밀링 가공의 커터 경로 및 칩 형성
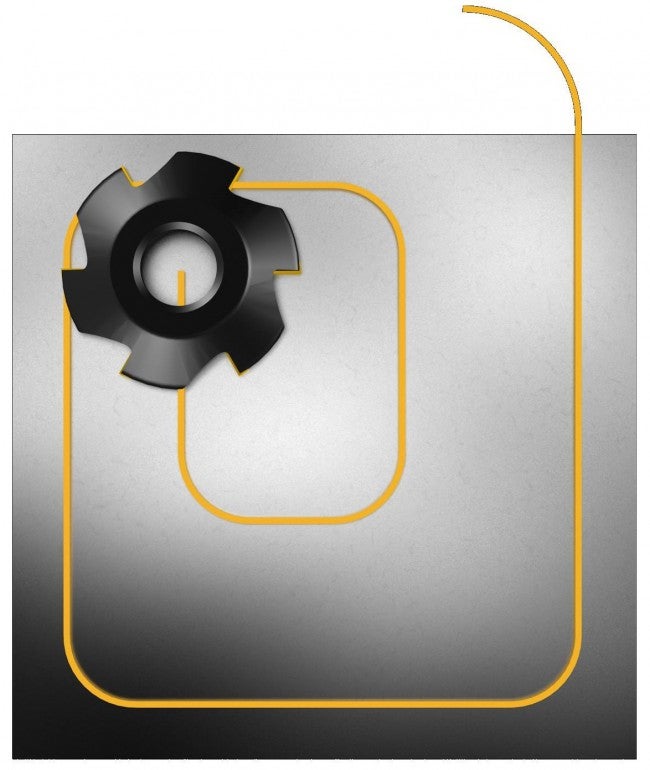
밀링 가공에서 올바른 커터 경로와 칩 형성은 안정적인 절삭날과 향상된 공구 수명을 위해 중요한 요소입니다.
반경 방향에서 밀링 커터의 각 절삭날은 가공물과 간헐적으로 맞물립니다. 각 맞물림에서 고려해야 할 세 가지 단계가 있습니다.
1. 절삭 진입
2. 절삭 맞물림 길이
3. 절삭에서 진출
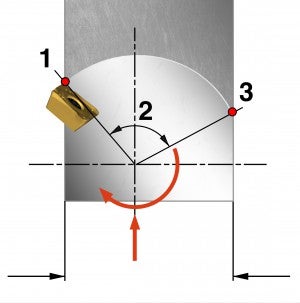
절삭 진입
초경 인서트를 사용할 경우 절삭 진입은 세 절삭 단계 중에서 가장 민감하지 않은 단계입니다. 초경은 진입의 충격에서 압축 응력을 효과적으로 처리합니다.
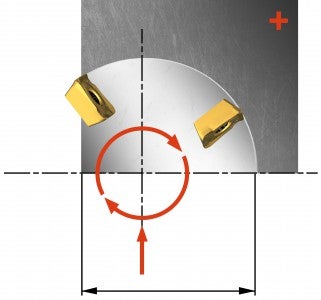
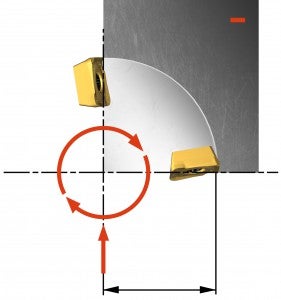
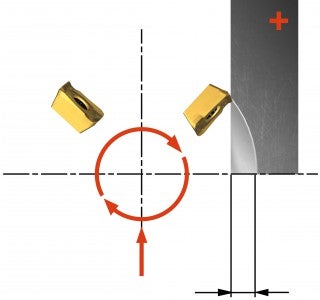
절삭에서 진출
가공물에서의 진출은 세 절삭 단계 중에서 가장 민감한 단계입니다.
항상 출구에서 두꺼운 칩의 형성을 방지하십시오. 초경 인서트를 사용할 경우 두꺼운 칩의 형성은 공구 수명을 크게 감소시킬 수 있습니다. 최종 절삭 지점에서는 칩을 충분히 지지하지 못해 구부러지기 쉽기 때문에 초경에 장력이 발생하여 절삭날이 파손될 수 있습니다.
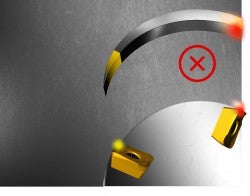
절삭 맞물림 길이
- 슬롯 가공 때 가능한 최대 맞물림 길이는 180°(ae = 100% DC)입니다.
- 정삭 밀링 가공의 경우 맞물림 길이가 매우 작을 수 있습니다.
- 반경 방향 절입 ae/DC의 비율에 따라 재종 요구사항이 크게 달라질 수 있습니다.
- 맞물림 길이가 클수록 절삭날로 전달되는 열이 커집니다.
- 맞물림 길이가 큰 경우 CVD 코팅 재종은 최상의 열 차단벽을 제공합니다.
