Rozgrzane do czerwoności
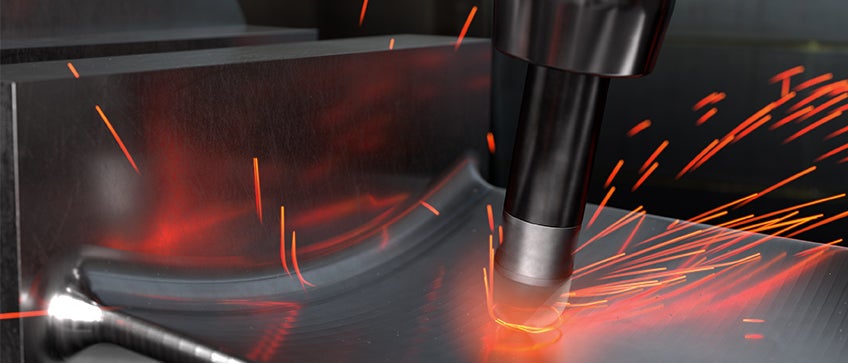
Wyzwanie: Wydajna obróbka podzespołów silników lotniczych wykonanych z superstopów żaroodpornych.
Rozwiązanie: Stworzenie zrównoważonego całościowego rozwiązania, obejmującego obrabiarkę, narzędzia, geometrie i materiały narzędziowe oraz strategię obróbki.
Superstopy żaroodporne (HRSA) to materiały dominujące w produkcji sprężarek i turbin silników odrzutowych. Gatunki najczęściej stosowane w tych zastosowaniach są oparte na niklu, np. Inconel, Waspaloy i Udimet.
Superstopy żaroodporne różnią się znacznie pod względem właściwości, w zależności od składu i procesu produkcji. Szczególnie duże znaczenie ma obróbka cieplna – utwardzanie wydzieleniowe, tzn. „starzenie” przedmiotu może podwoić jego twardość w porównaniu z przedmiotem wyżarzanym lub niepoddanym takiej obróbce
Coraz surowsze przepisy dotyczące emisji gazów cieplarnianych wymagają od nowych silników wyższych temperatur roboczych, co oznacza konieczność stosowania nowych materiałów do produkcji najsilniej rozgrzewających się podzespołów. Ponadto, rośnie ogólny udział superstopów żaroodpornych w silniku turboodrzutowym w porównaniu z innymi materiałami.
Natomiast korzyści płynące z zastosowania superstopów żaroodpornych stanowią wyzwanie dla producentów: Odporność na wysokie temperatury powoduje duże siły skrawania. Niska przewodność cieplna i doskonała hartowność powodują wysokie temperatury skrawania. Tendencja do utwardzania się podczas obróbki jest przyczyną powstawania karbu na krawędziach skrawających.

Wał z superstopu żaroodpornego.
Podzespoły – tarcze turbin, obudowy, łopatki turbin i wały – to przedmioty wymagające w obróbce, z których wiele ma cienkie ścianki i złożone kształty. Podzespoły silników o znaczeniu krytycznym dla bezpieczeństwa muszą spełniać surowe kryteria w zakresie jakości i dokładności wymiarów.
Do warunków wstępnych udanej obróbki należą obrabiarka o dużej mocy, sztywne narzędzia, płytki skrawające oferujące wysoką wydajność i optymalne programowanie. Stosowane są różne metody obróbki. Podzespoły takie, jak tarcze, pierścienie i wały są toczone, natomiast obudowy i łopatki turbin są frezowane.
Obróbkę superstopów żaroodpornych można ogólnie podzielić na trzy etapy. Pierwszy etap obróbki (FSM) polega na nadaniu odlewowi i odkuwce ogólnego kształtu. Przedmiot obrabiany jest zazwyczaj miękki (twardość wynosi zazwyczaj 25 HRC), ale często posiada chropowatą, nierówną powłokę lub łuskę. Głównym priorytetem jest dobra produktywność i wydajność skrawania metalu.
Między pierwszym i pośrednim etapem obróbki (ISM) przedmiot obrabiany poddawany jest obróbce cieplnej, przechodząc w stan starzenia i znacznie większej twardości (zazwyczaj około 36–46 HRC). Przedmiot obrabiany zyskuje swój ostateczny kształt, nie licząc naddatku pozostawionego z myślą o obróbce wykończeniowej. Podobnie nacisk kładziony jest na produktywność, ale ważne jest także bezpieczeństwo obróbki.
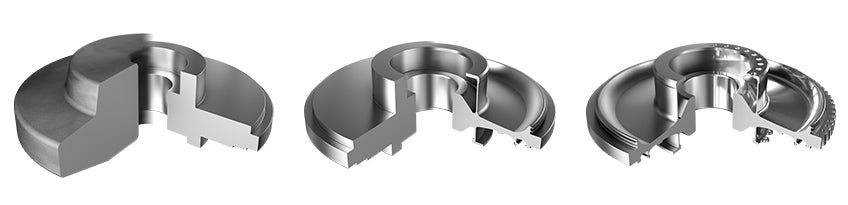
Pierwszy, pośredni i ostatni etap obróbki tarczy turbiny z superstopu żaroodpornego.
O ostatecznym kształcie i chropowatości powierzchni decyduje ostatni etap obróbki (LSM). Nacisk położony jest na chropowatość powierzchni, dokładne tolerancje wymiarowe oraz uniknięcie odkształceń i nadmiernych naprężeń resztkowych. W przypadku przedmiotów obrotowych o krytycznym znaczeniu, najważniejsze kryteria dotyczą odporności na zużycie zmęczeniowe, nie pozwalając na uszkodzenia powierzchni, które mogłyby powodować powstawanie pęknięć. Gwarancją niezawodności krytycznych elementów jest zastosowanie sprawdzonego, certyfikowanego procesu obróbki.
