En grønnere fremtid for aerospace-industrien
OEM-producenter skal have en holistisk tilgang til fremtidens fly.
Som en verdens største udledere af CO2-emissioner er der stort pres på aerospace-industrien for at levere grønnere fly, der er lettere og kan flyve længere. Men for at opnå det skal der arbejdes med materialer som aluminium og varmebestandige superlegeringer (HRSA), der er vanskelige at bearbejde. Her forklarer Sébastien Jaeger, Industry Solution Manager – Aerospace hos Sandvik Coromant, hvordan OEM-producenter i aerospace-industrien kan implementere avancerede værktøjsløsninger til bæredygtig bearbejdning af disse komponenter, der er svære at bearbejde.
Ifølge World Economic Forum (WEF) vil det "ikke kun hjælpe med at skabe en bæredygtig fremtid at opnå CO2-neutralitet i 2050, men det vil også gøre hele luftfartsbranchen økonomisk stærk og konkurrencedygtig." Men mens e-mobilitet har slået igennem i bilbranchen, hvor elbilsalget oversteg salget af dieselbiler i august 2021 i Storbritannien, vil denne udvikling tage længere tid i luftfartsbranchen.
Generelt forventes det ikke, at elektriske fly ikke bliver udbredt før 2035. Lonely Planet angiver i sin rapport, selvom easyJet håber at flyve med elektriske rutefly på ruter under 500 km i 2030, og selvom Norge har en målsætning om, at alle korte distancer tilbagelægges med elfly i 2040, forventes det, at "vi ikke kommer til at flyve lange distancer med elektriske jumbojets i den nærmeste fremtid: Batterierne er simpelthen for tunge."
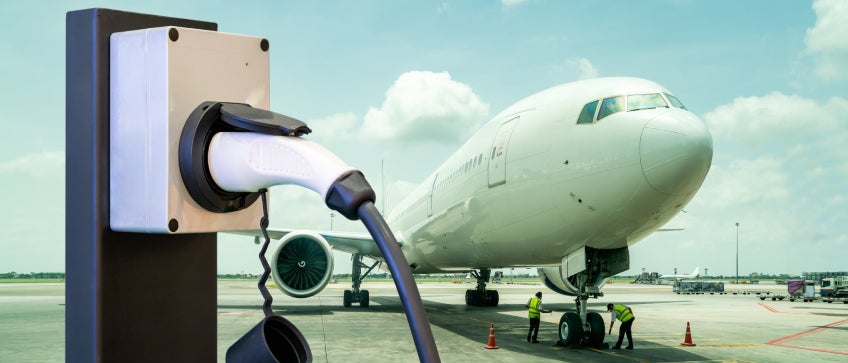
Elektriske fly forventes at blive udbredt i 2035.
Batterierne skal være lettere for at være en anvendelig løsning, og samtidig står OEM-producenterne over for stigende krav om at fremstille lettere komponenter for at opveje problemet. Vi kan være sikre på, at aluminium – især de nye typer aluminium med højere styrke, modstandsevne over for træthedsbrud og andre egenskaber – vil blive brugt for at gøre systemerne lettere.
Vi kan også se, at der bruges stadig flere af de nye varmebestandige superlegeringer (HRSA). Faktisk anvendes HRSA-materialer allerede til flydele, der stilles ekstreme performance-krav til, fordi disse materialer bevarer hårdheden, selv ved høje temperaturer. Disse materialeegenskaber vil være afgørende, da en løsning for at gøre luftfarten mere bæredygtig vil være at køre motorerne hårdere og ved højere temperaturer.
Komponenter skal også produceres til snævrere tolerancer og med flere forskellige design. Lige som elbilernes design vil fremtidens elektriske flydesign – inklusive flystel og motorer – variere mere fra producent til producent end de eksisterende fly med forbrændingsmotorer. Nogle OEM-producenter arbejder med delta-form, varierende vingeformer og vingekonstruktioner med stivere til flyskroget. Andre OEM-producenter kører videre med de traditionelle design med store rør, vinger og en motor.
