프로파일 밀링 가공이란?
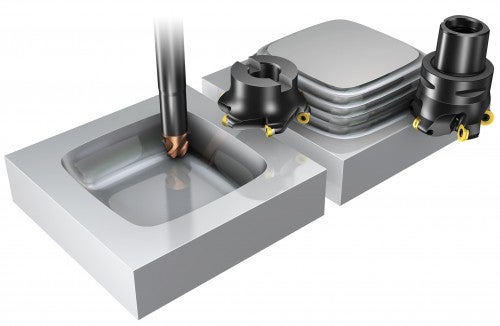
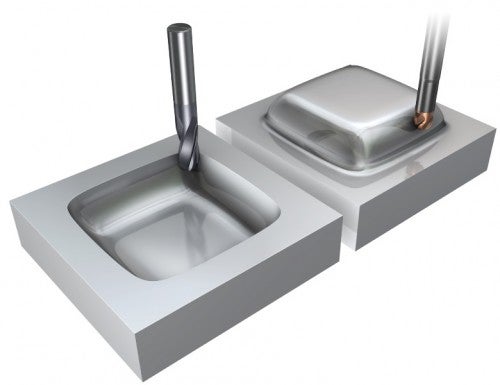
프로파일 밀링은 일반적인 밀링 가공입니다. 반경이 있는 원형 인서트 및 공구는 황삭 및 준황삭에 사용되는 밀링 커터이며, 볼 노즈 엔드밀은 정삭 및 슈퍼피니싱에서 사용되는 밀링 커터입니다.
프로파일 밀링 공정
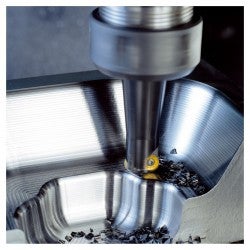
프로파일 밀링은 2차원 및 3차원에서 볼록 및 오목 모양을 다축 밀링 가공합니다. 가공물이 커지고 기계 구성이 복잡해지면 프로파일 밀링 공정 계획이 더욱 중요해집니다.
가공 공정은 다음과 같은 최소 3개의 작업 유형으로 구분됩니다:
- 황삭/준황삭
- 준정삭
- 정삭
종종 고속 가공 기술을 사용하여 수행되는 슈퍼피니싱이 필요할 수 있습니다. 나머지 부분을 밀링하는 일명 잔삭 밀링은 준정삭과 정삭에 포함됩니다. 최적의 정확도와 생산성을 위해 별도의 기계에서 황삭과 정삭을 수행하고 각 작업에 최적화된 절삭 공구를 사용하는 것이 좋습니다.
정삭 작업은 고급 소프트웨어 및 프로그래밍 기술이 적용된 4축/5축 공작 기계에서 수행해야 합니다. 이 작업을 통해 많은 시간이 소요되는 수작업을 상당히 줄이거나 완전히 없앨 수 있습니다. 최종 결과는 형상 정밀도와 더 높은 표면 구조 품질을 가진 제품이 될 것입니다.
공구 선택
황삭 및 준황삭에 최적화된 절삭 공구:
반경이 있는 원형 인서트 및 공구
정삭 및 슈퍼피니싱에 최적화된 절삭 공구:
반경이 있는 볼 노즈 엔드밀 및 공구
![]() | ![]() | ![]() | ![]() | |
원형 인서트 | 인서트 교환형 볼 노즈 | 헤드 교환형 볼 노즈 | 볼 노즈 솔리드 초경 | |
기계/스핀들 크기 | ISO 40, 50 | ISO 40, 50 | ISO 30, 40 | ISO 30, 40 |
안정성 요건 | 높음 | 중간 | 중간 | 낮음 |
황삭 | 매우 좋음 | 좋음 | 보통 | 보통 |
정삭 | 보통 | 보통 | 매우 좋음 | 매우 좋음 |
절입 깊이 ap | 중간 | 중간 | 얕음 | 얕음 |
다목적성 | 매우 좋음 | 매우 좋음 | 매우 좋음 | 매우 좋음 |
생산성 | 매우 좋음 | 좋음 | 좋음 | 좋음 |
프로파일 밀링을 위한 체크리스트
적절한 공구를 선택하고 최적의 가공 방법을 찾으려면 가공물의 프로파일을 신중하게 분석해야 합니다.
