 칩 두께에 영향을 주는 커터 맞물림을 보완합니다.
- 날당 이송 fz은 보정 계수에 따라 증가합니다. 이렇게 하면 더 작은 맞물림 호로 더 높은 이송 속도를 제공 할뿐만 아니라 동시에 칩 두께가 충분히 커집니다. 하지만 보정 계수가 적용되지 않을 수 있습니다. 표면 형상과 상승 성향이 이송을 제한할 수 있습니다.
얇은 편향 벽의 직각 밀링 가공
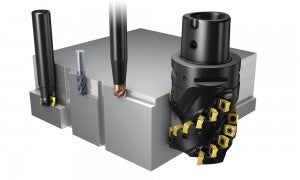
직각 밀링 가공 대상:
- 낮은 높이와 두께의 비율 < 15:1
- 적당한 높이와 두께의 비율 < 30:1
- 매우 큰 높이와 두께의 비율 > 30:1
- 얇은 박판 베이스
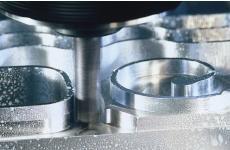
고려사항:
- 얇은 벽 단면의 가공 전략은 벽의 높이와 두께에 따라 달라집니다.
- 모든 경우에 패스 수는 벽 치수와 축 방향 절입 깊이에 따라 결정됩니다.
- 커터와 벽면의 안정성을 고려하십시오.
- 고속 가공 기법, 즉 작은 ap/ae와 높은 vc를 사용하면 공구 맞물림 시간이 줄어들고 그 결과로 충격과 편향도 줄어들기 때문에 얇은 벽 밀링 가공이 용이해집니다.
- 하향 밀링을 사용해야 합니다.
- 알루미늄 및 티타늄 밀링 가공에서도 동일한 방법을 사용합니다.
낮은 높이와 두께의 비율 < 15:1
패스를 지그재그 경로로 만들어야 합니다.
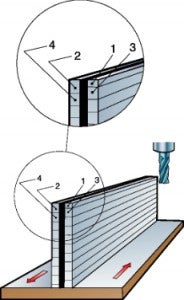
'얇은 벽' 밀링 가공
- 중첩되지 않는 패스로 벽의 한쪽 면을 가공합니다.
- 반대 면에서 위의 단계를 반복합니다.
- 후속 정삭 작업을 위해 양쪽면에 여유를 남깁니다.
적당한 높이와 두께의 비율 < 30:1
'워터라인' 밀링 가공:
- 오버래핑되지 않은 패스에서 한칸씩 걸러 주어진 깊이로 가공
스텝 지지 밀링 가공:
- 비슷한 접근법이지만 벽면 반대편 패스 간 겹치는 방법: 이는 가공 될 때 더 많은 지지를 제공합니다. 첫 번째 패스에서는 절입 깊이 ap/2가 줄어야 합니다.
- 어떤 경우든 0.2 – 1.0 mm 후속 정삭을 위해 양쪽에 여유를 남겨둡니다.
매우 큰 높이와 두께의 비율 > 30:1
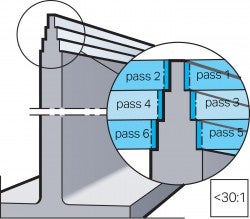
가공하는 동안 벽면을 교대로 만드는 것 외에도 '크리스마스 트리' 루틴을 사용하여 원하는 벽 두께에 단계별로 접근합니다.
- 더 얇은 부분을 가공할 때 항상 아래의 두꺼운 부분에 의해지지됩니다(아래 그림 참조)
- 이 계단 방식으로 벽을 아래로 이동하십시오.
얇은 벽
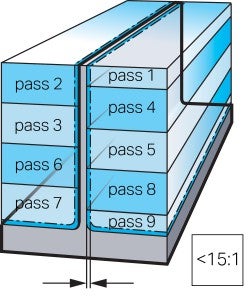
정삭 여유
워터라인
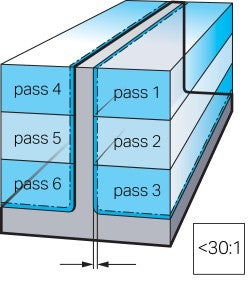
정삭 여유
얇은 벽
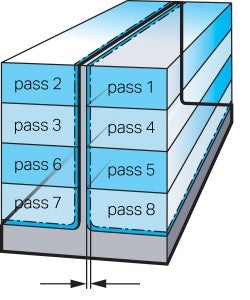
정삭 여유
얇은 벽으로된 베이스의 직각 밀링 가공
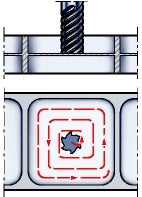
얇은 베이스 가공:
- 필요한 깊이까지 기본 영역의 중심에서 원호 램핑 가공을 사용하십시오.
- 원호 램핑 가공 경로에서 지점 바깥으로 밀링 가공하십시오.
이미 가공된 면의 반대면을 밀링 가공해야 하는 경우:
- 절삭날 수가 최소인 공구를 사용하십시오.
- 작업면에 가해지는 압력을 최소화하십시오.
부품의 베이스 중앙에 홀이 있는 경우:
- 첫 번째 면을 가공할 때 지지대를 제자리에 두십시오.
- 두 번째 면을 가공하십시오.
- 두 면을 모두 가공한 후에 지지대를 치우십시오.
홈 또는 슬롯 밀링 가공
일반적으로 홈 또는 슬롯 밀링 가공에서는 엔드밀 가공보다 사이드 및 평면 밀링을 선호합니다. 슬롯 또는 홈은 짧거나 길거나, 닫혀 있거나 열려... chevron_right
평면 밀링
평면 밀링 가공에 포함되는 작업 일반 평면 밀링 가공 고이송 밀링 가공 중절삭 평면 밀링 가공 와이퍼 인서트를 사용한 정삭 일반 평면 밀링... chevron_right
진동
밀링 가공에서 진동은 절삭 공구, 홀딩 공구, 기계, 가공물 또는 지그의 제한 사항 때문에 발생할 수 있습니다. 진동을 줄이기 위해 고려할 수 있는... chevron_right
문제 해결
다음 표에는 진동, 칩 걸림, 칩의 재절삭, 불만족스러운 표면 조도, 버 형성, 기계 동력, 공구 마모 등 밀링 문제 해결에 관한 정보가 나와 있습니다. 원인 해결책 진동 약한... chevron_right