Verktygsväg och spånbildning vid fräsning
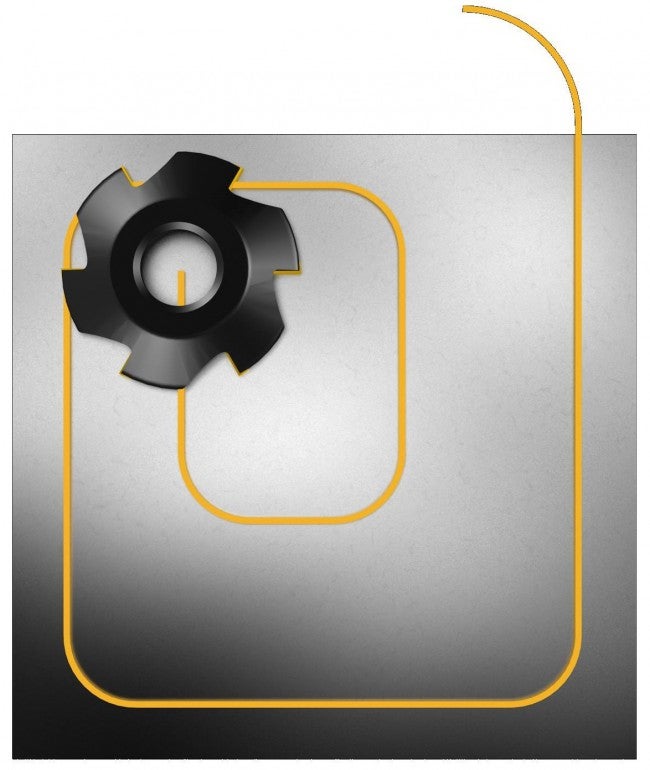
Korrekt verktygsväg och spånbildning är viktiga faktorer för att uppnå en säker skäregg och bättre verktygslivslängd vid fräsning.
Varje skäregg hos en fräs ger ett intermittent ingrepp i arbetsstycket i radiell riktning. Det finns tre faser i varje ingrepp som man bör tänka på:
1. Ingången i ingreppet
2. Ingreppsbågen i ingreppet
3. Utgången ur ingreppet
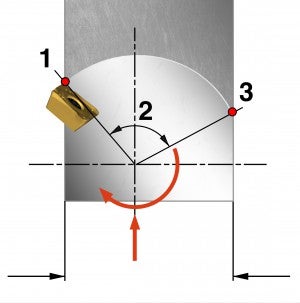
Ingång i ingrepp
Om man använder hårdmetallskär är ingången i ingreppet den minst känsliga av de tre skärfaserna. Hårdmetall hanterar tryckspänningarna vid ingången på ett bra sätt.
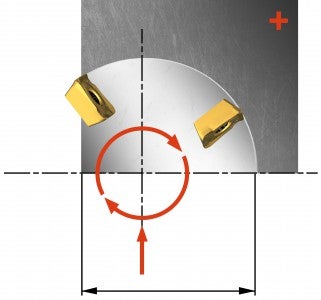
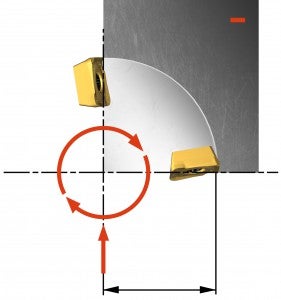
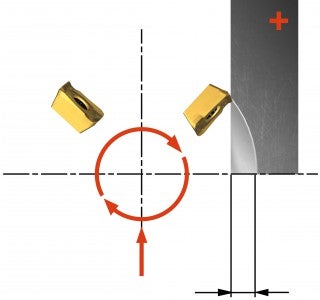
Utgång ur ingrepp
Utgången ur arbetsstycket är den känsligaste av de tre skärfaserna.
Vid fräsning bör man alltid försöka undvika bildning av tjocka spånor vid utgången. Tjock spånbildning orsakar ofta en drastisk sänkning av verktygslivslängden när man använder hårdmetallskär. Spånorna saknar stöd vid den avslutande fräsningpunkten och försöker därför böja sig, vilket skapar dragspänningar på hårdmetallen som kan orsaka skärbrott.
