선삭에서 가공물의 품질을 높이는 방법
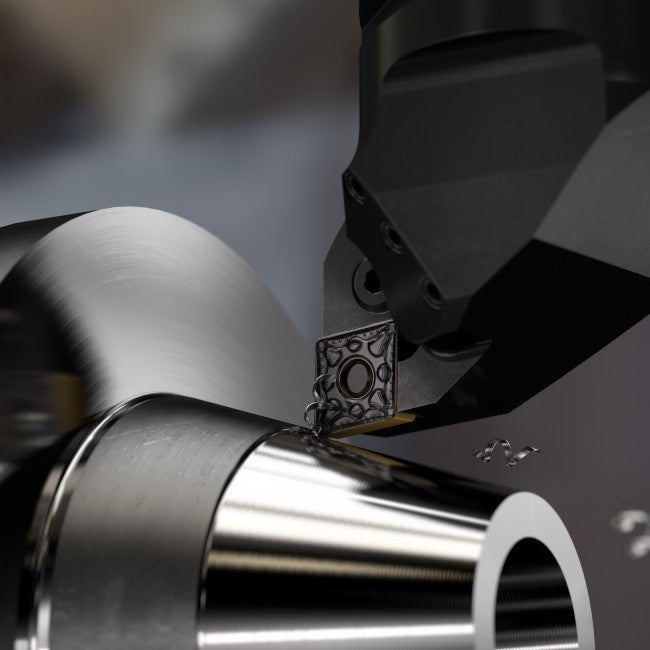
선삭 가공물의 품질을 높이려면 칩 컨트롤이 고려해야 할 가장 중요한 요소 중 하나입니다. 올바른 절삭 조건을 선택하고 좋은 부품 품질을 위한 적용 팁을 따르십시오.
성공적인 칩 컨트롤
칩 컨트롤은 선삭 가공의 핵심 요소 중 하나이고, 3가지 주요 칩 브레이킹 선택 방안이 있습니다.
- 셀프 브레이킹(예: 회주철)
- 공구에 부딪혀 브레이킹
- 가공물에 부딪혀 브레이킹
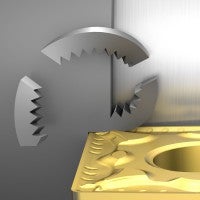
셀프 브레이킹
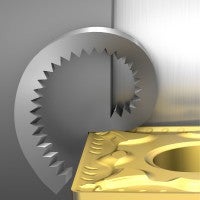
공구에 부딪혀 브레이킹
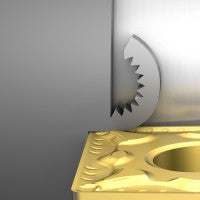
가공물에 부딪혀 브레이킹
칩 브레이킹에 영향을 주는 요인
- 인서트 형상 칩 홈의 폭과 마이크로/매크로 형상 디자인에 따라 칩이 개방된 형태 또는 더욱 압축된 형태임
- 노즈 반경: 노즈 반경이 작으면 클 때보다 칩 컨트롤 우수
- 절입각(리드각): 각도에 따라 칩은 다른 방향으로 향하게 됨; 직각 쪽으로 또는 직각으로부터 멀리 배출됨
- 절입 깊이: 가공물 소재에 따라 절입 깊이가 칩 브레이킹에 미치는 영향이 커서 절입 깊이가 깊을수록 칩 브레이킹 및 제거를 위한 절삭 부하가 커짐
- 이송: 빠른 이송은 일반적으로 더 강한 칩을 만듬. 일부 경우 칩 브레이킹 및 칩 컨트롤에 도움이 됨
- 절삭 속도: 절삭 속도의 변화는 칩 브레이킹 성능에 영향을 줄 수 있음.
- 소재: 일반적으로 짧은 칩 소재(예: 주철)가 가공이 쉬움. 기계적 강도와 크리프(소재가 압력을 받아 서서히 움직이거나 변형되는 현상. 예: 인코넬) 내성이 우수한 소재는
칩 브레이킹이 더욱 중요함
선삭의 절삭 조건
올바른 선삭 절삭 속도 및 이송을 선택할 때 기계, 공구, 인서트, 소재를 항상 고려해야 합니다.
- 인서트 안정성과 표면 조도를 보장하기 위해 낮은 이송에서 시작한 다음 이송을 증가시켜 칩 브레이킹을 향상시키십시오.
