การกลึงวัสดุพิเศษ
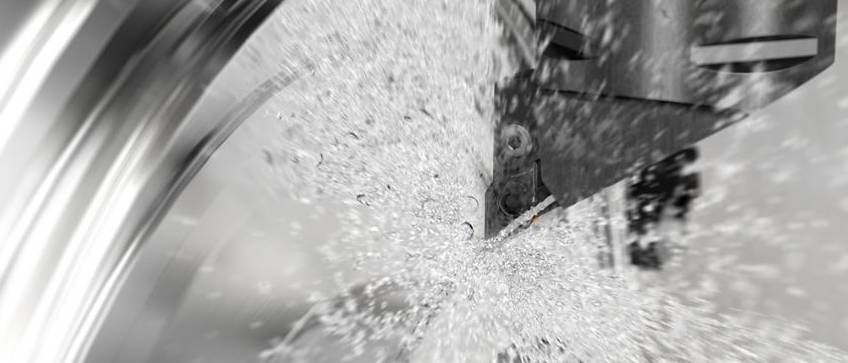
ซูเปอร์อัลลอยทนความร้อนและไทเทเนียมอัลลอยเป็นวัสดุที่มีคุณสมบัติตัดเฉือนยาก และไม่เหมือนกับโลหะชนิดอื่น จึงอาจจัดได้ว่าเป็นวัสดุที่มีความพิเศษ ซึ่งมีคุณสมบัติการใช้งานดีเยี่ยม เช่น อัตราส่วนความแข็งแรงต่อน้ำหนักสูง คงความแข็งแรงและความแข็งเอาไว้ได้ที่อุณหภูมิสูง และต้านทานการเกิดสนิมได้ดีเยี่ยม
อย่างไรก็ตาม เพราะวัสดุกลุ่มนี้ตัดเฉือนได้ยาก จึงทำให้จำเป็นต้องใช้ระบบเครื่องมือที่ "พิเศษ" ด้วยเช่นกัน โดยจะต้องผสมผสานระหว่างเครื่องมือที่ออกแบบสำหรับวัสดุชนิดนี้โดยเฉพาะรวมกับวิธีการตัดเฉือนและทางเดินเครื่องมือที่เหมาะสม เพื่อให้สามารถทำงานได้อย่างมีประสิทธิภาพ เชื่อถือได้ และมีคุณภาพ
เนื้อหานี้มีรายละเอียดโดยรวมเกี่ยวกับความต้องการในการตัดเฉือน และความก้าวหน้าที่ช่วยยกระดับประสิทธิภาพและความเชื่อถือได้ให้กับงานกลึงวัสดุกลุ่มนี้
วัสดุที่มีคุณสมบัติเฉพาะตัว แต่ตัดเฉือนยาก
ความสามารถในการตัดเฉือนวัสดุชิ้นงานขึ้นอยู่กับปัจจัยหลายอย่าง ซึ่งส่งผลต่อทั้งความต้องการและผลลัพธ์ของงานตัดเฉือน หรือถ้าพูดแบบรวมๆ ก็คือ ความยากง่ายของการตัดเฉือนวัสดุชิ้นงานเทียบกับการสึกหรอของเครื่องมือและเศษที่เกิดจากการตัดเฉือน ส่วนใหญ่เป็นที่ทราบกันอยู่แล้วว่า วัสดุพิเศษเหล่านี้มีความสามารถในการตัดเฉือนต่ำ ถึงแม้จะถูกมองว่าเป็นวัสดุที่ท้าทายสำหรับงานตัดเฉือน แต่การตัดเฉือนวัสดุเหล่านี้ จริงๆ แล้วก็ไม่ได้ยาก ถ้าหากใช้วิธีการที่ถูกต้อง
วัสดุพิเศษที่มักจะถูกนำมาใช้ค่อนข้างบ่อยจัดอยู่ในกลุ่ม ISO S ได้แก่ ซูเปอร์อัลลอยทนความร้อน (Heat-Resistant Superalloy หรือ HRSA) และไทเทเนียมอัลลอย ถ้าพิจารณาเฉพาะในส่วนของการตัดเฉือน เราสามารถจะแบ่งวัสดุกลุ่มนี้ออกเป็นกลุ่มย่อยเล็กลงได้อีกตามองค์ประกอบ ลักษณะ และคุณสมบัติ สมบัติทางเคมีและองค์ประกอบทางโลหะวิทยาโดยธรรมชาติของอัลลอยในกลุ่ม S จะเป็นตัวกำหนดสมบัติทางกายภาพและความสามารถในการตัดเฉือนของวัสดุชนิดนั้นๆ การควบคุมเศษในวัสดุกลุ่มนี้ค่อนข้างที่จะท้าทาย เนื่องจากเศษมีการแตกเป็นชิ้นเล็กๆ ก่อนที่จะถูกคายออก (Segmented Chip) รวมทั้งการที่แรงตัดจำเพาะอาจสูงกว่าของเหล็กกล้าได้ถึงสองเท่า (ค่านี้ใช้บอกว่าวัสดุนั้นๆ ตัดเฉือนได้ยากง่ายเพียงใด รวมทั้งใช้เพื่อระบุค่าแรงตัดและกำลังเครื่องจักรที่ต้องใช้)
