Rødglødende drift
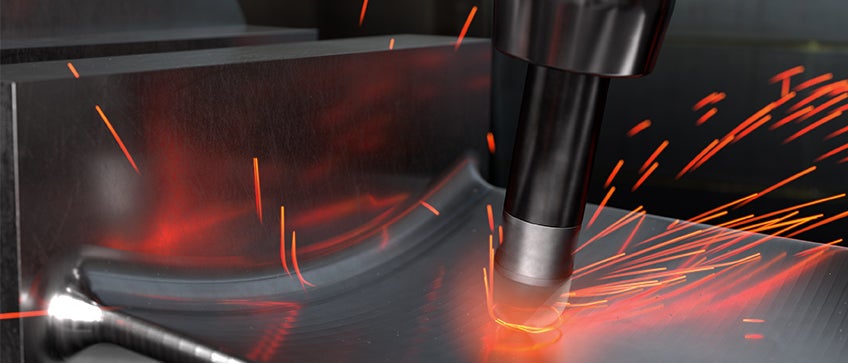
Udfordring: Effektiv bearbejdning af motordele i HRSA til fly.
Løsning: Udvikling af en afbalanceret holistisk løsning, der omfatter alt lige fra maskinen, værktøjerne, geometrierne og værktøjsmaterialerne til bearbejdningsstrategien.
Varmebestandige superlegeringer (HRSA) er de mest anvendte materialer til dele i jetmotorkompressorer og turbiner. De stålkvaliteter, der primært anvendes til disse applikationer, er nikkelbaseret som f.eks. Inconel, Waspaloy og Udimet.
Egenskaberne for HRSA-legeringerne varierer meget afhængigt af sammensætning og produktionsproces. Især varmebehandling er af stor betydning – en dispersionshærdet, dvs. "modnet" komponent kan have dobbelt så stor hårdhed som et blødt udglødet eller ubehandlet emne
Endnu strengere emissionslove kræver højere driftstemperatur af de nye motortyper og kræver nye materialer til komponenter, der opnår de højeste temperaturer. Den samlede mængde HRSA i en jetmotor er desuden stigende sammenlignet med andre materialer.
Men fordelene ved HRSA-materialer giver udfordringer i produktionen: Den store varmebestandighed medfører høje skærekræfter. Lav varmeledningsevne og fremragende hærdningsevne medfører høj skæretemperatur. Tendens til deformationshærdning medfører stråleslid.

Akselkomponent i HRSA.
Komponenterne – turbineskovle, huse, blisks og aksler – er krævende emner, da mange af dem er tyndvæggede og de alle har komplekse former. De sikkerhedskritiske motordele skal overholde strenge krav til kvalitet og dimensionsnøjagtighed.
Forudsætninger for succes er en stærk maskine, stive værktøjer, højtydende skær og optimal programmering. De mest udbredte metoder varierer en del. Skive-, ring- og akselkomponenter drejes normalt, mens huse og blisks ofte fræses.
Bearbejdningen af HRSA deles generelt op i tre trin. Ved skrubbearbejdning bearbejdes det støbte eller smedede råemne først, så det får selve grundformen. Emnet er normalt relativt blødt (typisk hårdhed omkring 25 HRC), men det har ofte en grov, ujævn overflade eller belægninger. Hovedprioriteten er god produktivitet og effektiv spånvolumen.
Mellem skrubbearbejdningen og mediumbearbejdningen bliver emnet varmebehandlet til en meget hårdere modnet tilstand (typisk med en hårdhed på 36-46 HRC). Nu får komponenten den endelige form, bortset fra bearbejdningstillægget til sletbearbejdning. Her fokuseres der igen på produktivitet, men processikkerhed er også vigtig.
