Fræsning af huller og kaviteter/lommer
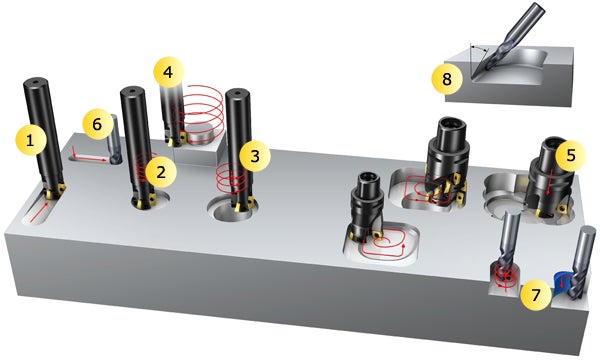
- Lineær ramping i to akser
- Cirkulær ramping
- Udvidelse af et hul
- Cirkulær udvendig fræsning eller ramping
- Dykfræsning
- Stepfræsning
- Slicing-metoder
- Lukkede lommer eller vinkler
Fræsning af huller: bearbejdning af åbninger
- Dannelse af åbninger i et solidt emne
- Udvidelse af et hul eller en lomme
- Åbning/udvidelse af en lomme
Dannelse af åbninger i et solidt emne
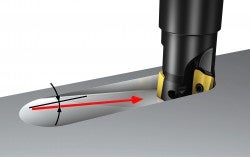
Lineær ramping
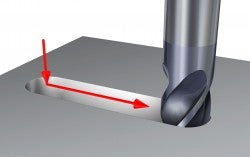
Stepfræsning
Åbning af et spor
Ved fræsning af et hul foretrækkes lineær ramping (2 akser samtidig) altid frem for stepfræsning.
Stepfræsning er en alternativ metode til fræsning af huller, men den giver ofte lange spåner og genererer uønskede skærekræfter på fræseren.Åbning af et hul eller en lomme
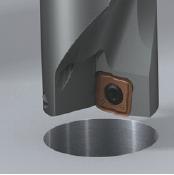
Boring
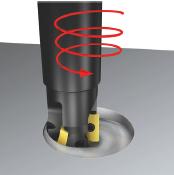
Cirkulær ramping
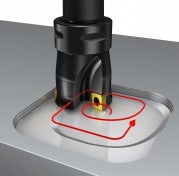
Ramping af en kavitet
Boring er den traditionelle og hurtigste metode til at fremstille et hul, men spånbrydningen kan være en udfordring i nogle materialer, og boring har ikke den krævede fleksibilitet til at producere varierende diametre og former, der ikke er runde.
Cirkulær ramping (3 akser samtidig) er en mindre produktiv metode end boring af et hul, men den kan være et godt alternativ i følgende tilfælde:
- Huller med stor diameter, hvis der er begrænset maskineffekt til rådighed
- Produktion af små serier. En tommelfingerregel for diametre over 25 mm: Fræsning er omkostningseffektiv op til serier på ca. 500 huller
- Når et stort udvalg af hulstørrelser skal bearbejdes
- Begrænset plads i værktøjsmagasin til at opbevare mange borstørrelser
- Produktion af bundhuller, hvor der kræves en plan bund
- Ikke-stive, tyndvæggede komponenter
- Afbrudt spån
- Materialer, der er vanskelige at bore i på grund af spånbrydning og spånafgang
- Ingen skærevæske til rådighed
- Ved fræsning af kaviteter/lommer ("ikke-runde huller")
Valg af metode – eksempel
Åbning af en kavitet/lomme
![]() | ||||||
![]() | ||||||
Boring og cirkulær fræsning ![]() ![]() | Boring og dykfræsning ![]() ![]() | Cirkulær ramping ![]() | ||||
Fordele + Højt spånvolumen til huller, der ikke er runde + Førstevalg til strukturdele af titan til flychassiser Ulemper – Kræver en stabil maskine – Spånafgang – horisontal maskine – Der kræves omhyggelig programmering | Fordele + Problemløser til applikationer med lange udhæng + Enkel programmering, der passer til ældre maskiner og multispindelmaskiner Ulemper – Lavt spånvolumen | Fordele + Færre værktøjer /ikke behov for bor) + Fleksibel (producerer en lang række størrelser) + Kræver ikke skærevæske = godt til åbne maskiner + Egner sig til alle maskinkoncepter og konfigurationer Ulemper – Mindre produktiv til store kaviteter | ||||
