Drejning i eksotiske materialer
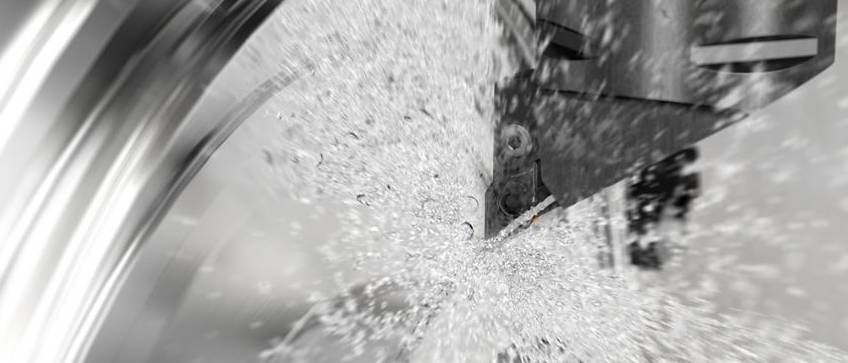
Varmebestandige superlegeringer og titanlegeringer er svære at bearbejde. De ligner ikke andre metaller, og kaldes derfor eksotiske. De har enestående egenskaber som f.eks. forholdet mellem styrke og vægt, en evne til at bevare styrke og hårdhed ved høje temperaturer og modstandsdygtighed over for korrosion.
Men da disse materialer også er vanskelige at bearbejde, så kræver de også "eksotiske" løsninger. Disse løsninger skal være veltilrettelagt med applikationstilpassede værktøjer og nøje udvalgte metoder og værktøjsbaner for at sikre effektivitet, sikkerhed og gode resultater.
Denne oversigt ser nærmere på bearbejdningskrav og innovationer, der har givet bedre performance og processikkerhed i drejning.
Unikke komponentegenskaber, men svære at bearbejde
Evnen til at bearbejde et emnemateriale afgøres af flere faktorer, der påvirker og definerer behov og resultater i metalbearbejdningen. Groft sagt er det muligheden for at bearbejde emnematerialet, der holdes op mod tendensen til genereret værktøjsslid og spånbrydning. Med den forskel at disse eksotiske materialer på de fleste områder er vanskelige at bearbejde. De anses for at være vanskelige at bearbejde spåntagende – men ikke problematiske, hvis de bare håndteres korrekt.
De mere eksotiske blandt de relativt almindelige emnematerialer er klassificeret i ISO S-gruppen: varmebestandige superlegeringer (HRSA) og titanlegeringer. Vedrørende bearbejdning kan alle disse materialer opdeles i flere undergrupper afhængig af materialets sammensætning, tilstand og egenskaber. Den kemiske og metallurgiske sammensætning af en S-klassificeret legering definerer de fysiske egenskaber og dermed materialets bearbejdelighed. Spånkontrol er generelt krævende på grund af segmenteringen af spånerne, og det er ikke usædvanligt, at de specifikke skærekræfter er dobbelt så store som ståls (det er det direkte mål for, hvor svært det er at bearbejde et materiale, og som definerer skærekræfterne og den nødvendige effekt).
Den primære årsag til, at HRSA-materialer er vanskelige at bearbejde, er at de fortsat har høj styrke ved høje temperaturer. De bliver ikke blødere og flyder ikke på samme måde, som de fleste andre materialer, og de koldhærder også let. Stor mekanisk belastning og høje temperaturer er koncentreret omkring skærkanten. Nikkel-, jern- eller koboltbaserede legeringer er undergrupper af HRSA, og de har enestående egenskaber til brug i komponenter, primært i aerospace-, energi- og medicinalindustrien, da deres gode egenskaber ikke ændrer sig ret meget, før materialerne er meget tæt på deres smeltepunkt. De er også meget korrosionshæmmende. Men set ud fra et bearbejdningssynspunkt kræver de en effektiv maskine, stabil opspænding, applikationstilpassede skærkvaliteter og -geometrier, optimeret køling og sidst men ikke mindst den rette bearbejdningsmetode og værktøjsløsning. Det kræver helt sikkert mere planlægning, og det kræver større arbejde før selve produktionen.
