Soustružení exotických materiálů
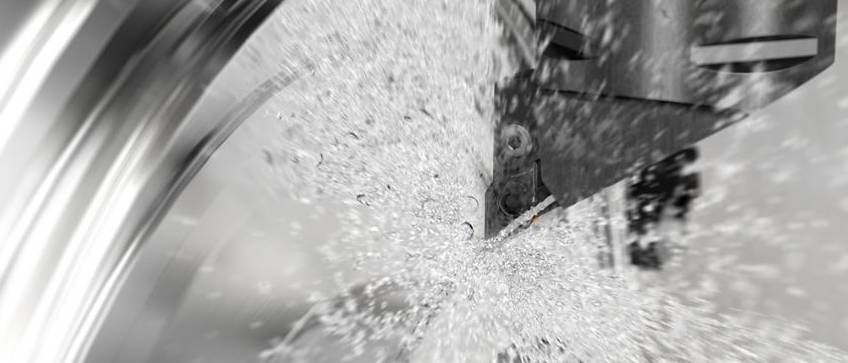
Žárovzdorné slitiny a slitiny titanu jsou náročné na obrábění. Nejsou stejné jako jiné kovy, a proto jsou označovány jako exotické materiály. Mají vynikající vlastnosti, jako například poměr pevnost/hmotnost, zachovávání pevnosti a tvrdosti při vysokých teplotách a vynikající odolnost vůči korozi.
Jelikož jsou však tyto materiály rovněž náročné na obrábění, vyžadují „exotická“ řešení. Ta musí být dobře naplánovaná se specifickými nástroji a pečlivě zvolenými metodami a drahami nástrojů, aby bylo možné dosáhnout efektivity, bezpečnosti a dobrých výsledků.
V tomto přehledu jsou uvedeny požadavky na obrábění a vývojové kroky, které zvýšily výkonnost a bezpečnost soustružení.
Součásti s jedinečnými vlastnostmi, ale náročné na obrábění
Schopnost obrobit materiál určité součásti závisí na několika faktorech, které ovlivňují a definují požadavky a výstupy při obrábění kovů. Obecně řečeno se jedná o vztahy mezi obrobitelností materiálu dané součásti, tendencí k opotřebení nástrojů a způsobem utváření třísky. S tím rozdílem, že podle většiny parametrů jsou tyto exotické materiály těžko obrobitelné. Jejich obrábění je považováno za náročné – ale nikoli složité, pokud se k němu přistoupí správně.
Exotičtější z relativně běžných materiálů spadají do skupiny ISO S: žárovzdorné superslitiny (HRSA) a slitiny titanu. Pro účely obrábění lze tuto skupinu rozdělit do několika podskupin v závislosti na složení, stavu a vlastnostech daného materiálu. Chemická povaha a metalurgické složení slitiny třídy S určují její fyzikální vlastnosti a tím i obrobitelnost. Kontrola utváření třísky je obecně náročný aspekt kvůli segmentaci třísek a není neobvyklé, že je nutné použít dvojnásobnou řeznou sílu než při obrábění oceli (jedná se o přímý ukazatel toho, jak těžké je materiál obrábět, a určuje potřebnou řeznou sílu a výkon).
Hlavním důvodem, proč jsou žárovzdorné superslitiny náročné na obrábění, je skutečnost, že si uchovávají vysokou tvrdost i při vysokých teplotách. Nedochází k jejich změkčování a tavení tak, jak je to známo u většiny jiných materiálů, a také je u nich patrná značná tendence k vytvrzování při zpracování. Vysoké mechanické a značné tepelné zatížení se koncentruje na řezné hraně. Slitiny na bázi niklu, železa nebo kobaltu jsou podskupinami v rámci žáruvzdorných slitin a mají jedinečné vlastnosti pro následné využití vyrobené součásti, a to především v leteckém, energetickém a zdravotnickém průmyslu, jelikož se jejich vlastnosti mění až při teplotách blízkých teplotě tavení. Jsou rovněž velice odolné vůči korozi. Z hlediska obrobitelnosti však vyžadují výkonný stroj, pevné uspořádání, specifické třídy a geometrie břitových destiček, optimalizovaný přívod řezné kapaliny a v neposlední řadě také správnou metodu obrábění a přístup nástroje. Je tedy zapotřebí více plánování a přípravných činností před výrobou.