เหตุผลหลักที่ทำให้วัสดุ HRSA เป็นวัสดุที่ท้าทายสำหรับงานตัดเฉือนก็คือ คุณสมบัติคงความแข็งแรงได้สูงที่อุณหภูมิสูง วัสดุชนิดนี้จะไม่อ่อนตัวลงและไม่ได้มีลักษณะการไหลเหมือนกับวัสดุชนิดอื่นๆ รวมทั้งยังเกิดการแข็งตัวในระหว่างการตัดเฉือนได้ง่าย ทำให้มีแรงกลและความร้อนสะสมสูงที่คมตัด อัลลอยที่มีนิกเกิล เหล็ก หรือโคบอลต์เป็นส่วนประกอบหลักจัดเป็นกลุ่มย่อยของวัสดุ HRSA ที่มีคุณสมบัติเฉพาะตัวเหมาะสำหรับผลิตเป็นชิ้นงานสำหรับอุตสาหกรรมอากาศยาน พลังงาน และการแพทย์ เนื่องจากสามารถคงคุณสมบัติที่ต้องการเอาไว้ได้จนเกือบถึงจุดหลอมเหลว รวมทั้งยังทนต่อการกัดกร่อนได้ดีเป็นพิเศษ แต่ในแง่ของความสามารถในการตัดเฉือน การทำงานกับวัสดุเหล่านี้จำเป็นต้องมีเครื่องจักรที่เหมาะสม การจับยึดที่แข็งแรง เกรดและรูปทรงเม็ดมีดที่ออกแบบมาโดยเฉพาะ ระบบนำหล่อเย็นที่มีประสิทธิภาพ และที่สำคัญที่สุด จะต้องใช้วิธีการตัดเฉือนและมุมเข้างานที่เหมาะสม ทั้งหมดนี้ส่งผลให้จำเป็นต้องมีการวางแผนการทำงานอย่างละเอียดมากขึ้น และทำให้ต้องทำงานส่วนหน้าของการผลิตมากขึ้น
ไทเทเนียมอัลลอยเองก็มีการแบ่งออกเป็นกลุ่มย่อยเช่นกัน โดยแต่ละกลุ่มจะมีระดับความสามารถในการตัดเฉือนแตกต่างกันออกไป โดยทั่วไปแล้ว ความสามารถในการตัดเฉือนจะแบ่งออกเป็น (ความเหนียว) แย่มากหรือแย่น้อย ทำให้จำเป็นต้องใช้เครื่องมือและวิธีการตัดเฉือนที่พิเศษมาก ความยากของการตัดเฉือนมีสาเหตุมาจากคุณสมบัติการนำความร้อนต่ำ ความแข็งแรงสูงที่อุณหภูมิสูง เศษบางจากการถูกเฉือนออกทำให้เกิดการครูด ส่งผลให้ผิวคายเศษมีพื้นที่สัมผัสแคบลง และแรงตัดสูงที่คมตัด เศษจากการตัดมีรูปทรงไม่สม่ำเสมอ ส่งผลให้แรงตัดไม่คงที่ รวมทั้งอัลลอยบางชนิดยังมีปริมาณคาร์ไบด์ค่อนข้างสูง ทำให้เกิดการเสียดสีกับเครื่องมือมากเป็นพิเศษ การใช้ความเร็วตัดสูงเกินไปจะทำให้เกิดปฏิกิริยาเคมีระหว่างเศษกับวัสดุทำเครื่องมือ ส่งผลให้คมตัดอาจกะเทาะ/หักทันที รวมถึงปัญหาการสะสม/การเชื่อมติดของเศษวัสดุที่คมตัด อัลลอยบางชนิดยังเกิดการแข็งตัวในระหว่างตัดเฉือนได้ง่าย ส่งผลให้เกิดการสึกหรอจากการแพร่ซึมของวัสดุและเป็นสาเหตุของการเกิดเศษคราบ ทั้งหมดนี้ส่งผลให้การทำงานในขั้นตอนต่อไปมีความยากขึ้นตามไปด้วย
วัสดุอาจจะพิเศษสำหรับการใช้งานก็จริง แต่การตัดเฉือนวัสดุ HRSA และไทเทเนียมอัลลอยให้ได้สำเร็จนั้นก็ไม่ใช่เรื่องง่าย
เมื่อต้องการลงวัสดุกลึง...