- 노즈 반경보다 큰 절입 깊이로 적용하십시오. 이것은 내경 가공에서 중요한 인서트의 반경 방향 처짐을 최소화합니다.
- 절삭 속도를 너무 낮게 설정하면 공구 수명이 감소합니다. 항상 추천 절삭 속도(vc m/min (ft/min))로 가공하십시오.
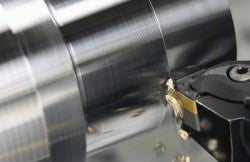
절삭유로 선삭 가공 부품 품질 개선
절삭유가 올바르게 적용되면 공정 안정성과 공구의 성능, 그리고 부품 품질이 개선됩니다. 절삭유 사용 시 유의사항:
- 정밀 절사유가 있는 공구는 정삭 작업에 강력히 추천됩니다.
- 칩 브레이킹에 필요한 절삭유 압력은 노즐 직경(배출구), 가공되는 소재, 절입 깊이 및 이송에 따라 달라집니다.
- 필요한 절삭유 유량은 압력과 절삭유 홀의 총 절삭유 공급 면적에 따라 달라집니다.
- 중삭 및 황삭 가공에서는 하부 절삭유를 사용하는 것이 좋습니다.
- 정삭 가공에서는 하부 절삭유와 정밀 절삭유를 모두 사용하는 것이 좋습니다.
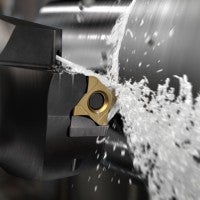
올바른 절삭유 적용을 통한 문제 해결
- 칩 컨트롤 문제: 상부 절삭유를 사용하십시오.
- 치수 문제: 일반적으로 고온에 의해 발생합니다. 상부 절삭유와 하부 절삭유를 모두 사용하고 최대한 높은 압력을 가하십시오.
- 표면 품질 불량: 칩 때문에 불량이 발생하면 상부 절삭유를 사용하십시오.
- 황삭 작업에서 공구 수명이 일정하지 않음: 하부 절삭유만 사용하십시오.
- 정삭 작업에서 공구 수명이 일정하지 않음: 상부 절삭유와 하부 절삭유를 모두 사용하십시오.
- 내경 가공 때 칩 배출 불량: 상부 절삭유와 하부 절삭유를 최대한 고압으로 사용하십시오.
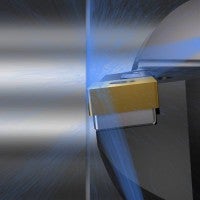
선삭 가공 부품의 표면 조도를 높이는 방법
일반적인 표면 조도 원칙:
- 표면 조도는 높은 절삭 속도를 사용하여 향상시킬 수 있습니다.
- 인서트 형상(중립, 포지티브 및 네거티브 상면각, 포지티브 여유각)이 표면 조도에 영향을 줍니다.
- 인서트 재종 선택은 표면 조도에 일부 영향을 줍니다.
- 진동이 발생할 경우 작은 노즈 반경을 선택하십시오.
와이퍼 인서트
와이퍼 인서트는 우수한 표면 조도나 칩 브레이킹 성능을 잃지 않고 높은 이송으로 부품을 선삭 가공 할 수 있습니다.
일반 가이드라인: 두 배 높은 이송, 동일한 표면 조도. 동일한 이송, 표면 조도 두 배 향상.
와이퍼 인서트는 가공물을 따라 인서트가 이송될 때 매끄러운 표면이 생성되도록 설계되었으며, 와이퍼 효과는 주로 직선 선삭 가공과 단면 가공에 효과가 있습니다.
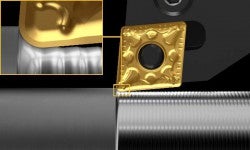
표준 반경
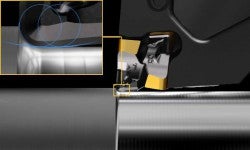
와이퍼 반경
이송률에 따른 비교(표준 인서트 vs 와이퍼 인서트)
주의! 표준 반경에 대한 모든 값은 이론상으로 계산됩니다. 와이퍼 반경에 대한 값은 저합금강의 실험 값을 기준으로 합니다.
