การกัดปาดหน้า
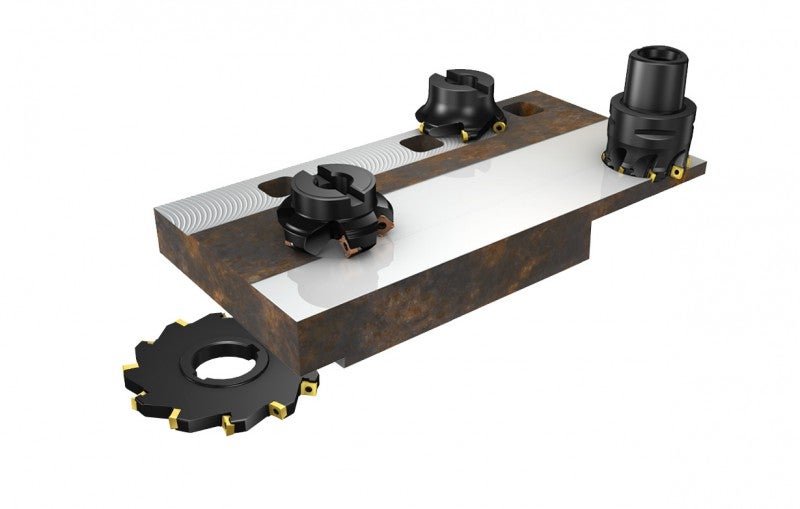
กระบวนการกัดปาดหน้ารวมถึง:
- การกัดปาดหน้าทั่วไป
- การกัดอัตราป้อนสูง
- การกัดปาดหน้างานหนัก
- การเก็บผิวละเอียดด้วยเม็ดมีดไวเปอร์
การกัดปาดหน้าทั่วไป
ความสำเร็จในการกัดปาดหน้าคืออะไร
การกัดปาดหน้าคือกระบวนการกัดที่ได้รับความนิยมที่สุดและสามารถทำได้โดยใช้เครื่องมือหลากหลายชนิด โดยหัวกัดที่ได้รับความนิยมในการใช้งานมากที่สุดคือหัวกดที่มีมุมเข้างาน 45º แต่ในบางกรณียังมีการใช้เม็ดมีดทรงกลม หัวกัดบ่าฉาก รวมถึงหัวกัดปาดข้างและหัวกัดปาดหน้าด้วย ควรเลือกหัวกัดที่เหมาะสมกับกระบวนการเพื่อให้มีประสิทธิภาพการผลิตสูงสุด (ดูวิธีการเลือกเครื่องมือจากข้อมูลด้านล่าง)
ตัวเลือกเครื่องมือ
ภาพรวมของหัวกัดปาดหน้า
แผนภาพด้านล่างแสดงถึงการใช้งานหลักของหัวกัดแต่ละประเภท ในด้านระยะกินลึก ap และอัตราป้อนงานต่อฟันตัด fz
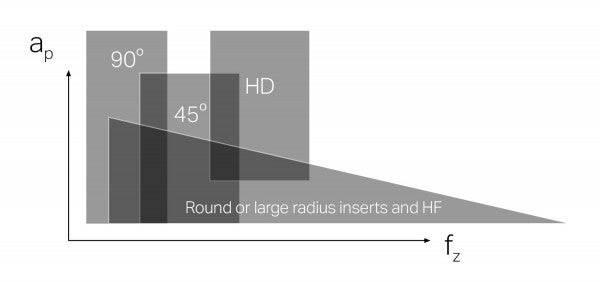
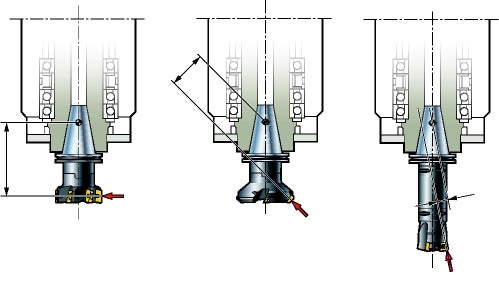
ทิศทางของแรงตัดที่สร้างจากมุมเข้างานต่างๆ
หัวกัดปาดหน้าและหัวกัดแนวดิ่ง 10° - 65°
หัวกัดเหล่านี้มักใช้งานกับกระบวนการกัดปาดหน้า แต่หัวกัดที่มีมุมเข้างานแคบมากซึ่งเหมาะสำหรับการกัดแนวดิ่งก็ยังรวมอยู่ในกลุ่มนี้ด้วย
หัวกัด 45°
- ตัวเลือกแรกสำหรับการกัดทั่วไป
- มีแรงสั่นสะเทือนต่ำในสภาพการทำงานที่ไม่มั่นคงและระยะยื่นสูง
- การทำเศษตัดให้บางช่วยเพิ่มประสิทธิภาพการผลิต
หัวกัด 90°
- เหมาะสำหรับชิ้นงานที่มีผนังบาง
- ชิ้นงานที่มีการจับยึดไม่มั่นคง
- ในจุดที่ต้องการมุมกัด 90°
เม็ดมีดทรงกลมและหัวกัดที่มีรัศมีกว้าง
เม็ดมีดทรงกลมมีความเอนกประสงค์อย่างมาก มีความสามารถสูงในการกัดไล่ระดับ และมักใช้สำหรับกระบวนการกัดปาดหน้าที่ทำได้ยากซึ่งรวมถึงกระบวนการกัดขึ้นรูป
- หัวกัดสำหรับใช้งานทั่วไป
- มีคมตัดที่แข็งแกร่งที่สุด
- มีคมตัดต่อเม็ดมีดสูง
- เหมาะอย่างยิ่งกับอัลลอยทนความร้อน เช่น ISO S
- การกัดนุ่มนวล
ตัวอย่างในการเลือกวิธีการ
การกัดปาดหน้า
![]() | ||||||
![]() | ||||||
มุมเข้างาน 25-65° | มุมเข้างาน 90° | มุมเข้างาน 10° | ||||
ข้อดี + ประสิทธิภาพการผลิตสูง + เหมาะสำหรบการกัดปาดหน้า + ตัวเลือกเม็ดมีดหลายคมตัด ข้อเสีย – ระยะกันลึกปานกลาง | ข้อดี + หัวกัดอเนกประสงค์ ใช้งานได้หลากหลายรูปแบบ + แรงตัดในแนวแกนต่ำ + มีระยะกินลึกสูงเมื่อเทียบกับขนาดเม็ดมีด ข้อเสีย – ประสิทธิภาพการผลิตต่ำ | ข้อดี + ประสิทธิภาพการผลิตสูง + อัตราป้อนงานสูงมาก + แรงตัดในแนวแกน (เหมาะสำหรับเพิ่มความมั่นคงให้สปินเดล) ข้อเสีย – ระยะกันลึกต่ำ | ||||
