งานกัดขึ้นรูปคืออะไร
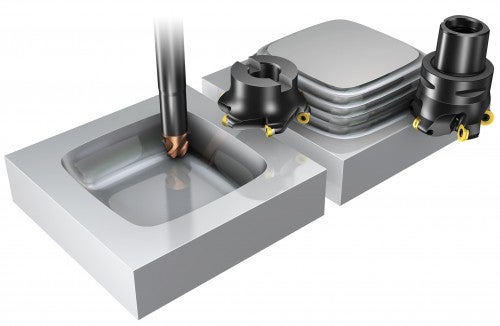
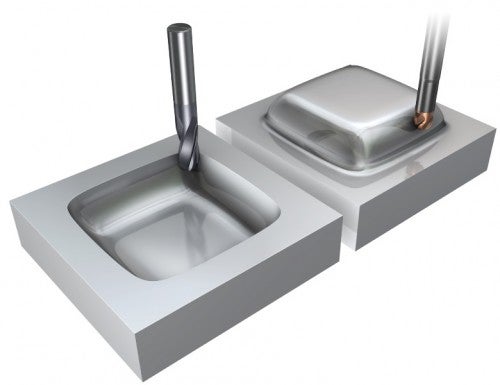
การกัดขึ้นรูปเป็นกระบวนการกัดทั่วไป โดยจะใช้ดอกกัดที่มีเม็ดมีดทรงกลมและเครื่องมือที่มีส่วนโค้งในการกัดหยาบและการกัดกึ่งหยาบ ส่วนดอกเอ็นมิลปลายมนคือดอกกัดที่ใช้สำหรับการเก็บผิวและการเก็บผิวละเอียดพิเศษ
กระบวนการกัดขึ้นรูป
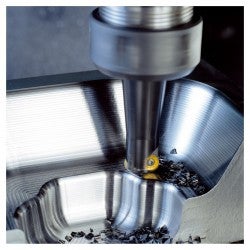
การกัดขึ้นรูปนั้นประกอบไปด้วยการกัดทรงนูนและทรงเว้าหลายแกนในแบบ 2 และ 3 มิติ ยิ่งชิ้นงานมีขนาดที่ใหญ่และการปรับตั้งเครื่องจักรที่ซับซ้อนมากเท่าใด การวางแผนกระบวนการกัดขึ้นรูปก็จะยิ่งมีความสำคัญมากขึ้นเท่านั้น
กระบวนการกัดถูกแบ่งออกเป็นสามประเภทด้วยกัน ซึ่งได้แก่
- การกัดหยาบ/การกัดกึ่งหยาบ
- การกัดเก็บผิวกึ่งละเอียด
- การเก็บผิวละเอียด
การเก็บผิวละเอียดพิเศษมักใช้เทคนิคในการกัดความเร็วสูงซึ่งมีความจำเป็นในบางกรณี การกัดเนื้อวัสดุที่เหลืออยู่ หรือที่เรียกว่าการกัดเนื้องานที่เหลือนั้นถือเป็นส่วนหนึ่งของกระบวนเก็บผิวกึ่งละเอียดและการเก็บผิวละเอียด เพื่อความแม่นยำและประสิทธิภาพในการผลิตสูงสุด ควรทำการกัดหยาบและการเก็บผิวละเอียดโดยใช้เครื่องจักรแยกจากกัน รวมถึงใช้เครื่องมือตัดที่มีความเหมาะสม
กระบวนการเก็บผิวละเอียดควรใช้เครื่องมือตัดเฉือน 4 ถึง 5 แกนที่มีซอฟต์แวร์และเทคนิคการตั้งโปรแกรมขั้นสูง ซึ่งจะช่วยลดเวลาที่ต้องใช้ในการเก็บงานให้เรียบร้อยด้วยตนเองลงอย่างมาก หรือแม้กระทั่งกำจัดขั้นตอนนี้ออกไปได้ ผลลัพธ์ที่ได้คือผลิตภัณฑ์ที่มีความแม่นยำของรูปทรงสูงกว่าและมีคุณภาพผิวงานที่ดีกว่า
ตัวเลือกเครื่องมือ
เครื่องมือตัดที่เหมาะสมในการกัดหยาบและการกัดกึ่งหยาบ:
เม็ดมีดทรงกลมและเครื่องมือที่มีส่วนโค้ง
เครื่องมือตัดที่เหมาะสมสำหรับการเก็บผิวละเอียดและการเก็บผิวละเอียดเป็นพิเศษ:
ดอกเอ็นมิลปลายมนและเครื่องมือที่มีส่วนโค้ง
![]() | ![]() | ![]() | ![]() | |
เม็ดมีดทรงกลม | หัวกัดปลายมนแบบถอดเปลี่ยนเม็ดมีดได้ | หัวกัดปลายมนแบบถอดเปลี่ยนเม็ดมีดได้ | ดอกโซลิดคาร์ไบด์ปลายม่น | |
ขนาดเคื่รองจักร / สปินเดล | ISO 40, 50 | ISO 40, 50 | ISO 30, 40 | ISO 30, 40 |
ความมั่นคงที่ต้องการ | สูง | ปานกลาง | ปานกลาง | ต่ำ |
การกัดหยาบ | ดีมาก | ดี | พอใช้ | พอใช้ |
การเก็บผิวละเอียด | พอใช้ | พอใช้ | ดีมาก | ดีมาก |
ระยะกันลึก ap | ปานกลาง | ปานกลาง | น้อย | น้อย |
ความอเนกประสงค์ | ดีมาก | ดีมาก | ดีมาก | ดีมาก |