이송 mm (inch) | 표준 RE 0.4 mm (0.016 inch) Ra µm (µinch) | 와이퍼 (-WF/-WM) RE 0.4mm (0.016 inch) Ra µm (µinch) | 표준 RE 0.8 mm (0.031 inch) Ra µm (µinch) | 와이퍼(-WMX) RE 0.8 mm (0.031 inch) Ra µm (µinch) |
0.07 (0.003) | 0.31 (12.4) | 0.30 (12.0) | - | - |
0.10 (0.004) | 0.63 (25.2) | 0.32 (12.8) | 0.31 (12.4) | - |
0.12 (0.005) | 0.90 (36.0) | 0.45 (18.0) | 0.45 (18.0) | - |
0.15 (0.006) | 1.41 (56.4) | 0.70 (28.0) | 0.70 (28.0) | 0.25 (10.0) |
0.18 (0.007) | 2.03 (80.8) | 1.00 (40.0) | 1.00 (40.4) | 0.30 (12.0) |
0.20 (0.008) | 2.50 (100.0) | 1.25 (50.0) | 1.25 (50.0) | 0.35 (14.0) |
0.22 (0.009) | 3.48 (139.2) | 1.74 (69.6) | 1.74 (69.6) | 0.40 (16.0) |
0.25 (0.010) | - | - | 2.25 (90.0) | 0.45 (18.0) |
0.28 (0.011) | - | - | 2.82 (112.8) | 0.50 (20.0) |
0.30 (0.012) | - | - | 3.23 (129.2) | 0.55 (22.0) |
0.35 (0.014) | - | - | 4.40 (176.0) | 0.60 (24.0) |
0.40 (0.016) | - | - | 5.75 (230.0) | 0.70 (28.0) |
0.45 (0.018) | - | - | 8.54 (341.6) | 1.1 (44.0) |
0.50 (0.020) | - | - | 10.55 (422.0) | 1.3 (51.0) |
이송 mm (inch) | 표준 RE 1.2 mm (0.047 inch) Ra µm (µinch) | 와이퍼(-WMX) RE 1.2mm (0.047 inch) Ra µm (µinch) | 표준 RE 1.6 mm (0.063 inch) Ra µm (µinch) | 와이퍼(-WMX) RE 1.6 mm 1) (0.063 inch) Ra µm (µinch) |
0.15 (0.006) | 0.47 (18.8) | - | - | - |
0.18 (0.007) | 0.68 (27.2) | - | - | - |
0.20 (0.008) | 0.83 (33.3) | 0.3 (12.0) | 0.63 (25.2) | - |
0.22 (0.009) | 1.16 (46.4) | 0.3 (12.0) | 0.87 (34.8) | - |
0.25 (0.010) | 1.50 (60.0) | 0.4 (16.0) | 1.12 (44.8) | 0.3 (12.0) |
0.28 (0.011) | 1.88 (75.2) | 0.4 (16.0) | 1.41 (56.4) | 0.35 (14.0) |
0.30 (0.012) | 2.16 (86.4) | 0.4 (16.0) | 1.62 (64.8) | 0.4 (16.0) |
0.35 (0.014) | 2.93 (117.2) | 0.5 (20.0) | 2.20 (88.0) | 0.4 (16.0) |
0.40 (0.016) | 3.83 (153.2) | 0.65 (26.0) | 2.88 (115.2) | 0.4 (16.0) |
0.45 (0.018) | 5.70 (228.0) | 0.85 (34.0) | 4.27 (170.8) | 0.5 (20.0) |
0.50 (0.020) | 7.03 (281.2) | 1.15 (46.0) | 5.27 (210.8) | 0.7 (28.0) |
0.55 (0.022) | 8.51 (340.4) | 1.2 (48.0) | 6.38 (255.2) | 0.9 (36.0) |
0.60 (0.024) | 10.13 (405.2) | 1.3 (52.0) | 7.59 (303.6) | 1.05 (42.0) |
0.65 (0.026) | - | - | 8.91 (356.4) | 1.25 (50.0) |
0.70 (0.028) | - | - | 10.31 (413.6) | 1.3 (52.0) |
0.85 (0.033) | - | - | 15.24 (609.6) | 1.9 (76.0) |
0.90 (0.035) | - | - | 17.09 (683.0) | 2.1 (84.0) |
- 1.6 mm (0.06 inch) 반경 값은 DNMX 인서트 기준입니다.
