Alumiinin koneistuksen optimointi autoteollisuudessa
Autoteollisuuden sektorilla käytetään yhä enemmän alumiinista valmistettuja moottorien, käyttövoimalaitteiden, vesipumppujen ja jarrujärjestelmien osia, joten alkuperäisvalmistajien ja niiden toimitusketjukumppanien haasteena on jyrsinnän kehittäminen tuottavammaksi. Oikeanlaisten työkalujen valitseminen on keskeisen tärkeää tämän segmentin markkinoilla erottumisessa, sillä optimoitujen jyrsimien oikeanlainen käyttö kaikessa moottorikomponenttien koneistuksessa voi tuottaa merkittäviä tuloksia.
Alumiinimoottoreita tuotetaan vuosi vuodelta enemmän sekä perinteisiin että hybridimallisiin henkilöautoihin. Niitä valmistetaankin tällä hetkellä vuosittain liki 100 miljoonaa kappaletta. Tällaisissa moottoreissa on usein muodoltaan monimutkaisia osia, joille on tehtävä valamisen jälkeen useita erilaisia mutta keskeisen tärkeintä jyrsintätoimintoja.
Sandvik Coromantilla on nyt tarjolla kattava valikoima autoteollisuuden alumiiniosien koneistukseen, kuten ensimmäisen vaiheen kuutiointiin, rouhintaan, väliviimeistelyyn ja viimeistelyyn. Tähän tarkoitukseen erityisesti kehitettyjä jyrsintyökaluja on yhteensä viisi, ja niistä jokainen on suunniteltu laadun ja osakustannusten optimointiin. Kustannusten optimoinnissa auttaa se, että valikoiman tietyt työkalut soveltuvat useisiin eri tehtäviin, kuten vaikkapa sekä rouhintaan että viimeistelyyn yhdellä käsittelykerralla työkierron aikojen nopeuttamiseksi.
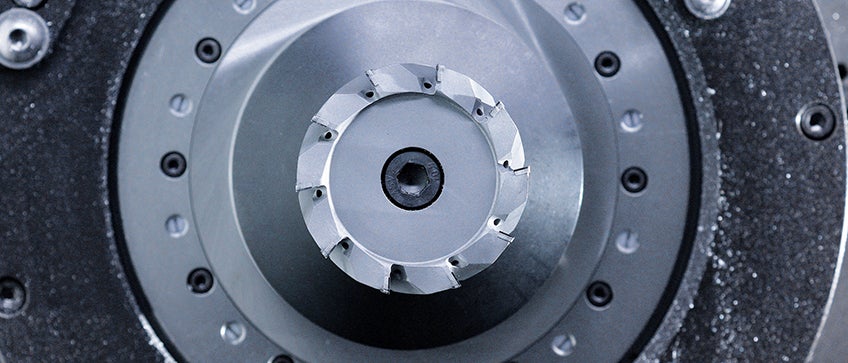
Otamme nyt esimerkiksi uraauurtavan M5C90-jyrsimen, jonka ansiosta rouhinta ja väliviimeistely onnistuvat yhdellä työkalulla. M5C90 on huippunopea tasojyrsintätyökalu, joka on suunniteltu erityisesti aikaa vievien asetusaikojen nopeuttamiseen asiakkaan tiloissa. M5C90:ssä on vähemmän hampaita kuin perinteisissä jyrsimissä johtuen pääasiassa sen viimeistelyrivin/sisähalkaisijan ainutlaatuisesta radiaalisesta ja aksiaalisesta teräpaikoituksesta (terää ei tarvitse säätää). Tämä paikoitus takaa jäysteettömän jyrsinnän ja optimaalisen pintalaadun sylinterikansissa, sylinterilohkoissa, jarrujärjestelmän osissa ja kaikissa alumiinityökappaleissa, joissa voidaan saavuttaa leveä jyrsimen kosketuspituus (ei käytettävissä ohutseinäisiin osiin).
M5C90:n käyttämisen mahdollisista hyödyistä hyvä esimerkki on parhaillaan käynnissä oleva asiakastapauskokeilu, jossa on mukana AlSi12Cu1-materiaalista valmistettu jarrujärjestelmän runkoventtiili. Työkalun ulkohalkaisijalla on kymmenen kovametalliterää ja sisähalkaisijalla neljä terää sekä yksi wiper-terä. Näin työkalun karanopeus voi olla 8 000 kierr./min, lastuamisnopeus 4 021 m/min (13 192 jalkaa/min) ja syöttö 0,25 mm/hammas (0,009 tuumaa/hammas). Lisäksi aksiaalinen lastuamissyvyys on 2 mm (0,078 tuumaa) ja radiaalinen lastuamissyvyys on 140 mm (5,51 tuumaa), jolloin metallilastuvirraksi voidaan saada 5 600 cm3/min (342 in3/min). Vaikka työkalujen kokonaiskestoikää ei ole vielä määritetty, sama työkalu on edelleen koneessa 18 käyttökuukauden jälkeen.