Titanlegeringer er også opdelt i undergrupper med varierende bearbejdelighed. Generelt vurderes bearbejdeligheden som forskellige grader af dårlig (sejhed), og det stiller meget specielle krav til værktøjer og metoder. Kravene defineres af den lave varmeledningsevne, den høje styrke ved høje temperaturer, de tynde spåner med tendens til rivning, der skaber et snævert kontaktområde på skærets overflade høje skærekræfter koncentreret tæt ved skærkanten. Spåner kan dannes cyklisk, hvilket giver variable skærekræfter, og nogle legeringer har et relativt højt indhold af karbider, der gør materialet ekstra abrasivt. Meget høje skærehastigheder kan medføre en kemisk reaktion mellem spånerne og værktøjsmaterialet, der kan medføre pludselig udflisning/brud på skærkanten og også klæbende materiale/fastsvejsning på skærkanterne. Nogle legeringer koldhærder også nemt, hvilket giver øget slid af diffusionstypen, som medfører kraftig gratdannelse. Dette kan også vanskeliggøre de efterfølgende operationer.
Eksotiske, ja, men vinduet for vellykket bearbejdning af mange HRSA-materialer og titanlegeringer er relativt lille.
Ved drejning af disse materialer, …
… afhænger det gode resultat af, at den kombinerede effekt af materialet og applikationsfaktorerne er afbalanceret. Der er et par grundlæggende tommelfingerregler, der er afgørende for, at der opnås gode resultater:
- planlæg på forhånd en god bearbejdningsstrategi, så detaljeret som muligt
- find den bedste værktøjsløsning
- find de bedste værktøjsbaner, og brug meget stabile værktøjsholdere
- brug det bedste fra den nye, applikationstilpassede værktøjsteknologi
- anvend kvalificerede skæredata for at etablere processikkerhed og produktivitet
- brug beregning af spiralskærelængde til at forudse spåntagningen
- anvend køling korrekt – moderne højtryksløsninger
- brug specialistanbefalinger og -hjælp.
Bearbejdningsprocessen bør altid planlægges omhyggeligt på grund af de kritiske og afgørende faktorer, som f.eks. emnematerialets tilstand/forhold. Støbning, smedning, stangmateriale, varmebehandling, opløsningsbehandling og modning påvirker komponenten betydeligt og på måder, der vil påvirke valget af værktøjer og metoder. Emnets overfladetilstand varierer og påvirker bearbejdningen, lige som hårdheden. Strategien for drejning bør også omfatte de krav, der stilles ud fra designegenskaberne af den komponent, der skal bearbejdes, samt de forskellige bearbejdningstrin, dvs. skrubbearbejdning (første trin), semi-sletbearbejdning (andet trin) og sletbearbejdning (sidste trin). Komplekse egenskaber og overfladeintegritet er almindelige problemer.
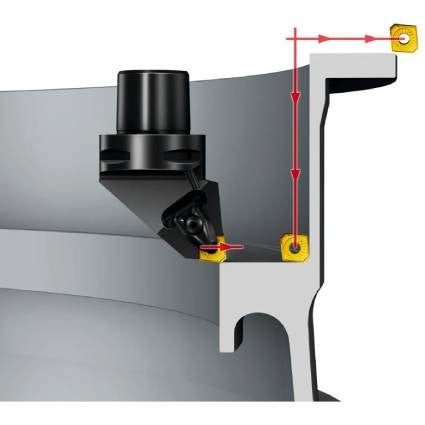
Komponentens design, materiale og tilstand danner grundlag for planlægning af drejning i eksotiske materialer. Hvis det er relevant, skal det først fastlægges, hvordan skrub-, semi-slet- og sletbearbejdningen bør udføres, også i forhold til materialets tilstand og kvalitetskravene. Planlægning af værktøjsbaner og reduceret tilspænding i programmeringen vil være afgørende for værktøjssliddets omfang, værktøjstype, cyklustider og sikkerhed.
