微小欠陥を克服する確実な方法
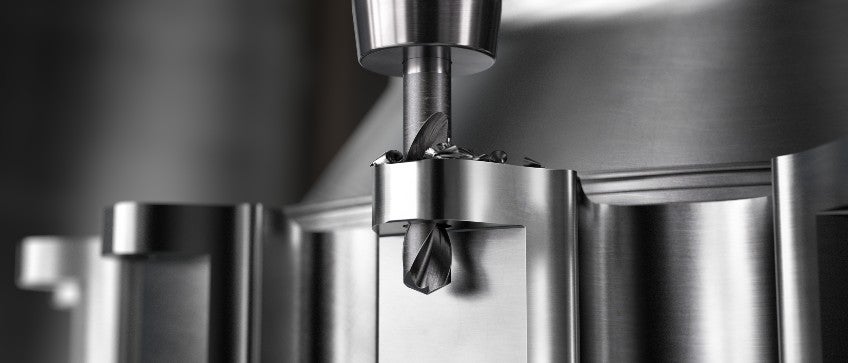
優れた超硬ドリルが穴品質の新しい可能性を開く。「2回測定して1回で切削する」という言葉は製造業においてよく使われるものですが、難削材の加工では「言うは行なうより易し」です。だからこそ、航空宇宙産業の世界的トップメーカーが、航空宇宙産業向け部品の穴品質を改善しながら、穴あけ工程におけるすべての第二段階の加工を廃止できないかと検討した際、金属加工の世界的リーダーに頼ることにしたのです。以下では、サンドビック・コロマントのグローバルプロダクトマネージャー、ジェームス・トルペが、良好な品質の穴の加工のためにドリルの設計がいかに不可欠なものであるか、について説明しています。
穴あけ加工はすべての加工プロセスのうちで最も一般的なものですが、それはまたほとんどの場合、簡単なものとして顧みられることのないものです。多くの現場では、既存の穴あけセットアップを変更または改良することなく同じ工具と切削条件を何年も使用しています。しかし、COVID-19パンデミックの予測不能な影響が継続する状況においては、このような考え方は完全に変更されるべきものです。製造業者は、顧客市場の予測不能で継続的な変化に直面しており、現在、自社の生産を採用する必要があると考えています。
例えばほとんどの製造業者は、新しいベンダーおよび製品を探しています。そのため特定の生産分野に特化していた加工工場は、CNC旋盤やフライス盤を種々の剛性の高い難削材の加工に使用し始めています。同時に製造業者は製品品質を犠牲にすることなく、収益を増やしサイクルタイムを削減するための新しい道を探求しなければなりません。
言い換えれば、製造業者にとって、どのように穴あけを行なうかを再考する時なのです。
白い層
穴の表面完全性は、航空機メーカーまたは航空宇宙産業への事業の多様化を望む一般機械産業にとっての重要な関心事です。部品の不具合を避けるには良好な穴品質が不可欠であり、そのほとんどは穴の加工または仕上げ工程により決定されます。
ツーリングソリューションおよびドリルの切れ刃形状は、製造および部分品質の最高基準を満たすために絶えず進化しています。またクーラントの使用についても、工具の温度上昇を抑えるための改善が行われています。そしてテストにより、これらの要素のそれぞれが被削材に対するいわゆる「白い層」の影響を制御できることが判明しました。
「白い層」という用語は、サンドビック・コロマントの顧客でもある航空宇宙産業の世界的トップメーカーによる造語です。白い層とは、ドリルの熱に起因する、部品の穴あけ後に見られる、薄い超微粒子構造のことです。白い層は被削材の表面特性を変えるだけでなく、顧客の品質管理プロセスでも容認できないものと考えられていました。
製造業者は、タービンディスク、コンプレッサ、ドラムおよびシャフト等、航空宇宙産業向け部品にあけられた穴に厳密な穴仕上げ加工を行ないます。そのためこの製造業者は、なぜ白い層が発生し、どのように制御するのかを詳しく調査するために、サンドビック・コロマントをパートナーに選びました。
このテストは品質管理のみを目的として行われたのではないことに注目することが重要です。お客様の経営層は加工時間全体の低減および収益の増加を希望しており、すべての第二段階の加工の廃止によりそれを達成することを希望していました。