ประสิทธิภาพการผลิตสูง ตัวเลือกพื้นฐาน | อเนกประสงค์ สำหรับการผลิตแบบผสมผสาน | ประสิทธิภาพการผลิตสูง สำหรับแก้ไข้ปัญหา |
วิธีการทำงาน
การกัดปาดหน้าพื้นผิวแบบกระแทก
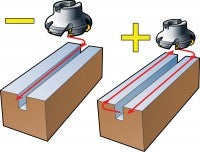
หลีกเลี่ยงการกดแบบกระแทก
- ควรหลีกเลี่ยงการกดกระแทกหากเป็นไปได้ (รองและร) เนื่องจากการกดกระแทกสร้างภาระให้คมตัดของเครื่องมืออย่างมาก เนื่องมาจากการเข้าและออกงานที่ไม่เหมาะสมหลายครั้ง
- อีกทางเลือกหนึ่งคือ ลดอัตราป้อนงานที่แนะนำลง 50% ในบริเวณที่มีการตัดกระแทกบนชิ้นงานเพื่อทำให้เศษตัดบางเมื่อตัดออกจากชิ้นงาน
การกดปาดหน้าส่วนที่เป็นผนังบางและมีการเบี่ยงเบน
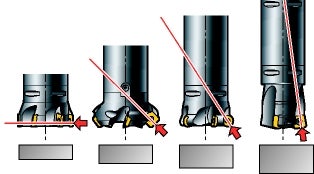
- ให้คำนึงถึงทิศทางของแรงตัดหลักที่สัมพันธ์กับความมั่นคงของชิ้นงานและอุปกรณ์จับยึด
- เมื่อกดชิ้นงานที่มีแรงในแนวแกนต่ำ ให้ใช้หัวกดบาฉาก 90° ซึ่งจะส่งแรงตัดส่วนใหญ่ไปที่แนวแกน
- ใช้หัวกดปาดหน้าเพื่อทำการกดเบาเป็นทางเลือก
- หลีกเลี่ยงการให้ระยะกินลึกในแนวแกนที่ต่ำกว่า 0.5-2 มม. เพื่อลดแรงตัดในแนวแกน
- ใช้หัวกดที่มีระยะพิตช์ห่างเพื่อให้มีคมตัดน้อยที่สุด
- ใช้คมตัดมุมบวก (-L) เพื่อลดแรงตัด
- ใช้หัวกดที่มีระยะพิตช์ไม่เท่ากันเพื่อแก้ไขปัญหา
การกดขอบส่วนที่บางโดยใช้หัวกดปาดหน้า
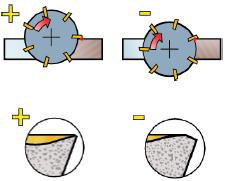
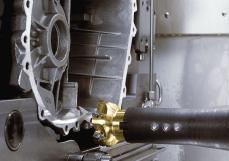
- หัวกดควรอยู่ในตำแหน่งเยื้องศูนย์สำหรับกระบวนการกดปาดหน้าในบริเวณขอบที่เป็นส่วนบาง การตัดจะมีความนุ่มนวลและกระจายแรงตัดไปที่ผนังได้สม่ำเสมอมากยิ่งขึ้น ซึ่งช่วยลดความเสี่ยงต่อการเกิดแรงสั่นสะท้าน
- เลือกระยะพิตช์ของหัวกดที่มีเม็ดมีดมากกว่า 1 ชิ้นที่สัมผัสกับชิ้นงานตลอดเวลา
- ให้เลือกรูปทรงรองหักเศษที่เล็กเบาที่สุดเท่าที่สามารถทำได้ (เบาแทนปานกลาง หรือปานกลางแทนหนัก)
- เลือกเม็ดมีดที่มีความโค้งน้อยกว่าและมีขอบคมตัดขนานสั้นกว่าเพื่อลดความเสี่ยงจากการสั่นสะท้านในผนังบางของชิ้นงาน
- ใช้ข้อมูลในการตัดเฉือนต่ำ ระยะกินลึกต่ำ ap และอัตราป้อนงานต่อฟันตัด fz ต่ำ
รายการตรวจสอบการใช้งานและคำแนะนำ
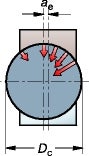