외경 선삭 가공에 대한 팁
진동이 발생하기 쉬운 가공물
1회 가공 패스(예: 튜브)
절삭 부하가 축 방향으로 척/스핀들로 향하도록 1회 가공 패스에서 전체 절삭을 수행하는 것이 좋습니다.
예:
외경(OD) 25 mm (0.984 inch)
내경(ID) 15 mm (0.590 inch)
절입 깊이 ap 4.3 mm (0.169 inch)
가공 후 벽 두께 = 0.7 mm (0.028 inch)
OD = 25 mm (0.984 inch) | ap 4.3 mm (0.169 inch) |
![]() | ID = 15 mm (0.590 inch) |
90°에 가까운 절입각(리드각 0°)을 적용하면 절삭 부하가 축 방향으로 향합니다. 이로 인해 부품에 가해지는 굽힘력이 최소화됩니다.
2회 가공 패스
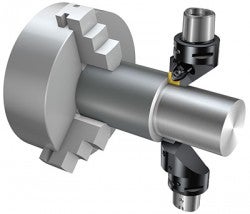
동기식 상부 및 하부 터릿 가공은 반경 방향 절삭 부하를 평준화시키고 가공물의 진동 및 굽힘을 방지합니다.
가는 가공물/벽이 얇은 가공물
가는 가공물/벽이 얇은 가공물을 가공할 때는 다음을 고려하십시오.
- 90°에 가까운 절입각(리드각 0°)을 사용하십시오. 작은 변화 (91/-1도에서 95/-5도 각도까지)는 가공 중 절삭 부하 방향에 영향을 미칩니다.
- 절입 깊이 ap는 노즈 반경 RE보다 커야 합니다. ap가 크면 축 방향 부하Fz가 증가하고 진동을 발생시키는 반경 방향 절삭 부하 Fx가 감소합니다.
- 날카로운 절삭 날과 작은 노즈 반경 RE 인서트를 사용하여 절삭 부하를 낮추십시오.
- 이 유형의 작업에 내마모성과 날카로운 인서트 형상이 필요하면서멧이나 PVD 재종을 사용해 보십시오.
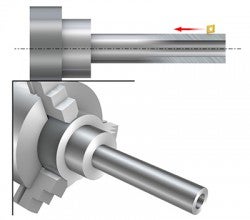
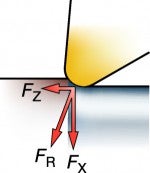
직각 가공/직각 선삭 가공
인서트 날의 파손을 최소화하려면 1~5단계를 따르십시오. 이 방법은 CVD 코팅 인서트에서 권장되며, 파손을 크게 줄일 수 있습니다.
1-4단계:
칩 걸림을 피하려면 각 단계(1~4)의 거리를 이송률과 동일하게 유지하십시오.
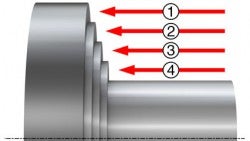
5단계:
최종 가공은 외경에서 시작해 내경 쪽으로 한번 수직 절삭으로 가공하십시오.
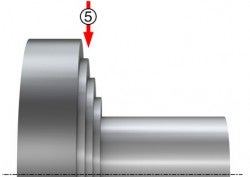
직각 단면 가공에서 안쪽에서 외측으로 가공할 때 반경 방향으로 칩이 감기는 문제가 발생할 수 있습니다. 공구 경로를 변경하면 칩 방향이 바뀌어 문제를 해결할 수 있습니다.
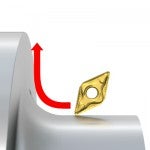
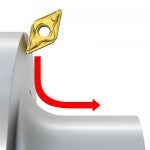
단면 가공
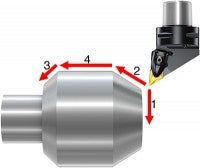
단면 (1)과 챔퍼 (2)에서 시작하십시오. 가능하면 가공물의 기하학적 조건이 허용하는 한 챔퍼 (3)을 가공하십시오. 축 방향 절삭(4)은 마지막 작업이며 가공 중에 인서트가 부드럽게 진입 및 진출을 유도합니다.
단면 가공은 다음 패스를 위해 가공물에 기준점을 설정하기 위한 첫 번째 작업입니다.
