Bardziej ekologiczna przyszłość branży lotniczej
Producenci oryginalnego wyposażenia muszą przyjąć bardziej całościowe podejście do samolotów przyszłości.
Jako jeden z największych sprawców emisji CO2 w skali globalnej, przemysł lotniczy, poddawany jest silnej presji, by samoloty stawały się bardziej ekologiczne, czyli lżejsze i mogły pokonywać większe odległości. Osiągnięcie tego celu wymaga jednak stosowania trudnych w obróbce materiałów: aluminium i superstopów żaroodpornych (HRSA). W niniejszym tekście Sébastien Jaeger, menedżer ds. rozwiązań przemysłowych dla branży lotniczej w firmie Sandvik Coromant wyjaśnia, dlaczego producenci z branży lotniczej mogą zastosować zaawansowane rozwiązania narzędziowe, aby w sposób zrównoważony obrabiać te niełatwe podzespoły.
Zgodnie z opinią Światowego Forum Ekonomicznego (WEF): „Osiągnięcie zerowej emisji netto CO2 do roku 2050 nie tylko pomoże stworzyć zrównoważoną środowiskowo przyszłość, lecz także zapewni finansową prężność i konkurencyjność branży lotniczej”. Jednak pomimo faktu, że e-mobilność zyskuje na znaczeniu w branży samochodowej – w sierpniu 2021 roku w Wielkiej Brytanii sprzedano więcej samochodów elektrycznych niż spalinowych – wdrożenie tych zmian w przemyśle lotniczym zajmie więcej czasu.
Ogólne prognozy mówią, że samoloty elektryczne nie staną się powszechne aż do 2035 roku. Raport Lonely Planet stwierdza, że pomimo faktu, że przewoźnik easyJet ma zamiar wprowadzić samoloty elektryczne na trasach poniżej 311 mil (500 km) do roku 2030, a norweskie linie lotnicze chcą do roku 2040 korzystać z maszyn elektrycznych na wszystkich lotach krótkodystansowych, „nieprędko polecimy ładowanym elektrycznym odrzutowcem w lot dalekobieżny: akumulatory są po prostu za ciężkie”.
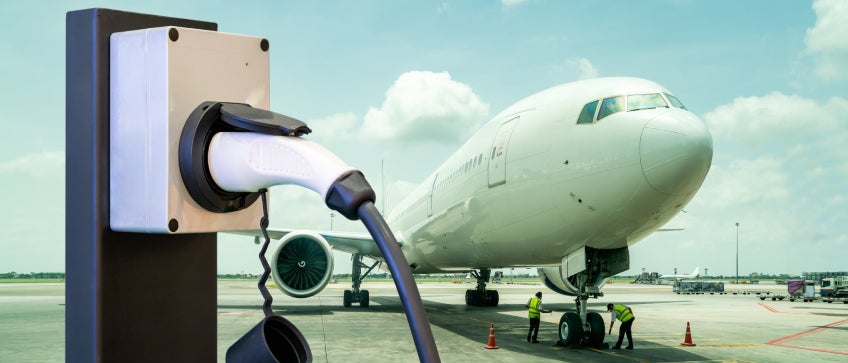
Samoloty elektryczne staną się powszechne w 2035 roku.
Dlatego, choć z jednej strony akumulatory muszą stać się lżejsze, aby ich stosowanie miało sens, rośnie nacisk na producentów oryginalnego sprzętu (OEM), aby dla równowagi stosowali lżejsze podzespoły. Nie ulega wątpliwości, że aluminium – a konkretnie nowe typy aluminium charakteryzujące się większą wytrzymałością, odpornością na zużycie zmęczeniowe i innymi właściwościami – będzie stosowane w celu odciążenia tych układów.
Obserwujemy także coraz częstsze zastosowanie nowych superstopów żaroodpornych (HRSA). W istocie superstopy te są już stosowane do produkcji tych części samolotów, które wymagają doskonałych parametrów, gdyż zachowują twardość nawet w wysokich temperaturach. Te właściwości materiałów będą mieć zasadnicze znaczenie, gdyż jedną ze strategii zmierzających do uczynienia podróży lotniczych bardziej zrównoważonymi będzie zwiększenie wytrzymałości i temperatur silników.
Podzespoły muszą również być wykonywane zgodnie z węższymi klasami tolerancji i mieć bardziej zróżnicowaną konstrukcję. Podobnie jak w przypadku samochodów elektrycznych, konstrukcja przyszłych samolotów elektrycznych – w tym ram kadłuba i silników – będzie różnić się w zależności od producenta bardziej niż ma to miejsce obecnie w przypadku samolotów z silnikami wewnętrznego spalania. Co się tyczy ram kadłuba, niektórzy producenci zastanawiają się nad kształtem deltoidalnym, zintegrowanym korpusem skrzydła lub zastosowaniem rozpórek w konstrukcji skrzydła. Inni producenci pozostają przy tradycyjnych konstrukcjach typu „wielka rura, skrzydła i silnik”.