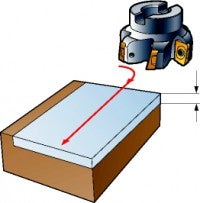
การกดเป็นแนวโค้งเข้าชิ้นงาน
- คำนึงถึงความมั่นคงของเครื่องมือตัดเฉือน ขนาดและประเภทของสปินเดล (แนวตั้งหรือแนวนอน) และกำลังรวมของเครื่องจักร
- ใช้หัวกดที่มีเส้นผ่านศูนย์กลางใหญ่กว่าชิ้นงาน 20 ถึง 50%
- คำนึงถึงความหนาสูงสุดของเศษตัดเมื่อปรับตำแหน่งของหัวกดเพื่อให้อัตราป้อนงานที่เหมาะสม
- ให้ตำแหน่งของหัวกดอยู่เยื้องศูนย์เพื่อให้เกิดเศษบางที่สุดขณะเดินหัวกดออกจากชิ้นงาน
- ทำการกดตามเพื่อให้เศษตัดมีลักษณะที่เหมาะสม หรือมีเศษตัดที่ไล่จากหนาไปหาบาง
- ตั้งโปรแกรมหัวกดให้กดเป็นแนวโค้งเข้าชิ้นงานหรือลดอัตราป้อนงานเพื่อให้การเข้างานนุ่มนวล
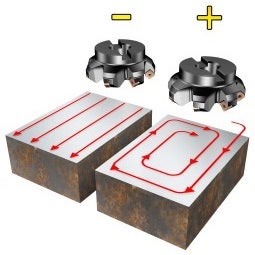
ให้หัวกดสัมผัสกับชิ้นงานเสมอ
- ทำการกดตามเพื่อให้เศษตัดมีลักษณะที่เหมาะสม หรือมีเศษตัดที่ไล่จากหนาไปหาบาง
- หลีกเลี่ยงการเข้าชิ้นงานและออกชิ้นงานโดยใช้การตั้งโปรแกรมทางเดินของเครื่องมือตัด
- ควรหลีกเลี่ยงการเข้าและออกชิ้นงานบ่อยครั้งถ้าเป็นไปได้ เนื่องจากจะทำให้เกิดแรงเครียดกับคมตัดอย่างมาก หรืออาจเสี่ยงต่อการหน่วงและการสั่นสะท้านได้ จึงควรตั้งโปรแกรมทางเดินของเครื่องมือให้หัวกดสัมผัสเต็มผิวงานแทนการเคลื่อนที่หลายๆ รอบในแนวขนาน และในขณะที่เปลี่ยนทิศทางตัด ควรตั้งโปรแกรมทางเดินของเครื่องมือเป็นแนวโค้งเล็กๆ เพื่อให้หัวกดเคลื่อนที่และสัมผัสชิ้นงานอย่างสม่ำเสมอ
การกดอัตราป้อนสูง
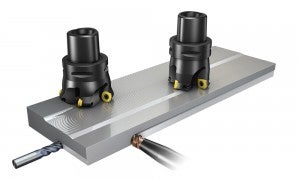
ความสำเร็จในการกัดปาดหน้าที่มีอัตราป้อนสูงคืออะไร? ในการกัดอะลูมิเนียมหรือโลหะหล่อขึ้นรูปด้วยเม็ดมีดคาร์ไบด์โบรอนไนไตรด์หรือเม็ดมีดเซรามิกสามารถใช้ความเร็วตัดถึง 1000 ม./นาทีได้ ทำให้อัตราป้อนงานและ vf สูงมาก การกัดประเภทนี้เรียกว่า การกัดความเร็วสูง (HSM)
ในการกัดวัสดุที่มีเศษตัดสั้น เช่น เหล็กหล่อเทา จะสามารถใช้หัวกัดปาดหน้าที่มีระยะพิตช์ใกล้ได้ ทำให้อัตราป้อนงานที่สูง ส่วนวัสดุซุปเปอร์อัลลอยทนความร้อนที่มีความเร็วการกัดที่ต่ำ หัวกัดที่มีระยะพิตช์ใกล้ทำให้อัตราป้อนงานที่สูง
การใช้หัวกัดที่มีมุมเข้างานแคบหรือหัวกัดเม็ดมีดทรงกลมสามารถทำการกัดปาดหน้าที่มีอัตราป้อนงานต่อฟันตัดสูงพิเศษ (สูงถึง 4 มม./ฟันตัด) ได้ เนื่องจากทำให้เกิดเศษบาง แม้ระยะกินลึกจะน้อยกว่า 2.8 มม. แต่อัตราป้อนงานที่สูงทำให้วิธีการกัดนี้มีประสิทธิภาพในการผลิตสูง เครื่องมือตัดบางชนิดถูกปรับแต่งมาสำหรับการกัดปาดหน้าอัตราป้อนสูงพิเศษที่ระยะกินลึกเชิงมุมต่ำ มุมเข้างานที่แคบนี้เป็นความต้องการลำดับแรกๆ เพื่อให้อัตราป้อนงานสูง รวมถึงการทำงานที่เบาและรวดเร็ว