Slitiny titanu se také dále dělí do podskupin s různými stupni obrobitelnosti. Obrobitelnost obecně odpovídá různým stupňům obtížnosti (tj. houževnatosti), která následně klade speciální nároky na použité nástroje a metody. Tyto nároky vyplývají z nízké tepelné vodivosti, vysoké pevnosti při vysokých teplotách, vzniku vysoce smykově deformovaných tenkých třísek s tendencí k oděru, což vede k tvorbě úzké kontaktní plochy na čele břitových destiček a vysokých řezných sil koncentrovaných v blízkosti řezné hrany. Třísky se mohou vytvářet cyklicky, což má za následek kolísání řezných silám, přičemž některé slitiny mají relativně vysoký obsah karbidů, a jsou proto zvlášť abrazivní. Nadměrné řezné síly mohou vyvolávat chemické reakce mezi třískou a materiálem nástroje, jejichž důsledkem je náhlé vylamování/lámání břitu či ulpívání/navařování materiálu na řezných hranách. U některých slitin dochází v průběhu zpracování také k vytvrzování, které zapříčiňuje difúzní opotřebení vedoucí k nadměrné tvorbě výčnělků. To pak může znesnadnit také následné operace.
Tyto materiály jsou sice exotické, ale rozsah parametrů nutných k úspěchu při obrábění je u mnoha žáruvzdorných slitin a slitin titanu relativně úzký.
Při soustružení těchto materiálů…
… závisí úspěšný výsledek na rovnováze kombinovaných vlivů materiálu a aplikačních faktorů. K dobrým výsledkům přispívá značnou měrou několik základních pravidel:
- co nejpodrobnější naplánování vhodné strategie obrábění,
- stanovení nejlepšího přístupu nástroje,
- stanovení nejlepších drah nástroje a použití velmi stabilního upínání nástrojů,
- použití toho nejlepšího z nových, specifických obráběcích technologií,
- použití správných řezných podmínek k zajištění bezpečnosti a produktivity procesu,
- použití výpočtů spirálových drah nástrojů k predikci řezů,
- správné používání řezné kapaliny – moderních vysokotlakých řešení,
- využití doporučení a podpory od specialistů.
Vzhledem k souvisejícím kritickým a rozhodujícím faktorům, jako je například aktuální stav materiálu obrobku, by obrábění mělo probíhat vždy až po pečlivém naplánování. Na součásti má značný vliv to, zda jsou odlévané, kované, zda jde o tyčový materiál, zda jsou tepelně zpracované, normalizačně žíhané nebo zda jde o vystárnutý materiál, a tyto faktory by se měly zohlednit při výběru použitých nástrojů a metod. Obrábění je rovněž ovlivněno stavem povrchu obrobku a jeho tvrdostí. Soustružnická strategie by měla rovněž obsahovat požadavky vyplývající z konstrukčních vlastností dané součásti, která se má obrábět, dále by měla brát v potaz různé fáze obrábění a rozlišovat mezi hrubováním (první fáze), polodokončováním (střední fáze) a dokončováním (poslední fáze). Problémy často představují i komplexní prvky a integrita povrchu.