Skæreforløbet i disse materialer …
… er i høj grad påvirket af skærkantens indgangsvinkel i emnet. Skærkantens indgrebsvinkel kombineret med skærgeometrien er afgørende for performance, værktøjslevetid, sikkerhed og resultater. Skærformer skal ofte vælges i forhold til den spåntagende bearbejdning, der skal foretages. Men det bør altid være en vigtig overvejelse for applikationen, at brug af en lille indgrebsvinkel vil påvirke til performance og værktøjslevetid.
Valg af skærkvalitet skal til dels ske på baggrund af indgrebsvinklen. Denne vinkel påvirker blandt andet den type slid, der danner stråleslid på skærkanten, og vinklens størrelse påvirker resultaterne og kan forårsage for tidligt værktøjssvigt. Når den rette fremgangsmåde vælges for applikationen, betyder det også, at der kan vælges en skærkvalitet, der kan give højere produktivitet og samtidig lang værktøjslevetid og høj sikkerhed.

Det skærende værktøjs indgrebsvinkel påvirker spåntykkelsen, tilspændingen, skærekræfter samt hvilken type spåntagning, der kan foretages. Med eksotiske materialer har valget af vinkel direkte konsekvenser for produktiviteten og procespålideligheden, der påvirker skærformen og næseradius, samt hvor godt et værktøjsmateriale kan anvendes. Runde skær og skær af xcel-typen er normalt det bedste valg.
Valg af værktøjsmateriale (skærkvalitet) bør være påvirket af den type af drejning, der skal foretages, skrubbearbejdning, semi-sletbearbejdning eller sletbearbejdning samt emnets tilstand og type spåntagning. På grund af disse materialers hårdhed bør plastisk deformation af skærkanten altid anses for at være den primære risikofaktor ved valg af skærkvalitet (stråleslid påvirkes som nævnt primært af indgrebsvinkel og spåndybde). Valg af skærkvalitet bør også kombineres med skærform, da det er et spørgsmål om styrke, der skal vurderes ved valg af løsning, spånbelastning og af, om den skærende bearbejdning skal være kontinuerlig eller afbrudt. Applikationstilpassede kvaliteter er derfor afgørende for bearbejdning af HRSA.
De primære krav er, at skæret i høj grad bevarer hårdheden selv under ekstremt høje temperaturer og har den rette sejhed, samt at skærets belægning har tilstrækkelig vedhæftning. Vendeskær til disse materialer bør have en positiv skærgeometri, en skarp og stærk skærkant samt en relativt åben spånbryder.
Fastlæggelse af de bedst egnede skæredata er også afgørende for effektiv bearbejdning af disse materialer. Skærehastigheden er begrænset af kombinationen af hastighed, tilspænding og spåndybde og kan optimeres for at opnå høj produktivitet, sikkerhed og kvalitet. Skærehastigheden er forbundet med generering af varme, og hvordan dette påvirker skæret; Den skal være høj nok, til at spånerne har tilstrækkelig plasticitet, men den må ikke være for høj, da det vil skabe ubalance i værktøjsmaterialet. Hastigheden ligger normalt omkring 130 til 260 sfm (40 til 80 m/min.) med applikationstilpassede hårdmetalskær og 490 til 1310 sfm (150 til 400 m/min.) med keramiske skær.
Tilspændingshastigheden er den vigtigste faktor, der påvirker indgrebstiden og spåntykkelsen. I eksotiske materialer skal den være mere omhyggeligt afbalanceret, da grænserne er relativt snævre: ved skrubbearbejdning skal spånerne maksimeres, men de må ikke overbelaste skærkanten, og ved sletbearbejdning skal spånen skal være tyk nok til at undgå for høj varme og deformationshærdning.
Spåndybden påvirker ofte skærkantens tilgang, og den bør derfor være under en bestemt værdi. Når der eksempelvis anvendes runde skær til HRSA, bør spåndybden ikke overstige 15 % af skærdiameteren. Spåndybden skal også programmeres omhyggeligt ved profildrejning. Udsparinger eller hjørner må ikke overskride skærkantens passende indgrebsvinkel.
Med hensyn til værktøjslevetid er det vigtigt at arbejde grundigt med den samlede bearbejdningslængde (SCL). Ved valg af korrekt værktøjslevetid kan maskinstop til skærvending forudses og programmeres, så overløb med et værktøj, der kører med den rette hastighed, kan færdiggøres, og hvor skærkanten stadig kan give den ønskede overfladekvalitet.