ตัวเลือกเครื่องมือ
หัวกัดอัตราป้อนสูง | หัวกัดเม็ดมีดทรงกลม | HF ปานกลาง | ||||
ระยะกันลกสูงสุด (ap), มม. | 1.2 - 2 | 1.3 | 1.3 | 10 | 7/8 | 2.8 |
เส้นผ่านศูนย์กลางหัวกัด (Dc), มม. | 25 - 160 | 10 - 25 | 4 - 20 | 25 - 160 | 10 - 42 / 25 - 125 | 63 - 160 |
วัสดุ | ![]() | ![]() | ![]() | ![]() | ![]() | ![]() |
หัวกัดอัตราป้อนสูง:
- การกัดปาดหน้าอัตราป้อนสูงที่มีประสิทธิภาพด้วยมุมเข้าหางาน 10° ช่วยให้อัตราป้อนงานต่อฟันตัดสูง fz
- อัตราป้อนงานสูงที่ระยะกินลึกต่ำ, ap
- เครื่องมือที่มีความแม่นยำสูงซึ่งปรับแต่งโดยเฉพาะสำหรับการกัดเหล็กชุบแข็งที่ความเร็วสูง
- การกัดเส้นขอบรูปแบบหยาบหรือกึ่งหยาบ และการปรับตั้งแบบไม่สมมาตรที่อัตราป้อนสูงพิเศษ
หมายเหตุ: สำหรับเม็ดมีดทรงกลมและหัวกัดที่มีส่วนโค้ง ค่า ap ควรต่ำกว่าค่าสูงสุดที่แนะนำเพื่อให้ทำการกัดอัตราป้อนสูงได้
หัวกัดเม็ดมีดทรงกลม:
- การทำให้เศษตัดบางสูงขึ้นโดยมีแรงตัดที่แนวแกนลดลง
- การกัดนุ่มนวล
- หัวกัดอเนกประสงค์สำหรับงานหนักและงานเบา
วิธีการทำงาน
หัวกัดมุมเข้าหางานแคบ
หัวกัดที่มีมุมเข้าหางานเล็กมากจะเพิ่มอัตราป้อนงานได้อย่างมาก, fz, เนื่องจากการทำให้เศษบางเมื่อ ap น้อย
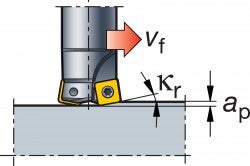
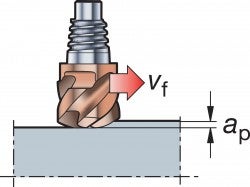
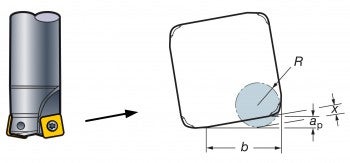
iC | ขนาด, มม. | วัสดุที่ยังไม่ได้ตัด | ||
iC | R | b | ap | x |
9 | 2.5 | 7.05 | 1.2 | 0.79 |
14 | 3.5 | 12.0 | 2.0 | 1.48 |
ความหนาสูงสุดของเศษตัดลดลงอย่างมากเนื่องจากมุมเข้างานแคบ ทำให้ใช้อัตราป้อนงานสูงพิเศษได้โดยที่เม็ดมีดไม่ทำงานหนักมากเกินไป
หมายเหตุ: หลีกเลี่ยงการกัดบางานที่ทำมุม 90° เนื่องจากจะสูญเสียประโยชน์ของมุมเข้างานไป กล่าวคือระยะกินลึกของชิ้นงานจะเพิ่มขึ้น
เพื่อหลีกเลี่ยงการสั่นสะท้านซึ่งเป็นสาเหตุที่ทำให้เม็ดมีดเกิดความเสียหาย จึงควรลดอัตราป้อนงานและปรับเปลี่ยนการทำงานให้เหมาะสมกับสภาวะเฉพาะทาง
หัวกัดเม็ดมีดทรงกลม
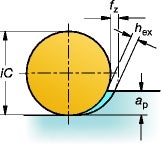
