Een groenere toekomst voor lucht- en ruimtevaart
OEM 's moeten kiezen voor een holistische benadering ten aanzien van de vliegtuigen van de toekomst.
Als één van de grootste bijdragers aan de wereldwijde CO2 emissies, staat de lucht- en ruimtevaartsector onder grote druk om groenere vliegtuigen te leveren die lichter zijn en langere afstanden kunnen afleggen. Echter om dit te bereiken moet er met moeilijk te bewerken aluminium en hittebestendige superlegeringen (HRSA's) worden gewerkt. Hier legt Sébastien Jaeger, Industry Solution Manager – Lucht- en ruimtevaart voor Sandvik Coromant uit hoe lucht- en ruimtevaart OEM's geavanceerde gereedschapsoplossingen kunnen toepassen voor het duurzaam bewerken van deze lastige componenten.
Volgens het World Economic Forum (WEF), “Zal het bereiken van netto nul CO2 emissies in 2050 niet alleen helpen een ecologisch duurzame toekomst te scheppen, maar ook zorgen voor een financieel veerkrachtige en concurrerende luchtvaarindustrie als geheel.” Hoewel elektrische mobiliteit steeds meer gevestigd raakt in de automotive sector — en in augustus 2021 zagen we dat de verkoop van elektrische voertuigen die van dieselvoertuigen inhaalde in het Verenigd Koningrijk — zal het langer duren voordat deze ontwikkelingen in de lucht- en ruimtevaart werkelijkheid worden.
Over het algemeen wordt niet verwacht dat geëlektrificeerde vliegtuigen wijdverbreid worden ingezet voor 2035. Lonely Planet rapporteert dat — hoewel easyJet hoopt om elektrische vliegtuigen te gebruiken op hun routes onder de 311 mijl (500 km) in 2030 en Noorwegen als doel heeft om alle korte vluchten elektrisch te maken in 2040 — “we binnen afzienbare tijd nog niet in oplaadbare jumbo's lange afstanden zullen vliegen: de batterijen zijn gewoonweg te zwaar. "
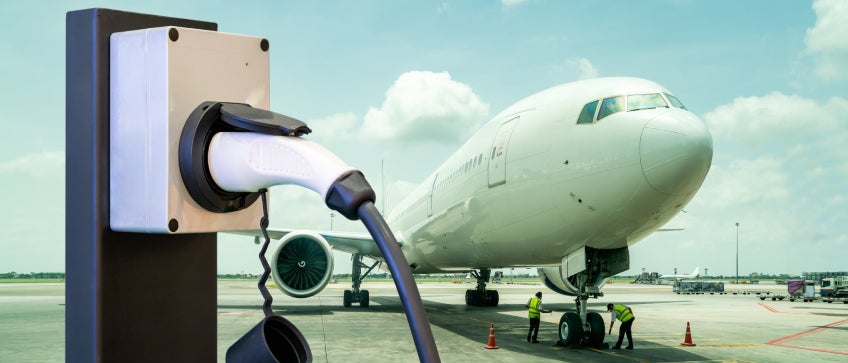
Geëlektrificeerde vliegtuigen zullen naar verwachting in 2035 wijdverbreid worden gebruikt.
Dus terwijl accu's lichter moeten worden om plausibel te zijn, rust er een toenemende plicht op de original equipment manufacturers (OEM's) om lichtere componenten te produceren om het gewichtsprobleem tegen te gaan. We kunnen er zeker van zijn dat aluminium — met name nieuwe soorten aluminium met grotere sterkte, moeheidbestendigheid en andere kenmerken gebruikt zullen worden om deze systemen lichter te maken.
We zien ook een toename van het gebruik van nieuwe hittebestendige superlegeringen (HRSA's). Feit is dat HRSA's al gebruikt worden in vliegtuigcomponenten die te maken hebben met extreme prestatievereisten omdat ze hun hardheid behouden wanneer ze te maken krijgen met intense hitte. Deze materiaaleigenschappen zullen essentieel blijken te zijn, omdat één benadering van duurzamere vliegreizen het harder en heter laten branden van motoren zal zijn.
Componenten moeten ook worden geproduceerd volgens nauwere toleranties en in meer uiteenlopende ontwerpen. Net als bij elektrische auto's zullen de elektrische vliegtuigontwerpen van de toekomst — waaronder de rompen en de motoren — meer variëren van fabrikant tot fabrikant dan bestaande vliegtuigen met inwendige verbrandingsmotoren. Voor de rompvorm kijken sommige OEM's naar de deltavorm, een mengvorm van vleugelromp en met stut verstevigde vleugelconcepten. Andere OEM's blijven trouw aan de traditionele "grote buis, vleugels en motoren" ontwerpen.