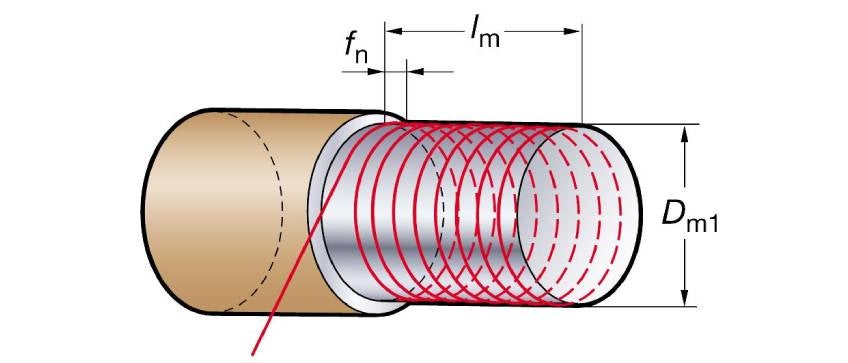
Beregning af den samlede bearbejdningslængde vil hjælpe med at forudse tid eller skærelængde for på den måde at reducere bearbejdningstiden og forbedre overfladekvaliteten ved bearbejdning af krævende eksotiske materialer. Maskinstop ved skærskift planlægges derefter ud fra den samlede bearbejdningslængde, så de passer til operationen og skæredataene for at optimere værktøjslevetid og maskinudnyttelsesgrad.
Værktøjsslid påvirkes i høj grad …
… af de høje skærekræfter i kombination med højere skærkanttemperaturer, hvilket giver tendens til, at bestemte typer skærkantslid opstår. De primære slidformer, der nævnes, er for det første stråleslid (den mekaniske slidtype, som er bestemt af spåndybden); for det andet plastisk deformation af skærkanten, der skyldes en kombination af høj temperatur og højt tryk, og for det tredje abrasivt slid, der primært skyldes de hårdere materialer. En anden type er oversideslid, der udvikler sig på keramiske skær, hvor lag på oversiden af skærkanten skæres af. Her spiller skærkantens indgrebsvinkel en afgørende rolle.
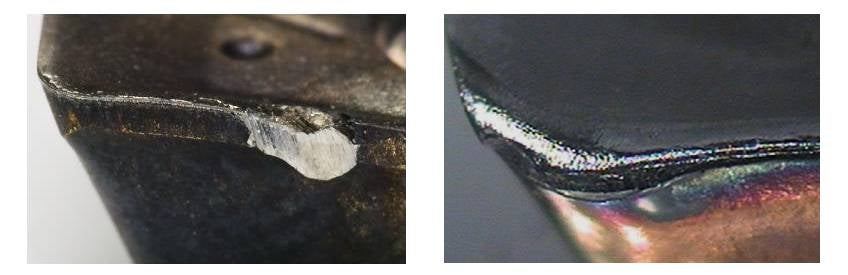
For eksotiske materialer afhænger valget af skærkvalitet ikke direkte af, om der skal foretages skrub- eller sletbearbejdning, som det er tilfældet for andre materialer. I stedet er valget af kvalitet i højere grad en optimeringsfaktor, hvilket er lidt mere komplekst afhængig af skærets form og skærkantens indgrebsvinkel samt operationstypen. Destruktive slidmønstre, som den viste stråleslid og plastiske deformation, skal primært undgås ved at kombinere passende værktøjer, skæredata og metode. Hårdmetalskær sammen med moderne sialon-keramik og til en vis grad whisker-keramik er ofte det bedst egnede og bredt anvendelige valg.
Den bedst egnede indgrebsvinkel til drejning af eksotiske materialer er den, hvor vinklen er lille, 45 grader eller mindre. Den ringeste løsning er, når indgrebsvinklen er 90/0 grader, eller når spåndybden er større end skærets næseradius. En stor/lille vinkel giver tynde spåner og højere tilspændingshastighed.