ความหนาของเศษตัดและ hex จะเปลี่ยนแปลงไปตามเม็ดมีดทรงกลมที่ใช้และขึ้นอยู่กับระยะกินลึก ap เมื่อใช้เทคนิคการกัดที่มีอัตราป้อนสูงด้วยเม็ดมีดกลม ควรรักษาระยะกินลึกให้ต่ำ (สูงสุด 10% ของเส้นผ่านศูนย์กลางเม็ดมีด, iC, มิฉะนั้น) ผลในการทำให้เศษตัดบางจะลดลง ซึ่งต้องลดอัตราป้อนงานลง
หมายเหตุ: เมื่อใช้หัวกัดเม็ดมีดทรงกลม จำเป็นจะต้องลดอัตราป้อนงานเมื่อเข้าใกล้ผนัง/บางาน เนื่องจากระยะกินลึกจะเพิ่มขึ้นฉับพลัน
เม็ดมีดที่แข็งแกร่งสำหรับการกัดหยาบทั่วไป
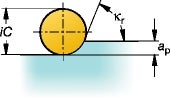
สำหรับเม็ดมีดกลมนั้น อัตราการกัดงานและมุมเข้างานจะแตกต่างไปตามระยะกินลึก ซึ่งประสิทธิภาพจะสูงสุดเมื่อระยะกินลึกต่ำกว่า 25% x เส้นผ่านศูนย์กลางของ, iC
การกัดปาดหน้างานหนัก
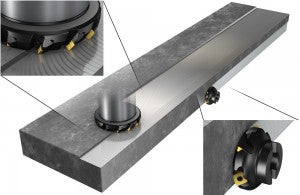
ความสำเร็จในการกัดปาดหน้าการงานหนักคืออะไร
การกัดปาดหน้าการงานหนักประกอบด้วยการกัดหยาบชิ้นงานที่ผ่านการรีดร้อนและทุบขึ้นรูป งานหล่อหรือโครงสร้างเชื่อมบนเครื่องกัดแกนที่มีขนาดใหญ่และเครื่องจักรกัดที่ทรงพลัง หรือเครื่องจักรอัตโนมัติครบวงจร วัสดุจำนวนมากจะถูกกำจัดออก ทำให้เกิดความร้อนและแรงตัดที่สูง ซึ่งทำให้เกิดความต้องการเฉพาะสำหรับเม็ดมีดกลึงตัดขึ้น:
- เกิดภาระงานที่คุมตัดหลักอย่างมากที่ระยะกินลึกสูงสุด
- เกิดการสึกหรอที่ขอบเม็ดมีดเนื่องจากชิ้นเสียดสีเมื่อระยะกินลึกใกล้ศูนย์
มุมเข้าทำงาน 60º เหมาะสำหรับการกัดงานหนัก การทำงานเช่นนี้ทำให้:
- รองรับระยะกินลึกได้ดี มีแรงตัดและการทำให้เศษตัดบางที่สม่ำเสมอซึ่งช่วยให้มีอัตราป้อนงานที่สูง
- ขนาดเผื่อแนวแกนในการทำงานลักษณะนี้สร้างผิวสำเร็จที่มีคุณภาพดี เนื่องจากเม็ดมีดมีขอบคมตัดแบบขนานกว้าง
ตัวเลือกเครื่องมือ
หัวกัดสำหรบการกัดงานหนัก | ||||
มุมเข้างาน (κr), มม. | 60° | 45° | 90° | เม็ดมีดทรงกลม |
ระยะกันลึกสูงสุด (ap), มม. | 13/18 | 10 | 15.7 | 12.5 |
เส้นผ่านศูนย์กลางหัวกัด (Dc), มม. | 160 - 500 | 80 - 250 | 40 - 200 | 66 - 200 |
วัสดุ | ![]() | ![]() | ![]() | ![]() |
หัวกัดสำหรับงานหนัก 60°
- ออกแบบเพื่อการจัดการเครื่องมือที่มีประสิทธิภาพ ลดเวลาหยุดทำงาน และสลับคมเม็ดมีดของเครื่องจักรได้อย่างรวดเร็วและปลอดภัย
- ความสามารถในการตัดสูงถึง 18 มม. เหมาะสำหรับการขจัดเนื้อโลหะและการกัดพื้นผิวที่มีลักษณะเป็นคลื่นไม่สม่ำเสมอ
- ประสิทธิภาพการผลิตสูง อัตราป้อนงานต่อฟันตัด 0.4 - 0.7 มม.