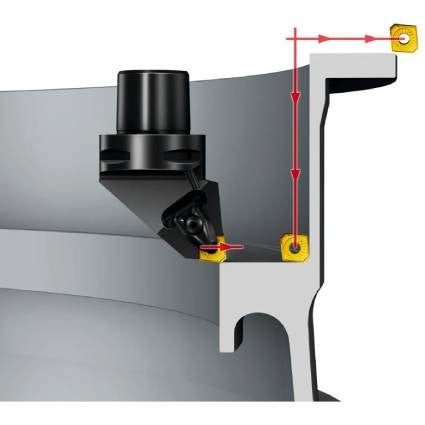
Při plánování soustružení exotických materiálů tvoří základ pro rozhodování konstrukce součásti, její materiál a stav materiálu. Pokud je to relevantní, stanovte, jak se má provádět první, střední a poslední stadium obrábění, a to ve vztahu k stavu materiálu a kvalitativním požadavkům. Plánování drah nástrojů a snížení rychlosti posuvu při programování určí, jakého rozsahu dosáhne opotřebení, jaký typ nástrojů bude třeba použít či jaké budou časy cyklů a bezpečnost procesu.
Řezná akce v těchto materiálech…
… je do značné míry ovlivňována způsobem vstupu řezné hrany do obrobku. Úhel nastavení řezné hrany v kombinaci s geometrií břitové destičky zásadně určuje výkonnost, životnost nástrojů, bezpečnost a výsledky. Tvary břitových destiček se často musí volit v těsném souladu s uvažovaným řezem. Skutečnost, že malý úhel nastavení přispívá k prodloužení výkonnosti a životnosti nástroje, by však měla být vždy klíčovým aspektem, který je třeba u dané aplikaci zvážit.
Třídu břitové destičky je nutné zvolit zčásti ve vztahu k úhlu nastavení. Tento úhel mimo jiné ovlivňuje typ opotřebení, které na řezné hraně vytváří vrub, jehož velikost ovlivňuje výsledky a může způsobit předčasné selhání nástroje. Pokud se zvolí fáze vstupu nástroje do obrobku správně, znamená to také, že lze zvolit třídu břitových destiček dosahující vyšší produktivity a současně zajistit delší životnost nástroje a bezpečnost procesu.

Úhel nastavení obráběcího nástroje ovlivňuje tloušťku třísky, rychlost posuvu, řezné síly a rovněž proveditelné typy řezů. U exotických materiálů má volba úhlu přímé důsledky na produktivitu a spolehlivost procesu a dále ovlivňuje tvar břitové destičky, zaoblení špičky a míru možného využití materiálu nástroje. Nejlepší volbou jsou obvykle kruhové břitové destičky a destičky typu xcel.
Výběr materiálu nástroje (třída břitové destičky) by měl proběhnout v souladu se zvažovaným typem soustružení, tedy zda se jedná u hrubování, polodokončování, nebo dokončování, a rovněž stavem obrobku a typem řezu. Vzhledem k tvrdosti těchto materiálů by se při výběru třídy břitových destiček vždy měla uvážit plastická deformace řezné hrany jakožto primární rizikový faktor (opotřebení ve tvaru vrubu, jak bylo zmíněno, je ovlivněno především úhlem nastavení a hloubkou řezu). Výběr třídy břitových destiček by se měl rovněž kombinovat s jejich tvarem, jelikož souvisí s pevností, kterou je třeba hodnotit zároveň se způsobem vstupu do řezu, průřezem třísky či tím, zda je řez spojitý, nebo přerušovaný. Pro obrábění žárovzdorných superslitin je tedy zásadní zvolit třídu destiček určenou speciálně na toto použití.
Primární požadavky jsou kladeny na vysoký stupeň tvrdosti břitových destiček při vysokých teplotách, jejich správnou houževnatost a dostatečnou adhezi povlaku. Vyměnitelná břitová destička pro tyto materiály by měla vykazovat pozitivní geometrii břitu, ostrou a silnou řeznou hranu a relativně otevřený lamač třísky.
