Vantaggi del refrigerante di precisione per la lavorazione dei materiali utilizzati nel settore aerospaziale
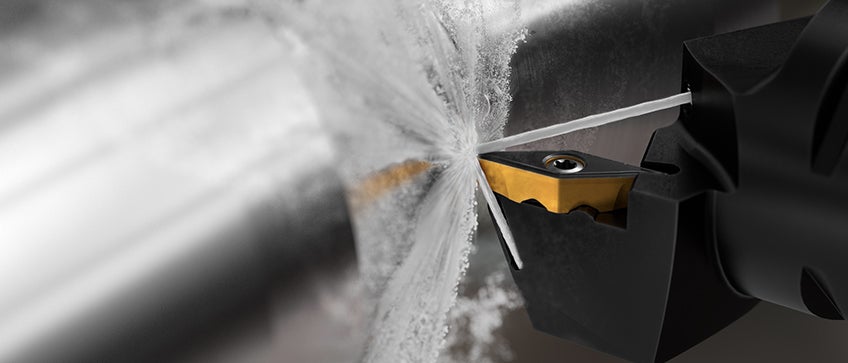
Il ruolo dei refrigeranti nella lavorazione dei componenti aerospaziali ha subito una certa evoluzione. Per molti anni, in presenza di materiali la cui lavorazione imponeva l'uso di refrigerante, le officine meccaniche indirizzavano i tubi in modo da inondare tutta la zona di taglio. Ma ora, applicando accuratamente il refrigerante ad alta precisione nella zona di lavorazione, è possibile accedere a nuovi vantaggi. Il ricorso a questa tecnologia è stato favorito dalla maggiore capacità dei sistemi di adduzione del refrigerante di molte macchine CNC, oltre che dalle nuove soluzioni di attrezzamento.
Fare la differenza
Per fare la differenza, il refrigerante deve essere applicato efficacemente ovvero direzionato in modo corretto ed erogato con getti ad alta precisione e in volume sufficiente. Disporre di un certo flusso di refrigerante o inondare la zona di lavorazione non è sufficiente. L'applicazione ragionata di refrigerante ad alta precisione può, invece, fare la differenza per quanto riguarda:
- formazione dei trucioli,
- distribuzione del calore
- incollamento del materiale del pezzo sul tagliente,
- integrità superficiale,
- usura dell'utensile.
Questi fattori di lavorazione di base incidono, a loro volta, sulla produzione permettendo di migliorare gli aspetti che decidono la competitività:
- produttività,
- durata utensile,
- controllo ed evacuazione truciolo,
- qualità dei componenti.
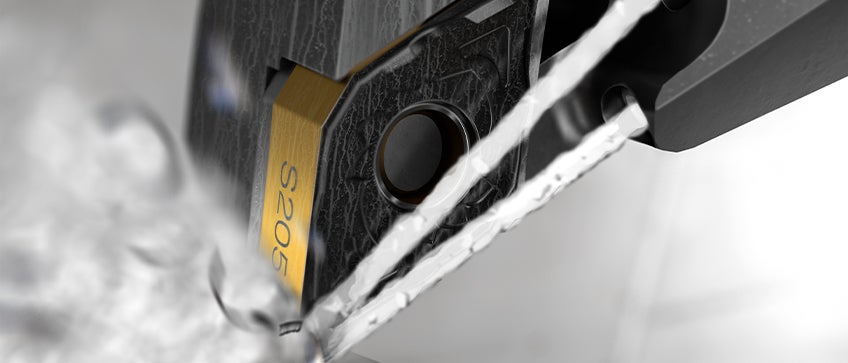
Se correttamente applicato, il refrigerante di precisione massimizza la produttività, aumenta la sicurezza del processo e migliora le prestazioni dell'utensile e la qualità del componente. Gli effetti positivi sono già evidenti con il refrigerante a bassa pressione ma, aumentando la pressione, è possibile lavorare con successo materiali sempre più difficili.
L'applicazione di refrigerante di precisione può fare la differenza sempre, soprattutto quando si parla di acciaio inossidabile e acciaio a basso tenore di carbonio. Ma è con i materiali più difficili da lavorare come, ad esempio, le superleghe resistenti al calore e le leghe di titanio, che i vantaggi risultano indiscutibilmente evidenti. È per questi motivi che una serie di sviluppi recenti ha reso il refrigerante ad alta precisione ancora più interessante e più facilmente disponibile.
