Zelenější budoucnost leteckého průmyslu
Výrobci OEM musí ke stavbě letadel budoucnosti přijmout holistický přístup.
Jelikož letecký průmysl patří mezi největší znečišťovatele ovzduší, kteří přispívají ke globálním emisím CO, čelí značnému tlaku, aby přišel s návrhem zelenějších letounů, které budou lehčí a budou schopny překonat delší vzdálenosti. K dosažení tohoto cíle je však nutná práce s těžko obrobitelnými materiály, jako jsou hliník a žárovzdorné superslitiny (HRSA). Sébastien Jaeger, manažer pro průmyslová řešení v oblasti leteckého průmyslu ze společnosti Sandvik Coromant, vysvětluje, jak mohou výrobci OEM v leteckém průmyslu zavádět pokročilá nástrojová řešení zajišťující, že obrábění těchto obtížných součástí zůstane udržitelné.
Podle Světového ekonomického fóra (WEF) „dosažení nulových emisí CO do roku 2050 nejenže pomůže vytvořit ekologicky udržitelnou budoucnost, ale zároveň zajistí, že letecký průmysl jako celek bude finančně odolný a konkurenceschopný“. Avšak zatímco v segmentu automobilového průmyslu se stále intenzivněji prosazuje elektromobilita – v srpnu 2021 předstihl ve Spojeném království prodej elektromobilů prodeje dieselových vozů – v leteckém průmyslu se tento vývoj projeví až za delší dobu.
Nelze předpokládat, že by se letadla poháněná elektřinou rozšířila do běžného provozu dříve než v roce 2035. Lonely Planet uvádí, že navzdory tomu, že společnost easyJet doufá, že bude schopna provozovat elektřinou poháněná letadla na trasách dlouhých do 500 km do roku 2030 a Norsko plánuje obsluhovat všechny lety na krátkou vzdálenost elektrickými letadly do roku 2040, „na létání na dlouhé vzdálenosti v dobíjecích jumbech si ještě dlouho počkáme – akumulátory jsou zkrátka příliš těžké.“
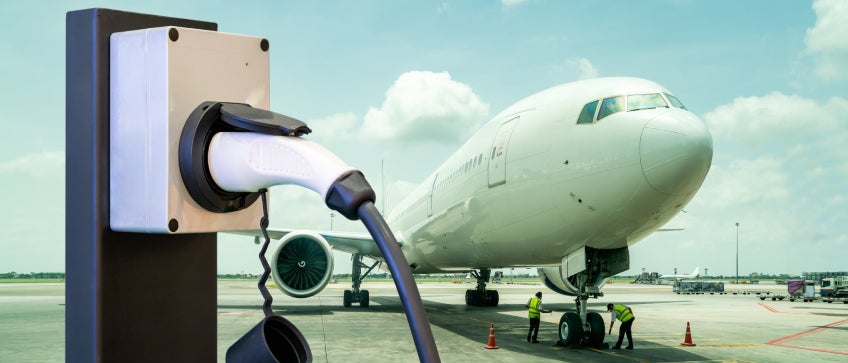
Elektrická letadla se podle očekávání rozšíří až v roce 2035.
Aby byly akumulátory reálně použitelné, musí klesnout jejich hmotnost; zároveň s tím na bedrech výrobců OEM spočívá břemeno v podobě požadavků na výrobu lehčích součástí, aby problém s hmotností akumulátorů vyvážili. Můžeme si být jisti, že k odlehčení těchto systémů se bude používat hliník – zvláště nové typy hliníku s vyšší pevností, odolností vůči únavovému opotřebení a dalšími pokročilými vlastnostmi.
Jsme rovněž svědky intenzivnějšího využívání nových žárovzdorných superslitin (HRSA). Ty se ve skutečnosti již dnes používají v leteckých součástech, na které jsou kladeny extrémní nároky na výkonnost, protože si uchovávají svou tvrdost i za vysokých teplot. Tyto vlastnosti materiálů se prokážou jako zcela zásadní, jelikož jednou z cest k dosažení udržitelnější letecké dopravy bude provozování motorů při vyšších zatíženích a teplotách.
Součásti se musí vyrábět s přísnějšími tolerancemi a variabilnějšími konstrukcemi. Stejně jako u elektromobilů i konstrukce elektrických letadel zítřka – včetně draků letounů a motorů – se budou mezi jednotlivými výrobci lišit více, než tomu je u stávajících strojů se spalovacími motory. V případě trupu letounu někteří výrobci OEM zkoumají koncepce deltovitého tvaru, trupu se splývajícími křídly (BWB – Blended Wing Body) a koncepci vyztuženého nosného křídla. Jiní výrobci OEM se drží tradiční konstrukce skládající se z „velké trubky, křídel a motoru“.