... ความสำเร็จจะขึ้นอยู่กับการหาจุดสมดุลระหว่างชนิดของวัสดุและปัจจัยในการทำงาน กฎพื้นฐานทั่วไปส่วนหนึ่งที่จะช่วยให้สามารถตัดเฉือนวัสดุกลึงได้อย่างมีประสิทธิภาพ ได้แก่:
- วางแผนวิธีการตัดเฉือนที่เหมาะสมล่วงหน้า พร้อมทั้งกำหนดรายละเอียดให้มากที่สุดเท่าที่จะสามารถทำได้
- เลือกมุมเข้างานที่เหมาะสมที่สุด
- เลือกทางเดินเครื่องมือที่ดีที่สุดและใช้ระบบจับยึดเครื่องมือที่มีความมั่นคงสูง
- ใช้เครื่องมือตัดเฉพาะทางที่ใหม่และดีที่สุด
- ใช้ค่าการตัดตามที่แนะนำเพื่อให้กระบวนการตัดเฉือนมีประสิทธิภาพและเชื่อถือได้
- คำนวณระยะการตัดรวมวัดแบบคลายเกลียวเพื่อวางแผนการตัด
- ใช้น้ำหล่อเย็นอย่างถูกวิธี รวมทั้งใช้ระบบน้ำหล่อเย็นแรงดันสูงที่ทันสมัย
- ใช้ประโยชน์จากคำแนะนำและบริการช่วยเหลือจากผู้เชี่ยวชาญ
ควรทำการวางแผนการตัดเฉือนอย่างละเอียดเสมอ เนื่องจากมีปัจจัยหลายอย่างที่ต้องตัดสินใจให้ชัดเจน เช่น ข้อจำกัดเกี่ยวกับสถานะ/ลักษณะของวัสดุชิ้นงาน ลักษณะของชิ้นงาน เช่น ชิ้นงานหล่อ ฟอร์จ แทงชิ้นงาน การอบชุบ การอบละลาย และการบ่มแข็ง มีผลอย่างมากต่อชิ้นงาน รวมถึงตัวเลือกเครื่องมือและวิธีการตัดเฉือนที่เหมาะสม สภาพผิวของชิ้นงาน รวมถึงความแข็งของชิ้นงานแต่ละประเภทจะมีความแตกต่างกันออกไปและมีผลต่อการตัดเฉือน การเลือกวิธีการกลึงควรพิจารณาถึงข้อกำหนดของการออกแบบชิ้นงานที่จะทำการตัดเฉือน รวมถึงการตัดเฉือนแต่ละขั้น ไม่ว่าจะเป็นการกลึงหยาบ (ขั้นแรก) การเก็บผิวกึ่งละเอียด (ขั้นกลาง) และการเก็บผิวละเอียด (ขั้นสุดท้าย) ความท้าทายที่พบบ่อยๆ ได้แก่ ปัญหาจากรูปทรงที่ซับซ้อนและคุณภาพผิวงานที่ได้
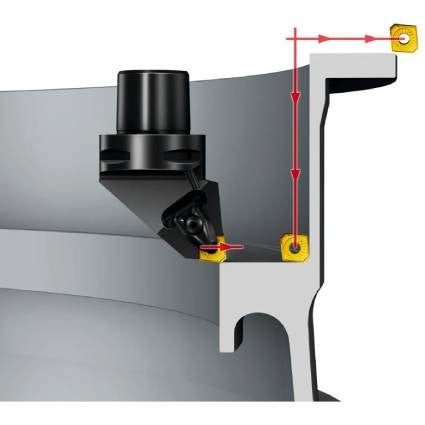
การวางแผนการกลึงวัสดุพิเศษจะต้องพิจารณาจากพื้นฐานของการออกแบบชิ้นงาน วัสดุ และลักษณะชิ้นงาน ในกรณีที่ทำได้ ควรกำหนดรูปแบบการทำงานสำหรับการตัดเฉือนขั้นแรก ขั้นกลาง และขั้นสุดท้ายตามความเหมาะสมกับลักษณะวัสดุและความต้องการด้านคุณภาพ การวางแผนทางเดินเครื่องมือและการโปรแกรมอัตราป้อนงานให้ต่ำลงเป็นปัจจัยที่จะช่วยบอกถึงระดับการสึกหรอ ประเภทของเครื่องมือ ระยะเวลาการผลิต และระดับความเชื่อถือได้
ลักษณะการตัดของวัสดุกลุ่ม …
… มักจะขึ้นอยู่กับวิธีการเข้าทำงานของคมตัด โดยมุมเข้าทำงานของคมตัดและหน้าลายเม็ดมีดจะมีผลอย่างมากต่อประสิทธิภาพ อายุการใช้งานของเครื่องมือ ความเชื่อถือได้ และชิ้นงานที่ออกมา การเลือกรูปทรงเม็ดมีดควรเลือกให้เหมาะกับลักษณะการตัดที่จะทำ อย่างไรก็ตาม การเลือกรูปแบบการทำงานนั้นควรพิจารณาจากข้อเท็จจริงที่ว่า การใช้มุมเข้าทำงานแคบจะยิ่งส่งผลดีต่อประสิทธิภาพและอายุการใช้งานของเครื่องมือ