Będą również istnieć różne kształty architektury silnika, np. elektryczny, z napędem akumulatorowym lub elektromagnetyczny, albo silniki hybrydowe, w których aktualnie używane silniki będą wspomagane przez silniki elektryczne. Producenci będą musieli produkować coraz bardziej różnorodne podzespoły zgodne z wąskimi tolerancjami, i jednocześnie poszukiwać nowych sposobów redukcji hałasu, ciężaru i emisji – wszystkie te czynniki wpływają na wydajność układów elektrycznych. Jednak aluminium i superstopy żaroodporne są trudne w obróbce, zatem osiągnięcie tego celu w sposób zrównoważony i efektywny kosztowo będzie dużym wyzwaniem.
Szybkie postępy
Jednym ze sposobów zmniejszenia masy i zwiększenia wydajności zużycia paliwa przez nowe samoloty jest zastosowanie technologii wytwarzania addytywnego (AM). Technologia AM umożliwia projektowanie spersonalizowanych części o złożonych kształtach oraz funkcjonalnych produktów o wąskich tolerancjach, co ułatwia obróbkę trudnych w obróbce przedmiotów, takich jak kratownice. Według wyników uzyskanych przez firmę Dassault Systemes, producenta oprogramowania: „W branży lotniczej redukcja masy wskutek zastosowania technologii AM może umożliwić oszczędność energii nawet o 25 procent”, natomiast „każdy kilogram (2.2 lbs) mniejszej masy podczas lotu może oznaczać roczną oszczędność paliwa sięgającą 3 tys. USD”.
Ale czy technologia wytwarzania addytywnego jest sama w sobie zrównoważona? Badanie przeprowadzone przez Wydział Inżynierii Produkcji Uniwersytetu Technicznego w Kluż-Napoka (Rumunia) stwierdza, że technologia AM to „doskonała alternatywa dla tradycyjnych metod produkcji (TM), takich jak formowanie wtryskowe, odlewanie lub obróbka”. Oto dalsze wnioski z badania: „Technologia AM ma potencjał obniżenia kosztów i zwiększenia wydajności energetycznej w porównaniu z tradycyjnymi procesami”.
Wytwarzanie addytywne będzie także mieć kluczowy wpływ na sposób wytwarzania produktów i ich różnorodność. Do jego zalet należą mniejsze: emisja dwutlenku węgla, zużycie materiałów oraz nakłady na transport, gdyż części można wytwarzać na miejscu zamiast importować.
Ponadto producenci mogą wytwarzać bardziej złożone, kompaktowe i innowacyjne części do samolotów dzięki szybkiemu tworzeniu i analizie prototypów. Szybkie tworzenie prototypów dotyczy kilku różnych technologii, ale jego celem jest szybkie stworzenie namacalnego trójwymiarowego prototypu na podstawie pliku CAD. Dzięki tym prototypom przed wdrożeniem produkcji na pełną skalę można przeprowadzić testy na niewielkich partiach nowych materiałów, aby zagwarantować najwyższy poziom innowacyjności, jakości i precyzji wykonania podzespołów.
Zastanowiliśmy się nad tym, w jaki sposób producenci w branży lotniczej mogą zastosować nowe metody, aby wytwarzać bardziej złożone podzespoły. Ale co z doborem właściwych narzędzi do danego zadania – zwłaszcza do obróbki aluminium i superstopów żaroodpornych?
Materiały te wymuszają stosowanie narzędzi o większej odporności na zużycie i trwałości. Dlatego firma Sandvik Coromant stworzyła gatunek S205 dla płytek stalowych używanych do toczenia. Struktura metalurgiczna gatunku S205 obejmuje warstwę Inveio® złożoną z ciasno upakowanych, ustawionych jednokierunkowo kryształów. Tworzą one wytrzymałą barierę ochronną wokół płytki, która zwiększa wytrzymałość narzędzia i poprawia jego właściwości mechaniczne. Płytka ta sprawdziła się już w produkcji szeregu podzespołów lotniczych, w tym tarcz turbin, pierścieni i wałów silników. Klienci Sandvik Coromant poinformowali o wzroście prędkości skrawania o 30 do 50% po zastosowaniu gatunku S205 w porównaniu do konkurencyjnych gatunków do toczenia superstopów żaroodpornych.