Budeme se rovněž setkávat s různými druhy architektury motorů od elektrifikovaných, akumulátorových nebo elektromagnetických až po hybridní motory, kde budou stávajícím motorům v pohonu asistovat elektromotory. Výrobci budou nuceni vyrábět stále více součástí s přísnějšími tolerancemi a rovněž nacházet způsoby k snížení hluku, hmotnosti a emisí – což jsou všechno faktory, které ovlivňují celkovou výkonnost elektrických systémů. Součásti z hliníku a žárovzdorných superslitin jsou však těžko obrobitelné a dosažení tohoto cíle udržitelnou a cenově výhodnou cestou bude veliká výzva.
Rychlý postup vpřed
Jednou cestou, jak lze vyrábět lehčí letadla s účinnějším využitím paliva, je aditivní výroba (AM). Aditivní výroba umožňuje vývoj velmi komplexně tvarovaných, individuálně konstruovaných součástí a funkčních výrobků s přísnými tolerancemi, a složitě obrobitelné součástí, jako například příhradové struktury, tak bude možné vyrábět snadněji. Podle zjištění softwarové společnosti Dassault Systemes „v oblasti leteckého průmyslu může snížení hmotnosti v důsledku zavedení aditivní výroby přinést až 25procentní úsporu energie“, zatímco „každý kilogram, o který se sníží letová hmotnost, může na nákladech na palivo ušetřit každoročně až 3 000 amerických dolarů“.
Je však aditivní výroba sama o sobě udržitelná? Studie, na níž se podílelo oddělení konstrukčního strojírenství Rumunské technické univerzity v Kluži, popisuje, že aditivní výroba je „skvělou alternativou k tradičním výrobním metodám, jako je tlakové vstřikování, odlévání nebo obrábění“. Dále se v ní uvádí: „AM má potenciál snížit náklady a dosáhnout lepší energetické účinnosti než konvenční procesy.“
AM bude mít rovněž zásadní vliv na způsoby výroby produktů a jejich diverzitu. K výhodám náleží mimo jiné snížení uhlíkových emisí, spotřeby materiálů a nároků na přepravu, protože součásti lze vyrábět interně namísto jejich dovážení z jiných výrobních závodů.
Díky rychlé přípravě prototypů mohou výrobci mohou rovněž vyrábět komplexnější, kompaktnější a inovativní součásti pro letecký průmysl. Rychlá příprava prototypů zahrnuje několik různých technik, ale cílem je rychlá výroba fyzického 3D prototypu ze souboru CAD (počítačem podporované projektování). S těmito prototypy lze provádět maloobjemové zkoušky nových materiálů ještě před zahájením sériové výroby, aby se ověřilo, že se součásti vyrábějí s nejvyšší možnou mírou inovace, kvality a přesnosti.
Podívali jsme se na to, jakým způsobem mohou výrobci OEM v leteckém průmyslu zavádět nové metody výroby komplexnějších součástí. Jak je to ale s výběrem správných nástrojů pro danou úlohu, zvláště pokud jde o obrábění houževnatého hliníku nebo žárovzdorných superslitin?
Tyto materiály vyžadují použití nástrojů s vyšší odolností vůči opotřebení a delší životností. Právě z tohoto důvodu vyvinula společnost Sandvik Coromant nástrojovou třídu ocelových břitových destiček S205 používaných k soustružení. Metalurgie materiálu S205 zahrnuje vrstvu Inveio® tvořenou krystaly uspořádanými v těsné mřížce a orientovanými v jednom směru. Tato vrstva vytváří silnou ochrannou bariéru kolem břitové destičky, nástroj tak zpevňuje a zlepšuje jeho mechanické vlastnosti. Tato břitová destička se již osvědčila ve výrobě celé řady leteckých součástí včetně disků turbín leteckých motorů, kroužků a hřídelí. Zákazníci společnosti Sandvik Coromant již při použití třídy S205 hlásí o 30 až 50 % vyšší řezné rychlosti v porovnání s konkurenčními třídami pro soustružení žárovzdorných superslitin.