- 최소 반경 및 최대 캐비티 깊이 정의
- 소재에서 제거할 양을 미리 확인하십시오.
- 진동 방지를 위해 가능하면 공구 셋업과 가공물 클램핑을 고려하십시오. 모든 가공은 최적화된 기계에서 수행되어야 프로파일에 대한 기하학적 정밀도가 향상됩니다.
- 정삭 및 슈퍼피니싱 작업을 위해 별도의 정밀한 공작 기계를 사용함으로써 많은 시간이 소요되는 수동 폴리싱의 필요성을 줄이거나 경우에 따라 완전히 없앨 수 있습니다.
- 작업시간을 크게 줄이려면 일부 고급 프로그래밍이 필요할 수 있습니다. 고속 가공 기술로 솔리드 초경 엔드밀을 사용하여 그물 모양을 가공하여 최고의 사상면을 얻으십시요.
- 일반적으로 대형 가공물을 황삭 및 준정삭 가공할 때는 기존의 방법과 툴링을 사용해야 생산성이 높아집니다. 예외적으로 알루미늄은 절삭 속도가 빠르기 때문에 황삭에도 사용됩니다.
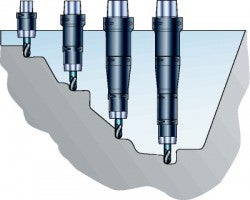
진동을 줄이는 방법
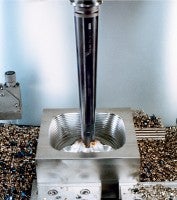
진동은 긴 오버행을 사용하여 깊은 프로파일을 밀링 가공할 때 장애가 됩니다. 이 문제를 극복하기 위한 일반적인 방법은 절입 깊이, 속도 또는 이송을 줄이는 것입니다.
- 견고한 모듈러 공구를 사용하여 런아웃 정밀도를 높임
- 모듈러 공구를 사용하면 유연성과 사용 가능한 조합의 수가 증가
- 게이지 라인에서 절삭날의 가장 낮은 지점까지를 나타내는 전체 공구 길이가 게이지 라인에서 직경의 4-5 배를 초과하는 경우 진동방지 공구 또는 연장 바를 사용
- 굽힘 강성을 급격히 높여야 하는 경우에는 헤비 메탈로 만든 연장 바를 사용
- 스핀들 속도 20,000 rpm 이상을 위한 밸런싱된 공구 및 홀딩 공구 사용
- 커터 직경과 비교하여 연장부 및 어댑터에서 최대한 큰 직경을 선택
- 홀딩 툴과 절삭 공구의 반지름 차이는 1 mm (0.039 inch)면 충분합니다. 오버사이즈 커터를 사용하십시오.
- 플런지 밀링은 긴 공구를 사용하여 밀링할 수 있는 대체 방법
점차적으로 공구 길이 연장
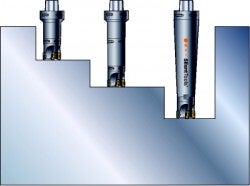

마지막 패스가 가공물 깊이 들어가는 황삭 작업에서 최대의 생산성을 유지하려면 커터에 일련의 확장 옵션을 적용해야 합니다.
- 연장부가 길면 생산성이 저하되고 진동을 발생시킬 수 있으므로 처음에는 가장 짧은 길이를 사용하십시오.
- 프로그램에서 사전 결정된 위치에서 확장된 공구로 변경하십시오. 캐비티 형상에 따라 변경 지점이 달라집니다.