Til drejning af HRSA er værktøjets indgrebsvinkel afgørende for, om et PVD- og CVD-belagt skær er den bedst egnede løsning. Dette for at beskytte mod de termiske effekter. PVD er velegnet til en indgrebsvinkel på 90/0 grader og CVD til 45 grader. Ved drejning i titan opnår man derimod ikke en fordel af skærbelægningen. I dette tilfælde er det en vigtigere faktor at vælge det bedst egnede skærkantforhold, eksempelvis runde skær til sletbearbejdning. Nye varianter af PVD-skær giver stor hårdhed og god modstandsdygtighed mod deformation af skærkanten og termisk chok. Kombineret med skarpe skærkanter kan de også udmærke sig i skrub- til sletbearbejdning af klæbende materialer.
Den rette skærform …
… er en vigtig applikationsfaktor ved bearbejdning af disse materialer. Det runde skær (R-form) er blevet en af de primære anbefalinger til disse materialer. Det runde skær har den nødvendige styrke til en skarp, positiv skærkant; en spåntykkelse, der varierer langs en lang skærkant, giver mulighed for høj tilspændingshastighed; en stor skærradius, der ikke begrænser tilspændingshastigheden på grund af den overfladekvalitet, skæret producerer. Det runde skær giver også programmeringsfleksibilitet til at foretage profildrejning og lommedrejning, som det kræves af mange komponentformer.
Et firkantet skær (S-form) er i nogle tilfælde bedst egnet til skrubbearbejdning, da det er velegnet til skrubdrejning i forskellige retninger med en vinkel på 45 grader. Det rombiske skær (C-form) er ekstremt fleksibelt med hensyn til værktøjsbaner, og når det udvides til at være et Xcel-skær, giver det endnu bedre værktøjstilgængelighed i hjørner og udsparinger. Denne kombination af skærform og 45-graders indgrebsvinkel reducerer også radiale skærekræfter, sikrer en konstant spåntykkelse og reducerer strålesliddet. Resultatet er højere produktivitet, længere værktøjslevetid og bedre sikkerhed.
Programmeringsoptimering …
… er vigtig, og i det følgende gives der et par anbefalinger til at opnå forbedre performance, især ved brug af runde skær, der generelt er velegnede til bearbejdning af eksotiske materialer:
- undgå indstikning og vælg blødere påvirkninger; halver tilspændingshastigheden, hvis disse overløb er nødvendige,
- ved drejning op til et hjørne bør tilspændingen også reduceres til det halve, ellers bør værktøjet rulle op til hjørnet, hvor den programmerede radius er den samme som skærdiameteren. (Retningslinjerne for den programmerede minimumradius er ca. 25 % af skærets diameter og komponentradius er 75 % af skærets diameter. Tilspænding i værktøjets centrum gælder for den programmerede radius.),
- til skrubbearbejdning med runde skær bør den programmerede radius svare til skærets diameter og til sletbearbejdning skal det sikres, at den programmerede radius er større end skærets diameter,
- overvej alternative værktøjsbaner, flere overløb og bearbejdning i begge retninger for at udnytte skærene fuldt ud,
- beskyt keramiske skær ved først at affase emnet og ved at bruge tilspænding ind i fasen,
- sørg for at bevare en tilpas indgrebsvinkel i forhold til indgrebsvinklen gennem hele bearbejdningsprocessen. Begrænsning af vinklen er afgørende for at opnå god performance, og brug af runde skær er en vigtig booster for at udnytte mulige potentialer med moderne skærkvaliteter,
- undgå enhver omviklingseffekt ved profildrejning eller indstikning, og brug alternative værktøjsbaner eller mindre skærdiameter, for at skæret ikke skal blive overbelastet,
- overvej at vælge trokoidedrejning, eller at bryde bearbejdningen op i mindre overløb, især ved lommebearbejdning.
