Plunge milling
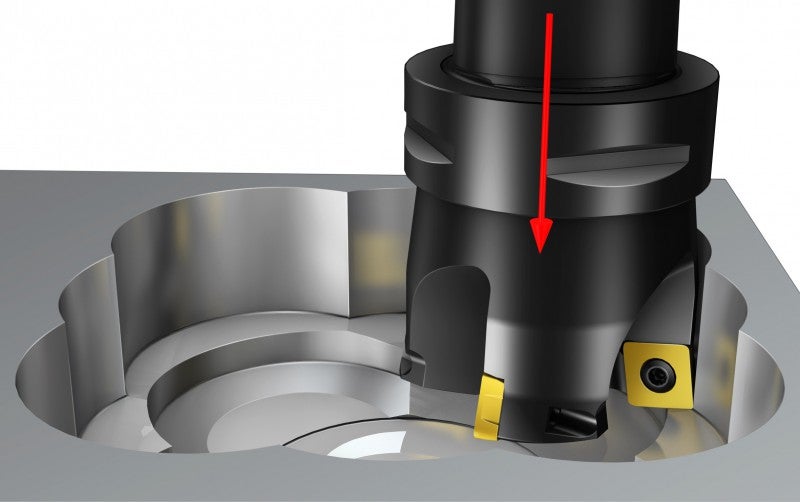
What is successful plunge milling?
In plunge milling, the cutting is performed at the end of the tool instead of at the periphery, which is advantageous due to the change in direction of the cutting forces from predominately radial to axial. In general, plunge milling is an alternate method when side millling is not possible due to vibrations.
For example:
- When the tool overhang is greater than 4 x DC
- When the stability is bad
- For semi-finishing of corners
- For difficult to cut materials such as titanium
It can also be an alternative when machine power or torque is a limitation.
Note: Under favorable conditions plunge milling is not the first choice due to a lower metal removal rate.
Choice of tools
Cutter selection is determined primarily by the diameter.
Plunge drilling
Plunging with drilling tools can be more effective up to approx. DC = 35 mm, see Drilling.
How to apply plunge milling operations
Cutting process
Plunge milling operations vary considerably from traditional milling. It uses the end of the tool to cut instead of the periphery, which beneficially changes the direction of the cutting forces from predominantly radial to axial. It can be compared to a boring operation with interrupted cuts.
Power consumption and noise are low.
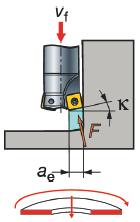
Plunge milling = interrupted boring.
Axial cutting forces.

Traditional milling.
Mainly radial forces.
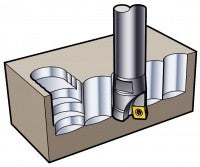
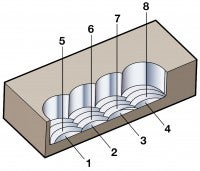
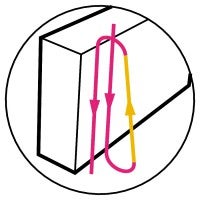
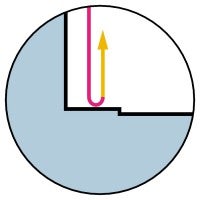