- มีขอบคมตัดแบบขนานกว้างเพื่อให้คุณภาพการกัดกึ่งหยาบที่ดี
- ขอบเม็ดมีดทนทานต่อการเสียดสีที่ระยะกินลึกต่ำ
- หัวกัดแข็งแรงเพื่อความปลอดภัยในการตัดที่มีความต้องการสูง
หัวกัดสำหรับงานหนักปานกลาง 45-90°
- การกัดปาดหน้าสำหรับงานหนักปานกลางที่มีความสามารถในการกัดบางที่สุด
- มีระยะกินลึก 6-8 มม. ที่อัตราป้อน 0.2 – 0.6 มม.
- สำหรับใช้งานในสภาวะที่ไม่เอื้ออำนวยในเครื่องจักรกลอัตโนมัติครบวงจรขนาดใหญ่
- ใช้งานร่วมกับเม็ดมีดไวเปอร์เพื่อให้การกัดผิวสำเร็จมีคุณภาพดี
- ตัวเลือกที่เหมาะสมที่สุดสำหรับการกัดบ่าและการกัดปาดหน้างานหนักปานกลาง
หัวกัดเม็ดมีดทรงกลมขนาดใหญ่
- หัวกัดสำหรับงานหนักปานกลาง มีคมตัดแข็งแรงสำหรับสภาพการทำงานที่ยาก เช่นการกัดผ่านสะเก็ดหรือการกัดกระแทก รูปทรงเม็ดมีดทรงกลมทำให้กระบวนการตัดนุ่มนวล
- ใช้ได้ 8 คมตัดในสภาวะการทำงานที่เหมาะสม
- ระยะกินลึกสูงสุด 10 มม. ความหนาของเศษสูงสุดอาจแตกต่างกันได้สูงสุดถึง 0.55 มม. ต่อฟันตัด ทั้งนี้ขึ้นอยู่กับรูปทรงของเม็ดมีดและระยะกินลึก
วิธีการทำงาน
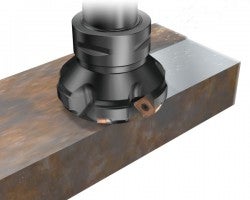
เม็ดมีดขนาดใหญ่ที่มีเส้นผ่านศูนย์กลางกว้างจะถูกใช้สำหรับงานหนัก โดยมีความเร็วในการตัดปกติ แต่มี ap และ fz สูงเมื่อเทียบกับ ae ทำให้มีประสิทธิภาพการผลิตอย่างมาก
การเข้าตัดชิ้นงาน
เนื่องจากการกัดหนักมีลักษณะการทำงานที่ไม่เอื้ออำนวย การเข้างานจึงมีความสำคัญเป็นอย่างมาก
- หากเป็นไปได้ควรตั้งโปรแกรมทางเดินของเครื่องมือตัดให้เดินหัวกัดเป็นแนวโค้งเข้าชิ้นงาน
- ลดอัตราป้อนงานลงจนกว่าหัวกัดจะสัมผัสเต็มหน้าชิ้นงาน
ตำแหน่งและขนาดของหัวกัด
ในการกัดงานหนักที่ต้องมีการกัดผ่านพื้นผิวชิ้นงานหลายๆ รอบ จำเป็นจะต้องทำตามข้อแนะนำในเรื่องดังนี้:
- ตำแหน่งและการเข้าชิ้นงานของหัวกัด
- ขนาดของหัวกัดเทียบกับความสามารถของเครื่องมือตัดเฉือน
- ทางเดินของเครื่องมือตัดเพื่อหลีกเลี่ยงการออกงานที่ไม่เหมาะสม
สังเกตอุณหภูมิที่สูงไว้
การกัดงานหนักที่มีความยากลำบากจะสร้างอุณหภูมิที่สูง เมื่อใช้แทนแม่เหล็กเพื่อกัดยึดชิ้นงาน เศษตัดจำนวนมากที่เกิดขึ้นจะติดอยู่รอบๆ หัวกัด ซึ่งจะทำให้การคายเศษตัดขัดหรือไม่สมบูรณ์ และเกิดการตัดเศษตัดซ้ำ ทำให้อายุการใช้งานของเครื่องมือลดลง เพื่อหลีกเลี่ยงเหตุการณ์เช่นนี้ ควรให้พื้นที่ทำงานไม่มีเศษตัด รวมถึงเพิ่มระยะกินลึกเพื่อให้หน้าสัมผัสกับผิวงานอยู่ใกล้กับคมตัดหลักของเม็ดมีดที่มีความแข็งแรงกว่า เพื่อป้องกันไม่ให้ขอบของเม็ดมีดสัมผัสกับพื้นผิวหรือชิ้นที่มีการเสียดสี
หมายเหตุ: ควรใส่ถุงมือขณะทำการติดตั้งเม็ดมีดแบบถอดเปลี่ยนได้กับหัวกัดเพื่อป้องกันการบาดเจ็บเนื่องจากความร้อน