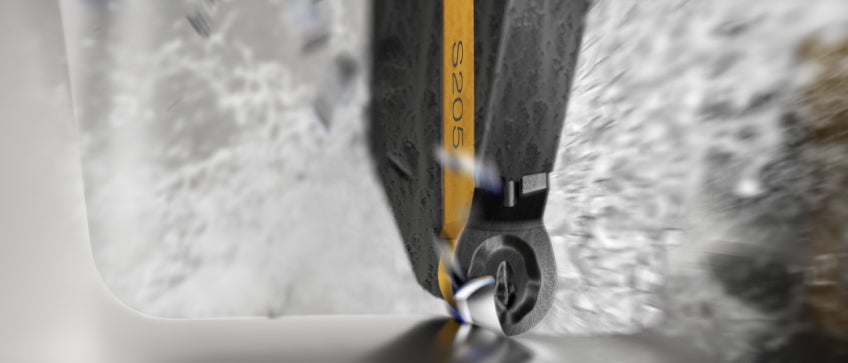
Holistický přístup
Již jsme se zaměřili na výrobní procesy a nástroje, ale jak tyto dva prvky nejlépe kombinovat? Snahy o sestavení uceleného řešení mohou být nakonec ztrátou času, pokud nejsou systémy navrženy tak, aby spolu dobře fungovaly.
Za tímto účelem poskytuje společnost Sandvik Coromant svým zákazníkům z oblasti leteckého průmyslu podporu v podobě tzv. řešení pro specifické součásti. Takové řešení zahrnuje několik fází včetně zkoumání požadavků na strojní vybavení a provádení časových studií ke stanovení nákladů na jednu součást. Dále se jedná o analýzu výrobních metod při realizaci, které se vztahují k metodě časového měření (MTM – Methods-Time Measurement) i k procesům u koncového uživatele. Řešení pro specifické součásti rovněž zahrnuje programování počítačem podporované výroby (CAM) a projektový management lokálních i přeshraničních projektů.
U jednoho ze zákazníků společnosti Sandvik Coromant, který ve své výrobě čelil problémům s lámáním třísek, toto řešení pro specifické součásti umožnilo detekovat příčinu a navrhnout odpovídající řešení. Specialisté společnosti Sandvik Coromant pro tohoto zákazníka vyvinuli novou strategii s dynamickými křivkami pohonu, která umožnila kontrolovat lámání třísek v každém okamžiku. Tento nový přístup jsme nazvali „lopatkové soustružení“ a tuto technologii jsme si nechali patentovat. Díky lopatkovému soustružení dosáhl tento zákazník zkrácení doby cyklu o 80 %, navíc s vynikající kontrolou utváření třísek a dvojnásobnou životností nástrojů.
Zákazník byl navíc schopen omezit vytížení strojů ze čtyř na jeden, a tím i potřebu využívání strojů na více než jednu úlohu, čímž se zvýšila bezpečnost obráběcích procesů a snížila četnost odstávek v důsledku alarmů na strojích. Omezené vytížení strojů a schopnost dokončit výrobní dávky s nižším počtem výměn nástrojů díky houževnatějším třídám obrábění, jako je například S205, budou klíčové aspekty při výrobě udržitelných letadel.
Zásadní úlohu bude hrát také software, jako například CoroPlus® Tool Guide, který tvoří součást digitálního portfolia společnosti Sandvik Coromant. Zákazníci mohou přijímat zásadní rozhodnutí ohledně volby nástroje řezných parametrů ještě dříve, než vůbec zahájí výrobu.
Uzavřená smyčka
Vedle nových přístupů k nástrojům a výrobě mohou výrobci OEM z leteckého průmyslu obrátit svoji pozornost také k udržitelnosti výroby. Podle zprávy Air Transport Action Group (ATAG) společnost Kaiser, která dodává hliník letecké společnosti Boeing, nyní zavádí uzavřený recyklační systém – jeden z největších programů svého druhu v daném odvětví. Společnost Kaiser odhaduje, že se v tomto odvětví v rámci jejího schématu každoročně recykluje kolem deseti milionů kilogramů kovových odřezků a šrotu.
Ve společnosti Sandvik Coromant jsme uvedli v život vlastní systém recyklace nástrojů ze slinutých karbidů, v jehož rámci vykupujeme opotřebené nástroje ze slinutých karbidů zpět od zákazníků a znovu je využíváme k výrobě zbrusu nových. Ve výsledku tak většina surovin použitých při výrobě nástrojů Sandvik Coromant ze slinutých karbidů pochází z kovového odpadu. V praxi naplňujeme udržitelný způsob podnikání v podmínkách omezených zdrojů a minimalizujeme nadměrné plýtvání a tvorbu odpadů. Tímto způsobem jsme zjistili, že výroba nástrojů z recyklovaného materiálu vyžaduje o 70 % méně energie a současně dochází k snížení emisí oxidu uhličitého o 40 %.
Letecký průmysl čelí značnému tlaku, aby přišel s návrhem zelenějších letounů, které budou lehčí a budou schopny překonat delší vzdálenosti. Volbou správných procesů a nástrojů – nemluvě o holistickém přístupu k výrobě – však výrobci OEM pro letecký průmysl mohou přispět k zelenější budoucnosti celého leteckého průmyslu.