= program table feed

= rapid traverse
Avoid re-cutting on return stroke. Gradually decrease plunge depth.
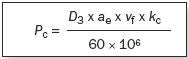
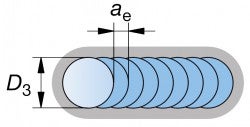
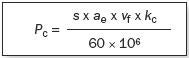
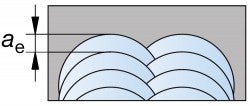
Power consumption calculation.
Feed in plunge milling
Feed in plunge milling | ||
Insert size | Overhang < 3xDC | Overhang > 3xDC |
9 | fz = 0.15 (0.10 - 0.20) | fz = 0.10 (0.08 – 0.15) |
14 | fz = 0.20 (0.10 - 0.25) | fz = 0.15 (0.10 - 0.20) |
Oversized cutter L ≤ 3xDC
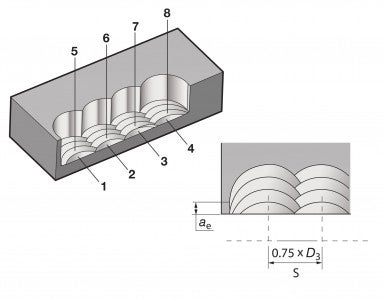
iC | max ae |
9 | 8 |
14 | 13 |
s = 75% DC
Oversized cutter L ≥ 3xDC
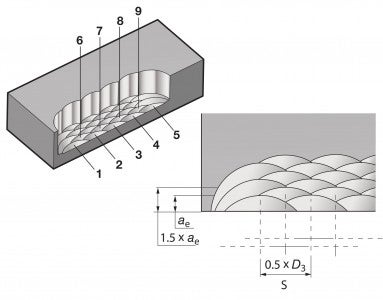
iC | max ae |
9 | 7 |
14 | 12 |
s = 50% DC
ae = max for insert
Side step s = X % DC
* S is tool overhang specific
Plunge milling tips
- Horizontal machine facilitates chip evacuation
- Start milling from bottom and work up
- Use cutting fluid or compressed air to facilitate chip evacuation
- In comparison with traditional methods, plunge milling requires a lower feed per tooth
- Ensure that more than one tooth is engaged
- Use extra close pitch cutters
- Use maximum ae – depending on insert size
- Use s = 0.75 x DC when moving sideways
- Gradually decrease plunge depth to minimize vibration
- Use a "hook program" to prevent re-cutting on the return stroke. Feed 1 mm away from wall at the end of the cut
- Note: A drilling cycle is not recommended due to re-cutting which can cause vibration during retraction
- Always strive to leave a constant stock for a subsequent finishing operation
Slots
- Plunging is an effective technique for machining deep and closed slots
- Chip evacuation becomes essential. A horizontal set-up and the use of cutting fluid or compressed air will assist in this process
- A drill is recommended for deep and narrow slots, as it provides the best chip evacuation and highest step-over rate
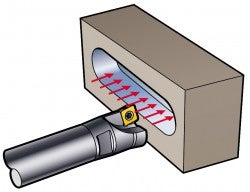
Cavities/pockets
- Chip evacuation is critical, just like in closed slotting
- Use a horizontal set-up and cutting fluid or compressed air
- Chip evacuation can be further improved by driling the largest possible start hole. 1.5 x DC is recommended
- Reduce feed in the first two plunge steps
- Move sideways and try to prevent full slotting
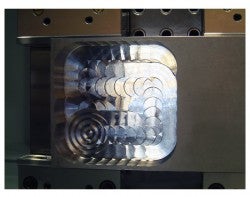
Corners
Plunge milling of the remaining stock (rest milling) after a roughing operation in deep 90 degree corners can be advantageous.
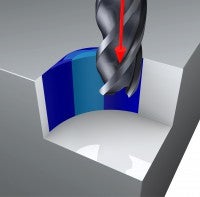
DC = 12.7 mm
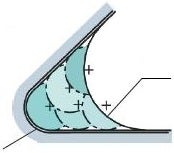
Start radius = 16 mm
End radius = 6 mm
Corner machining
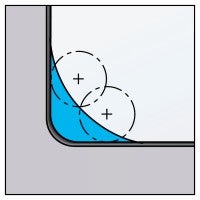
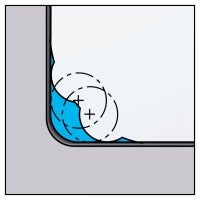
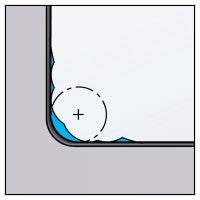
Milling holes and cavities/pockets
Two-axes ramping linear Circular ramping Widening a hole Circular external milling... keyboard_arrow_right
Slicing methods
Slicing and trochoidal milling methods were originally developed for roughing and... keyboard_arrow_right
Ramping: Two axis linear and circular
What is successful ramping? Linear ramping is a commonly used, efficient way of... keyboard_arrow_right
Widening a hole
Widening an existing hole can be performed either by circular ramping or circular... keyboard_arrow_right