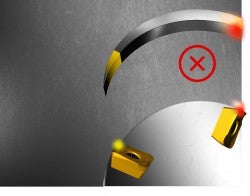
Ingreppsbågen i passeringen
- Största möjliga ingreppsbåge är 180° (ae = 100 % Dc) vid spårfräsning
- Vid finfräsning kan bågen vara mycket liten
- Kraven på sorten kan skilja sig mycket beroende på graden av radiellt ingrepp, ae/Dc
- Ju större ingreppsbåge, desto mer värme överförs till skäreggen
- Med en stor ingreppsbåge ger CVD-belagda sorter det bästa värmeskyddet
- Med en liten ingreppsbåge är spåntjockleken normalt mindre, och den skarpare eggen hos PVD-belagda sorter genererar mindre värme och lägre skärkrafter
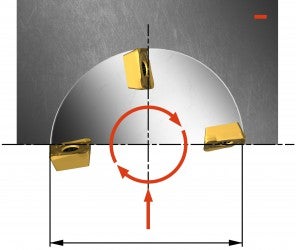
Stor (max.) ingreppsbåge
- Lång ingreppstid
- Höga radiella krafter
- Mer värme genereras
- CVD-belagda sorter
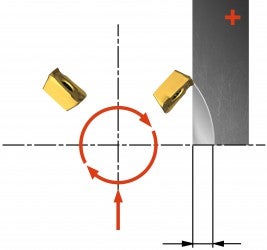
Liten ingreppsbåge
- Kort tid i ingrepp och lägre värme möjliggör högre vc
- Tunnare spånor möjliggör högre fz
- Vassa eggar
- PVD-belagda sorter
Ingång i komponenten
Om fräsen programmeras för rak ingång i arbetsstycket bildas tjocka spånor vid utgången tills fräsen är helt i ingreppet. Det kan minska verktygslivslängden dramatiskt, särskilt i hårdare stål, titan och varmhållfasta legeringar. Ur vibrationssynpunkt är det också mycket viktigt att gå in i arbetsstycket mjukt.
Det finns två sätt att öka verktygslivslängden:
1. Lägre matning
Minska matningen till 50 procent tills fräsen är helt i ingreppet.
2. Rullande ingång
Programmera en medurs inrullning in i ingreppet (moturs löser inte problemet med tjocka spånor). Genom att skäret rullar in i ingreppet är spåntjockleken vid utgången alltid noll, vilket möjliggör högre matning och längre livslängd.
Fräspositionering
Positionera fräsen förskjutet från mitten – åt vänster – för att få en tjockare spåna vid ingången och en tunn spåna vid utgången (vedfräsning). En mer konstant och gynnsam riktning av skärkrafterna uppnås, vilket minimerar vibrationstendenserna.
Om fräsen positioneras symmetriskt på centrumlinjen genereras tjocka spånor vid utgången, och större risk för vibrationstendenser uppstår.
Fräsdiametern, Dc, bör vara 20-50 % större än skärbredden, ae.
Man måste också ta hänsyn till den tillgängliga spindeleffekten, eftersom den påverkar valet av stigning.
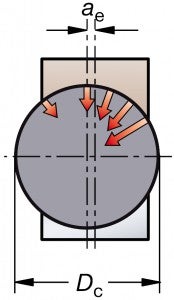
Fräsen bör vara +20–50 % större än
ae, och positionerad förskjutet från mitten.
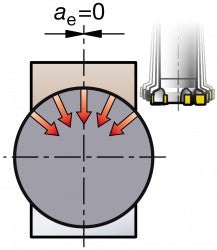
Fräsen på centrumlinje kan
generera vibrationer.
Håll fräsen i ingrepp
Skarpa riktningsförändringar i ett ingrepp genererar tjocka spånor vid utgång. Följ dessa rekommendationer för säker och optimerad fräsning:
- Håll fräsen konstant i ingreppet
- Rulla runt alla hörn
- Skärbredden ae bör vara 70 % av Dc för att säkerställa maximal täckning av hörnet
- Rulla runt utvändiga hörn vid periferifräsning
- Programmera runt avbrott och hål när det är möjligt
Arbetstips
Det finns flera faktorer att tänka på för att uppnå en optimerad uppborrningsprocess.... chevron_right
Invändig spårsvarvning
Två utmaningar vid invändig spårsvarvning är långa överhäng och dålig spånavgång.... chevron_right
Fräsning på insidan av hörn
Fräsning på insidan av hörn kräver noggrant hänsynstagande till fräsens ingreppsbåge,... chevron_right
Tips för gängsvarvning
Ett vanligt problem vid gängsvarvning är att spånorna lindar sig runt robotar, chuckar,... chevron_right