Jetbreak è stato il primo
Durante gli anni '80 e '90 del secolo scorso, Sandvik Coromant ha sviluppato la prima versione di Jetbreak, un sistema di refrigerante ad alta pressione. Un attento percorso di ricerca ha permesso di integrare negli utensili da taglio getti di refrigerante direzionati con precisione a pressioni altissime (100-1000 bar), al fine di lavorare materiali esigenti in termini di lavorabilità e controllo truciolo. I getti di refrigerante si facevano strada formando un cuneo di fluido tra il truciolo e il tagliente. La lunghezza di contatto è stata ridotta con un abbassamento della temperatura nella zona di lavorazione. Inoltre, è stato possibile influire sull'arricciatura del truciolo migliorandone il controllo e, in alcuni casi, la rottura.
Jetbreak è presto diventato il sistema ideale per i materiali caratterizzati da scarsa lavorabilità e/o trucioli problematici. Si è imparato molto sugli effetti derivanti dalla distribuzione della pressione del refrigerante e dalle dimensioni dell'ugello. Variando i dati relativi ai getti, è stato possibile realizzare un formatrucioli variabile, guidare i trucioli a nastro nella direzione desiderata e persino migliorare la lunghezza dei trucioli. Su scala limitata, sono state implementate soluzioni per risolvere, in particolare, i problemi dell'industria petrolifera, del settore aerospaziale e delle aziende che producono cuscinetti a sfera. Jetbreak, tuttavia, doveva essere installato con portautensili speciali ed è stato utilizzato principalmente nei torni verticali.
Adozione standard del refrigerante ad alta precisione
Molte moderne macchine CNC prevedono l'adduzione standard di refrigerante a pressioni comprese tra 70 e 100 bar oppure la propongono come funzione opzionale con serbatoi e pompe di capacità adeguata. Questo è sufficiente per integrare il refrigerante ad alta precisione e sfruttarne i conseguenti vantaggi in termini di prestazioni e risultati su centri di lavoro, centri di tornitura, torni verticali e sulle macchine multi-task più comuni. L'equipaggiamento standard è sufficiente ed è facile canalizzare il refrigerante fino al punto in cui viene applicato il getto.
Indispensabili per la lavorazione con refrigerante ad alta precisione sono gli utensili modulari; in parte per garantire il cambio rapido degli utensili e ridurre al minimo i fermi macchina ma anche per fissare in modo efficiente gli attacchi e i canali del refrigerante lungo il percorso dalla macchina al tagliente. Il sistema modulare di utensili a cambio rapido Coromant Capto® è stata la base per lo sviluppo di Jetbreak e lo è ancora oggi per i nuovi utensili standard con refrigerante ad alta precisione. Questo sistema è ideale come piattaforma modulare, perché concepito per l'adduzione interna di refrigerante ma adatto anche all'erogazione di refrigerante ad alta precisione. Si tratta di uno standard ISO consolidato ed è disponibile, come opzione, su molte macchine CNC con utensili fissi e rotanti.
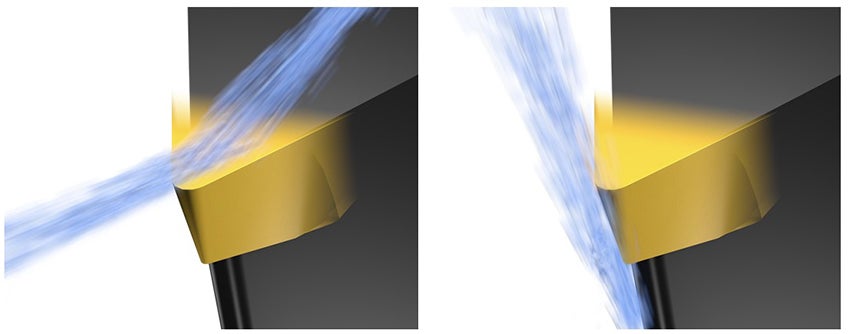
Il refrigerante di precisione sopra l'inserto, direzionato esattamente sulla zona di taglio, migliora il controllo truciolo e la sicurezza del processo. Il refrigerante sotto l'inserto aumenta la durata utensile e la produttività, specialmente in applicazioni caratterizzate da una forte generazione di calore nell'inserto.