- 최고의 생산성을 유지할 수 있도록 각 공구 길이에 맞게 절삭 조건 사용
실제 절삭 속도
볼 노즈 또는 원형 인서트 커터의 절삭 속도를 계산할 때 공구의 직경값을 사용하면 실제 절삭 속도 vc가 훨씬 더 낮습니다. 단, 절입 깊이 ap가 얕은 경우만 해당. 테이블 이송 및 생산성이 크게 저하됩니다.
가공 때 실제 또는 유효 직경 Dcap에 대한 절삭 속도의 기본 계산,
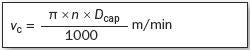
직각 엔드밀
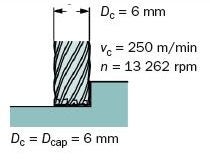
볼 노즈 커터
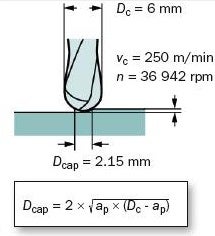
원형 인서트 커터
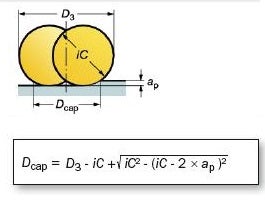
포인트 밀링 가공 – 경사진 커터
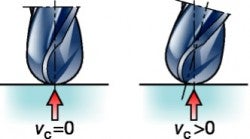
볼 노즈 엔드밀을 사용할 때 절삭날에서 가장 예민한 부분은 절삭 속도가 제로에 가깝고 절삭 과정에 바람직하지 않은 공구 중심부입니다. 치즐 에지의 좁은 공간 때문에 툴 센터에서 칩 배출이 중요합니다.
따라서 스핀들 또는 가공물을 10~15도 기울여서 공구 중심에서 절삭 영역을 멀리 이동시키는 것이 좋습니다.
- 최소 절삭 속도 상승
- 향상된 공구 수명 및 칩 형성
- 표면 조도 향상
센터 절삭 커터의 예
중심 부분, z = 2
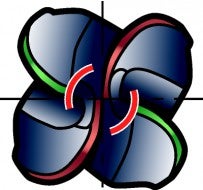
원주 부분, z = 4
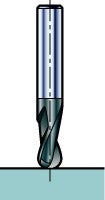
Z = 2
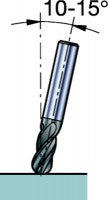
Z = 4
얕은 절삭
낮은 절입 깊이에서 원형 인서트 또는 볼 노즈 커터를 사용하는 경우 절삭날의 짧은 맞물림 시간 때문에 절삭 속도 vc를 증가시킬 수 있습니다. 절삭 영역에서 열 확산 시간은 짧아지고, 즉 절삭날과 가공물 온도는 모두 낮게 유지됩니다. 또한 칩이 얇아지는 효과로 인해 날당 이송 fz을 증가시킬 수 있습니다.
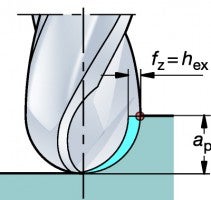
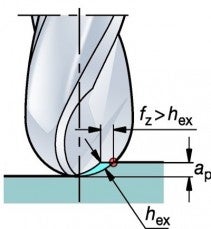
얕은 절삭
예를 들어 얕은 절삭, 기울어지지 않은 커터와 기울어진 커터 비교
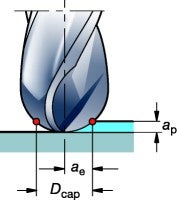
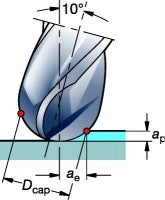
이 예는 ae/ap가 작고 절삭 속도를 높일 수 있는 방법과 기울어진 커터를 사용할 때의 이점도 있습니다.
볼 노즈 솔리드 초경
Dc = 10 mm, 재종 GC 1610.
