Milling holes and cavities/pockets
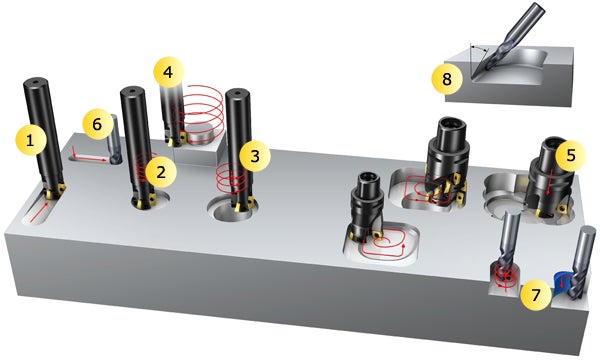
- Two-axes ramping linear
- Circular ramping
- Widening a hole
- Circular external milling or ramping
- Plunge milling
- Peck milling
- Slicing methods
- Closed pockets or angles
Hole milling: creating openings
- Creating openings in a solid workpiece
- Widening a hole or a cavity
- Opening up/widening a cavity or pocket
Creating openings in a solid workpiece
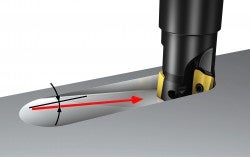
Linear ramping
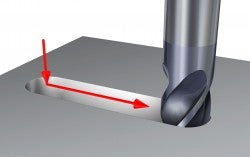
Peck milling
Opening a slot
When milling a hole, linear ramping (2-axes simultaneously) is always preferred to peck milling.
Peck milling is an alternative hole milling method, but it often produces long chips and generates undesirable cutting forces on the cutter.Opening a hole or a cavity
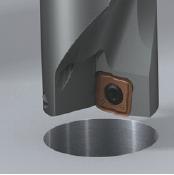
Drilling
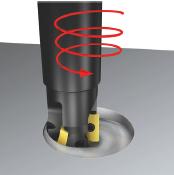
Circular ramping
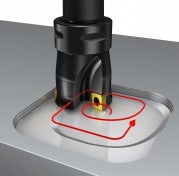
Ramping a cavity
Drilling is the traditional and fastest method of producing a hole, but chip breaking can be a challenge in some materials, and it lacks the flexibility to produce varying diameters and non-round shapes.
Circular ramping (3-axis simultaneously) is a less productive method than drilling a hole, but can be a good alternative in cases of:
- Large diameter holes when machine power is limited
- Smaller series production. A rule of thumb for diameters larger than 25 mm: milling is cost efficient up to a series of approx. 500 holes
- When a range of hole sizes are to be machined
- Limited tool magazine space to store many drill sizes
- Production of blind holes, when a flat bottom is required
- Non-rigid, thin walled components
- Interrupted cuts
- Difficult materials to drill due to chip breaking and chip evacuation
- No cutting fluid is available
- When milling cavities/pockets (“non-round holes”)
Choice of method - example
Opening up a cavity/ pocket
![]() | ||||||
![]() | ||||||
Drilling and circular milling ![]() ![]() | Drilling and plunge milling ![]() ![]() | Circular ramping ![]() | ||||
Advantages + High material removal for non-round holes + First choice in aerospace frame titanium structural parts Disadvantages – Requires a stable machine – Chip evacuation – horizontal machine – Careful programming required | Advantages + Problem solver in long overhang applications + Simple programming suitable for older/multi-spindle machines Disadvantages – Low material removal | Advantages + Reduced tools (no drill needed) + Flexible (produces wide range of sizes) + No cutting fluid required = good for open machines + Suitable for all machine concepts and configurations Disadvantages – Less productive for large cavities | ||||
The basic choice for pockets | Problem solver Long overhangs | The basic choice for 3D cavities |
Widening a hole or a cavity
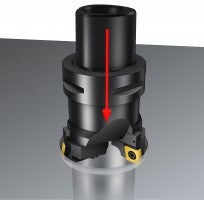
Boring
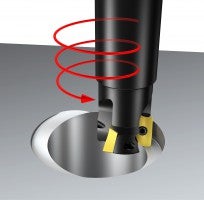
Circular ramping
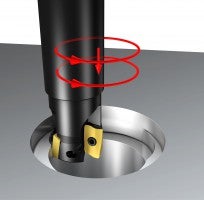
Circular milling
Widening a hole
Boring is normally the fastest method, for the same reasons as drilling, but hole milling is sometimes a good alternative. Two alternate milling methods can be used: circular ramping (3-axes) or circular milling (2-axes). Circular ramping is preferred when the hole is deeper than ap max, or in vibration sensitive applications. In addition, the roundness/concentricity of the hole becomes better when ramping, especially with long overhangs. Roundness will be improved if the workpiece is rotated instead of moving the milling cutter in a circular path in both circular ramping and milling operations.Widening a cavity
Internal shoulder milling and plunge milling require a starting hole and should be compared to ramping a cavity directly into a solid block.
- Ramping (3-axes) has an advantage because it only requires one tool and can produce 3D-shapes, making it suitable for profile milling. If applied with high feed techniques (light and fast), the cutting forces will be directed in a favorable manner that minimizes vibration problems
- Plunge milling often solves problems with long overhangs and/or deep cavities
- Internal shoulder milling requires more programming than plunge milling, but it is faster
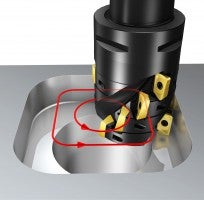
Internal shoulder milling
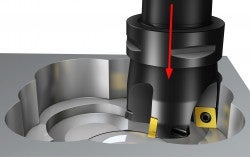
Plunge milling
Rest (remaning stock) milling
When the roughing of a cavity is completed, stock often remains, especially in corners. Plunge milling with a smaller cutter is one method for coming closer to the finished shape. Slicing (light and fast) is another technique often used in corner milling. Trochoidal milling is one type of slicing technique that is also used for milling slots, pockets etc.
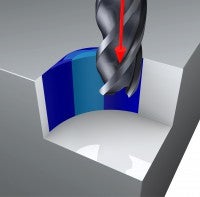
Plunging in corners
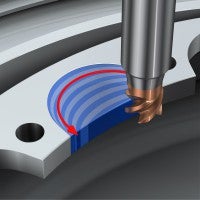
Slicing technique – light and fast
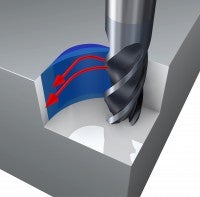
Slicing in corners
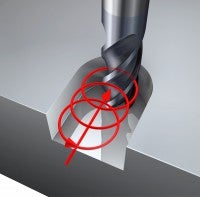
Trochoidal
How to open up/widen a cavity or pocket
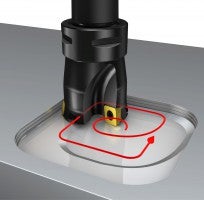
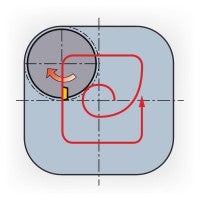