Una fresa con refrigerante ad alta precisione prevede un sistema di adduzione interno ed è dotata di ugelli posizionati e direzionati in base al tipo di utensile e all'applicazione a cui è destinata. I canali sono collegati alla macchina utensile o alla pompa supplementare in modo da erogare il refrigerante a pressioni di circa 70 bar. Oggi, questo sistema è ampiamente disponibile e, anche se la pressione non è altissima, è certamente sufficiente per un deciso miglioramento delle prestazioni e dei risultati. La soluzione fa buon uso di una risorsa che molte officine meccaniche hanno già o in cui possono investire per il futuro.
Refrigerante di precisione per la tornitura
Gli utensili di tornitura con refrigerante di precisione sono strutturati in modo da erogare getti di refrigerante precisi con flusso laminare parallelo. I getti creano un cuneo idraulico tra inserto e truciolo, agendo sulla forma e sul flusso dei trucioli e riducendo la temperatura nella zona di lavorazione. Gli ugelli montati vicino al tagliente indirizzano con precisione i getti ad alta velocità, allontanando i trucioli dalla faccia dell'inserto, raffreddandoli e spezzettandoli in modo da favorirne l'evacuazione.
Nelle operazioni di finitura, i vantaggi sono evidenti anche a pressioni più basse, fino a 10 bar su materiali come acciaio, acciaio inossidabile, alluminio, titanio e superleghe resistenti al calore. Oltre che una maggiore sicurezza dovuta a un migliore controllo truciolo, il refrigerante di precisione può assicurare un notevole miglioramento della durata utensile e favorire l'adozione di una maggiore velocità di taglio. Con il refrigerante di precisione, si può spesso ottenere un aumento del 50% della durata utensile.
La velocità di taglio influisce sulla temperatura e, di conseguenza, sull'usura dell'utensile più di qualsiasi altro fattore. Aumentare la velocità di taglio sul titanio oltre i valori previsti riduce sensibilmente la durata utensile. Ma aumentando proporzionalmente l'avanzamento, la riduzione della durata utensile è generalmente minore. È per questo che agire sull'avanzamento è spesso un modo interessante per migliorare il volume di truciolo asportato senza incidere troppo sulla durata utensile. In queste macchine, tuttavia, l'avanzamento elevato non è sempre un'opzione praticabile a causa delle maggiori forze di taglio e dell'effetto sul controllo truciolo.
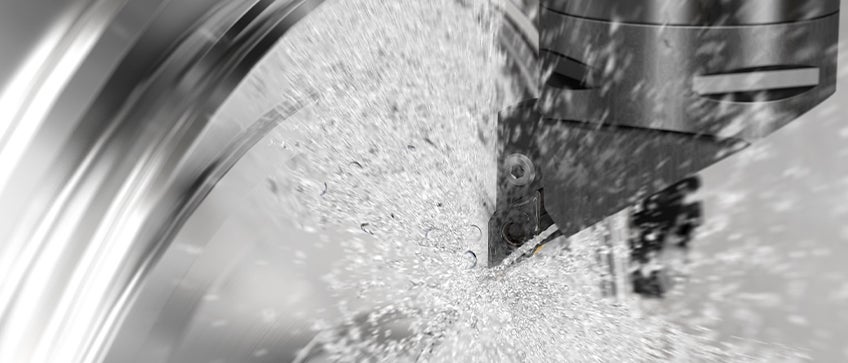
Tornitura di un disco turbina in HRSA. Il refrigerante di precisione può svolgere un ruolo fondamentale nella lavorazione dei materiali ISO S.
L'effetto del refrigerante di precisione può quindi incidere positivamente sulle prestazioni, grazie alla possibilità di utilizzare velocità di taglio più elevate senza aumenti di temperatura e riduzione della durata utensile. C'è un evidente effetto di raffreddamento, senza le maggiori forze di taglio dovute ad avanzamenti più elevati. Per i materiali classificati ISO S, è possibile ottenere un aumento del 20% della velocità di taglio mantenendo la stessa lunghezza di taglio.