소재: 강, 400HB
깊은 절삭 ap - Dc/2의 추천 절삭 데이터:
vc = 170 m/min
fz = 0.08 mm/r = hex
ap준정삭 - 2 mm (0.079 inch) vc - 300 m/min (984 ft/min) 얕은 절삭과 짧은 맞물림 시간으로 절삭 속도를 약 | vc hex vf Dc = 10 mm (0.394 inch) | vc hex vf Dc = 10 mm (0.394 inch) |
vc - 5 * 170 - 850 m/min (557–2789 ft/min) 주의: fz ae슈퍼피니싱 - 0.1 mm | 슈퍼피니싱에서는 기울어지지 않은 커터를 사용하지 않는 것이 좋습니다. | vc hex vf Dc = 10 mm (0.394 inch) |
프로파일 밀링의 생산성: 일정한 스톡
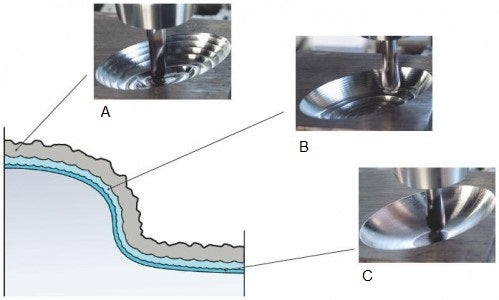
A: 황삭
B: 준정삭
C: 정삭 및 슈퍼피니싱
프로파일 밀링 가공, 특히 고속에서 가공할 때 높고 일관된 생산성을 결정하는 기준 중 하나는 일정한 스톡입니다.
- 금형 제작에서 공통인 이러한 작업에서 생산성을 극대화하려면 밀링 커터의 크기를 특정 작업에 맞추는 것이 중요합니다.
- 주요 목표는 사용된 공구별로 작업 부하 및 방향의 변화가 거의 없도록 균일하게 분산된 작업 여유 또는 스톡을 구현하는 것입니다.
각 공정별로 한개의 커터 직경을 사용하는 대신, 커터의 크기를 크게, 작게, 특히 경황삭 및 준정삭에서는 커터 크기를 낮추는 것이 유리할 수 있습니다.
- 선행 작업에서 가능한 일정한 양으로 최대한 적은 스톡이 유지되면 정삭 가공에서 최고의 품질을 달성합니다.
- 최종 형상 요건에 최대한 근접하는 것을 목표로 삼아야 합니다.
- 안전한 절삭 공정
일정한 스톡의 이점
- 일부 준정삭 및 실질적인 모든 정삭은 부분 유인 작업이나 때로는 무인 작업으로 진행할 할 수 있습니다.
- 공작 기계 가이드 웨이, 볼 스크류 및 스핀들 베어링에 미치는 부정적인 영향이 감소합니다.
솔리드 가공물 기초 가공
- 캐비티를 기초 가공할 때는 ap를 최소화하고 후속 프로파일 밀링에서 일정한 스톡을 남기는 방법을 선택해야 합니다.
- 직각면/엔드밀 또는 롱에지 커터는 제거해야 하는 스톡을 계단식으로 남깁니다. 그 결과 절삭 부하 변화와 공구 휨이 발생하며, 정삭에서 최종 모양의 기하학적 정밀도에 영향을 주는 불균일한 스톡이 발생합니다.
- 원형 인서트 커터를 사용하면 패스 간의 부드러운 전환이 발생하고 프로파일링 작업에 더 적은 양의 스톡이 남겨져 더 좋은 가공물 품질을 얻을 수 있습니다.
- 세 번째 대안은 고이송 커터를 사용해 캐비티를 기초 가공하는 방법입니다. 이 방법을 사용하면 절입 깊이가 얕아서(계단형 스텝이 작아서) 적은 스톡이 일정하게 발생합니다.