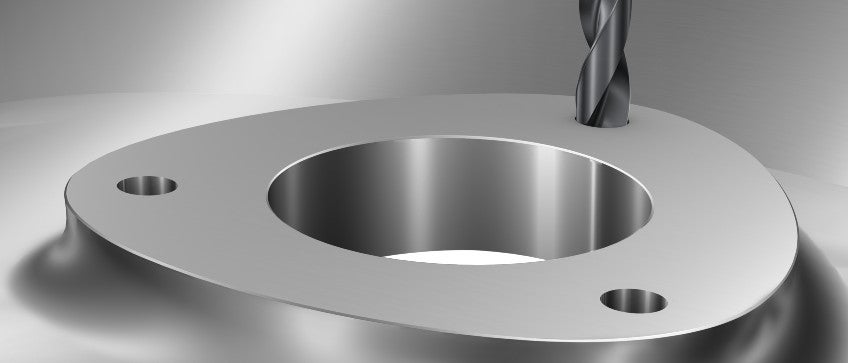
穴の表面完全性は、航空機メーカーまたは航空宇宙産業への事業の多様化を望む一般機械産業にとっての重要な関心事です。これが、CoroDrill 860-SMによる耐熱合金 (HRSA) 製ケーシングの突起部の穴あけです
。
次のアクション
第二段階の加工は、超硬ドリルを使用しての穴の作製の後に行われるもので、部品を仕上げるためのリーマ加工、プランジエンドまたはフライス加工が考えられます。第二段階の加工は、公差の厳しい穴を加工する場合を除いて、寸法精度よりも、主に表面完全性の要求を満たす (白い層のような問題を低減する) ために行われるものです。
総コストの観点からすると、第二段階の加工は、表面完全性を維持するための別の方法である低い切削条件を維持しての加工よりもかなり費用がかかります。そのためサンドビック・コロマントのお客様は、第二段階の加工の全廃についての調査を希望されたのです。いずれの第二段階の加工もなしに穴を指定サイズに加工できるサプライヤは、部品当たりコストの大幅な削減という点で優位にあります。
白い層の原因および予防可能性の調査では、航空宇宙産業においてよく用いられる高強度のニッケルクロム被削材のインコネル718の穴あけテストが4回行われました。そのような調査がお客様によって行なわれたのは初めてのことでした。
テストでは、サンドビック・コロマント製の2本の超硬ドリル、CoroDrill® R840とCoroDrill® R846を使用して穴あけを評価しました。各テストは2種類の切削条件のセット、それぞれ58 mm/minと98 mm/minの送り速度、および829 rev/minと757 rev/minのスピンドル回転数で行なわれました。白い層の厚さとともに、切削抵抗およびトルクデータもテスト全体にわたって測定されました。
これらのテスト以降、CoroDrill R840はCoroDrill® 860-GM、CoroDrill R846はCoroDrill® 860-SMに変更されることになりました。これらの次世代工具は、いずれも穴品質に妥協することなく、工具寿命をさらに延ばすよう設計されています。
結果は、白い層の厚さの原因についてのいくつかの価値ある洞察をもたらしました。特筆すべきは、湾曲した径方向の刃先処理のため、CoroDrillでは生成された白い層が少なかったことです。その一方で、CoroDrill R840のストレートな刃先と刃先に施された面取り部は、切削抵抗、トルクおよび白い層の厚さの増加と関係があるものと考えられます。したがって、ドリルの設計が、切削条件を犠牲にすることなく白い層を少なくして高い穴品質を達成できるかどうかを決定することになります。
世界的な航空機メーカーがサンドビック・コロマントと行なったテストは、白い層についての一つまたは二つのことを明らかにしただけでなく、このメーカーは、リーマ加工およびプランジ加工のようないくつかの第二段階の加工を廃止して、時間とコストにおけるメリットを得ることができたのです。その上さらに、この結果はサンドビック・コロマントの超硬ドリルCoroDrill® 860の製品レパートリー設計の 検証ともなったのです。