การเลือกเกรดเม็ดมีดควรต้องเลือกให้เหมาะกับมุมเข้าทำงานที่ใช้ด้วยเช่นกัน เนื่องจากมุมเข้าทำงานจะมีผลต่อรูปแบบการสึกหรอเป็นรอยบากที่คมตัด ขนาดของรอยบากที่เกิดขึ้น และอาจทำให้เครื่องมือหมดสภาพเร็วกว่าปกติได้ การเลือกวิธีการเข้าทำงานที่เหมาะสมยังช่วยให้สามารถเลือกเกรดเม็ดมีดที่มีประสิทธิภาพสูงกว่าได้ พร้อมทั้งยังช่วยยืดอายุการใช้งานและความเชื่อถือได้

มุมเข้าทำงานของเครื่องมือตัดส่งผลต่อความหนาของเศษ อัตราป้อนงาน แรงตัด รวมถึงรูปแบบการตัดที่สามารถทำได้ การเลือกมุมเข้าทำงานสำหรับงานตัดเฉือนวัสดุพิเศษจะส่งผลโดยตรงต่อประสิทธิภาพและความเชื่อถือได้ของงาน รวมทั้งยังเกี่ยวข้องกับการเลือกรูปทรงเม็ดมีดและรัศมีปลายคมตัด รวมไปถึงประสิทธิภาพของวัสดุทำเครื่องมือตัด โดยปกติแล้ว เม็ดมีดทรงกลมและเม็ดมีด Xcel เป็นตัวเลือกที่ดีที่สุดสำหรับงานประเภทนี้
การเลือกวัสดุทำเครื่องมือ (เกรดเม็ดมีด) ควรพิจารณาจากรูปแบบการกลึงที่ทำว่าเป็นการกลึงหยาบ การเก็บผิวกึ่งละเอียด หรือการเก็บผิวละเอียด รวมไปถึงลักษณะของชิ้นงานและรูปแบบการตัด วัสดุพิเศษมีความแข็ง ดังนั้นจึงควรพิจารณาเรื่องการเสียรูปถาวรของคมตัดด้วยเสมอ เนื่องจากเป็นปัจจัยเสี่ยงหลักในการเลือกเกรดเม็ดมีด (การสึกหรอแบบรอยบากเป็นผลมาจากมุมเข้าทำงานและระยะกินลึกดังที่กล่าวไปแล้วก่อนหน้านี้) การเลือกเกรดเม็ดมีดยังควรทำไปพร้อมกับการเลือกรูปทรงเม็ดมีด เนื่องจากจำเป็นต้องประเมินความแข็งแรงของเครื่องมือจากมุมเข้าทำงานที่ใช้ รวมทั้งยังต้องพิจารณาความเหมาะสมกับอัตราการกลึงและลักษณะการตัดว่าเป็นการตัดต่อเนื่องหรือการตัดกระแทก เกรดเฉพาะทางจึงถือเป็นหัวใจสำคัญของงานตัดเฉือนวัสดุ HRSA
ข้อพิจารณาสำคัญคือ เม็ดมีดจะต้องมีความแข็งขณะอุณหภูมิสูงและความเหนียวในระดับที่เหมาะสม และชั้นเคลือบผิวต้องมีประสิทธิภาพการยึดเกาะเพียงพอ นอกจากนี้ เม็ดมีดสำหรับการตัดเฉือนวัสดุกลุ่มนี้ยังมีลักษณะเฉพาะตัว ได้แก่ เป็นเม็ดมีดมุมบวก คมตัดคมและแข็งแรง และร่องหักเศษเป็นแบบเปิด
การเลือกค่าการตัดที่เหมาะที่สุดถือเป็นกุญแจสำคัญต่อความสำเร็จของการตัดเฉือนวัสดุกลุ่มนี้เช่นกัน ค่าความเร็วตัดจะขึ้นอยู่กับความเร็วที่ผิวชิ้นงาน อัตราป้อนงาน และระยะกินลึก โดยสามารถปรับเปลี่ยนได้เพื่อให้การตัดเฉือนมีประสิทธิภาพ ความเชื่อถือได้ และคุณภาพระดับสูง ความเร็วตัดจะมีผลต่อความร้อนที่เกิดขึ้นและผลกระทบของความร้อนที่มีต่อเม็ดมีด โดยความร้อนจะต้องสูงพอที่จะทำให้เศษเปลี่ยนรูปได้ แต่จะต้องไม่สูงจนเกินไปจนกระทั่งเกิดความไม่สมดุลกับวัสดุทำเครื่องมือ ค่าความเร็วที่ผิวชิ้นงานโดยทั่วไปจะอยู่ในช่วง 130 ถึง 260 ฟุต/นาที (40 ถึง 80 ม./นาที) สำหรับเม็ดมีดคาร์ไบด์เฉพาะทางและอยู่ในช่วง 490 ถึง 1,310 ฟุต/นาที (150 ถึง 400 ม./นาที) สำหรับเม็ดมีดเซรามิก