Er zullen ook vele vormen van motorarchitectuur zijn, zoals geëlektrificeerd, accu-aangedreven of elektromagnetisch, of hybride motoren waarbij de huidige motoren worden ondersteund door elektromotoren. OEM's zullen ook gevraagd worden om een toenemende variëteit aan producten met nauwe toleranties te produceren, terwijl ook nieuwe manieren worden gevonden voor het reduceren van geluid, gewicht en emissies — alle factoren die invloed hebben op hoe elektrische systemen presteren. Maar aluminium en HRSA-onderdelen zijn moeilijk om te bewerken, dus zal het een hele uitdaging zijn om dit duurzaam en kosteneffectief te realiseren.
Snelle vooruitgang
Eén pad dat leidt naar het produceren van lichtere en zuinigere vliegtuigen is door middel Additive Manufacturing (AM) technieken. AM maakt de ontwikkeling mogelijk van zeer complex gevormde maatwerkdelen en functionele producten met nauwe toleranties, zodat moeilijk te bewerken componenten zoals roosters gemakkelijker bewerkt kunnen worden. Volgens bevindingen van het softwarebedrijf Dassault Systemes, “kan in de lucht- en ruimtevaartsector, een gewichtsreductie dankzij AM-processen resulteren in een energiebesparing van tot wel 25%, terwijl “elke kilogram (2.2 lbs) van gewichtsverlies op een vlucht tot wel US$ 3000 aan brandstof per jaar kan besparen.”
Maar is AM-productie op zichzelf duurzaam? Een studie, mede geschreven door de afdeling machinebouw van de technische universiteit van Cluj-Napoca in Roemenië, beschrijft AM als “een geweldig alternatief voor Traditional Manufacturing (TM) methoden zoals spuitgieten, gieten, of bewerken.” De studie vervolgt: “AM heeft het potentieel om kosten te verlagen en om energiezuiniger te zijn dan conventionele processen.”
AM zal ook een cruciaal effect hebben op de manier en diversiteit waarop producten geproduceerd zullen worden. Voordelen kunnen onder andere minder CO2 uitstoot zijn, minder materiaalgebruik en minder transport omdat componenten in huis gemaakt kunnen worden in plaats ze te importeren.
Fabrikanten kunnen ook complexere, compactere en innovatievere lucht- en ruimtevaartcomponenten produceren middels "rapid prototyping". Rapid prototyping refereert naar verschillende technieken, maar het doel is om snel een tastbaar 3D-prototype te produceren op basis van een computer aided design (CAD) bestand. Met deze prototypen kunnen testen met kleine aantallen van nieuwe materialen worden uitgevoerd vóór de full-scale productie, om te waarborgen dat componenten zijn gemaakt met de ultieme innovatie, kwaliteit en precisie.
Wij hebben gekeken naar de wijze waarop lucht- en ruimtevaart OEM 's nieuwe methoden kunnen adopteren voor het produceren van complexere componenten. Maar hoe zit het dan met het beschikken over de juiste gereedschappen voor de taak — met name bij het bewerken van taai aluminium en HRSA's?
Deze materialen vereisen het gebruik van gereedschappen met een hogere slijtvastheid en langere standtijd. Daarom ontwikkelde Sandvik Coromant de hardmetaalsoort S205 voor wisselplaten die worden gebruikt bij het draaien van staal. De metallurgie van S205 omvat een Inveio® laag van dicht op elkaar gepakte, in één richting uitgelijnde kristallen. Dit creëert een sterke beschermende barrière rond de wisselplaat voor het versterken van het gereedschap en het verbeteren van zijn mechanische eigenschappen. De wisselplaat heeft zijn nut al bewezen bij de productie van een reeks van vliegtuigonderdelen waaronder motor turbineschijven, ringen en assen. Sandvik Coromant 's klanten hebben al 30 tot 50% hogere snijsnelheden gemeld met S205 vergeleken met concurrerende soorten voor het draaien in HRSA.