Jos käsittelyyn kaivataan jyrsintä, jolla voidaan viimeistellä myös ohutseinäisiä alumiiniosia, kuten vaihdelaatikon suojuksia ja koteloita, Sandvik Coromantilla on tarjolla toinen yhtä tehokas jyrsin: M5F90. Rouhinta ja viimeistely onnistuvat yhdellä käsittelykerralla myös M5F90-työkalulla. Erityisesti ohutseinäisten alumiiniosien koneistukseen ja pistesuuntaustoimintoihin kehitetyssä jyrsinrungossa (25–80 mm:n, 0,98–3,15 tuuman halkaisija) on juotetut PCD-kärjet. Jokaisessa kärjessä on sekä rouhinta- että viimeistelysärmä. Rouhinta-alue toimii perinteisenä jyrsintätyökaluna, jossa kaikilla teräsärmillä on sama halkaisija ja sama korkeus. Viimeistelyalue taas koostuu radiaalisista ja aksiaalisista porrastetuista teräsärmistä. Tiheän teräjaon ansiosta koneistus onnistuu ilman jäysteitä ja pintalaadusta tulee erinomainen.
Aikaa voidaan säästää merkittävästi, kuten havaittiin myös asiakastapauksessa, jossa kokeiltiin alumiinista (korkea piipitoisuus) valmistetun sylinterikannen tasojyrsintää. M5F90-ratkaisua käyttämällä työkierron aika nopeutui 150 prosenttia kilpailijan valmistamaan PCD-erikoisjyrsimeen verrattuna ja jäysteiden muodostuminen saatiin karsittua kokonaan. Ratkaisun lastuamisarvot: karanopeus 15 915 kierr./min lastuamisnopeus 2 000 m/min (6 562 ft/min) syöttö 0,16 mm/hammas (0,006 tuumaa/hammas) ja leikkuusyvyys 1,5 mm (0,06 tuumaa).
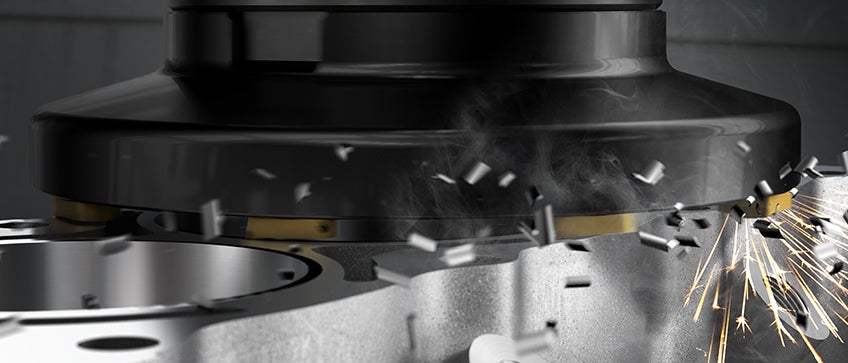
Toisessa M5F90-esimerkissä alumiiniketjun työkierron ajat nopeutuivat 44 prosenttia verrattuna kilpailijan halkaisijaltaan 63 mm:n (2,48 tuuman) kääntöteräiseen jyrsimeen, jossa oli kuusi PCD-terää. Ja mikä parasta, ratkaisun avulla pystyttiin karsimaan aiemmin tarvittu harjalla tehtävä jäysteenpoistaminen.
Toinen uusi erikoistyökalu on M610. Sillä voidaan jyrsiä moottorisylinterikansien pintoja/yläosia, joissa on kaksoismetallisia, yleensä alumiinista ja harmaasta valuraudasta (CGI) koostuvia kiinnityskohtia.
Kaksoismetallimateriaalien koneistuksesta haastavaa tekevät monet erilaiset mekaaniset ja lämpöominaisuudet. Olemassa olevat tähän käyttötarkoitukseen suunnitellut jyrsimet ovat monimutkaisia ja edellyttävät säätämistä, mikä heikentää tuottavuutta. Lisäksi tällaiset työkalut aiheuttavat usein työkappaleen GCI-osien pirstoutumista.