อัตราป้อนงานเป็นปัจจัยหลักที่ส่งผลต่อระยะเวลาการตัดเฉือนและความหนาของเศษ ในกรณีของวัสดุพิเศษ จะต้องใช้ความระมัดระวังเป็นพิเศษในการเลือกอัตราป้อนงานที่สมดุลเนื่องจากค่าที่เหมาะสมจะอยู่ในช่วงแคบมาก โดยสำหรับการกลึงหยาบ จะต้องปรับอัตราป้อนงานให้ได้เศษขนาดใหญ่ที่สุด แต่จะต้องไม่เกินกำลังของคมตัด ในขณะที่สำหรับการเก็บผิวละเอียด จะต้องปรับค่าให้ได้เศษหนาพอที่จะป้องกันไม่ให้เกิดความร้อนสูงเกินไปและไม่มีการแข็งตัวระหว่างตัดเฉือน
ระยะกินลึกมักจะส่งผลต่อมุมเข้าทำงานของคมตัด ทำให้จำเป็นต้องเลือกค่าไม่สูงเกินกว่าที่กำหนด ตัวอย่างเช่น ในกรณีที่ใช้เม็ดมีดทรงกลมกับวัสดุ HRSA ควรใช้ระยะกินลึกไม่เกิน 15% ของเส้นผ่านศูนย์กลางเม็ดมีด นอกจากนี้ยังควรเลือกระยะกินลึกอย่างระมัดระวังสำหรับการกลึงขึ้นรูปด้วยเช่นกัน เนื่องจากมักจะต้องมีการกลึงช่องหรือบ่าชิ้นงาน ดังนั้นจึงต้องระวังไม่ให้ระยะกินลึกสูงกว่าอาร์คที่เหมาะสมของหน้าสัมผัสคมตัด
ในส่วนของอายุการใช้งานของเครื่องมือ สิ่งสำคัญคือจะต้องคำนวณระยะการตัดรวมวัดแบบคลายเกลียว (Spiral Cutting Length หรือ SCL) อย่างละเอียด ซึ่งจะช่วยให้สามารถวางแผนและโปรแกรมช่วงหยุดเดินเครื่องจักรเพื่อสลับคมเม็ดมีดได้ล่วงหน้า รวมทั้งยังช่วยให้สามารถใช้งานเครื่องมือด้วยความเร็วที่เหมาะสมจนครบรอบการตัด โดยที่คมตัดยังคงรักษาคุณภาพผิวงานเอาไว้ได้ตามที่ต้องการ
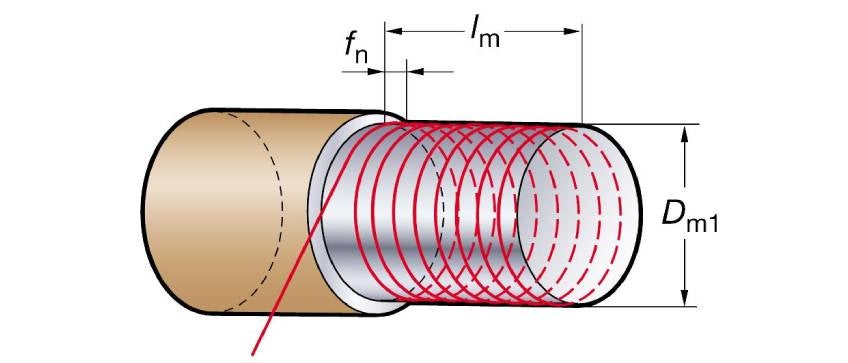
การคำนวณระยะการตัดรวมถึงการวัดแบบคลายเกลียวช่วยในการคาดการณ์ระยะเวลาหรือระยะการตัด เพื่อให้สามารถลดระยะเวลาตัดเฉือนและปรับปรุงคุณภาพผิวงานสำหรับการทำงานกับวัสดุพิเศษ รวมทั้งยังช่วยให้สามารถวางแผนช่วงหยุดเครื่องจักรเพื่อเปลี่ยนเม็ดมีดได้อย่างเหมาะสมตามลักษณะงานและค่าการตัด ซึ่งจะช่วยยืดอายุการใช้งานของเครื่องมือและเพิ่มอัตราการใช้ประโยชน์จากเครื่องจักร
การสึกหรอของเครื่องมือเป็นผลมาจาก …
… สภาวะที่มีแรงตัดสูงรวมกับอุณหภูมิสูงที่คมตัด โดยมักจะทำให้คมตัดเกิดการสึกหรอเป็นรูปแบบเฉพาะ การสึกหรอที่พบได้บ่อย ได้แก่ การสึกหรอแบบรอยบาก ซึ่งกล่าวถึงไปแล้วก่อนหน้านี้ (การสึกหรอทางกลโดยเป็นรอยเส้นของวัสดุชิ้นงานที่ระดับเดียวกับระยะกินลึก) การเสียรูปถาวรของคมตัด ซึ่งเป็นผลมาจากสภาวะอุณหภูมิสูงและความดันสูง และสุดท้ายคือการสึกหรอจากการเสียดสี ซึ่งเกิดจากการตัดเฉือนวัสดุที่มีความแข็งมากกว่าปกติ การสึกหรออีกประเภทหนึ่งคือ การสึกหรอเป็นรอยเฉือนด้านบนของเม็ดมีดเซรามิก ซึ่งชั้นด้านบนของคมตัดถูกเฉือนหลุดออก วิธีการเข้าทำงานของคมตัดมีบทบาทอย่างมากต่อรูปแบบการสึกหรอที่เกิดขึ้น
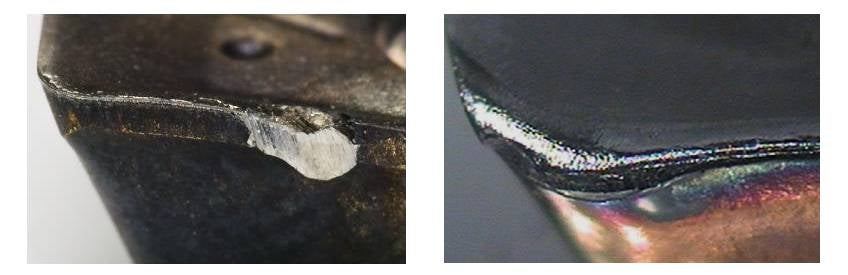
สำหรับวัสดุพิเศษ การเลือกเกรดเม็ดมีดจะไม่ได้เกี่ยวข้องโดยตรงกับการกลึงหยาบและการเก็บผิวละเอียดเหมือนกับวัสดุชนิดอื่นๆ แต่การเลือกเกรดจะมีจุดประสงค์เพื่อเป็นการเพิ่มประสิทธิภาพมากกว่า ดังนั้นจึงอาจมีความยุ่งยากมากกว่าเล็กน้อย เนื่องจากจะต้องพิจารณารูปทรงของเม็ดมีดรวมกับการเข้าทำงานของคมตัดและลักษณะการทำงาน การป้องกันการสึกหรอเชิงทำลาย เช่น การสึกหรอแบบรอยบากและการเสียรูปถาวร (ในภาพ) สามารถทำได้โดยการเลือกใช้เครื่องมือที่เหมาะสม รวมกับค่าการตัดและวิธีการที่เหมาะสม เม็ดมีดคาร์ไบด์ รวมถึงเม็ดมีดเซรามิกไซอะลอนและเม็ดมีดเซรามิกใยวิสเกอร์ (ในบางกรณี) มักจะเป็นตัวเลือกที่เหมาะที่สุดและสามารถใช้งานได้ค่อนข้างหลากหลาย