버 형성은 종종 절삭 끝 부분(가공물에서 나갈 때)에서 문제가 됩니다. 챔퍼 또는 반경을 유지(모서리 R 처리)하면 버가 형성되는 것을 최소화하거나 방지할 수 있습니다.
가공물의 챔퍼는 (단면 가공과 축 방향 선삭 가공 모두에서) 인서트 날의 진입을 더욱 부드럽게 만듭니다.
단속 절삭

단속 가공 때:
- 빠른 단속 가공(예: 육각 봉)에 적용하려면 절삭날 인성을 제공하는 PVD 재종을 사용하십시오.
- 대형 가공물과 강단속 가공에서 인성을 제공하려면 고인성 CVD 재종을 사용하십시오.
- 치핑 저항성을 충분히 높이려면 강력한 칩 브레이커를 사용해 보십시오.
- 열 균열 방지를 위해 절삭유를 사용하지 않는 것이 도움이 될 수 있습니다.
언더컷(연삭용 릴리프)으로 가공물 정삭 가공

다음을 위해 축 방향 및 단면 선삭 가공에서 가장 큰 노즈 반경 RE를 사용하십시오.
- 강력한 날과 안전성
- 우수한 표면 품질
- 고이송 사용 가능
언더컷 폭을 초과하지 않은 상태에서 마지막 작업으로 언더컷을 수행하여 버를 제거하십시오.
내경 선삭을 위한 팁
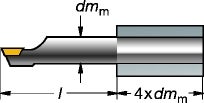
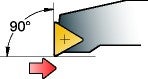

- 가장 큰 바 직경을 선택하십시오. 동시에 바와내경 사이에 칩 배출을 위한 충분한 공간이 있는지 확인하십시오.
- 절삭 조건과 관련해 칩 배출이 충분하고 올바른 유형의 칩이 생성되고 있는지 확인하십시오.
- 가장 작은 오버행을 선택하십시오. 동시에 보링 바 길이가 권장 클램핑 길이를 허용하는지 확인하십시오. 클램핑 길이가 바 직경의 3배보다 짧으면 안 됩니다.
- 진동에 민감한 부품을 생산하는 경우 진동 방지 보링 바를 사용하십시오.
- 보링 바 방향으로 절삭 부하를 가하려면 90°(리드각 0°)에 최대한 근접한 절입각을 선택하십시오. 절입각이 75°(리드각 -15°)보다 작아서는 안 됩니다.
- 공구 편향을 최소화하기 위해 교환형 인서트에서 포지티브 기본 모양과 인서트 형상을 우선적으로 사용하십시오.
- 절입 깊이보다 작은 인서트 노즈 반경을 선택하십시오.
- 불충분한 절입 깊이는 절삭 중 마찰로 인한 진동을 증가시킬 수 있습니다.절삭 가공의 효과를 높이기 위해 노즈 반경보다 큰 절입 깊이를 선택하십시오.
- 과도한 절삭날 진입(큰 절입 깊이 및/또는 이송)은 공구 편향에 의해 발생하는 진동을 증가시킬 수 있습니다.
- 일반적으로 코팅이 얇은 인서트나 비코팅 인서트는 코팅이 두꺼운 인서트보다 절삭 부하가 낮습니다. 이는 길이와 직경의 차이가 클 때 특히 중요합니다. 날카로운 절삭날은 일반적으로 진동을 최소화하여 홀 품질을 향상시킵니다.
- 내경 선삭 가공에서는 개방형 칩 브레이커가 있는 형상을 사용하는 것이 좋을 수가 있습니다.
- 일부 가공에서는 칩 걸림이나 진동의 위험에 대처하기 위해 인성이 더 높은 인서트 재종을 고려할 수 있습니다.
- 칩 형성의 개선이 필요할 경우 공구 경로의 개선을 고려하십시오.
고경도 부품 선삭을 위한 팁
선삭 관련 일반 권장사항 외에도 고경도 부품 선삭과 관련하여 고려해야 할 몇 가지 사항이 있습니다(생산 공정에 열처리 전의 가공물 자체 준비가 포함된 경우).
