Soluciones para el mecanizado eficaz de aluminio en la industria de la automoción
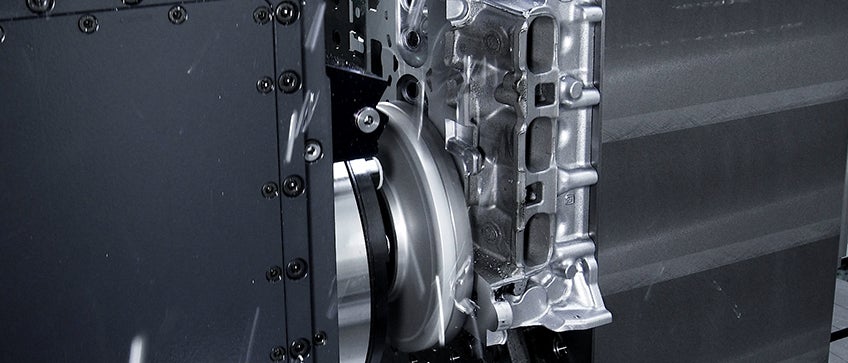
El uso de aluminio crece cada vez más en el sector de la automoción para la fabricación de piezas de motores, sistemas de propulsión, bombas de agua y sistemas de frenado. El reto de los fabricantes de equipos originales y sus proveedores colaboradores es ofrecer operaciones de fresado más productivas. Puesto que el uso correcto de fresas optimizadas en todo el espectro de operaciones de mecanizado para motores puede generar grandes beneficios, la selección de las herramientas es clave para garantizar una diferenciación de mercado clara en este segmento. Aquí lo explica Emmanuel David, director global de Productos y soluciones especiales de aluminio para la automoción de Sandvik Coromant.
La tendencia a utilizar materiales ligeros ha hecho que aumente la popularidad del aluminio en la industria de la automoción. De hecho, la cantidad de aluminio en un automóvil corriente ha pasado de 50 kg en 1990 a 151 kg en 2019. Las previsiones para 2025 apuntan a que esta cifra podría aumentar hasta los 196 kg, según European Aluminium.
Para hacer frente a la creciente demanda, Sandvik Coromant ahora dispone de una oferta completa para mecanizado de aluminio en la industria de la automoción, desde premecanizado de referencias de primera etapa hasta desbaste, semiacabado y acabado. Cada herramienta de fresado de ingeniería especial, cinco en total, ha sido diseñada para ofrecer una calidad y un coste por pieza optimizado. Para ayudar a conseguir esto último, determinadas herramientas de la gama realizan una combinación de tareas como el desbaste y el acabado en una misma operación para reducir así el tiempo de ciclo.
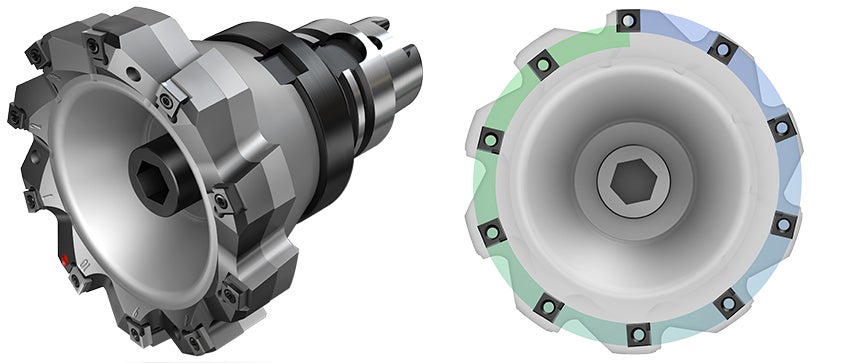
Un ejemplo es la fresa de planeado de superacabado M5B90 con su exclusivo posicionamiento axial y radial de las plaquitas. Esta configuración, junto con la plaquita wiper, garantiza un mecanizado sin rebabas con una excelente calidad superficial. Esto se debe a que el modelo viene con una fila adicional de plaquitas colocadas tangencialmente en el diámetro exterior, lo que se traduce en mayores velocidades de avance, que a su vez reducen el tiempo del proceso.
Una de las principales aplicaciones donde es crítica la M5B90 es en la fabricación de culatas para turismos. Estos componentes son importantes porque sellan la parte superior del cilindro para crear la cámara de combustión. Además, la culata también aloja el engranaje de las válvulas y las bujías.
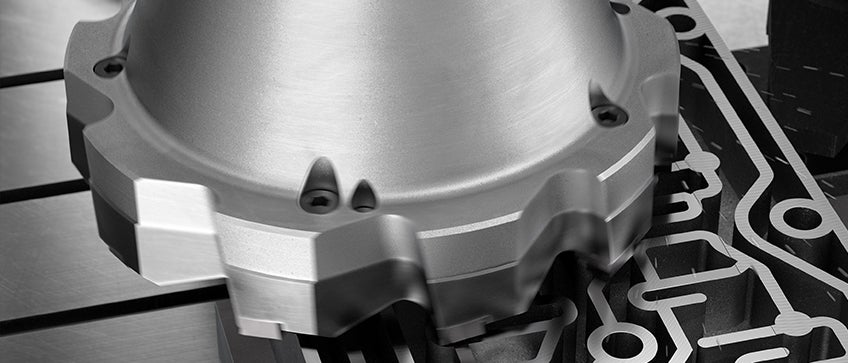
Debido a la precisión de esta operación, muchos fabricantes experimentan inestabilidad en el proceso, problemas con las rebabas y una vida útil imprevisible de las plaquitas. La mayoría de las fresas para este procedimiento requieren ajustes constantes del cartucho, que además difieren de una configuración a otra. Cambiar a la fresa M5B90 permitió una operación de acabado fluida con un desgaste predecible y sin rebabas. La herramienta produce únicamente virutas delgadas, que se eliminan fácilmente durante el proceso de corte para evitar dañar la superficie de la pieza. Además, pasar a la fresa M5B90 amplió la vida útil de 30 000 a 45 000 piezas de media.
En resumen, la posibilidad de reducir la duración de los ciclos y el coste por pieza, a la vez que mejora la vida útil y la calidad, es una realidad. En la industria de la automoción, donde predomina la producción en serie, hasta un pequeño ahorro en el tiempo de ciclo puede suponer importantes beneficios económicos. Por este motivo, es difícil ignorar cualquier tecnología que demuestre la capacidad de ofrecer mayores beneficios.