การกลึงวัสดุพิเศษควรใช้มุมเข้าทำงานแคบ โดยควรเท่ากับหรือน้อยกว่า 45 องศา ลักษณะการทำงานที่ให้ประสิทธิภาพต่ำสุดคือ การใช้มุมเข้าทำงาน 90/0 องศาหรือใช้ระยะกินลึกมากกว่ารัศมีปลายคมตัดของเม็ดมีด การใช้มุมเข้าทำงานกว้าง/แคบเกินไปจะทำให้เศษบางลงและอัตราป้อนงานสูงขึ้น
สำหรับการกลึงวัสดุ HRSA มุมเข้าทำงานของเครื่องมือจะเป็นตัวกำหนดว่า ควรเลือกใช้เม็ดมีดเคลือบผิวแบบ PVD หรือ CVD ชั้นเคลือบผิวของเม็ดมีดจะช่วยป้องกันผลกระทบเนื่องจากความร้อน การเคลือบผิวแบบ PVD เหมาะสำหรับมุมเข้าทำงาน 90/0 องศา และการเคลือบผิวแบบ CVD เหมาะสำหรับมุมเข้าทำงาน 45 องศา ในทางกลับกัน การเคลือบผิวจะไม่มีข้อใดๆ สำหรับการกลึงไทเทเนียม ดังนั้นในกรณีนี้ สิ่งสำคัญคือต้องเลือกรูปแบบคมตัดที่เหมาะกับงานมากที่สุด เช่น ใช้เม็ดมีดทรงกลมสำหรับการเก็บผิวละเอียด เม็ดมีด PVD รุ่นใหม่มีความแข็งสูงและต้านทานการเสียรูปของคมตัดรวมถึงผลกระทบจากการเปลี่ยนแปลงอุณหภูมิได้ดี อีกทั้งยังมีคมตัดคม ทำให้เหมาะสำหรับใช้กับการกลึงหยาบจนถึงการเก็บผิวละเอียดในวัสดุที่มีการพอกติดคมตัด
รูปทรงเม็ดมีดที่เหมาะสม …
… ถือเป็นปัจจัยการทำงานสำคัญสำหรับการตัดเฉือนวัสดุกลุ่ม เม็ดมีดทรงกลม (ทรง R) เป็นรูปทรงหลักที่แนะนำสำหรับการทำงานกับวัสดุดังกล่าว เนื่องจากคมตัดมุมบวกมีความคมและแข็งแรง เศษที่ได้จากการตัดจะมีความหนาแตกต่างกันตามแนวคมตัด ทำให้สามารถใช้อัตราป้อนงานได้สูง รัศมีเม็ดมีดมีขนาดใหญ่ ทำให้ไม่ต้องจำกัดอัตราป้อนงานเนื่องจากผิวงานที่ได้ นอกจากนี้ เม็ดมีดทรงกลมยังช่วยให้โปรแกรมการทำงานได้อเนกประสงค์ขึ้น โดยสามารถทำได้ทั้งการกลึงขึ้นรูปและการกลึงหลุม ซึ่งพบได้บ่อยในชิ้นงาน
ในบางกรณี เม็ดมีดทรงสี่เหลี่ยมจัตุรัส (ทรง S) อาจจะเหมาะที่สุดสำหรับการตัดเฉือนขั้นแรก เนื่องจากสามารถกลึงหยาบในทิศทางต่างๆ ได้ดีด้วยมุมเข้างาน 45 องศา เม็ดมีดทรงสี่เหลี่ยมขนมเปียกปูน (ทรง C) มีความยืดหยุ่นในแง่ของทางเดินเครื่องมือ และหากเป็นเม็ดมีดรุ่น Xcel จะทำให้ยิ่งเข้าถึงบริเวณตัดเฉือน เช่น มุม บ่างาน และช่องต่างๆ ได้ง่ายยิ่งขึ้น การใช้เม็ดมีดรูปทรงนี้รวมกับมุมเข้างาน 45 องศาสามารถลดแรงตัดแนวรัศมี ให้เศษที่มีความหนาสม่ำเสมอ และลดการสึกหรอแบบรอยบาก ส่งผลให้ประสิทธิภาพการทำงานสูงขึ้น อายุการใช้งานนานขึ้น และให้ความเชื่อถือได้สูงขึ้น
การโปรแกรมเครื่องมืออย่างมีประสิทธิภาพ …
… มีความสำคัญ โดยคำแนะนำต่อไปนี้จะช่วยเพิ่มประสิทธิภาพการทำงานให้สูงยิ่งขึ้น โดยเฉพาะกับการใช้เม็ดมีดทรงกลม ซึ่งเหมาะสำหรับการทำงานกับวัสดุพิเศษ:
- หลีกเลี่ยงการจ่วงตัดและพยายามลดการกระแทก แต่ถ้าหากหลีกเลี่ยงไม่ได้ ให้ลดอัตราป้อนงานลงครึ่งหนึ่ง
- สำหรับการกลึงบ่างาน ควรลดอัตราป้อนงานลงครึ่งหนึ่งหรือควรเดินเครื่องมือเป็นแนวโค้ง (Roll) เข้าไปยังบ่างาน โดยใช้รัศมีโปรแกรมเท่ากับเส้นผ่านศูนย์กลางเม็ดมีด (แนะนำให้ใช้รัศมีโปรแกรมขั้นต่ำประมาณ 25% ของเส้นผ่านศูนย์กลางเม็ดมีด และรัศมีชิ้นงาน 75% ของเส้นผ่านศูนย์กลางเม็ดมีด อัตราป้อนงานที่ศูนย์กลางของเครื่องมือเป็นค่าสำหรับรัศมีโปรแกรม)
- สำหรับการกลึงหยาบด้วยเม็ดมีดทรงกลม ให้ใช้รัศมีโปรแกรมเท่ากับเส้นผ่านศูนย์กลางเม็ดมีด และสำหรับการเก็บผิวละเอียด ให้ใช้รัศมีโปรแกรมใหญ่กว่าเส้นผ่านศูนย์กลางเม็ดมีด
- ควรพิจารณาทางเดินเครื่องมือแบบอื่นๆ การกลึงหลายรอบ และการกลึงสองทิศทาง เพื่อให้สามารถใช้งานเม็ดมีดได้เต็มศักยภาพ
- ป้องกันความเสียหายของเม็ดมีดเซรามิก โดยการลบมุมที่ชิ้นงานก่อน จากนั้น จึงป้อนเครื่องมือที่บริเวณที่ลบมุมไว้
- รักษาสมดุลของมุมเข้างานกับอาร์กของหน้าสัมผัสเม็ดมีดให้อยู่ในระดับที่เหมาะสมตลอดการตัดเฉือน การจำกัดมุมเข้างานเป็นสิ่งสำคัญต่อประสิทธิภาพ และการใช้เม็ดมีดทรงกลมเป็นสิ่งสำคัญที่จะช่วยให้ใช้งานเกรดเม็ดมีดสมัยใหม่ได้อย่างเต็มศักยภาพ
- ป้องกันอย่าให้เศษพันรอบเครื่องมือขณะกลึงขึ้นรูปหรือกลึงแนวดิ่ง เพื่อป้องกันไม่ให้เกิดแรงกระทำมากเกินไปที่เม็ดมีด โดยควรเลือกทางเดินเครื่องมือแบบอื่นหรือใช้เม็ดมีดที่มีเส้นผ่านศูนย์กลางเล็กลงในกรณีนี้
- พิจารณาใช้การกลึงแบบโทรคอยด (Trochoidal Turning) เพื่อช่วยให้การหักเศษเป็นชิ้นเล็กๆ โดยเฉพาะสำหรับการกลึงหลุม
ประเด็นหลักที่ต้องพิจารณาในส่วนของประเภทเครื่องมือและวิธีการที่ใช้ในการตัดเฉือนวัสดุ HRSA และไทเทเนียม มีดังต่อไปนี้:
- ควรพิจารณาใช้น้ำหล่อเย็นความเที่ยงตรงสูงเสมอ การจ่ายเจ็ทน้ำหล่อเย็นความเที่ยงตรงสูงไปยังด้านหลังและที่คมตัดผ่านทางช่องจ่ายน้ำหล่อเย็นภายใน มีข้อดีหลายอย่างที่จะช่วยเพิ่มประสิทธิภาพให้กับการกลึง การกัด และการเจาะ หัวฉีดน้ำหล่อเย็นที่ใช้เทคโนโลยีล่าสุดมีทั้งรุ่นมาตรฐานและรุ่นสั่งทำพิเศษสำหรับระดับแรงดันต่างๆ รวมทั้งสามารถนำมาติดตั้งได้กับเครื่องจักรทุกประเภทที่มีระบบจ่ายน้ำหล่อเย็นที่มีแรงดันเพียงพอ ในกรณีที่ต้องการลงทุนซื้อเครื่องจักรใหม่ ควรเลือกเครื่องจักรที่สามารถจ่ายแรงดันน้ำหล่อเย็นได้ 70 บาร์เพื่อช่วยในการหักเศษสำหรับการกลึงไทเทเนียม ในขณะที่เครื่องจักรที่สามารถจ่ายแรงดันได้สูงสุด 200 บาร์จะเหมาะสำหรับการกลึงวัสดุ HRSA เนื่องจากเศษจะแข็งกว่า
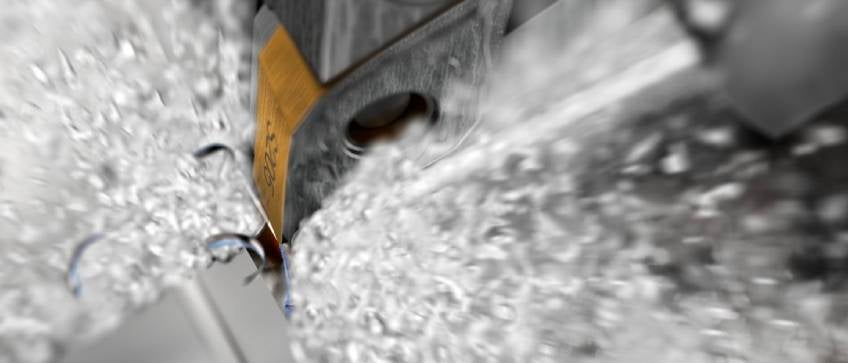