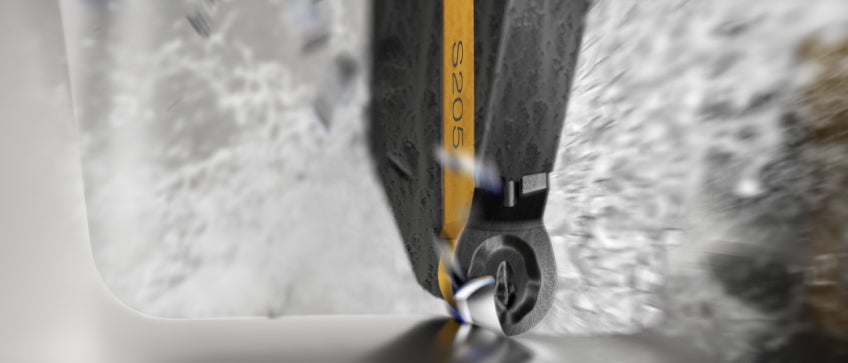
Holistische benadering
We hebben gekeken naar productieprocessen en gereedschappen, maar hoe kunnen we die twee het beste combineren? Er kan immers tijd worden verspild bij het samenstellen van een volledig geïntegreerde oplossing wanneer de systemen niet zijn ontworpen om goed met elkaar samen te werken.
Daarvoor ondersteunt Sandvik Coromant haar klanten in de lucht- en ruimtevaart met wat we een componentenoplossing noemen. De oplossing kent verschillende stadia, waarbij er wordt gekeken naar de machinevereisten en naar tijdstudies om de kosten per component te onderzoeken. Maar ook het analyseren van de productiemethoden bij de run-off, zowel gerelateerd aan Methods-Time Measurement (MTM) als aan eindgebruikersprocessen. De componentenoplossing omvat ook computer-aided manufacturing (CAM) programmering en projectmanagement van lokale of grensoverschrijdende projecten.
Voor een Sandvik Coromant klant die last had van spaanbrekingsproblemen bij zijn productie, stelde de componentenoplossing ons in staat de oorzaak te vinden en een oplossing te bedenken. Voor de klant ontwikkelden Sandvik Coromant 's specialisten een nieuwe strategie met dynamische aandrijvingscurven welke ons in staat stelden de spaanbreking op elk moment te beheersen. We noemden deze nieuwe benadering “trochoïdaal draaien” en we hebben er nu een patent op. Met trochoïdaal draaien realiseerde de klant een afname van de cyclustijd van 80% met een geweldige spaanbeheersing en een verdubbeling van de standtijd.
Daarnaast was de klant in staat het gebruik van vier machines te reduceren tot één machine, door het reduceren van de noodzaak voor multitasking, met veiligere bewerkingsprocessen en "groen licht" productie. Minder machinegebruik en de mogelijkheid om productieruns af te ronden met minder gereedschapswisselingen, dankzij robuustere bewerkingssoorten zoals S205, zal essentieel zijn voor de productie van duurzamere vliegtuigen.
Software zal ook een doorslaggevende rol spelen, zoals de CoroPlus® Tool Guide welke onderdeel uit maakt van Sandvik Coromant’s digitale portfolio. Klanten kunnen cruciale beslissingen nemen omtrent de keuze van het gereedschap en de snijparameters, zelfs nog voordat ze met de productie zijn begonnen.
Sluit het circulaire systeem
Behalve nieuwe benaderingen voor gereedschappen en productie, kunnen lucht- en ruimtevaart OEM's zich ook wenden tot productie. Volgens een rapport van de Air Transport Action Group (ATAG), gebruikt Kaiser, dat het bedrijf is dat aluminium levert aan Boeing, nu een closed-loop recycling systeem — één van de grootste programma's in zijn soort in de industrie. Kaiser schat dat door het programma elk jaar circa tien miljoen aan verspaningsafval en afkeurmetaal wordt hergebruikt door de sector.
Bij Sandvik Coromant, hebben we ons eigen circulaire systeem geïnitieerd voor het recyclen van hardmetalen gereedschappen waarbij we de versleten hardmetalen gereedschappen van de klant terugkopen en deze hergebruiken om gloednieuwe exemplaren te maken. Het resultaat is dat de meeste van de grondstoffen die worden gebruikt in Sandvik Coromant’s gecementeerde hardmetalen gereedschappen afkomstig is van afval. Wij doen aan een duurzame bedrijfsvoering in een omgeving van beperkte bronnen en minimaliseren overmatig afval. Door dit te doen zijn we er achter gekomen dat het maken van gereedschappen op basis van gerecycled materiaal 70% minder energie vraagt, terwijl 40% minder koolstofdioxide wordt uitgestoten.
Er is sprake van een toenemende druk op de lucht- en ruimtevaartsector om groenere vliegtuigen te produceren die lichter zijn en langere afstanden kunnen afleggen. Echter met de juiste processen en gereedschappen, om nog maar te zwijgen over een meer holistische benadering van de productie, kunnen OEM's in de lucht- en ruimtevaart hun steentje bijdragen om een groenere toekomst voor de lucht- en ruimtevaart tot stand te brengen.