Pro úspěch obrábění těchto materiálů je zásadní stanovení nejvhodnějších řezných podmínek. Řeznou rychlost omezuje kombinace otáček, posuvu a hloubky řezu a lze ji optimalizovat tak, aby se dosáhlo vysoké produktivity, bezpečnosti a kvality. Řezná rychlost souvisí s tvorbou tepla a tím, jak toto teplo ovlivňuje břitovou destičku; rychlost musí být dostatečná k tomu, aby tříska měla dostatečnou plasticitu, ale ne příliš vysoká, aby nedošlo k nerovnováze v materiálu nástroje. Rychlost se obvykle pohybuje v rozsahu 40 až 80 m/min při použití specifických břitových destiček ze slinutých karbidů a v rozsahu 150 až 400 m/min u keramických břitových destiček.
Rychlost posuvu je hlavní faktor, který ovlivňuje dobu v řezu a tloušťku třísky. V exotických materiálech musí být tyto aspekty vyváženy pečlivěji, jelikož rozsah mezních hodnot je relativně úzký: Při hrubování musí být dosaženo maximální velikosti třísek, ale nikoli takové, která by vedla k přetěžování břitu, zatímco při dokončování musí být tříska dostatečně tlustá, aby se předcházelo nadměrné tvorbě tepla a vytvrzování obrobku při zpracování.
Hloubka řezu často ovlivňuje způsob přibližování řezné hrany k obrobku, a proto musí ležet pod určitou hodnotou. Například při použití kruhových břitových destiček v žárovzdorných superslitinách by hloubka řezu neměla překročit 15 % průměru destičky. Hloubku řezu je nutné pečlivě naprogramovat i při tvarovém obrábění. Při programování obrábění je nutné zohlednit i zahloubení a rohy, aby během záběru řezné hrany nedošlo k překročení vhodného poloměru oblouku.
Z hlediska životnosti nástroje je důležité intenzivně pracovat se spirálovou dráhou nástroje (SCL). Její správné nastavení umožní předvídat běh stroje, naprogramovat jeho zastavení za účelem výměny břitových destiček a dalším přínosem bude skutečnost, že průchody nástroje bude možné realizovat se správnou rychlostí, aniž by řezná hrana přestala poskytovat požadovanou kvalitu obrobené plochy.
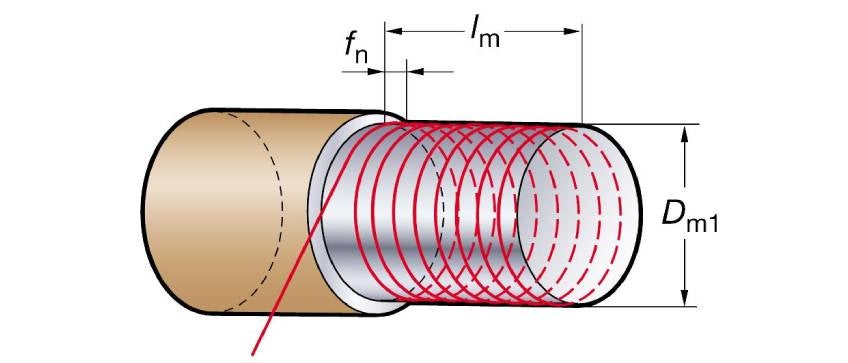
Výpočet spirálové dráhy nástroje pomůže předvídat dobu v řezu nebo řeznou délku, zkrátit tak strojní čas a zdokonalit strukturu povrchu při obrábění náročných exotických materiálů. Zastavení stroje za účelem výměny břitových destiček se poté plánuje s ohledem na spirálovou dráhu nástroje, aby lépe vyhovovalo dané operaci a řezným podmínkám a v důsledku toho přineslo optimalizaci životnosti nástroje a využití obráběcího stroje.
Opotřebení nástroje do značné míry ovlivňují…
… vysoké řezné síly v kombinaci s vyššími teplotami působícími na řeznou hranu, což má často za následek vznik určitých typů opotřebení břitu. K hlavním z nich patří zmíněné opotřebení ve tvaru vrubu (typ mechanického opotřebení, kde hloubka řezu kopíruje linii materiálu obrobku); plastická deformace břitu – důsledek kombinace vysoké teploty a tlaku, a konečně abrazivní opotřebení vyskytující se zejména při obrábění tvrdších materiálů. Dalším typem opotřebení je vyštipování čela, ke kterému dochází na keramických břitových destičkách, u nichž se odlupují vrstvy v horní části břitu. Hlavní úlohu zde hraje způsob vstupu břitu do řezu.