การเก็บผิวละเอียดด้วยเม็ดมีดไวเปอร์
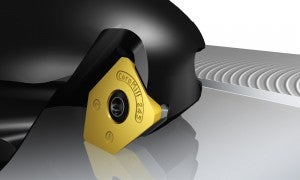
วิธีการที่จะทำให้การเก็บผิวละเอียดในการกัดปาดหน้าสำเร็จ
ผิวสำเร็จที่ดีเยี่ยมนั้นเกิดขึ้นจากการใช้เม็ดมีดมาตรฐานควบคู่กับเม็ดมีดไวเปอร์หนึ่งชุดหรือมากกว่า เม็ดมีดไวเปอร์ให้ประสิทธิภาพสูงสุดเมื่อใช้อัตราป้อนงานต่อรอบสูง fn รวมกับหัวกัดที่มีเส้นผ่านศูนย์กลางขนาดใหญ่และระยะพิเศษ รวมทั้งมีพื้นที่สำหรับทำการปรับตั้ง
สามารถเพิ่มอัตราป้อนงานต่อรอบได้ถึง 4 เท่าโดยยังคงคุณภาพพื้นผิวที่ดีไว้ได้ เม็ดมีดไวเปอร์ใช้งานได้ในงานกัดปาดหน้าส่วนใหญ่ทั่วไปเพื่อให้คุณภาพผิวงานที่ดี แม้ในสภาวะที่ไม่เอื้ออำนวย
ตัวเลือกเครื่องมือ
หัวกัด | ||||||
มุมเข้างาน (κr), มม. | 45° | 45° | 65° | 90° | 25° | 90° |
ระยะกันลึกสูงสุด (ap), มม. | 6 | 10 | 6 | 10 | 0.9 | 8.1 |
เส้นผ่านศูนย์กลางหัวกัด (Dc), มม. | 40 - 250 | 32 - 250 | 40 - 250 | 40 - 200 | 80 - 250 | 125 - 500 |
ผิวสำเร็จ (Ra) | < 1.0 | < 1.0 | < 1.0 | < 1.0 | < 1.0 | < 1.0 |
วัสดุ | ![]() | ![]() | ![]() | ![]() | ![]() | ![]() |
เม็ดมีดคมตัดไวเปอร์มีความยาวในขนาดต่างๆ (Bs) รวมถึงแบบตัดด้านซ้ายและด้านขวาสำหรับเม็ดมีดแต่ละประเภทด้วย นอกจากนี้ยังมีเกรดสำหรับวัสดุชิ้นงานส่วนใหญ่เช่นกัน โดยส่วนใหญ่หัวกัดที่ออกแบบมาสำหรับงานเก็บผิวละเอียดโดยเฉพาะจะใช้ช่องใส่เม็ดมีดแบบปรับได้ซึ่งเป็นช่องใส่เม็ดมีดแบบเฉพาะ หรืออาจเป็นเครื่องมือที่ใช้ตลับเม็ดมีดก็ได้
วิธีการทำงาน
ในการเก็บผิวละเอียดด้วยหัวกัดปาดหน้าขนาดใหญ่ ควรใช้อัตราป้อน fz ต่ำ แต่สามารถเพิ่มอัตราป้อนงานได้ 2-3 เท่า เมื่อใช้หัวกัดพร้อมเม็ดมีดไวเปอร์โดยไม่สูญเสียคุณภาพของพื้นผิว
การขัดเงาอัตราป้อนสูง
ความหยาบของผิวงาน | ||
![]() | อัตราป้อนงาน fn | |
fn1 <= 0.8 * bs1 | fn2 <= 0.6 * bs2 |
A: เมดมดขนาดมาตรฐานเท่านั้น
B: ใช้งานร่วมกับเม็ดมดไวเปอร์ 1 ชุด
C: fn = อัตราป้อนงาน / รอบ
bs1 | bs2 | |
![]() |
- เมื่อ fn เกิน 80% ของความยาวขอบคมตัดแบบขนาน Bs ของเม็ดมีดแบบปกติ คมตัดไวเปอร์จะทำให้คุณภาพพื้นผิวสูงขึ้น
- เมื่อใช้หัวกัดที่มีเส้นผ่านศูนย์กลางขนาดใหญ่และมีเม็ดมีดจำนวนมาก ควรใช้เม็ดมีดไวเปอร์เพื่อคงคุณภาพของผิวสำเร็จไว้เมื่ออัตราป้อนงานต่อรอบการหมุน fn สูงขึ้น
- การเบี่ยงเบนหนีศูนย์ในแนวแกน ซึ่งขึ้นอยู่กับมุมเอียงของสปินเดล ขนาดของหัวกัด การติดตั้ง และความแม่นยำในการปรับตั้งเครื่องมือ สามารถส่งผลกระทบต่อความเป็นคลื่นของพื้นผิวชิ้นงานได้ ปลายของขอบคมตัดไวเปอร์จะชดเชยในจุดนี้เพื่อทำให้ผิวงานเรียบไม่เป็นคลื่น ซึ่งอัตราป้อนงานต่อรอบการหมุนจะถูกขอบคมตัดไวเปอร์จำกัดไว้ที่ 60%