Ogólne wymogi względem płytek wymiennych obejmują dobrą udarność krawędzi oraz znaczny stopień przywierania pokrycia do podłoża. Choć podstawowe kształty ujemne mają zapewniać wytrzymałość i ekonomiczność, geometria powinna być dodatnia.
Podczas obróbki superstopów żaroodpornych należy zawsze stosować chłodziwo, za wyjątkiem frezowania za pomocą płytek ceramicznych. Płytki ceramiczne wymagają stosowania dużych ilości chłodziwa, natomiast precyzyjne doprowadzanie strumienia ma zasadnicze znaczenie w przypadku płytek węglikowych. W przypadku stosowania płytek węglikowych wysokie ciśnienie chłodziwa przynosi kolejne korzyści, w tym większą trwałość narzędzia i wydajną kontrolę spływu wiórów.
Parametry obróbki mogą być różne, w zależności od warunków i materiału. Podczas pierwszego etapu obróbki dąży się do uzyskania dobrej produktywności, głównie poprzez zastosowanie wysokich posuwów i dużych głębokości skrawania. Podczas etapu pośredniego często stosuje się płytki ceramiczne celem uzyskania większych prędkości. Podczas ostatnich etapów nacisk położony jest na jakość, a głębokość skrawania jest niewielka. Duża prędkość skrawania może wpływać negatywnie na chropowatość powierzchni (do obróbki wykończeniowej używane są płytki węglikowe).
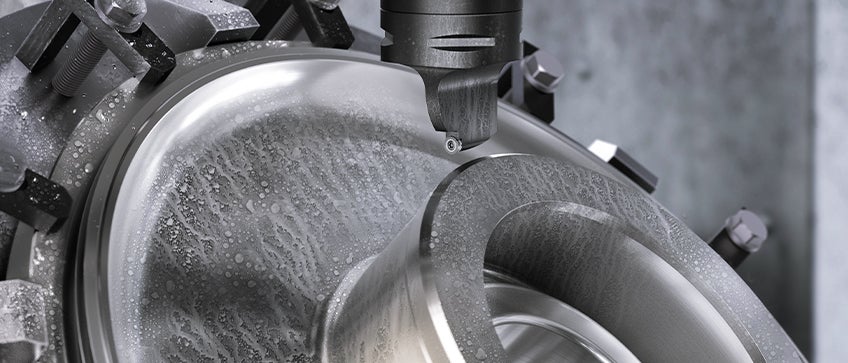
Tarcze turbin to podzespoły o krytycznym znaczeniu wykonane z zaawansowanych materiałów, wymagające wysokiego poziomu bezpieczeństwa obróbki dzięki zastosowaniu optymalnych narzędzi skrawających i rozwiązań.
Odkształcenia plastyczne i powstawanie karbu to typowe objawy zużycia płytek węglikowych, natomiast wykruszanie występuje często w przypadku płytek ceramicznych. Podatność na odkształcenia plastyczne maleje wraz ze wzrostem odporności na zużycie i twardości w wysokich temperaturach. Dodatnia geometria i ostra krawędź także są ważne dla ograniczenia powstawania wysokich temperatur i oporów skrawania. Środki zaradcze zapobiegające tworzeniu się karbu na głównej krawędzi skrawającej to mały kąt przystawienia, np. wskutek zastosowania płytki kwadratowej lub okrągłej, lub głębokość skrawania mniejsza od długości promienia zaokrąglenia naroża.
Płytki z pokryciem PVD są bardziej odporne na powstawanie karbu na głównej krawędzi skrawającej, natomiast płytki z pokryciem CVD cechują się większą odpornością na powstawanie karbu na krawędzi pomocniczej. Podczas obróbki wykończeniowej powstawanie karbu na krawędzi pomocniczej może mieć negatywny wpływ na chropowatość powierzchni.
Podsumowanie
Wydajna obróbka podzespołów silników wykonanych z superstopów żaroodpornych wymaga zrównoważonego całościowego rozwiązania, uwzględniającego w szczególności takie czynniki, jak stan przedmiotu obrabianego, materiał narzędzia oraz powiązane zalecane parametry skrawania, zastosowanie chłodziwa oraz zoptymalizowane strategie obróbki.
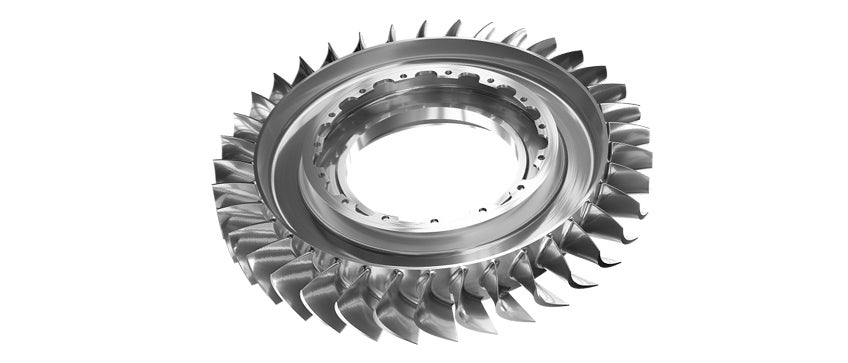
Narzędzia do pośredniego i ostatniego etapu obróbki superstopów żaroodpornych posiadają ostre, bardzo dodatnie geometrie do obróbki wykończeniowej i średniej oraz geometrie do czynności wymagających większej udarności.