M610-ratkaisua ei puolestaan tarvitse asettaa eikä säätää, ja sillä voidaan saada parhaimmillaan aikaan suuria syöttönopeuksia ilman osien pirstoutumista, jäysteitä tai naarmuja. Tämä ominaisuus on tärkeä, sillä pintaan jäävät viat voivat aiheuttaa sylinterilohkon ja -kannen välisiä vuotoja, mikä voi vaarantaa tehon ja suorituskyvyn. Jotkin globaalit autoteollisuuden alkuperäisvalmistajat ovat jo saavuttaneet merkittäviä hyötyjä ottamalla M610:n käyttöön.
Eräs asiakas on saanut valtavaa kilpailuetua kaksoismetallisten moottorilohkojen polttopinnan viimeistelyssä. Kilpailijan säädettävään teräelementtijyrsimeen verrattuna työkalujen kestoikää saatiin pidennettyä M610-ratkaisulla 833 prosenttia. Lisäksi sillä saatiin käsiteltyä yli 4 000 osaa, kun taas kilpailijan terällä niitä saatiin käsiteltyä vain 480. Myös M610:n nopeus oli kymmenen kertaa suurempi. 15-teräisen M610:n lastuamisarvot: lastuamisnopeus 3 000 m/min (9 843 ft/min) syöttönopeus 5 720 mm/min (225 tuumaa/min) karanopeus 3 820 kierr./min syöttö 0,15 mm/hammas (0,006 tuumaa/hammas) ja alumiinin lastuamissyvyys 0,5 mm (0,02 tuumaa) ja valuraudassa 0,05 mm (0,002 tuumaa).
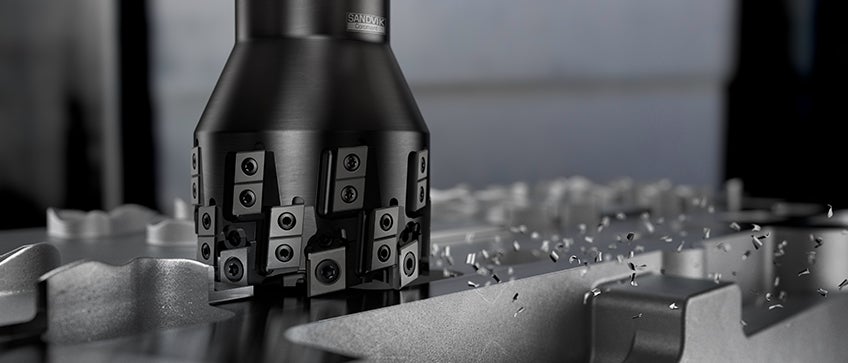
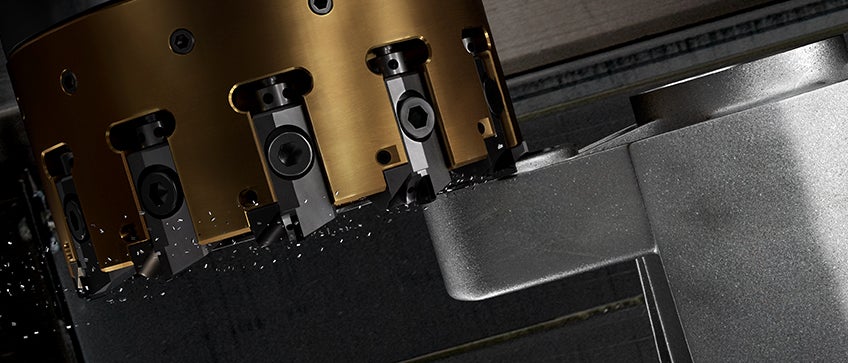
Tuoteperheeseen kuuluu myös tangentiaalinen M5Q90-rouhintajyrsin, joka soveltuu ensimmäisen vaiheen kuutiointiin (pintojen ensimmäinen koneistus valamisen jälkeen) yhdellä käsittelykerralla ilman jäysteitä. Työkalun PCD-tangentiaaliterät takaavat tasaisen ja vakaan lastuamisen virrankulutuksen vähentämiseksi ja värinän estämiseksi.