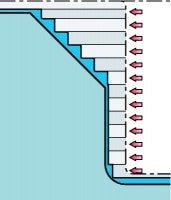
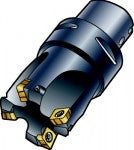
사각 직각 커터,
크고 균일하지 않은 스톡이 남음
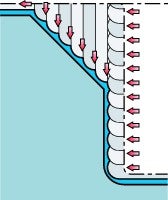
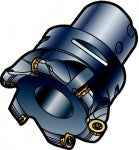
원형 인서트 커터,
작은 스톡이 남음
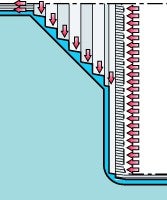
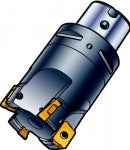
고 이송 커터,
작은 스톡이 남음
카피 밀링 가공
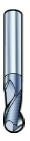
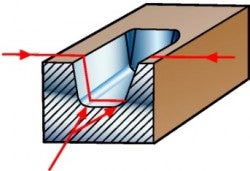
캐비티에 대한 공구 경로를 프로그래밍할 때 전통적이고 쉬운 기존 방법은 소재에 많은 진입구와 진출부가있는 일반 카피 밀링 기술을 사용하는 것입니다. 하지만, 이렇게 하려면 강력한 소프트웨어 프로그램, 기계 및 절삭 공구가 매우 제한된 방식으로 사용된다는 것을 의미합니다. 공구 경로 편차를 방지하려면 미리보기 기능이 있는 소프트웨어가 설치된 기계를 사용하는 것이 좋습니다.
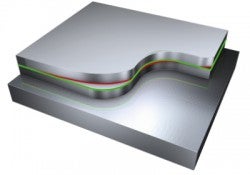
가공 방법, 공구 경로, 밀링 및 홀딩 공구를 선택할 때는 유연한 생각이 필요합니다.
− 인서트 중심 지점에 큰 부하가 가해짐
− 이송 감소
− 공구 수명 단축
− 기계적 영향
− 형상 에러
− 프로그램 및 절삭 시간 연장
카피 밀링 공구 경로는 주로 상향 밀링과 하향 밀링을 결합한 것으로서,절삭 시 바람직하지 않은 맞물림과 벗어남이 여러 번 발생합니다. 진입구와 진출부가 생겼다는 것은 공구가 휘면서 표면에 상승된 자국을 남긴다는 것을 의미합니다. 절삭력과 공구의 휨이 줄어들어 진출부 영역에서 약간의 소재 언더커팅이 생깁니다.
결론
- 경사도가 큰 벽에서는 가급적이면 카피 밀링을 하지 말아야 합니다. 플런지 가공에서는 칩 두께가 크고 절삭 속도가 느려야 합니다.
- 공구 중심에서는 특히 커터가 바닥 부분에 닿을 때 날이 깨질 수 있습니다.
- 미리보기 기능이 있는 이송 속도 제어 장치를 사용하십시오. 그렇지 않으면 감속이 충분하지 않아 공구 중심이 파손될 수 있습니다.
- 커터가 벽에 닿을 때 접촉 길이가 길어서 휨, 진동 또는 공구 파손의 위험이 있습니다.
- 볼 노즈 엔드밀을 사용할 때는 절삭 속도가 0 이기 때문에 가장 중요한 영역은 공구 중심에 있습니다. 공구 센터 영역 사용을 피하고 스핀들 또는 가공물을 기울여 포인트 밀링을 적용하여 조건을 개선하십시오.
- 절삭 공정은 가파른 벽을 따라 상향 카피 가공을 하는 것이 가장 유리한 절삭 속도에서 칩 두께가 최대 값을 갖기 때문에 더욱 바람직합니다.
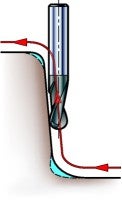
둥굴게 파먹는 위험성
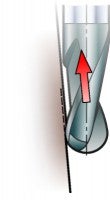
상향 카피:
추천 vc 최대 칩 두께
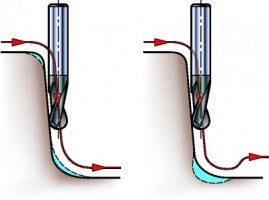
캐비티 바닥:
공구 센터에서 파손될 위험
특히 고속 가공 기술을 사용할 때는 형상 에러가 자주 발생합니다.