Hvad bør du se på inden for værktøjstyper og metoder til bearbejdning af HRSA og titan? Her er et par hovedpunkter:
- Præcisionskøling bør altid være på dagsordenen. Med præcisionsdyser, der leverer kølevæske ind bag på og ved skærkanten via indvendig køling i værktøjet, giver mange fordele, der udnyttes til drejning, fræsning og boring. Avanceret dyseteknologi, der fås både som standard og specialfremstillede løsninger med forskellige trykområder, kan anvendes til alle maskintyper med tilstrækkelig kølevæskeforsyning. Kølevæsketryk: Nye maskininvesteringer bør altid have et kølevæsketryk på 70 bar til drejning af titan, da det giver bedre spånbrydning, men et tryk på op til 200 bar er en fordel til drejning af HRSA, da spånbrydningen af dette materiale er mere vanskelig.
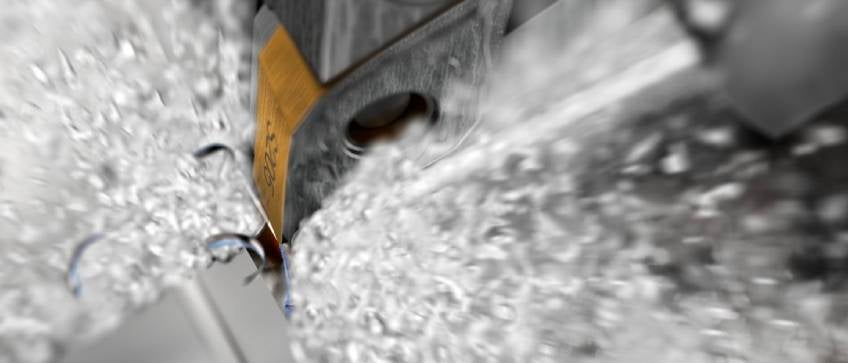
Brugen af køling er en afgørende applikationsfaktor i bearbejdningen af eksotiske materialer. Præcisionskøling fås i dag som standard eller som specialfremstillet højteknologisk løsning, og den er så effektiv, at den gør en klar forskel for spåntagning, spånbrydning, værktøjslevetid og produktivitet. Generelt gør de høje temperaturer, der genereres i disse materialer, køling nødvendig, men når der tilføres rigelige mængder kølevæske præcist under højt tryk i kombination med applikationstilpassede skær og indvendig køling vil det optimere både performance og resultater.
- Adgangsforhold er ofte et problem ved drejning i eksotiske materialer. Komplekse former og værktøjsudhæng gør det kritisk at vælge de rette værktøjer og metoder. Prøv at se på modulære systemer, hvor du kan få et pålideligt koncept med værktøjsblade, der har skærkanter i forskellige vinker, og hvor der er flere udhæng. Udvalget af adapter- og bladalternativer bør give fleksibilitet til at bygge næsten ethvert værktøj ud fra et begrænset udvalg af standardværktøjer, så det passer til konfigurationer og giver god adgang til steder med begrænset plads både ud- og indvendigt. Blade bør indeholde de nødvendige radiale og aksiale frigange for at nå dybt ned i vinklede spor, og med præcisionskøling, der tilføres gennem værktøjet og ud til skærkanten.
- Værktøjsmaterialet er kernen i enhver bearbejdningsoperation, og det er en kritisk faktor ved bearbejdning af eksotiske materialer. Dette område kræver applikationstilpassede skærkvaliteter i kombination med den rette skærgeometri, primært i form af det sidste nyeste inden for hårdmetal- og keramiske skær. Ubelagte hårdmetalkvaliteter har stadig en vigtig position, men den nyeste udvikling inden for skærbelægningsteknologi har ikke mindst leveret belagte hårdmetalskær, der har flyttet grænserne for skærkantens kapacitet ved at reducere bearbejdningstiden og forlænge værktøjslevetiden.
- Indbygget vibrationsdæmpning i udborestænger, blade og endda i fræsere bør være inkluderet for at minimere vibrationstendensen. Antivibrationsteknologi har taget kæmpestore spring og bør være et naturligt valg, ikke mindst hvis værktøjsudhæng har en tendens til at skabe ustabilitet. Produktivitet, processikkerhed og emnekvalitet er faktorer, der hænger direkte sammen med kvaliteten og tilgængeligheden af vibrationsdæmpede værktøjer. Mange operationer er umulige at udføre uden denne egenskab: i dag kan indvendig drejning med udhæng på op til fjorten gange diameteren på op til 250 mm udføres meget effektivt og med en finish af høj kvalitet.