Det grundlæggende valg til lommer | Problemløser Lange udhæng | Det grundlæggende valg til 3D-kaviteter |
Udvidelse af et hul eller en lomme
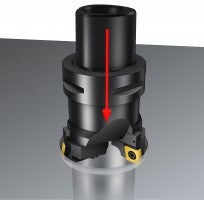
Opboring
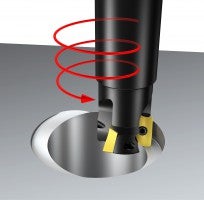
Cirkulær ramping
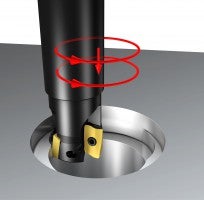
Cirkulær fræsning
Udvidelse af et hul
Opboring er normalt den hurtigste metode af de samme årsager som ved boring, men fræsning af huller er nogle gange et godt alternativ. Der kan bruges to forskellige fræsemetoder: cirkulær ramping (3 akser) eller cirkulær fræsning (2 akser). Cirkulær ramping foretrækkes, når hullet er dybere end ap maks., eller i vibrationsfølsomme applikationer. Hullets rundhed/koncentricitet bliver også bedre, når der anvendes ramping, især med lange udhæng. Rundheden forbedres, hvis emnet roteres i stedet for at bevæge fræseren rundt i en cirkulær bane. Det gælder både for cirkulær ramping og fræsning.Udvidelse af en kavitet
Indvendig hjørnefræsning og dykfræsning kræver et starthul og kan sammenlignes med ramping af en kavitet direkte ind i en solid blok.
- Ramping (3 akser) har en fordel, fordi metoden kun kræver et værktøj og kan producere 3D-former, hvilket gør den velegnet til profilfræsning. Hvis den anvendes med teknikker med høj tilspænding (let og hurtig), vil skærekræfterne blive dirigeret på en gunstig måde, der minimerer vibrationsproblemer
- Dykfræsning løser ofte problemer med lange udhæng og/eller dybe kaviteter
- Indvendig hjørnefræsning kræver mere programmering end dykfræsning, men er hurtigere
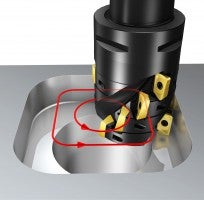
Indvendig hjørnefræsning
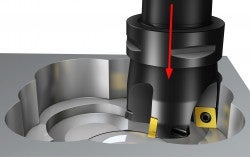
Dykfræsning
Fræsning af detaljer (resterende materiale)
Når skrubfræsningen af en kavitet er færdig, er der ofte materiale tilbage, især i hjørner. Dykfræsning med en mindre fræser er en af metoderne til at nærme sig den endelige form. Slicing (let og hurtig) er en anden teknik, der ofte anvendes ved hjørnefræsning. Trokoidefræsning er en form for slicing-teknik, der også anvendes til at fræse spor, lommer osv.
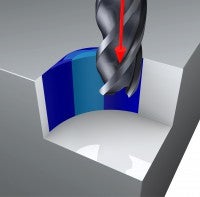
Dykfræsning i hjørner
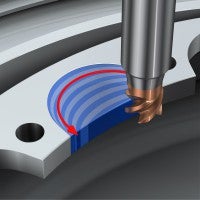
Slicing-teknik – let og hurtig
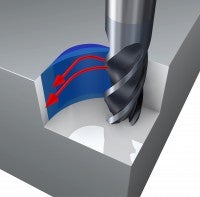
Slicing i hjørner
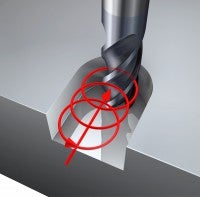
Trochoide
Sådan åbnes/udvides en kavitet eller lomme
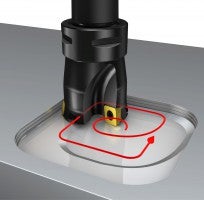
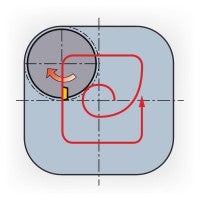