Der kommer også forskellige former for motorkonstruktioner som elektriske, batteridrevne eller elektromagnetiske motorer samt hybridsystemer, hvor de nuværende motorer understøttes af elmotorer. OEM-producenter vil være nødt til at fremstille flere forskellige komponenter med snævre tolerancer, og samtidig skal de også finde nye måder at reducere støj, vægt og emissioner på – og alle de faktorer påvirker, hvordan de elektriske systemer fungerer. Men aluminium- og HRSA-komponenter er vanskelige at bearbejde, så det vil være en udfordring at gøre det bæredygtigt og omkostningseffektivt.
Hurtige fremskridt
En måde at fremstille lettere og mere brændstoføkonomiske fly på er ved hjælp af AM-teknikker, dvs. additiv bearbejdning. Additiv bearbejdning gør det muligt at udvikle specialfremstillede dele med meget komplekse former og funktionelle produkter med snævre tolerancer, så flydele, der er vanskelige at bearbejde, som f.eks. gitterkonstruktioner, bliver nemmere at fremstille. Ifølge undersøgelser foretaget af softwarefirmaet Dassault Systemes kan "vægtreduktionen opnået med AM-processer i flyindustrien give energibesparelser på op til 25 %", og "hvert kilo, vægten reduceres med på en flyrejse, kan give en brændstofbesparelse på op til 3.000 USD."
Men er selve AM-produktionen bæredygtig? En undersøgelse, hvor instituttet for maskinteknik ved Rumæniens tekniske universitet i Cluj-Napoca er medforfatter, beskriver additiv bearbejdning (AM) som "et godt alternativ til traditionel bearbejdning, som sprøjtestøbning, trykstøbning eller spåntagende bearbejdning." Undersøgelsen konkluderer også, at: "additiv bearbejdning (AM) har potentiale til at kunne sænke omkostningerne og være mere energieffektiv end konventionelle processer."
AM vil også have afgørende indflydelse på, hvordan og hvor forskelligt produkterne fremstilles. Fordelene kan være lavere CO2-emissioner, mindre materialeforbrug og mindre transport, fordi delene kan fremstilles lokalt i stedet for blive importeret.
Producenterne kan altså fremstille mere komplekse, kompakte og innovative flydele takket være hurtig fremstilling af prototyper. Hurtig fremstilling af prototyper henviser til flere forskellige teknikker, men målsætningen er hurtigt at fremstille en konkret 3D-prototype ud fra en CAD-fil. Med disse prototyper kan man foretage mindre test af nye materialer, før de tages fuldt i brug i produktionen, for at sikre at komponenterne fremstilles med højeste innovation, kvalitet og præcision.
Vi har set på, hvordan OEM-producenter i aerospace-industrien kan anvende nye metoder til produktion af mere komplekse komponenter. Men hvad med at finde de rette værktøjer til opgaven, især når der arbejdes i hård aluminium og HRSA?
Disse materialer kræver brug af værktøjer med højere slidstyrke og længere værktøjslevetid. Derfor udviklede Sandvik Coromant S205-kvaliteten, der bruges til drejning i stål. S205's metallurgiske egenskaber omfatter et Inveio®-lag af tætpakkede, ensrettede krystaller. Det giver en stærk beskyttende barriere omkring skæret, der styrker værktøjet og forstærker de mekaniske egenskaber. Skæret har allerede vist sig at være nyttig til fremstilling af flere flykomponenter, bl.a. motorturbineskovle, ringe og aksler. Sandvik Coromants kunder har allerede rapporteret om 30 til 50 % højere skærehastigheder ved brug af S205 sammenlignet med konkurrerende kvaliteter til drejning i HRSA.