ประสิทธิภาพการผลิต | ดีมาก | ดี | ดี | ดี |
รายการตรวจสอบสำหรบการกัดขึ้นรป
ควรศึกษาโปรไฟล์ของชิ้นงานอย่างละเอียดเพื่อให้สามารถเลือกเครื่องมือและวิธีการตัดเฉือนที่เหมาะสมได้
- กำหนดรัศมีต่ำสุดและความลึกสูงสุดของเบ้า
- คาดการณ์ปริมาณวัสดุที่จะขจัดออก
- คำนึงถึงการปรับตั้งเครื่องมือและการยึดจับชิ้นงานเพื่อหลีกเลี่ยงการสั่นสะท้าน ควรใช้เครื่องจักรที่มีความเหมาะสมในการตัดเฉือนเพื่อให้โปรไฟล์มีรูปทรงที่แม่นยำ
- การใช้เครื่องจักรสำหรับการเก็บผิวละเอียดและการเก็บผิวละเอียดเป็นพิเศษแยกจากกัน จะช่วยลดเวลาที่ต้องใช้ในการขัดผิวงานด้วยตนเองลงอย่างมากหรือแม้กระทั่งกำจัดขั้นตอนนี้ออกไปได้
- การตั้งโปรแกรมขั้นสูงอาจจำเป็นเพื่อให้ประหยัดค่าใช้จ่ายได้อย่างมาก ควรใช้ดอกเอ็นมิลคาร์ไบด์พร้อมเทคนิคความเร็วสูงเพื่อตัดชิ้นงานให้มีขนาดใกล้เคียงกับที่กำหนดและมีผิวสำเร็จที่มีคุณภาพดีที่สุดเท่าที่จะเป็นไปได้
- การกัดหยาบและการแต่งผิวกึ่งสำเร็จในชิ้นงานขนาดใหญ่จะมีประสิทธิภาพในการผลิตสูงสุดเมื่อใช้เครื่องมือและวิธีการทั่วไป ยกเว้นอลูมิเนียมที่สามารถใช้การกัดหยาบความเร็วสูงได้
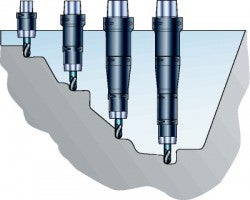
วิธีลดการสั่นสะท้าน
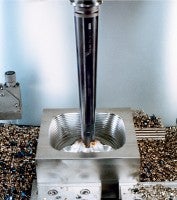
การสั่นสะท้านคืออุปสรรคในการกัดขึ้นรูปเมื่อใช้ระยะยื่นเครื่องมือที่ยาว วิธีการทั่วไปเพื่อกำจัดปัญหานี้คือการลดความลึก ความเร็ว หรืออัตราป้อนในการตัด
- ใช้เครื่องมือแบบถอดเปลี่ยนชิ้นส่วนได้ที่มีการเบี่ยงเบนหนศูนย์อย่างแม่นยำ
- เครื่องมือแบบถอดเปลี่ยนชิ้นส่วนได้ทำให้มีความยืดหยุ่นและการผสมผสานที่เพิ่มมากขึ้น
- ใช้เครื่องมือหรือตัวต่อลดแรงสั่นสะท้านเมื่อความยาวรวมของเครื่องมือจากความยาวพิกัดจนถึงคมตัดสูงกว่าความยาวพิกัด 4-5 เท่า
- ใช้ตัวต่อเพิ่มความยาวที่ทำจากโลหะหนักหากต้องการเพิ่มความต้านทานการโก่งตัวให้สูงขึ้น
- ใช้แรงตัดและการจับยึดเครื่องมือที่มีสมดุลสำหรับสปินเดลที่มีความเร็วมากกว่า 20,000 รอบต่อนาที
- เลือกตัวต่อเพิ่มความยาวและอะแดปเตอร์ที่มีเส้นผ่านศูนย์กลางกว้างที่สุดที่สามารถใช้งานได้ โดยเทียบกับเส้นผ่านศูนย์กลางของหัวกัด
- ความแตกต่างในแนวรัศมี 1 มม. (0.039 นิ้ว) ระหว่างตัวจับและเครื่องมือตัดเพียงพอต่อการลดแรงสั่นสะท้าน ใช้หัวกัดที่มีขนาดใหญ่พิเศษ
- การกัดแนวดิ่งเป็นอีกหนึ่งทางเลือกในการกัดโดยใช้เครื่องมือที่มีความยาวเป็นพิเศษ
การเพิ่มความยาวของเครื่องมือทีละน้อย
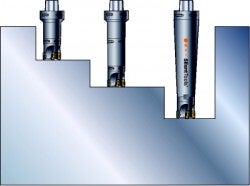