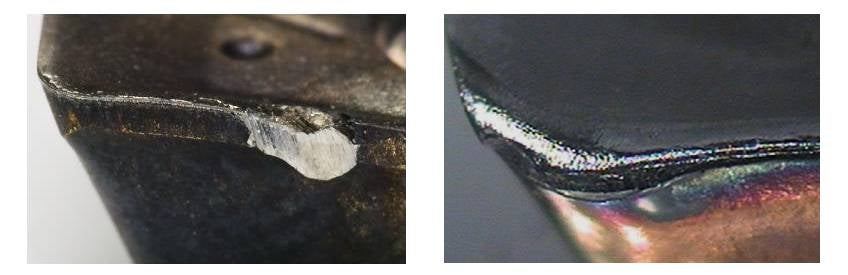
Výběr třídy břitových destiček používaných k obrábění exotických materiálů nesouvisí přímo s rozdílem mezi hrubováním a dokončováním do takové míry, jak je tomu u jiných materiálů. Namísto toho jde spíše o faktor zajišťující optimalizaci procesu – faktor, jehož stanovení je složitější a závisí na tvaru břitové destičky, způsobu vstupu břitu do obrobku a typu operace. Výskyt častých druhů opotřebení, jako je například uvedené opotřebení ve tvaru vrubu či plastická deformace, se musí omezovat především kombinací vhodných nástrojů, řezných podmínek a metody. Nejvhodnější a široce použitelnou volbou bývají břitové destičky ze slinutých karbidů společně s moderní keramikou na bázi SiAlON a do určité míry také whiskery vyztužená keramika.
Při soustružení exotických materiálů je nejvhodnější malý úhel nastavení s hodnotou nejvýše 45°. Nejhorší podmínky představuje úhel nastavení 90/0 stupňů nebo hloubka řezu větší než zaoblení špičky použité břitové destičky. Velký/malý úhel s sebou nese vznik tenkých třísek a možnost použití vyšší rychlosti posuvu.
Při soustružení žárovzdorných superslitin úhel nastavení určí, zda je vhodnější břitová destička s povlakem PVD, nebo CVD. Ten je důležitý kvůli ochraně proti tepelným účinkům. Povlak PVD je vhodný pro úhel nastavení 90/0 stupňů, povlak CVD pak pro úhel 45 stupňů. Oproti tomu při soustružení titanu nepřináší povlak břitových destiček znatelné výhody. V tomto případě je důležitějším faktorem vhodný tvar břitu, například kulaté břitové destičky pro dokončování. Nové řady břitových destiček s povlakem PVD poskytují vysokou tvrdost a dobrou odolnost vůči deformaci břitu a teplotním rázům. V kombinaci s ostrými břity mohou rovněž při obrábění ulpívajících materiálů dosahovat vynikajících výsledků v celé škále operací od hrubování po dokončování.
Správný tvar břitové destičky…
… představuje důležitý faktor pro její použití při obrábění těchto materiálů. Kruhové destičky (tvar R) se staly jednou z hlavních doporučovaných možností pro obrábění těchto materiálů. Kruhové břitové destičky jsou dostatečně pevné na to, aby bylo dosaženo ostré, pozitivní řezné hrany, nabízejí různou tloušťku třísky podél řezné hrany, čímž umožňují dosažení vyšších rychlostí posuvu, vyznačují se velkým poloměrem zaoblení, který neomezuje rychlost posuvu z důvodu vytvářené struktury povrchu. Kruhové břitové destičky dále přinášejí možnost flexibilního programování a lze je využít k tvarovému obrábění a výrobě dutin, které jsou nezbytné k výrobě součástí různých tvarů.