There are two clear strategies:1. Circular ramping (3-axes) – small ap
Use a cutter with a small entering angle. A round insert cutter is another alternative.
This “light and fast” technique provides an excellent metal removal rate and is the first choice for less stable machines (acc. to ISO 40) and when the cavity has a profiled shape, i.e. die and mould.
Note: Avoid machining all the way against a 90° shoulder because the effect of a low approach angle will be lost, i.e. the depth of cut increases dramatically.
Cutting parameters:
- Maximum cutter diameter = 1.5 x component corner radius
- Circular ramp to depth – anti-clockwise
- Roll into the next cut
- Radial cut – max. ae = 70% DC
- Axial cut for round insert cutter 25% iC
- Tool path radius in the corner = DC
- Reduce corner feed
2. Circular milling (2-axes) – large ap
Drill a hole, and then change to a shoulder end mill or a long edge cutter. A typical application area is found in aerospace framing – titanium machining.Application hints
Ensure good chip evacuation to prevent re-cutting of chips/chip jamming:
- Horizontal spindle (ISO 50) is preferred
- High pressure coolant or compressed air with through tool coolant
- DC should be no greater than 75% of hole dia. Use a large axial cut – maximum ae = 2 x DC
The drilled hole should be entered in a circular path:
- Control radial engagement, maximum ae = 30% of DC
Control radial engagement to minimize vibration in corners, and to maximize productivity:
- Use the largest radius possible in the corners, spiral morph programming
- Use the largest DC possible and complete rest milling separately at no greater than 1.5 x the corner radius
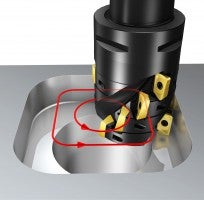
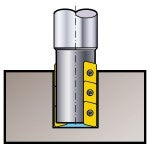

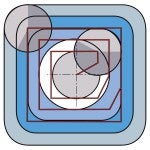

Small corner radius
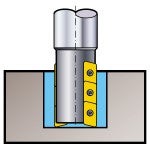

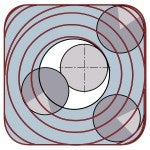

Spiral morph programming
Widening a hole
Widening an existing hole can be performed either by circular ramping or circular... keyboard_arrow_right
Ramping: Two axis linear and circular
What is successful ramping? Linear ramping is a commonly used, efficient way of... keyboard_arrow_right
Peck milling
What is successful peck milling? Peck milling is an alternative to ramping for opening... keyboard_arrow_right
Plunge milling
What is successful plunge milling? In plunge milling, the cutting is performed at... keyboard_arrow_right