เพื่อรักษาประสิทธิภาพในการผลิตของกระบวนการกัดหยาบให้สูงสุด ควรใช้ตัวต่อเพิ่มความยาวสำหรับหัวกัดแบบต่างๆ โดยเฉพาะในจุดที่ทำการตัดรอบสุดท้ายซึ่งอยู่ลึกลงไปในชิ้นงาน
- เริ่มจากตัวต่อเพิ่มความยาวที่สั้นที่สุดก่อน เนื่องจากตัวต่อที่มีความยาวมากขึ้นจะลดประสิทธิภาพการผลิตและทำให้เกิดการสั่นสะเทือนขึ้น
- เปลี่ยนไปใช้เครื่องมือที่ต่อเพิ่มระยะในจุดที่กำหนดไว้ล่วงหน้าในโปรแกรม รูปทรงของเบ้าจะกำหนดจุดที่จะเปลี่ยนเครื่องมือ
- ปรับเปลี่ยนข้อมูลในการตัดสำหรับความยาวเครื่องมือต่างๆ เพื่อรักษาประสิทธิภาพในการผลิตให้สูงสุด
ความเร็วตัดจริง
หากใช้ค่าเส้นผ่านศูนย์กลางปกติของเครื่องมือเพื่อคำนวณความเร็วการตัดด้วยเม็ดมีดทรงกลมหรือดอกกัดปลายมน ความเร็วตัดจริง vc จะต่ำกว่าหากมีความลึกในการตัด ap ตื้น ซึ่งจะทำให้อัตราป้อนงานและประสิทธิภาพในการผลิตได้รับผลกระทบอย่างมาก
คำนวณความเร็วในการตัดโดยใช้เส้นผ่านศูนย์กลางใช้งานหรือในการตัดจริง Dcap
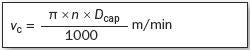
ดอกเอ็นมิลบางงาน
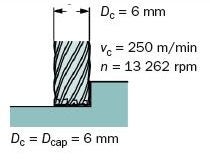
ดอกกัดปลายมน
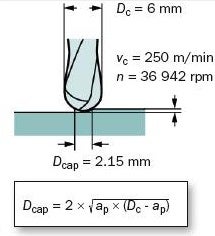
เม็ดมีดกลม
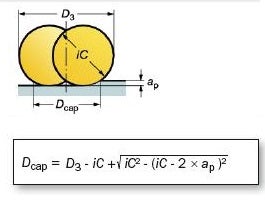
การกัดเฉพาะจุด – การเอียงดอกกัด
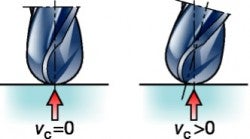
เมื่อใช้ดอกเอ็นมิลปลายมน จุดที่สำคัญที่สุดของคมตัดคือจุดศูนย์กลางของเครื่องมือที่มีความเร็วในการตัดใกล้คาศูนย์ ซึ่งเป็นสิ่งที่ไม่เอื้ออำนวยต่อกระบวนการตัด การคายเศษจากจุดศูนย์กลางของเครื่องมือเป็นสิ่งที่จำเป็นเนื่องจากมีพื้นที่คมจักที่แคบ
ด้วยเหตุนี้จึงควรเอียงสปินเดลหรือชิ้นงาน 10 ถึง 15 องศา ซึ่งจะทำให้พื้นที่การตัดห่างออกไปจากจุดศูนย์กลางของเครื่องมือ
- ความเร็วตัดต่ำสุดจะสูงขึ้น
- อายุการใช้งานเครื่องมือยาวนานขึ้นและมีลักษณะของเศษดีขึ้น
- ผิวสำเร็จที่ดียิ่งขึ้น
ตัวอย่างของดอกกัดสำหรับการตัดตรงกลาง
ส่วนตรงกลาง z = 2
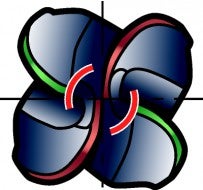
ส่วนด้านข้าง z = 4
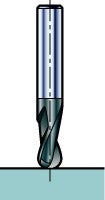
Z = 2
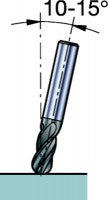
Z = 4
การกัดตื้น
เมื่อใช้เม็ดมีดทรงกลมหรือดอกกัดปลายมนในระยะกินลึกที่ตื้น อาจเพิ่มความเร็วตัด vc ขึ้นได้เนื่องจากคมตัดสัมผัสกับชิ้นงานเป็นเวลาสั้นๆ ระยะเวลาในการแพร่ความร้อนในบริเวณที่ทำการตัดก็สั้นลงเช่นเดียวกัน กล่าวคือคมตัดและอุณหภูมิของชิ้นงานจะอยู่ในระดับต่ำเสมอ นอกจากนี้ยังเพิ่มอัตราป้อน/ฟันตัด fz ได้อีกด้วย เนื่องจากมีเศษตัดที่บาง