- 버 방지
- 정밀한 치수 공차 유지
- 열처리 전 단계에서 챔퍼 및 반경 생성
- 갑작스런 진입 및 진출 금지
- 절삭 때 롤인(roll-in) 또는 롤아웃(roll-out) 형태로 진입 또는 진출
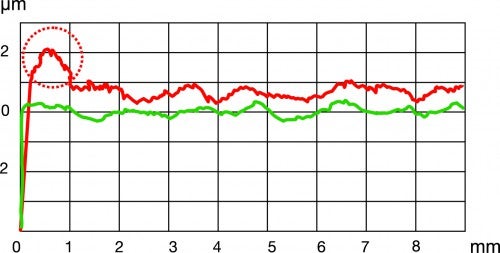
표면 측정
X축: 형상 길이
Y축: 직경 편차
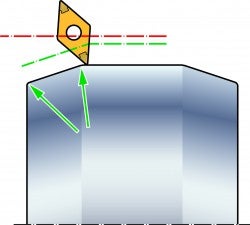
주요 표면
셋업
- 우수한 장비 안정성, 가공물 클램핑 및 정렬이 중요합니다.
- 한쪽에서만 지지되는 가공물의 경우 일반적으로 최대 2:1의 가공물 길이 대 직경 비율이 허용됩니다. 추가로 심압대 지지가 있는 경우 이 비율을 높일 수 있습니다.
- 열 적으로 대칭인 주축 및 심압대 디자인은 추가적인 치수 안정성을 증가시킵니다.
- Coromant Capto® 시스템을 사용하십시오.
- 모든 오버행을 최소화하여 시스템 강성을 극대화하십시오.
- 내경 선삭에서 초경 섕크 보링 바 및 진동 방지 공구를 사용해 보십시오.
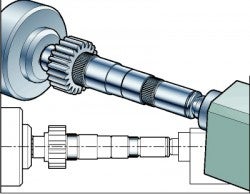
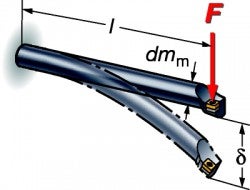
인서트 마이크로 형상
CBN 인서트를 위한 두가지 일반적인 준비된 절삭날은 S 타입과 T 타입입니다.
- S 타입: 최상의 인선 강성을 제공합니다. 마이크로 치핑에 대한 내성과 일관된 표면 품질을 보장합니다.
- T 타입: 연속 절삭에서는 최상의 표면 조도를 제공하고, 단속 절삭에서는 버 형성을 최소화합니다. 절삭 부하가 감소합니다.
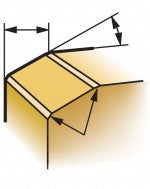
S 타입
가벼운 호닝을 적용한 챔퍼
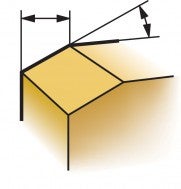
T 타입
호닝을 적용하지 않은 챔퍼
인서트 코너 형상
- 안정적인 조건에서는 표면 조도 극대화를 위해 항상 와이퍼 형상을 사용하십시오.
- 높은 생산성이 필요할 때는 절입각이 작은 인서트를 사용하십시오.
- 안정성이 좋지 않은 경우(가는 가공물 등)에는 일반 반경 인서트를 사용해야 합니다.
습식 또는 건식 가공
절삭유를 사용하지 않는 고경도 부품 선삭(HPT)은 이상적인 상황이며, 실행 가능합니다. CBN과 세라믹 인서트 모두 높은 절삭 온도를 견딜 수 있어 절삭유와 관련된 비용과 문제점들을 제거할 수 있습니다.
일부 적용 영역인 가공물의 열 안정성을 제어하기 위해 절삭유가 필요할 수 있습니다. 이 경우 선삭 작업 전체에 걸쳐 절삭유가 지속적으로 흐르게 하십시오.
일반적으로 가공 시 발생하는 열은 칩(80%), 가공물(10%) 및 인서트(10%)로 분산됩니다. 이러한 사실은 절삭날 영역에서 칩을 배출하는 것의 중요성을 보여줍니다.
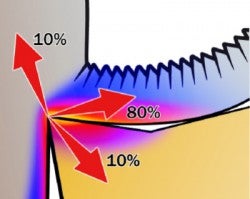
절삭 조건과 마모
절삭날 영역의 높은 열은 절삭 부하를 감소시킵니다. 따라서 절삭 속도가 너무 낮으면 발열량이 적어 인서트 파손을 유발할 수 있습니다.