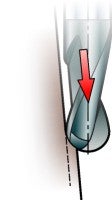
하향 카피:
매우 낮은 vc에서 칩 두께가 두꺼움
공구 수명이 단축되지 않도록 이송 감소
상향 및 하향 밀링의 방향이 바뀌면 공구에 가해지는 휨 및 절삭 부하가 달라집니다. 공구 경로의 임계 단면에서 이송 속도를 줄이면 절삭날이 깨질 위험이 줄어들고, 보다 긴 공구 수명으로 더욱 안전한 절삭 공정이 이루워집니다.
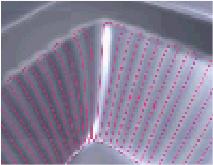
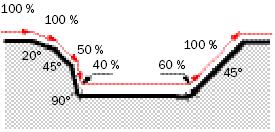
윤곽선 밀링
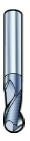
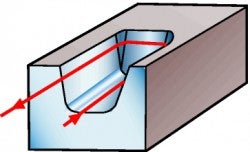
일정한 Z값에서 소재를 '분리'하는 것으로 제한된 프로그래밍 기술을 사용하는 대신, 하향 밀링과 결합하여 윤곽선 공구 경로를 사용하는 것이 매우 좋습니다. 결과는 다음과 같습니다.
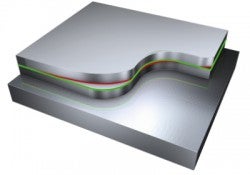
+ 가공 시간 대폭 단축
+ 기계 및 공구 활용율 향상
+ 가공된 모양의 형상 품질 개선
+ 시간이 많이 소요되는 정삭 및 수동 연마 작업 감소
+ 절삭 속도 제어 - ve
+ HSM 사용
+ 고 이송
+ 긴 인서트 수명
+ 안정성
초기 프로그래밍 작업은 더 어렵고 다소 오래 걸립니다. 그러나 일반적으로 시간당 기계 비용이 워크스테이션의 3배이므로 초기 비용은 신속하게 회수됩니다. 공구 경로 편차를 피하기 위해 미리보기 기능이 있는 소프트웨어가 설치된 기계를 사용하는 것이 좋습니다.결론
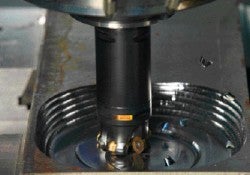
- 하향 밀링을 보장하는 가장 좋은 방법은 '워터라인 밀링'처럼 공구 경로의 윤곽 가공을 사용하는 것입니다.
- 밀링 커터의 원주를 따라 윤곽 가공을 하며 큰직경 공구로 가공하면 더 많은 날이 효과적으로 사용되므로 생산성이 향상됩니다.
- 기계에서 스핀들 속도가 제한적인 경우 윤곽 가공을 하면 절삭 속도를 유지하고 제어하는 데 도움이 됩니다.
- 또한 윤곽 가공은 또한 작업 부하 및 방향의 변화를 빠르게 만듭니다. 고속 가공 및 고 이송 밀링과 고경도 소재에서는 절삭날과 공정이 휨의 차이를 만들거나 진동을 발생시킬 수 있는 모든 변화에 취약하므로 특히 중요합니다.
- 우수한 공구 수명을 위해 가능한 한 오래동안 절삭부위에 계속 체류하십시오.
주의! 절삭 속도가 0 인 공구의 중심에서 절삭하지 마십시오.