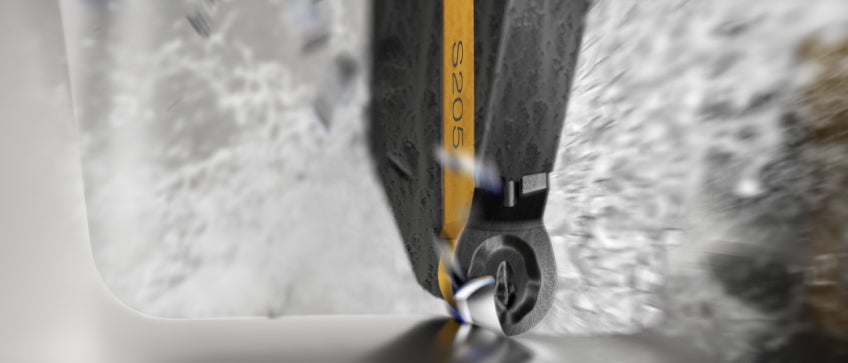
Podejście całościowe
Omówiliśmy narzędzia i procesy używane do produkcji, ale jak znaleźć ich najlepsze połączenie? W końcu można stracić sporo czasu na opracowanie w pełni zintegrowanego rozwiązania, jeśli zastosowane układy nie będą odpowiednio zestrojone.
Aby wesprzeć swoich klientów z branży lotniczej, firma Sandvik Coromant oferuje im tak zwane rozwiązanie do podzespołów. Obejmuje ono kilka etapów, w tym analizę wymogów obrabiarki i badania czasowe w celu ustalenia kosztu jednostkowego podzespołu. Częścią rozwiązania jest także analiza metod produkcji przy rozruchu, obejmująca pomiar czasu metody (MTM) i procesy końcowe u użytkownika końcowego. Rozwiązanie do podzespołów obejmuje także programowanie za pomocą narzędzi do komputerowego wspomagania produkcji (CAM) oraz zarządzanie projektami lokalnymi lub transgranicznymi.
W przypadku jednego z klientów Sandvik Coromant, który zmagał się z problemami z odłamywaniem wiórów podczas produkcji, rozwiązanie do podzespołów umożliwiło nam namierzenie przyczyny i opracowanie rozwiązania. Dla tego klienta specjaliści z Sandvik Coromant zaprojektowali nową strategię wykorzystującą dynamiczne krzywe napędu, co umożliwiło kontrolę odłamywania wiórów w dowolnym momencie. Nazwaliśmy to nowe podejście „scoop turning” i obecnie dysponujemy prawami patentowymi do tego rozwiązania. Metoda ta umożliwia klientowi skrócenie czasu cyklu o 80% przy lepszej kontroli spływu wiórów i podwojonej trwałości narzędzia.
Ponadto klientowi udało się ograniczyć liczbę wykorzystywanych obrabiarek z czterech do jednej, co zmniejszyło zapotrzebowanie na wielozadaniowość, podniosło poziom bezpieczeństwa obróbki i przełożyło się na bardziej ekologiczną produkcję. Mniejsza liczba potrzebnych obrabiarek oraz możliwość realizacji przebiegów produkcyjnych z ograniczeniem koniecznych zmian narzędzi dzięki zastosowaniu do obróbki bardziej udarnych gatunków, takich jak S205, będzie kluczem do bardziej zrównoważonej produkcji lotniczej.
Dużą rolę odegra także oprogramowanie, takie jak CoroPlus® Tool Guide, będące częścią cyfrowego asortymentu firmy Sandvik Coromant. Klienci mogą podejmować kluczowe decyzje dotyczące doboru narzędzi i parametrów skrawania przed przystąpieniem do produkcji.
Domknięcie pętli
Oprócz nowego podejścia do narzędzi i produkcji, producenci z branży lotniczej mogą także zająć się recyklingiem. Zgodnie z raportem Air Transport Action Group (ATAG), Kaiser, czyli dostawca aluminium dla firmy Boeing, stosuje obecnie zamknięty system recyklizacji, który obecnie należy do największych tego rodzaju programów w branży. Firma Kaiser szacuje, że dzięki programowi, około 10 milionów kilogramów ścinków i złomu metalowego zostanie wykorzystanych ponownie przez branżę.
W firmie Sandvik Coromant wdrożyliśmy nasz własny obiegowy system recyklizacji narzędzi węglikowych, w ramach którego odkupujemy od klientów zużyte narzędzia i wykorzystujemy je ponownie w produkcji nowych. W efekcie, surowce używane do produkcji narzędzi węglikowych Sandvik Coromant pochodzą w większości ze złomu. Realizujemy zrównoważoną działalność gospodarczą w środowisku ograniczonych zasobów i redukujemy do minimum marnotrawstwo zasobów. W ten sposób stwierdziliśmy, że produkcja z materiałów z odzysku zmniejsza zużycie energii o 70% i emisję dwutlenku węgla o 40%.
Narasta nacisk na przemysł lotniczy, by samoloty stawały się bardziej ekologiczne, czyli lżejsze i mogły pokonywać większe odległości. Dzięki zastosowaniu właściwych procesów i narzędzi – nie mówiąc o bardziej całościowym podejściu do produkcji – producenci samolotów mogą mieć swój wkład w bardziej ekologiczną przyszłość dla swojej branży.