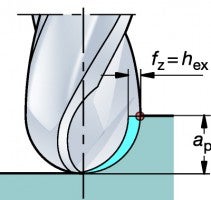
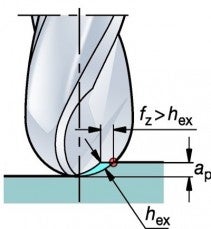
การกัดตื้น
ตัวอย่างของการกัดตื้นโดยใช้การเอียงดอกกัดและไม่เอียงดอกกัด
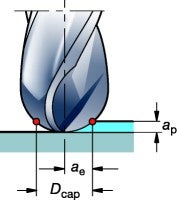
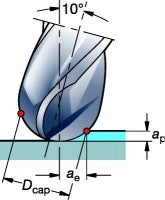
ตัวอย่างนี้แสดงให้เห็นถึงความเป็นไปได้ในการเพิ่มความเร็วตัดเมื่อ ae/ap ต่ำ และข้อได้เปรียบในการเอียงดอกกัด
ดอกเอ็นมิลคาร์ไบด์ปลายมน
Dc = 10 มม., เกรด GC 1610
วัสดุ: เหล็กกล้า, 400HB
ข้อมูลการตัดที่แนะนำสำหรับการตัดลึก ap - Dc/2:
vc = 170 ม./นาที
fz = 0.08 มม./รอบ = hex
apการแต่งผิวกึ่งสำเรจ - 2 มม. (0.079 นว) vc - 300 ม./นาที (984 ฟต/นาที) สามารถเพิ่มความเร็วขึ้นได้ราว 75% เนื่องจาก | vc hex vf Dc = 10 มม. (0.394 นิ้ว) | vc hex vf Dc = 10 มม. (0.394 นิ้ว) |
vc - 5 * 170 - 850 ม./นาที (557–2789 ฟุต/นาที) หมายเหตุ: fz aeการเก็บผิวละเอียดเป็นพิเศษ - 0.1 มม. | ไม่แนะนำใหทำการตัด โดยไม่เอียงดอกกัดในการเก็บผิวละเอียดเป็นพิเศษ | vc hex vf Dc = 10 มม. (0.394 นิ้ว) |
ประสิทธิภาพการผลิตในงานกัดขึ้นรูป: การเผื่อเนื้องานที่สม่ำเสมอ
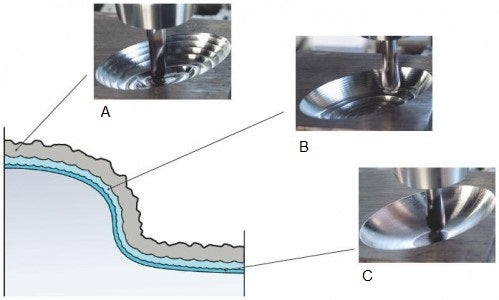
A: การกัดหยาบ
B: การเก็บผิวกึ่งละเอียด
C: การเก็บผิวละเอียดและการเก็บผิวละเอียดพิเศษ
การเผื่อเนื้องานสม่ำเสมอเป็นหนึ่งในเงื่อนไขสำหรับการกัดขึ้นรูปขั้นพื้นฐานเพื่อให้ประสิทธิภาพการผลิตสูงและมีความสม่ำเสมอ โดยเฉพาะอย่างยิ่งเมื่อใช้ความเร็วตัดสูง
- เพื่อให้มีประสิทธิภาพในการผลิตสูงสุดในกระบวนการผลิตแม่พิมพ์และแบบหล่อเหล่านี้ จึงจำเป็นต้องปรับขนาดของหัวกัดให้เหมาะสมกับงานแต่ละประเภท
- เป้าหมายหลักคือการสร้างชิ้นงานที่มีการเผื่อเนื้องานที่สม่ำเสมอเพื่อลดการเปลี่ยนเครื่องมือและทิศทางการเคลื่อนที่ของเครื่องมือในการทำงานลง
การใช้หัวกัดที่ไล่ขนาดจากใหญ่ไปหาเล็ก โดยเฉพาะในการกลึงหยาบกระแทกน้อยและการเก็บผิวกึ่งสำเร็จนั้น มีความเหมาะสมกว่าการใช้เครื่องมือที่มีเส้นผ่านศูนย์กลางขนาดเดียวตลอดทั้งกระบวนการ
- การเผื่อเนื้องานให้เหลือน้อยที่สุดเท่าที่จะสามารถทำได้ในกระบวนการก่อนหน้า จะส่งผลให้คุณภาพของการเก็บผิวละเอียดดีที่สุด
- เป้าหมายที่ควรเน้นย้ำคือการทำให้รูปร่างสุดท้ายของชิ้นงานมีความใกล้เคียงกับค่าที่กำหนดไว้ให้มากที่สุด
- กระบวนการตัดเฉือนที่มีความปลอดภัย
จุดเด่นของการเผื่อเนื้องานที่สม่ำเสมอ