Anche la tornitura interna è un'area in cui il refrigerante di precisione può svolgere un ruolo importante per aiutare a garantire una buona formazione del truciolo e a migliorare le proprietà di taglio su materiali difficili come il titanio. In questo modo, la soluzione aumenta la sicurezza e la durata utensile nelle operazioni di barenatura. Nella lavorazione di fori relativamente grandi e profondi con barre di alesatura - come nel caso dei componenti per i carrelli di atterraggio - può essere vantaggioso utilizzare utensili modulari sia nella parte posteriore che in quella anteriore dell'utensile. Essere in grado di cambiare la testina di taglio sulla barra bloccata assicura un cambio rapido, facile e preciso, oltre che quella flessibilità che permette di effettuare vari tagli con un solo setup. CoroTurn SL è un sistema che combina barre di alesatura antivibranti con il bloccaggio "millerighe" delle testine per la barenatura di fori più grandi con profondità di dieci volte il diametro ed è predisposto anche per il refrigerante di precisione.
La variazione dell'integrità superficiale del componente è influenzata dalla temperatura e dalle forze generate durante la lavorazione. Il refrigerante contribuisce certamente al controllo della temperatura e, come è stato dimostrato, il refrigerante di precisione fornisce un risultato più affidabile. Gli ugelli dell'utensile sono puntati direttamente sulla parte dell'inserto a contatto con la superficie finita. E dato che gli ugelli non sono regolabili, molte delle variabili scompaiono, rendendo più sicuro e omogeneo il processo di lavorazione.
Ottimizzazione delle operazioni correttamente impostate
Grazie alla possibilità di inserire un cuneo idraulico nella zona di lavorazione, soprattutto nelle operazioni che vanno dalla lavorazione media alla tornitura finale, lo spessore del truciolo è più controllabile e il cuneo idraulico più facile da applicare che nelle operazioni di sgrossatura.
La lavorazione con refrigerante ad alta precisione non dovrebbe essere vista come un modo per compensare le carenze dovute ad altri fattori - ad es. inserti inadatti, instabilità, dati di taglio scorretti, ecc. Il refrigerante di precisione è un elemento che ottimizza le operazioni già correttamente impostate. La soluzione offre la possibilità di ridurre i tempi ciclo, migliorare l'omogeneità dei componenti in termini di qualità e aumentare la sicurezza dei processi di tornitura e fresatura.
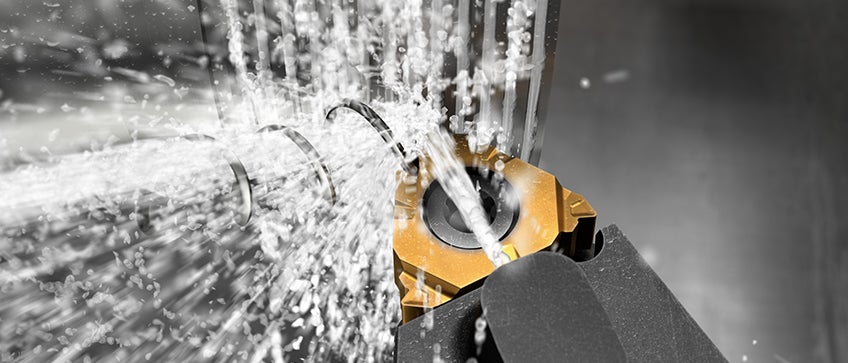
Tornitura dei filetti con refrigerante di precisione.
La necessità di ottimizzare una serie di operazioni, soprattutto in presenza di materiali difficili e problemi relativi alla formazione dei trucioli, rende il refrigerante di precisione un'opzione interessante. Il crescente numero di macchine multi-task e di torni verticali di nuova generazione ha evidenziato i vantaggi della lavorazione con refrigerante di precisione, soprattutto in termini di controllo truciolo. Gli inconvenienti derivanti dall'accumulo dei trucioli sono importanti, dato che queste macchine vengono sempre più utilizzate dalle officine meccaniche che producono componenti per il settore aerospaziale in materiali difficili da lavorare.