Čtvercové břitové destičky (tvar S) jsou v některých případech nejvhodnější na první stadium obrábění, jelikož umožňují provádět hrubovací řezy v různých směrech pod úhlem 45 stupňů. Kosočtvercové břitové destičky (tvar C) se vyznačují flexibilitou z hlediska dráhy nástroje, a pokud jsou prodlouženy do podoby břitových destiček typu xcel, poskytují ještě lepší přístup nástroje do vnitřních či vnějších rohů či při vytváření oddělovacích a odlehčovacích zápichů. Tato kombinace tvaru břitové destičky a úhlu nastavení 45 stupňů rovněž snižuje radiální řezné síly, zajišťuje konstantní tloušťku třísky a omezuje opotřebení ve tvaru vrubu. Výsledkem je vyšší produktivita, delší životnost nástroje a vyšší bezpečnost.
Optimalizace programu…
… je důležitým hlediskem, přičemž v následujícím textu naleznete doporučení, která vám pomohou zvýšit výkonnost, zvláště při použití kruhových břitových destiček, které jsou obecně vhodné pro obrábění exotických materiálů:
- vyhýbejte se ponornému vstupu do řezů a tlumte nárazy; pokud jsou tyto řezy nezbytné, snižte rychlost posuvu na polovinu;
- také při obrábění rohů by se měl posuv snížit na polovinu nebo by měl nástroj narolovat do rohu tam, kde naprogramovaný rádius dopovídá průměru břitové destičky. (Doporučení platí pro případ, kdy minimální programovaný rádius činí přibližně 25 % průměru břitové destičky a poloměr součásti 75 % průměru břitové destičky. Posuv ve středu nástroje je uveden pro programovaný rádius.);
- pro hrubování pomocí kruhových břitových destiček nastavte programovaný rádius na stejnou hodnotu, jako je průměr břitové destičky, a pro dokončovací operace dbejte na to, aby byl programovaný rádius větší než průměr břitové destičky;
- uvažte alternativní dráhy nástroje, více samostatných průchodů a obrábění v obou směrech, abyste břitové destičky plně využili;
- zajistěte ochranu keramických břitových destiček předběžným sražením hran obrobku a vstupem nástroje v oblasti zkosení;
- během obrábění udržujte vhodnou rovnováhu mezi úhlem nastavení a obloukem záběru břitové destičky. Omezení úhlu je zásadní pro dobrou výkonnost, zatímco použití kruhových břitových destiček je důležitým faktorem pro lepší využití potenciálu nabízeného moderními třídami břitových destiček;
- zamezte namotávání třísek při tvarovém obrábění nebo ponorném frézování, aby nedocházelo k přetěžování břitové destičky, nebo použijte alternativní dráhy nástroje či břitové destičky s menším průměrem;
- zvažte využití trochoidálního soustružení a rozdělení řezu do vhodných menších řezů, zvláště při výrobě dutin.
Co byste měli sledovat u typů nástrojů a metod pro obrábění žárovzdorných superslitin a titanu? Zde je několik hlavních hledisek:
- Vždy by se mělo uvažovat o použití přesného přívodu řezné kapaliny. Přívod řezné kapaliny za řeznou hranu a přímo k ní prostřednictvím nástrojů s vnitřním přívodem přináší množství výhod při soustružení, frézování a vrtání. Nejnovější technologii trysek, dostupnou jako standardní nebo konstrukčně přizpůsobené řešení s různými rozsahy tlaku, lze využívat u všech typů strojního vybavení s odpovídajícím přívodem řezné kapaliny. S ohledem na lepší utváření třísky by nové stroje, do kterých plánujete investovat a jež budou sloužit k soustružení titanových součástí, měly nabízet možnost nastavení tlaku řezné kapaliny na hodnotu 70 bar, ale vzhledem k horšímu odlamování třísky v případě obrábění žárovzdorných slitin je výhodný tlak až 200 bar.