공구 경로 전략
Z – 일정한 윤곽 가공, 두 축. 황삭에서 정삭까지 가공
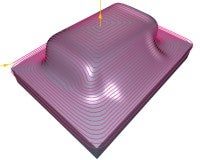
워터라인 밀링 Z - 일정한 윤곽 가공
- CAM으로 제어되는 최대 스캘럽 기능 사용 가능
- 부드러운 맞물림 및 벗어남
- 간편한 프로그래밍
- 다양한 공구 선택
헬리컬 윤곽 가공, 3~5축. 정삭
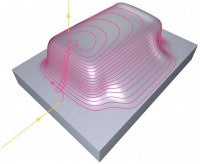
램핑 공구 경로의 윤곽 가공
- 원활한 방향 변화
- 좋은 형상 정밀도 및 표면 조도
- 스캘럽 높이 제어
- 지속적인 맞물림
- 짧은 프로그램
- 짧은 공구
조각된 표면 생성
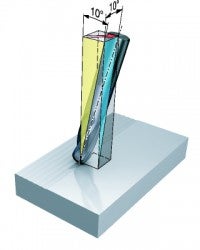
약 10° 기울어진 커터를 이용해 두 방향으로 하향 밀링 가공을 하면 표면 조도가 향상되고 신뢰할 수 있는 성능이 나옵니다. 반경 모양 절삭날 또는 볼 노즈 커터는 커스프(cusp) 높이인 h에서 다음 조건에 따라 표면을 형성합니다.
- 폭, ae, 절삭
- 날당 이송, fz
다른 중요한 요소는 절삭력과 런아웃의 공구 지표(TIR)에 영향을 주는 절입 깊이 ap가 있습니다. 최상의 결과를 얻으려면 다음과 같이 하십시오.
- Coromant Capto®의 고정밀 유압 척을 사용하십시오.
- 공구 오버행을 최소화하십시오.
황삭 및 준황삭
날당 이송이 절삭폭 및 깊이보다 훨씬 작으면 생성된 표면에서 이송 방향의 커스프 높이가 훨씬 더 작습니다.
정삭 및 슈퍼피니싱
모든 방향으로 매끄럽고 대칭인 표면 질감을 구현하는 것이 좋습니다. 이때 표면은 선택한 방법에 관계없이 나중에 쉽게 연마할 수 있습니다.
이 결과를 얻으려면 조건이 fz ≈ ae여야 합니다.
최상의 표면 질감을 원하면 슈퍼피니싱에서 기울어진 2날 커터를 사용하십시오.
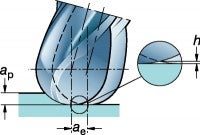
fz가 ae
보다 훨씬 작은 준황삭
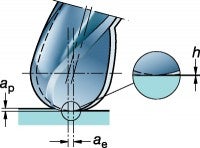
기울어진 커터를 이용하고 fz가 ae
와 동일한 슈퍼피니싱
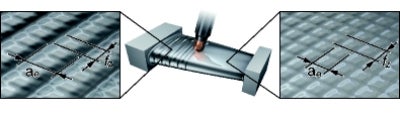
홈 또는 슬롯 밀링 가공
일반적으로 홈 또는 슬롯 밀링 가공에서는 엔드밀 가공보다 사이드 및 평면 밀링을 선호합니다. 슬롯 또는 홈은 짧거나 길거나, 닫혀 있거나 열려... chevron_right
척 선택
척은 원형 생크 공구를 고정하는 데 사용됩니다. 척에는 여러 스타일이 있으며 다음에 따라 척을 선택합니다. 적용: 엔드밀, 드릴, 탭, 리머 가공물... chevron_right
평면 밀링
평면 밀링 가공에 포함되는 작업 일반 평면 밀링 가공 고이송 밀링 가공 중절삭 평면 밀링 가공 와이퍼 인서트를 사용한 정삭 일반 평면 밀링... chevron_right
진동
밀링 가공에서 진동은 절삭 공구, 홀딩 공구, 기계, 가공물 또는 지그의 제한 사항 때문에 발생할 수 있습니다. 진동을 줄이기 위해 고려할 수 있는... chevron_right