- การเก็บผิวกึ่งสำเร็จบางประเภทและกระบวนการเก็บผิวเกือบทุกชนิดสามารถทำโดยใช้มนุษย์ควบคุมบางส่วน หรือไม่ใช้มนุษย์เลยก็ได้
- ลดผลกระทบเชิงลบต่อรางนำทางของเครื่องมือตัดเฉือน บอลสกรู และแบริ่งของสปินเดล
การเจาะชิ้นงานเนื้อตัน
- ในการคว้านรัศมีชิ้นงาน จำเป็นที่จะต้องเลือกวิธีการที่มี ap น้อยที่สุด และมีการเผื่อเนื้องานที่สม่ำเสมอสำหรับการกัดขึ้นรูปในกระบวนการถัดไป
- หัวกัดบางงาน/เอนมิล หรือหัวกัดขอบยาวจะเหลือเนื้องานแบบขั้นบันไดเอาไว้ซึ่งต้องกำจัดออก เนื่องจากจะทำให้เกิดแรงตัดและการเบี่ยงเบนของเครื่องมือที่ต่างกัน ทำให้เนื้องานไม่สม่ำเสมอ และเกิดผลกระทบต่อความแม่นยำของรูปทรงและรูปร่างสุดท้ายของชิ้นงาน
- การใช้หัวกัดแบบเม็ดมีดทรงกลมจะทำให้รอยต่อระหว่างรอบการตัดเรียบเนียนขึ้นและเหลือเนื้องานสำหรับกระบวนการกัดขึ้นรูปน้อยลง ทำให้ชิ้นส่วนมีคุณภาพที่ดีขึ้น
- ทางเลือกที่สามคือการใช้หัวกัดความเร็วสูงเพื่อคว้านรัศมี ซึ่งจะทำให้เนื้องานมีขนาดเล็กและสม่ำเสมอเนื่องจากมีระยะกันลึกที่น้อย หรือมีขั้นบันไดที่เล็กนั่นเอง
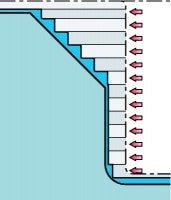
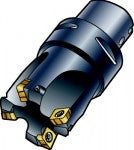
หัวกัดบ่าฉาก
ทำให้เหลือเนื้องานในปริมาณมากและไม่สม่ำเสมอ
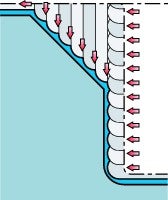
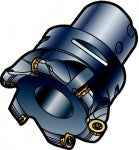
หัวกัดแบบเม็ดมีดทรงกลม
เหลือเนื้องานน้อย
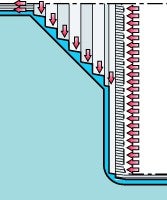
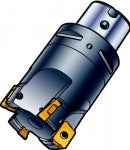
หัวกัดอัตราป้อนสูง
เหลือเนื้องานน้อย
การกัดลอกแบบ
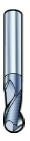
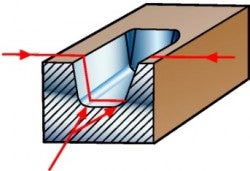
เทคนิคการกัดลอกแบบเป็นวิธีการทั่วไปซึ่งง่ายต่อการตั้งโปรแกรมทางเดินของเครื่องมือตัดมากที่สุดสำหรับการคว้านเบา โดยวิธีการนี้จะมีการเข้าและออกจากวัสดุชิ้นงานหลายครั้ง แต่จะเป็นการจำกัดการใช้งานโปรแกรมซอฟต์แวร์ที่ทรงพลัง เครื่องจักร และเครื่องมือตัดอย่างมาก จึงควรใช้เครื่องจักรและซอฟต์แวร์ที่มีฟังก์ชัน Look Ahead เพื่อหลีกเลี่ยงความเบี่ยงเบนจากทางเดินของเครื่องมือตัด
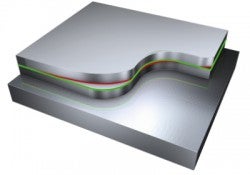
แนวทางที่เปิดกว้างต่อการเลือกวิธีการ ทางเดินของเครื่องมือตัด รวมทั้งหัวกัดและตัวจับยึดคือสิ่งที่จำเป็น
− จุดศูนย์กลางของเม็ดมีดได้รับภาระอย่างหนัก
− อัตราป้อนลดลง
− อายุการใช้งานของเครื่องมือลดลง
− เกิดแรงกระแทกเชิงกล
− รูปแบบผิดเพี้ยน
− ใช้เวลาในการดำเนินโปรแกรมและเวลาตัดนานขึ้น