M5Q90-ratkaisusta voi olla hyötyä muun muassa alumiinisten sylinterikansien ja -lohkojen käsittelyssä. Esimerkiksi valetun sylinterikannen kuutiointi sisältäisi yleensä nokka-akselin pinnan, tulo-/lähtöpinnan ja polttopinnan koneistuksen. Kun AS-9-alumiiniseoksesta valetut sylinterikannet rouhinta-tasojyrsittiin vaakatasossa olevassa koneistuskeskuksessa erääseen asiakkaaseen liittyvässä tapaustutkimuksessa, työkalujen kestoiässä saavutettiin erittäin vaikuttavia tuloksia. Työkappaleita saatiin tuotettua yli 10 000 kappaletta, kun lastuamisnopeus oli 3 000 m/min (9 843 tuumaa/min), hammassyöttö oli 0,2 mm (0,008 tuumaa) ja aksiaalinen lastuamissyvyys oli 2,0 mm (0,079 tuumaa) 40 mm:n eli 1,57 tuuman täydellä kosketuksella.
Tarjolla on myös toisen vaiheen rouhintaan ja väliviimeistelyyn tarkoitettu M5R90. Tämä vakiojyrsin on yhteensopiva säädettävien teräelementtien kanssa, ja sen avulla voidaan saavuttaa jopa 8 mm:n (0,315 tuuman) lastuamissyvyys 0,4 tai 0,8 mm:n (0,016 tai 0,031 tuumaa) säteellä riippuen käytössä olevasta teräelementistä. Helposti säädettävistä teräelementeistä on hyötyä monissa autoteollisuuden käyttökohteissa, kuten totesimme äskettäisessä asiakaskokeilussa, jossa keskityttiin moottorinsuojuksen tasojyrsintään. MRHB Si12 ‑alumiiniseoksesta valetulla M5R90-ratkaisulla saatiin aikaan äärimmäisen myönteisiä tuloksia vastaavaan kilpailijan jyrsimeen verrattuna. M5R90 pidensi työkalujen kestoikää samojen lastuamisarvojen pohjalta kahdeksasta kymmeneen tuhanteen työkappaleeseen. Lisäksi kilpailijan jyrsintä piti säätää aina tuhannen osan jälkeen, koska sen liikkuva teräelementti heikensi pintalaatua. M5R90-ratkaisulla voitiin puolestaan tuottaa 8 000 osaa ennen kuin teräelementtiä piti säätää lainkaan.
Tuoteperheeseen sisältyy myös superviimeistelyyn tarkoitettu M5B90-tasojyrsin, jossa on ainutlaatuinen aksiaalinen ja radiaalinen terien paikoitus. Tämä kokoonpano ja wiper-terä varmistavat jäysteettömän lastuamisen ja erinomaisen pintalaadun, kuten eräs henkilöautojen sylinterikansien valmistaja havaitsi hiljattain. Yrityksellä oli prosessin epävakauteen ja jäysteisiin liittyviä ongelmia, ja haittaa aiheutti myös epäsäännöllinen terien kestoikä, joka riippui asetuksesta toiseen vaihtuvista teräelementtien säädöistä. Kun prosessissa siirryttiin käyttämään M5B90-jyrsintä, viimeistelystä tuli sujuvampaa ja kulumisesta ennakoitavampaa ja jäysteet katosivat kokonaan. Työkalu tuottaa vain erittäin ohuita lastuja, jotka on helppo poistaa lastuamisprosessin aikana työkappaleen pintaan tulevien vaurioiden estämiseksi. Lisäksi M5B90 pidensi työkalujen kestoikää keskimäärin 30 000–45 000 osaan.
Asiakkaille voidaan tarjota myös CoroDrill®- ja CoroTap®-tuoteperheen poraus- ja kierteitystyökaluja osana samaa ratkaisuperhettä, joka on suunniteltu autoteollisuuden alumiiniosien koneistukseen. Valikoimaan sisältyy myös viimeistelyyn tarkoitettu CoroMill® Century 590 ‑tasojyrsin.
Kaikissa tapauksissa tarjolla on merkittävä mahdollisuus nopeuttaa työkierron aikoja, pienentää osakustannuksia, pidentää työkalujen kestoikää ja parantaa laatua, kuten on huomattavissa mainituissa asiakasesimerkeissä. Autoteollisuuden työkappaleita tuotetaan pääasiassa suurissa erissä, joten pienimmälläkin työkierron nopeuttamisella voidaan parantaa toiminnan taloudellista kannattavuutta. Siksi kaikki tekniikat, joilla voidaan saavuttaa todistetusti suurempia hyötyjä, ovat tutustumisen arvoisia.