設計を通じてより良いものを
製品レンジには、全産業分野において加工が難しい鋼 (ISO P)、ステンレス鋼 (ISO M)、鋳鉄 (ISO K) および高硬度鋼 (ISO H) 被削材の穴あけ用の良好なオールラウンダーとして設計されている前述のCoroDrill 860-GMが含まれます。CoroDrill 860-SMは熱耐合金 (HRSA)、チタンおよびインコネルのような耐熱合金 (ISO S) 材種の加工用に最適化されています。後者のドリルは、特に航空宇宙産業で定評があります。
サンドビック・コロマントのエンジニアは、長い工具寿命および良好な穴品質はドリルの設計に依存する、という信念に基づいてCoroDrill 860-GMおよびCoroDrill 860-SMを開発しました。CoroDrill 860-GMは革新的な研磨フルートデザインとなっていて、切りくずの排出を改善しています。また、高いコア強度および穴あけ中の低い切削抵抗を達成しています。
一方、CoroDrill 860-SMには新しい材種が採用され、加工が難しい耐熱合金 (HRSA) の加工時にさらなる工具寿命の改善を実現するためにさらに最適化された刃先形状を備えています。その結果が優れた穴品質です。
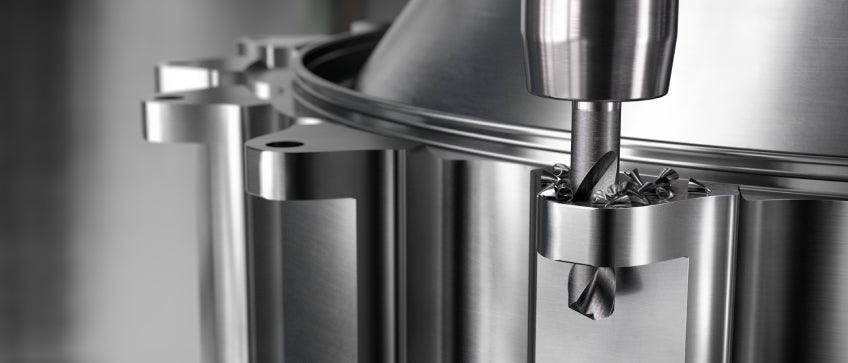
CoroDrill 860-SMの長い工具寿命と良好な穴品質は、ドリルの設計によるものです。
CoroDrill 860は、既に種々の産業分野でのラボテストにおいて定評を得ています。フランスの機械エンジニアリング企業は、AISI 4140構造用鋼の加工のためにCoroDrill 860-GMを採用しました。食いつきが凹部の場合にも凸部の場合にも、良好な真直度および公差で高品質な穴あけを達成することができました。それ以来この会社は、サンドビック・コロマントとの新規取引を開始しました。
もう一社のサンドビック・コロマントのお客様であるイタリアの一般機械産業メーカーは、高強度の鋼合金34CrNiMo6の加工にCoroDrill 860を-GM使用して、それまでの競合他社のドリルに対して、45%の生産性向上を達成しました。工具寿命も2倍になりました。その他にもCoroDrill 860-SMは、インコネル718の加工で素晴らしい結果を達成しました。特にポーランドのカトウィツェで行なわれたテストでは、CoroDrill 860-SMの使用によりCoroDrill R840との比較において180%の工具寿命改善を達成できました。
航空宇宙産業、一般機械産業あるいはその他の分野であれ、どの産業分野であっても、ドリルが目的に対して適切に設計されていれば、高い工具性能が達成可能です。またそれと並行して、サンドビック・コロマントのCoroPlus®ツールガイドのような追加のオンラインツールが、さらなるサポートを提供することができます。ウェブブラウザを介してアクセスし、希望する被削材、穴径および深さを入力すれば、ユーザーは、要求事項に合った最適な超硬工具および切削条件を見つけることができます。
「2回測定して1回で切削する」穴あけがまだ達成されない間は、高性能なCoroDrill 860-GMおよびCoroDrill 860-SMが、どのように穴あけするかという製造業者の再考を手助けします。