ทางเดินของเครื่องมือคัดลอกแบบมักประกอบด้วยการกัดทวนและการกัดตาม รวมถึงหน้าสัมผัสกับชิ้นงานที่ไม่พึงประสงค์จำนวนมาก ในแต่ละครั้งที่เครื่องมือเคลื่อนที่เข้าและออกชิ้นงาน จะเกิดการเบี่ยงเบนขึ้น ทำให้เกิดรอยบนพื้นผิว แรงตัดและการโก่งตัวของเครื่องมือจะลดลง ทำให้เกิดรอยเว้าเล็กน้อยบนวัสดุในจุดที่เครื่องมือเคลื่อนที่ออก
ผลสรุป
- หลีกเลี่ยงการกัดลอกแบบตามแนวผนังที่มีความชัน และเนื่องจากเศษตัดขณะการกัดในแนวดิ่งจะมีขนาดใหญ่ จึงควรใช้ความเร็วตัดที่ต่ำ
- คมตัดของเครื่องมือมีความเสี่ยงต่อการเสื่อมสภาพที่จุดศูนย์กลาง โดยเฉพาะเมื่อหัวกัดเจาะถึงด้านล่างของชิ้นงาน
- ควรควบคุมความเร็วของอัตราป้อนงานด้วยฟังก์ชัน Look Ahead มิฉะนั้นจะไม่สามารถลดความเร็วเพื่อป้องกันความเสียหายต่อศูนย์กลางเครื่องมือได้ทัน
- หัวกัดจะมีการสัมผัสมากเมื่อเจาะถึงผนัง และมีความเสี่ยงต่อการเบี่ยงเบน การสั่นสะท้าน และการแตกหักของเครื่องมือ
- เมื่อใช้ดอกเอ็นมิลปลายมน จุดที่สำคัญที่สุดคือจุดศูนย์กลางของเครื่องมือ เนื่องจากมีความเร็วตัดใกล้กับศูนย์ ให้หลีกเลี่ยงการใช้บริเวณจุดศูนย์กลางของเครื่องมือ และเอียงสปินเดลหรือชิ้นงานสำหรับการกัดเฉพาะจุดเพื่อเพิ่มประสิทธิภาพให้สูงขึ้น
- กระบวนการกัดลอกแบบตามผนังชั้นในทิศทางขึ้นจะส่งผลดีกว่าเนื่องจากมีความหนาสูงสุดของเศษตัดในความเร็วตัดที่ดีกว่า
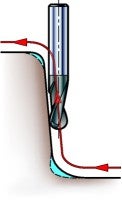
มีความเสี่ยงต่อการเกิดรอยเซาะ
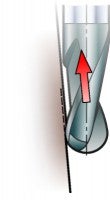
การลอกแบบในทิศทางขึ้น:
ความหนาของเศษตัดสูงสุดใน vc ที่แนะนำ
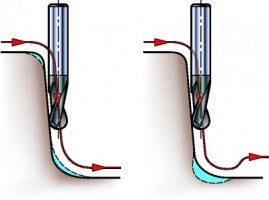
ที่ด้านล่างของร่อง:
เสี่ยงต่อการเสื่อมสภาพที่จุดศูนย์กลางของเครื่องมือ
ความผิดพลาดในการขึ้นรูปเป็นเรื่องปกติ โดยเฉพาะเมื่อใช้เทคนิคการตัดเฉือนความเร็วสูง
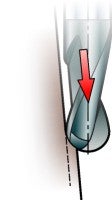
การลอกแบบในทิศทางลง:
ความหนาของเศษตัดสูงที่ vc ต่ำเป็นพิเศษ
ลดอัตราการป้อนงานเพื่อยืดอายุการใช้งานของเครื่องมือ
การย้อนทิศทางในการกัดขึ้นและลงจะทำให้เครื่องมือได้รับการเบี่ยงเบนและแรงตัดสลับกัน การลดอัตราป้อนงานในส่วนที่สำคัญของทางเดินเครื่องมือจะช่วยลดการเสื่อมสภาพของคมตัด พร้อมทำให้กระบวนการตัดปลอดภัยขึ้นและมีอายุการใช้งานของเครื่องมือที่ยาวนานกว่าเดิม
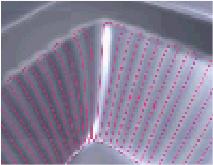
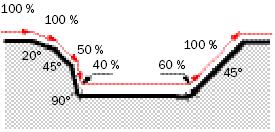
การกัดขอบรูป
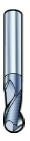
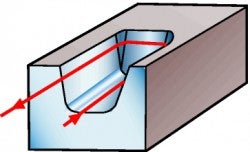