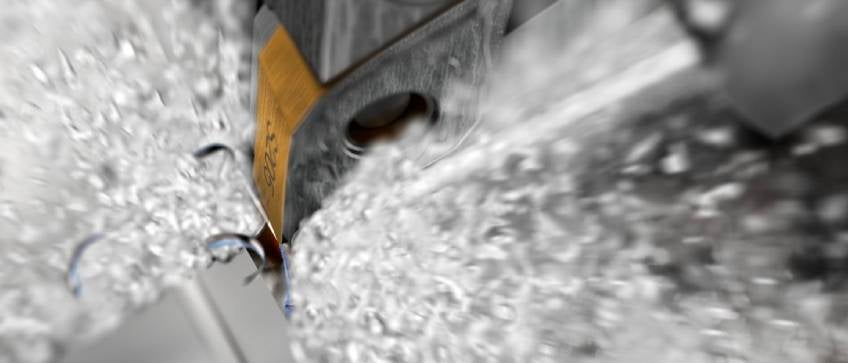
Použití řezné kapaliny je při obrábění exotických materiálů rozhodující faktor. Používání přesného přívodu řezné kapaliny je v současnosti technicky vyspělou technologií dodávanou jako standard nebo jako konstrukčně přizpůsobené řešení a poskytuje jasné pozitivní účinky na řez, utváření třísky, životnost nástrojů a produktivitu. Vysoké teploty vznikající při obrábění těchto materiálů obecně vyžadují odpovídající chlazení, ale pokud je dodáváno dostatečné množství řezné kapaliny, za vysokého tlaku a s přesným směrováním, dochází v kombinaci se specifickými břitovými destičkami a vnitřním přívodem řezné kapaliny k optimalizaci výkonnosti a výsledků operací.
- Při soustružení exotických materiálů dochází často k problémům s přístupem do místa řezu. Složité tvary a vyložení nástroje způsobují, že správná volba nástrojového vybavení a metod je zcela zásadní. Podívejte se na modulární systémy, které nabízejí spolehlivou koncepci obashující nožové planžety s řeznými hrany v různých úhlech a různým vyložením nástroje. Nabídka adaptérů a planžet by měla být dostatečně flexibilní na to, aby bylo možné z nevelkých zásob standardních nástrojů vytvořit téměř jakýkoliv nástroj, který bude vyhovovat dané konfiguraci a umožní práci v omezeném prostoru uvnitř i vně obrobku.Planžety by měly mít požadovanou pracovní vůli v radiálním i axiálním směru, aby bylo možné dosáhnout hluboko do úhlových drážek, a nabízet přesný přívod řezné kapaliny k břitu tělem nástroje.
- Materiál nástroje je ústředním bodem každé obráběcí operace a u exotických materiálů představuje zásadní faktor. V této oblasti obrábění je zapotřebí použít specifické třídy břitových destiček v kombinaci se správnou geometrií, převážně v podobě nejnovějších typů ze slinutých karbidů a keramiky. Nepovlakované karbidové třídy zaujímají důležitou pozici i nadále, ale nejnovější vývoj v oblasti technologií povlaků břitových destiček přinesl speciálně povlakované břitové destičky ze slinutých karbidů, které dále zvýšily výkon břitů tím, že umožnily zkrátit dobu v řezu a prodloužit životnost nástrojů.
- K minimalizaci sklonů k vibracím by se měly využívat vyvrtávací tyče, nožové planžety, či dokonce frézy s integrovaným tlumením. U antivibračních technologií došlo ke skokovému pokroku a měly by být přirozenou volbou zvláště v případech, kdy vyložení nástroje obvykle způsobuje destabilizaci procesu. Produktivita, bezpečnost procesu a kvalita obrobené součásti jsou faktory, které přímo souvisí s kvalitou a dostupností tlumeného nástrojového vybavení. Bez této technologie nelze řadu operací dokonce vůbec provádět: v současnosti je možné velmi efektivně a s vysokou kvalitou obrobeného povrchu vykonávat dokonce vnitřní soustružení s vyloženími nástroje v délce až čtrnáctinásobku průměru, jenž může dosahovat až 250 mm.