- ขอบคมตัดไวเปอร์จะยื่นออกมาจากด้านล่างของเม็ดมีดกลางตัดประมาณ 0.05 มม. เมื่อติดตั้งกับหัวกัดที่มีช่องใส่เม็ดมีดแบบคงที่ และสามารถปรับตำแหน่งคมตัดไวเปอร์ให้มีความแม่นยำสูงได้สำหรับหัวกัดแบบตลับเม็ดมีด ส่วนที่ยื่นออกมาทำให้เม็ดมีดไวเปอร์ได้รับภาระมากกว่าเม็ดมีดทั่วไป ซึ่งอาจทำให้เกิดการสั่นสะเทือนได้ ดังนั้นจึงควรใช้ไวเปอร์สำหรับการกัดเบาที่มีระยะกินลึกปานกลางในปริมาณจำกัด
- ระยะกินลึกควรมีค่าต่ำเพื่อรักษาแรงในแนวแกนและลดการสั่นสะเทือน ในการเก็บผิวละเอียด ระยะกินลึกในแนวแกนที่แนะนำคือ 0.5 – 1.0 มม.
- ควรใช้ความระมัดระวังอย่างมากในการติดตั้งเม็ดมีดไวเปอร์เพื่อให้คมตัดยาวของเม็ดมีดอยู่ในตำแหน่งที่ถูกต้อง
ตัวอย่าง:
- ความกว้างของขอบคมตัดแบบขนาน, Bs, บนเม็ดมีดคือ 1.5 มม.
- หัวกัดมีเม็ดมีด 10 ชุด และมีอัตราป้อนงานต่อฟันตัดที่ fz 0.3 มม. อัตราป้อนงานต่อรอบการหมุน, fn, จะมีค่าเท่ากับ 3 มม. (สองเท่าของความยาวของขอบคมตัดแบบขนาน)
- เพื่อให้มีผิวสำเร็จมีคุณภาพดี อัตราป้อนงานต่อรอบการหมุนควรมีค่าสูงสุดที่ 80% ของ 1.5 มม. = 1.2 มม.
- เม็ดมีดไวเปอร์จะมีขอบคมตัดแบบขนานที่มีความกว้างประมาณ 8 มม.
- ผลลัพธ์: อัตราป้อนงานต่อรอบอาจเพิ่มจาก 1.2 มม. เป็น 60% ของ 8 มม. = 4.8 มม. ได้
หมายเหตุ! ควรคำนึงถึงข้อจำกัดอื่นๆ เช่น กำลังของเครื่องจักรด้วย
รายการตรวจสอบการใช้งานและคำแนะนำ
คำแนะนำสำหรับ "การขัดเงาผิว":
- ใช้ความเร็วในการตัดสูงและ/หรือใช้เม็ดมีดเซอร์เมทเพื่อให้ผิวงานมีความมันเงา
- ใช้น้ำหล่อเย็นหรือละอองน้ำมันในการทำงานกับวัสดุที่มีเนื้อเหนียวเช่น ISO M และ S
- เม็ดมีดเคลือบผิว PVD ที่มีความคมและมี ap 0.5 – 0.8 มม. สร้างผิวสำเร็จที่มีคุณภาพดีที่สุด
- ควรใช้เกรดเดียวกันในเม็ดมีดไวเปอร์สำหรับเม็ดมีดที่ใช้ทำงาน
การกัดบ่าฉาก
การปฏบตงานกดบาฉากประกอบไปดวย: การกดบาฉาก/ กดปาดหนา การกดขอบขาง การกดบาฉากผนงเบยงแบบบาง การกดบาฉาก/... keyboard_arrow_right
งานกัดขึ้นรูป
การกดขนรปเปนกระบวนการกดทวไป โดยจะใชดอกกดทมเมดมดทรงกลมและเครองมอทมสวนโคงในการกดหยาบและการกดกงหยาบ... keyboard_arrow_right
คำแนะนำสำหรับการเจาะ
เคลดลบและคำแนะนำเกยวกบระบบจายนำหลอเยน การจายนำหลอเยนอยางถกตองถอเปนปจจยสำคญ เพอใหการเจาะมประสทธภาพ... keyboard_arrow_right
การเจาะแบบปรับระยะในแนวรัศมี
การเจาะแบบปรบระยะในแนวรศมสามารถทำไดดวยดอกสวานเมดมดเทานน การปรบระยะในแนวรศมของเสนผานศนยกลางของดอกสวานเมดมดจะชวยเพมพนทการตดเฉอน... keyboard_arrow_right