แทนที่จะใช้เทคนิคในการตั้งโปรแกรมที่จำกัดเพียง "การเฉือน" วัสดุในค่า Z คงที่เพียงอย่างเดียว การเปลี่ยนมาใช้ทางเดินเครื่องมือแบบขอบรูปคู่กับการกัดตามผลลัพธ์รวมถึง:
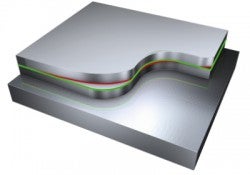
+ เวลาที่ใช้ในการตัดเฉือนลดลงอย่างมาก
+ ใช้ประโยชน์จากเครื่องมือและเครื่องจักรได้มากขึ้น
+ คุณภาพของรูปร่างชิ้นงานที่ตัดเฉือนดีขึ้น
+ ใช้เวลาในการเก็บผิวงานและขัดชิ้นงานด้วยตนเองน้อยลง
+ ควบคุมความเร็วตัด - ve ได้
+ ทำการตัดเฉือนความเร็วรอบสูงได้
+ อัตราป้อนงานสูง
+ อายุการใช้งานของเม็ดมีดยาวนาน
+ มีความปลอดภัย
การตั้งโปรแกรมขั้นแรกยังยากและอาจใช้เวลานานกว่า แต่สิ่งนี้จะถูกชดเชยด้วยต้นทุนเครื่องจักรต่อชั่วโมงที่คุ้มค่ากว่าการทำงานแบบเดิมถึงสามเท่า จึงควรใช้เครื่องจักรและซอฟต์แวร์ที่มีฟังก์ชัน Look Ahead เพื่อหลีกเลี่ยงความเบี่ยงเบนจากทางเดินของเครื่องมือตัดผลสรุป
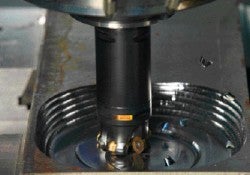
- ใช้ทางเดินเครื่องมือสำหรับกัดขอบรูป เช่น "การกัดตามแนวระดับน้ำ" ซึ่งเป็นวิธีการกัดตามที่ดีที่สุด
- การกัดขอบรูปโดยใช้ขอบนอกของหัวกัดจะมีประสิทธิภาพการผลิตที่สูงกว่า เนื่องจากเครื่องมือที่มีเส้นผ่านศูนย์กลางใหญ่กว่าจะใช้ฟันตัดได้มีประสิทธิภาพยิ่งขึ้น
- การกัดขอบรูปจะช่วยควบคุมและคงความเร็วในการตัดเอาไว้ หากเครื่องจักรจำกัดความเร็วของสปินเดล
- การกัดขอบรูปยังทำให้มีการเปลี่ยนเครื่องมือและทิศทางการเคลื่อนที่ในการทำงานลดลงอีกด้วย ซึ่งเป็นสิ่งที่สำคัญอย่างยิ่งในการกัดความเร็วสูงและมีอัตราป้อนสูงรวมถึงการกัดวัสดุที่มีความแข็ง เนื่องจากกระบวนการได้รับผลกระทบจากความเปลี่ยนแปลงจากการเบี่ยงเบนหรือการสั่นสะเทือนได้ง่ายกว่า
- ควรใช้เครื่องมือตัดอย่างต่อเนื่องและนานที่สุดเท่าที่เป็นไปได้ เพื่อให้เครื่องมือมีอายุการใช้งานที่ดี
หมายเหตุ! หลีกเลี่ยงการกัดด้วยจุดศูนย์กลางของเครื่องมือที่มีความเร็วตัดใกล้ค่าศูนย์
กลยุทธ์ในการกำหนดทางเดินของเครื่องมือตัด
Z – การกัดขอบรูปต่อเนื่อง, สองแกน สำหรับการกัดหยาบและการเก็บผิวละเอียด
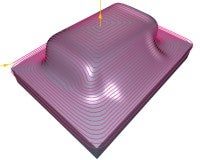
การกัดตามแนวระดับน้ำในแกน Z - การกัดขอบรูปต่อเนื่อง
- เป็นที่นิยม หากใช้งานฟังก์ชันการกัดแบบสแกลลอปที่ควบคุมโดย CAM ได้สูงสุด
- การยืดและหดดอกกัดนุ่มนวล
- เขียนโปรแกรมได้ง่าย
- มีเครื่องมือให้เลือกใช้หลากหลาย
การกัดขอบรูปเฮลิคอล 3 - 5 แกน การเก็บผิวละเอียด
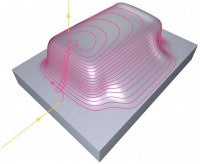