- 맞물림 길이가 작으면 일반적으로 칩 두께가 더 작고, PVD 코팅 재종의 절삭날이 더 날카로울수록 열이 덜 발생하고 절삭 부하가 감소합니다.
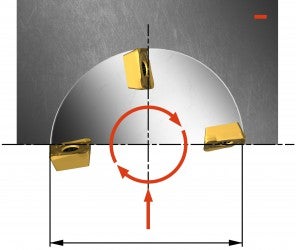
큰(최대) 맞물림 길이
- 긴 절삭 시간
- 높은 반경 방향 부하
- 더 많은 열 발생
- CVD 코팅 재종
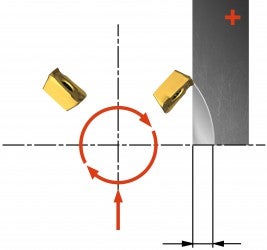
작은 맞물림 길이
- 절삭 시간이 짧고 열이 덜 발생해 vc를 높일 수 있습니다.
- 칩이 더 얇아 fz를 높일 수 있습니다.
- 날카로운 날
- PVD 코팅 재종
가공물 진입
커터가 가공물에 직선으로 진입하도록 프로그램된 경우 커터가 완전히 맞물릴 때까지 출구에서 두꺼운 칩이 생성됩니다. 그 결과 특히 고경도 강, 티타늄 및 내열합금에서 공구 수명이 크게 감소합니다. 또한 진동을 줄이려면 가공물로 부드럽게 진입하는 것이 필수적입니다.
공구 수명을 향상시키는 두 가지 방법이 있습니다.1. 이송 감소
커터가 완전히 맞물릴 때까지 이송을 50%까지 줄이십시오.2. 롤 인(roll in) 진입
시계 방향으로 롤인(roll in) 형태로 진입하도록 프로그램합니다(반시계 방향은 두꺼운 칩 문제를 해결하지 못합니다). 롤인(roll in) 형태로 진입하면 출구의 칩 두께가 항상 0이 되어 이송을 높이고 공구 수명을 향상시킬 수 있습니다.
커터 위치
입구에서 두꺼운 칩을 생성하고 출구에서 얇은 칩을 생성하려면 커터를 중심에서 벗어나도록 왼쪽에 배치하십시오(하향 밀링). 절삭 부하의 방향이 더욱 일정해지고 유리해져 진동 경향이 최소화됩니다.
커터를 중심선 위에서 대칭으로 배치하면 출구에서 두꺼운 칩이 생성되어 진동 경향에 대한 위험이 높아집니다.
커터 직경 DC는 절삭 폭 ae보다 20-50% 더 커야 합니다.
또한 사용 가능한 스핀들 동력도 피치 선택에 영향을 미치므로 고려해야 합니다.
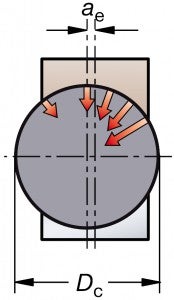
커터는 ae보다 +20–50%
더 커야 하고 중심을 벗어나도록 배치되어야 합니다.
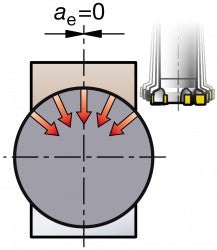
중심선 위에 커터가 있으면
진동이 발생합니다.
커터 맞물림 유지
절삭 방향을 급격하게 변경하면 출구에서 두꺼운 칩이 발생합니다. 안전하고 최적화된 밀링 공정을 위해 다음 권장사항을 따르십시오.
- 커터 맞물림을 유지하십시오.
- 모든 코너 주위를 롤링하십시오.
- 코너의 최대 적용범위를 포함하려면 절삭 폭 ae가 DC의 70%여야 합니다.
- 원주 밀링에서는 외경 코너 주위를 롤링하십시오.
- 가능하면 단속 및 홀 주위를 프로그램하십시오.
평면 밀링
평면 밀링 가공에 포함되는 작업 일반 평면 밀링 가공 고이송 밀링 가공 중절삭 평면 밀링 가공 와이퍼 인서트를 사용한 정삭 일반 평면 밀링... chevron_right
턴 밀링 가공
성공적인 턴 밀링 가공이란? 턴 밀링 가공은 센터를 중심으로 가공물을 회전시키면서 곡면을 밀링 가공하는 것으로 정의됩니다. 기존의 밀링 또는... chevron_right
진동
밀링 가공에서 진동은 절삭 공구, 홀딩 공구, 기계, 가공물 또는 지그의 제한 사항 때문에 발생할 수 있습니다. 진동을 줄이기 위해 고려할 수 있는... chevron_right
슬라이싱 방법
슬라이싱과 트로코이드 밀링 가공은 원래 고경도 강, ISO H 및 HRSA 소재, ISO S 같은 난삭재의 황삭 및 준황삭 가공을 위해 개발되었지만,... chevron_right