Der findes to klare strategier:1. Cirkulær ramping (3 akser) – lille ap
Vælg en fræser med lille indgrebsvinkel. En fræser med runde skær er et andet alternativ.
Denne "lette og hurtige" teknik giver en utroligt god spånvolumen og er førstevalg til mindre stabile maskiner (iht. ISO 40), og når lommen har en profileret form, f.eks. formfremstilling.
Bemærk: Undgå at bearbejde hele vejen mod et 90°-hjørne, fordi effekten af en lille indgrebsvinkel mistes, dvs. at spåndybden øges dramatisk.
Fræseparametre:
- Maksimal fræserdiameter = 1,5 x komponentens hjørneradius
- Cirkulær rampe i dybden – mod uret
- Lav tilkørsel med radius til det næste indgreb
- Radial spåntagning – maks. ae = 70 % DC
- Aksial spåntagning for fræsere med runde skær 25 % iC
- Radius for værktøjsbane i hjørnet = DC
- Reducer hjørnetilspændingen
2. Cirkulær fræsning (2 akser) – stor ap
Bor et hul, og skift derefter til en hjørnepindfræser eller en valsefræser. En typisk applikation er emner til fly – bearbejdning af titan.Applikationstip
Sørg for god spånafgang for at forhindre genbearbejdning af spåner/spånhamring:
- En vandret spindel (ISO 50) foretrækkes
- Højtryksvæske eller trykluft med kølevæske gennem værktøjet
- DC bør ikke være større end 75 % af huldia. Brug en stor aksial spåndybde – maks. ae = 2 x DC
Indføringen i det borede hul bør ske i en cirkulær bane:
- Kontrollér det radiale indgreb, maks. ae = 30 % af DC
Kontrollér det radiale indgreb for at minimere vibrationerne i hjørnerne og maksimere produktiviteten:
- Brug den størst mulige radius i hjørnerne, spiral-morph-programmering
- Brug størst mulig DC, og færdiggør detaljefræsningen separat med ikke over 1,5 x hjørneradiussen
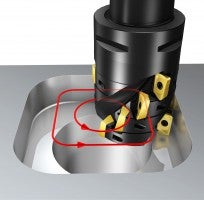
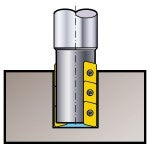

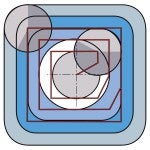

Lille hjørneradius
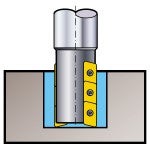

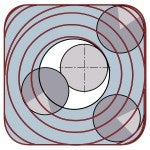

Spiral-morph-programmering
Udvidelse af et hul
Udvidelse af et eksisterende hul kan udføres enten med cirkulær ramping eller cirkulær... chevron_right
Ramping: Toakset lineær og cirkulær
Hvad er vellykket ramping? Lineær ramping anvendes ofte på emner, som en effektiv... chevron_right
Cirkulær ramping
Hvad er cirkulær ramping med bor med vendeskær? Et roterende værktøj laver et hul... chevron_right
Stepfræsning
Hvad er vellykket stepfræsning? Stepfræsning er et alternativ til ramping for at... chevron_right