การกัดขอบรูปโดยใช้ทางเดินเครื่องมือแบบไล่ระดับ
- เปลี่ยนทิศทางได้อย่างนุ่มนวล
- ความแม่นยำของรูปทรงและผิวสำเร็จคุณภาพดี
- ควบคุมความสูงของผิวคลื่นได้ดี
- หน้าสัมผัสคงที่
- โปรแกรมการทำงานสั้น
- เครื่องมือมีขนาดสั้น
การกัดแต่งผิวงาน
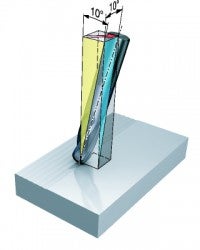
ทำการกัดตามด้วยเอนหัวกัดประมาณ 10° ทั้งสองทิศทางเพื่อให้ผิวสำเร็จมีคุณภาพดีและมีประสิทธิภาพที่น่าเชื่อถือ หัวกัดปลายมนหรือคมตัดทรงกลมจะสร้างรอยหยักบนผิวงานที่ความสูงเฉพาะ h ซึ่งขึ้นอยู่กับ:
- ความกว้าง, ae, ของการกัด
- อัตราป้อนงานต่อฟันตัด, fz
ปัจจัยสำคัญอื่นๆ ได้แก่ระยะกินลึก ap ซึ่งส่งผลต่อแรงตัดและการอ่านค่าการเบี่ยงเบนหนีศูนย์ของเครื่องมือ – TIR เพื่อให้ได้ผลลัพธ์ที่ดีที่สุด:
- ให้ใช้หัวจับไฮดรอลิกความแม่นยำสูงรวมกับ Coromant Capto®
- ลดระยะยื่นของเครื่องมือ
การกัดหยาบและการกัดกึ่งหยาบ
หากอัตราป้อนงานต่อฟันตัดน้อยกว่าความกว้างและระยะกินลึก พื้นผิวที่ได้จะมีรอยหยักในทิศทางที่ป้อนงานน้อยกว่า
การเก็บผิวละเอียดและการเก็บผิวละเอียดพิเศษ
การทำให้ผิวงานมีลวดลายที่นุ่มนวลและสมมาตรในทุกทิศทางนั้นมีประโยชน์อย่างยิ่ง เนื่องจากช่วยให้ขัดผิวได้ง่ายดายไม่ว่าจะเลือกวิธีการใดก็ตาม
โดยจะทำเช่นนี้ได้ต่อเมื่อ fz ≈ ae
ควรใช้ฟันตัดทำมุมเอนในการเก็บผิวละเอียดเป็นพิเศษเสมอเพื่อให้ลวดลายของผิวงานมีคุณภาพดีที่สุด
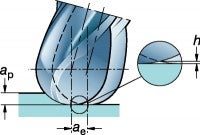
การกัดกึ่งหยาบที่มีค่า fz น้อยกว่า ae
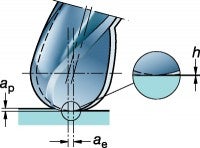
การเก็บผิวละเอียดเป็นพิเศษด้วยหัวกัดทำมุมเอนและมี fz เท่ากับ ae
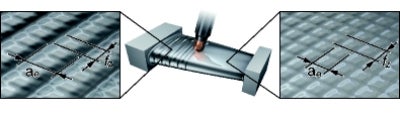
การกัดร่องหรือช่อง
การกดรองหรอชองเปนงานกดขางและงานกดปาดหนาทพบไดบอย โดยเฉพาะอยางยงในการกดดวยดอกเอนมล รองหรอชองมไดหลายลกษณะ... keyboard_arrow_right
การกัดบ่าฉาก
การปฏบตงานกดบาฉากประกอบไปดวย: การกดบาฉาก/ กดปาดหนา การกดขอบขาง การกดบาฉากผนงเบยงแบบบาง การกดบาฉาก/... keyboard_arrow_right
การกัดปาดหน้า
กระบวนการกดปาดหนารวมถง: การกดปาดหนาทวไป การกดอตราปอนสง การกดปาดหนางานหนก การเกบผวละเอยดดวยเมดมดไวเปอร การกดปาดหนาทวไป ความสำเรจในการกดปาดหนาคออะไร การกดปาดหนาคอกระบวนการกดทไดรบความนยมทสดและสามารถทำไดโดยใชเครองมอหลากหลายชนด... keyboard_arrow_right
เรื่องราวความสำเร็จ
อตราการขจดเนอโลหะ 236% วธท 1: การกดรองเตมหนาและการกดแทง ดอกเอนมล 2S342-1000-100CMA... keyboard_arrow_right