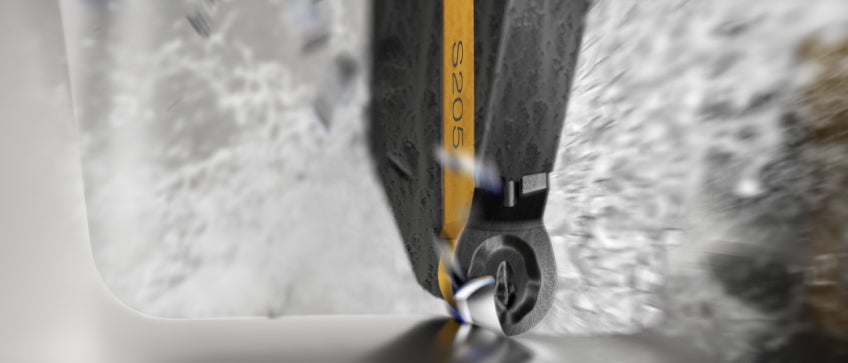
Holistisk tilgangsvinkel
Vi har set på produktionsprocesser og værktøjer, men hvordan kan vi kombinere de til ting bedst muligt? Der kan jo spildes tid på at udarbejde en fuldt integreret løsning, hvis systemerne ikke er designet til at fungere godt sammen.
Derfor hjælper Sandvik Coromant sine kunder i aerospace-industrien med det, vi kalder en komponentløsning. Løsningen består af flere trin inklusive en gennemgang af maskinkravene og tidsstudier, der undersøger omkostningerne pr. komponent. Produktionsmetoderne analyseres også indledningsvist, både ved at foretage MTM-målinger (metode-/tidsmåling) og ved at se på slutbrugerprocesserne. Komponentløsningen inkluderer også CAM-programmering og projektstyring af lokale projekter eller projekter på tværs af landegrænser.
For en af Sandvik Coromants kunder, der havde problemer med spånbrydningen i sin produktion, gjorde komponentløsningen det muligt for at finde årsagen og en løsning. Sandvik Coromants specialister udviklede en ny strategi for kunden med dynamiske værktøjsbaner, der gjorde det muligt at styre spånbrydningen meget nøjagtigt. Vi kaldte denne nye løsning for "scoop-drejning", og den metode har vi nu patent på. Med scoop-drejning kunne kunden reducere cyklustiden med 80 %, opnå god spånkontrol og fordoble værktøjslevetiden.
Kunden kunne desuden også reducere antallet af maskiner fra fire til en, hvilket mindskede behovet for multi-tasking og gav sikrere bearbejdningsprocesser og problemfri produktion. Brug af færre maskiner og mulighed for at afslutte produktionsforløb med færre værktøjsskift takket være de stærkere kvaliteter som S205, vil være nøglen til en mere bæredygtig flyproduktion.
Software vil også spille en afgørende rolle, f.eks. CoroPlus® Tool Guide der er en del af Sandvik Coromants digitale sortiment. Kunderne kan træffe vigtige beslutninger om valg af værktøj og skæreparametre allerede før produktionens opstart.
Et lukket cirkulært af kredsløb
Ud over nye løsninger til værktøjer og fremstilling kan OEM-producenter i aerospace-industrien også se på produktionen. Ifølge en rapport udarbejdet af ATAG (Air Transport Action Group) anvender virksomheden Kaiser, der leverer aluminium til Boeing, nu et lukket genbrugssystem, et af de største af sin slags i branchen. Kaiser vurderer, at branchen vil kunne genbruge omkring ti millioner kilo afskårne stykker metal og metalskrot om året takket være dette genbrugssystem.
Hos Sandvik Coromant har vi lavet vores eget cirkulære system til genbrug af hårdmetalværktøjer, hvor vi tilbagekøber kundernes kasserede hårdmetalværktøjer og skær og genbruger dem i produktionen til helt nye værktøjer. På den måde kommer de fleste af de råmaterialer, der anvendes i Sandvik Coromants hårdmetalværktøjer, fra hårdmetalskrot Vi driver en bæredygtig virksomhed i en verden med begrænsede ressourcer og minimerer vores affaldsmængder. Ifølge vores beregninger vil vores produktion af værktøjer af genbrugte materialer give et 70 % lavere energiforbrug og et 40 % lavere CO2-udslip.
Der er stigende pres på aerospace-industrien for at levere grønnere fly, der er lettere og kan flyve længere. Men med de rette processer og værktøjer, for ikke at tale om en mere holistisk tilgang til produktion, kan OEM-producenter i aerospace-industrien være med til at gøre luftfartsindustrien grønnere.