การใช้น้ำหล่อเย็นมีความสำคัญอย่างมากสำหรับการตัดเฉือนวัสดุพิเศษ ระบบน้ำหล่อเย็นความเที่ยงตรงสูงในปัจจุบัน ทั้งรุ่นมาตรฐานและรุ่นสั่งทำ สามารถสร้างความแตกต่างให้กับการตัด การหักเศษ อายุการใช้งานของเครื่องมือ และประสิทธิภาพการทำงาน โดยทั่วไปแล้ว การตัดเฉือนวัสดุกลุ่มนี้จะทำให้เกิดความร้อนสูงและจำเป็นต้องมีการระบายความร้อนออก ซึ่งเมื่อมีการใช้น้ำหล่อเย็นในปริมาณมากพอ รวมทั้งมีการจ่ายไปยังจุดที่ต้องการด้วยแรงดันสูงและความเที่ยงตรงสูง รวมกับการเลือกใช้เม็ดมีดเฉพาะทางและช่องจ่ายน้ำหล่อเย็นภายในตัวเครื่องมือ จะทำให้งานมีประสิทธิภาพและคุณภาพมากขึ้น
- การเข้าถึงบริเวณตัดเฉือนเป็นปัญหาที่พบได้บ่อยกับการกลึงวัสดุพิเศษ เนื่องจากรูปทรงชิ้นงานมักจะมีความซับซ้อนและต้องใช้เครื่องมือที่มีระยะยื่นยาว จึงทำให้การเลือกเครื่องมือและวิธีการตัดเฉือนที่ถูกต้องเหมาะสมเป็นปัจจัยที่สำคัญมาก ในจุดนี้ อาจลองพิจารณาเลือกใช้ระบบเครื่องมือแบบถอดเปลี่ยนชิ้นส่วนได้ ซึ่งมีแผ่นเบลดสำหรับติดตั้งคมตัดท่องศาต่างๆ รวมทั้งมีระยะยื่นให้เลือกหลายขนาด ตัวต่อและแผ่นเบลดรุ่นต่างๆ ช่วยเพิ่มความอเนกประสงค์ โดยสามารถประกอบเครื่องมือได้ตรงตามความต้องการจากเครื่องมือมาตรฐานไม่กี่ชิ้น รวมทั้งยังมีประสิทธิภาพในการตัดเฉือนจุดที่มีพื้นที่จำกัด ทั้งสำหรับการกลึงนอกและใน ทั้งนี้ควรเลือกแผ่นเบลดที่มีระยะหลบแนวรัศมีและแนวแกนตรงตามที่ต้องการ เพื่อให้สามารถเข้าตัดเฉือนในร่องเอียงได้ พร้อมทั้งสามารถจ่ายน้ำหล่อเย็นความเที่ยงตรงสูงผ่านช่องจ่ายภายในเครื่องมือไปยังคมตัดได้อย่างแม่นยำ
- วัสดุทำเครื่องมือถือเป็นหัวใจของงานตัดเฉือนทุกประเภท และยิ่งสำคัญมากขึ้นอีกสำหรับการตัดเฉือนวัสดุพิเศษ ซึ่งจำเป็นต้องใช้เกรดเม็ดมีดเฉพาะทางรวมกับรูปทรงเม็ดมีดที่เหมาะสม โดยในปัจจุบันมักจะเป็นการใช้เม็ดมีดคาร์ไบด์และเม็ดมีดเซรามิกรุ่นล่าสุด เม็ดมีดคาร์ไบด์ไม่เคลือบผิวยังคงมีบทบาทสำคัญในปัจจุบัน แต่ความก้าวหน้าล่าสุดของเทคโนโลยีเคลือบผิวเม็ดมีดทำให้เรามีเม็ดมีดคาร์ไบด์เคลือบผิวแบบพิเศษ ซึ่งสามารถยกระดับประสิทธิภาพของคมตัดได้อีกขึ้น โดยช่วยให้ระยะเวลาตัดเฉือนสั้นลง พร้อมทั้งยืดอายุการใช้งานของเครื่องมือ
- การเลือกใช้ดามกลึงคว้าน แผ่นเบลด หรือแม้แต่หัวกัดที่มีระบบลดแรงสั่นสะเทือนในตัวถือว่ามีความสำคัญมาก เพื่อช่วยลดการสั่นสะเทือนให้เหลือน้อยที่สุด เทคโนโลยีลดการสั่นสะเทือนมีความก้าวหน้าอย่างมากในปัจจุบัน และกำลังกลายมาเป็นมาตรฐานสำหรับงานที่ต้องการระยะยื่นยาวจนทำให้เครื่องมือไม่นิ่ง คุ ณภาพและตัวเลือกของระบบเครื่องมือลดแรงสั่นสะเทือนที่ใช้จะส่งผลโดยตรงต่อประสิทธิภาพการผลิต ความเชื่อถือได้ และคุณภาพของชิ้นงาน โดยมีงานจำนวนมากที่ไม่สามารถทำได้หากปราศจากเทคโนโลยีนี้ ระบบลดแรงสั่นสะเทือนในปัจจุบันช่วยให้สามารถทำการกลึงในด้วยระยะยื่นถึง 14 เท่าของเส้นผ่านศูนย์กลางหรือ 250 มม. ได้อย่างมีประสิทธิภาพ พร้อมทั้งยังให้คุณภาพผิวงานระดับสูง