상면 마모는 인서트 강도에 점진적으로 영향을 미치지만, 표면 조도에는 큰 영향을 주지 않습니다. 이와 반대로 전면 마모는 치수 공차에 점진적으로 영향을 줍니다.
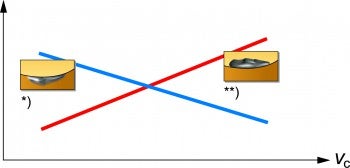
공구 수명과 마모의 관계
*) 전면 마모 **) 상면 마모
인서트 교환 기준
인서트 교체 기준으로 표면 조도(B)를 미리 설정하는 경우가 많습니다. 표면 조도는 별도의 스테이션에서 자동으로 측정되며 지정된 표면 품질로 값이 제공됩니다.
최적화되고 더욱 안정적인 공정을 위해 인서트 교체 기준으로 가공물 수(A)를 미리 설정하십시오. 이 값은 사전 결정된 표면 처리보다 10-20 % 작아야 하며, 정확한 수치는 사례별로 결정됩니다.
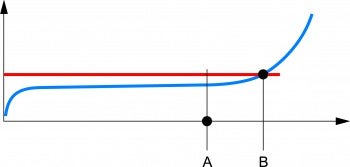
A: 사전 설정된 가공물 수
B: 사전 설정된 표면 조도
X축: 가공물 수
Y축: 표면 조도
청색선: 인서트 마모
적색선: 최대 Ra/Rz 값
1회 가공 패스 전략
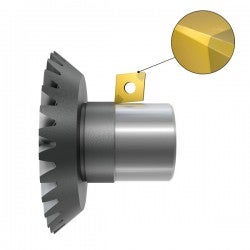
1회 가공 패스 전략은 외경 가공과 내경 가공 모두에 적합합니다. 안정적인 셋업이 중요하며, 내경 선삭에서는 공구 오버행이 바 직경(1xD)을 초과하면 안 됩니다. 가공의 효과를 높이기 위해 챔퍼링되어 가볍게 호닝된 인서트와 적절한 절삭 속도 및 이송을 추천합니다.
장점
- 빠른 가공 시간
- 단일 공구 위치
단점
- 엄격한 치수 공차 유지의 어려움
- 더 짧은 공구 수명(2회 절삭 보다)
- 비교적 빠른 마모로 인한 공차 편차
2회 가공 패스 전략
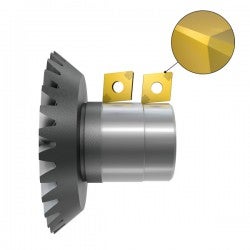
2회 가공 패스 전략을 사용하면 고품질 표면의 무인 가공이 가능합니다. 1.2 mm (0.047 inch) 반경의 황삭 인서트와 챔퍼만 있는 정삭 인서트를 추천합니다. 두 인서트 모두 와이퍼 형상이어야 합니다.
장점
- 황삭 및 정삭 가공에 최적화된 툴링
- 안정성, 정밀 공차, 공구 교체로 인하여 잠재적으로 작업 시간 증가
단점
- 인서트 2개 필요
- 공구 위치 2개
- 공구 교체 1회 추가
평면 밀링
평면 밀링 가공에 포함되는 작업 일반 평면 밀링 가공 고이송 밀링 가공 중절삭 평면 밀링 가공 와이퍼 인서트를 사용한 정삭 일반 평면 밀링... chevron_right
홈 또는 슬롯 밀링 가공
일반적으로 홈 또는 슬롯 밀링 가공에서는 엔드밀 가공보다 사이드 및 평면 밀링을 선호합니다. 슬롯 또는 홈은 짧거나 길거나, 닫혀 있거나 열려... chevron_right
정삭 보링 가공
정삭 보링 가공은 기존 홀을 완성하고 정밀한 홀 공차, 올바른 위치 및 고품질 표면 조도를 달성하기 위해 수행됩니다. 일반적으로 0.5 mm (0.020... chevron_right
척 선택
척은 원형 생크 공구를 고정하는 데 사용됩니다. 척에는 여러 스타일이 있으며 다음에 따라 척을 선택합니다. 적용: 엔드밀, 드릴, 탭, 리머 가공물... chevron_right