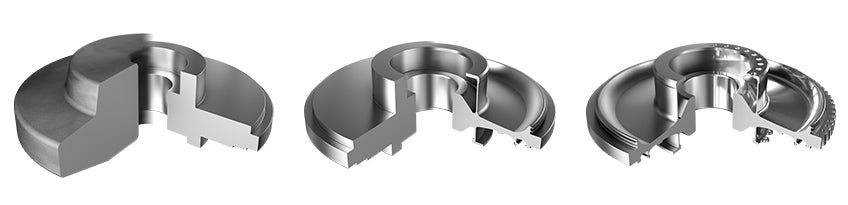
Skrub-, medium- og sletbearbejdning af turbineskovle i HRSA.
Den endelige form og overfladefinish bliver til ved sletbearbejdningen. Her er der fokus på overfladekvalitet, nøjagtige dimensionstolerancer og at forhindre deformationer og kraftig egenspænding. I kritiske roterende komponenter er materialetræthed det vigtigste kriterium, og der er ikke plads til fejl i overfladen, der kan medføre revnedannelse. Kritiske deles pålidelighed sikres ved at anvende en veldokumenteret, certificeret bearbejdningsproces.
Almindelige krav til vendeskær omfatter god skærkantsejhed og god vedhæftning af belægningen på substratet. Selvom negative former bruges på grund af den høje styrke og økonomien, skal geometrien være positiv.
Der bør altid anvendes køling ved bearbejdning af HRSA, undtagen når der fræses med keramiske skær. Keramiske skær kræver rigelige mængder kølevæske, mens præcisionen af kølevæskestrømmen er afgørende for hårdmetalskær. Ved brug af hårdmetalskær giver højt kølevæsketryk yderligere fordele, bl.a. længere værktøjslevetid og effektiv spånkontrol.
Bearbejdningsparametre varierer afhængig af forholdene og materialet. I første trin (FSM) er målsætningen primært god produktivitet, der opnås ved hjælp af høj tilspændingshastighed og stor spåndybde. I andet trin (ISM) anvendes der ofte keramiske skær for at opnå højere hastighed. I det sidste trin (LSM) er der fokus på kvalitet, og der køres med lille spåndybde. Da høj skærehastighed kan forringe overfladekvaliteten, anvendes der hårdmetalskær til sletbearbejdning.
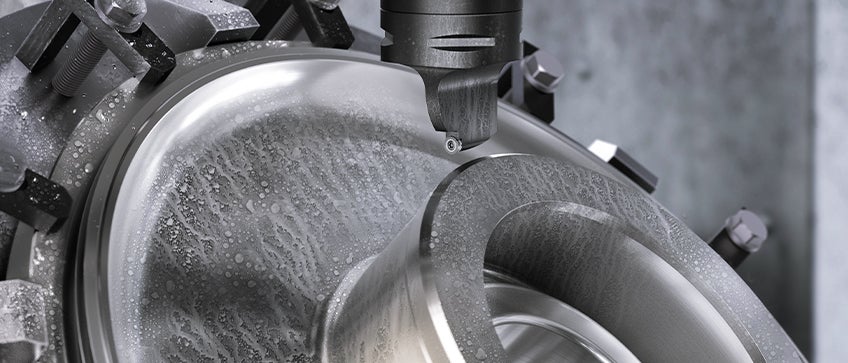
Turbineskovle er kritiske komponenter, der fremstilles i avancerede materialer, hvilket kræver høj processikkerhed med optimerede skærende værktøjer og løsninger.
Plastisk deformation og stråleslid er typiske slidbilleder på hårdmetalskær, mens grubeslid er almindelig på de keramiske skær. Tendensen til plastisk deformation reduceres ved at forbedre slidstyrken og evnen til at bevare hårdheden selv under ekstremt høje temperaturer. En positiv geometri og en skarp skærkant er også vigtige for at reducere varmeudvikling og skærekræfter. Stråleslid på hovedskærkanten kan afhjælpes ved at bruge en lille indgrebsvinkel, eksempelvis ved at bruge et firkantet eller et rundt skær eller en spåndybde, der er mindre end næseradiusen.
PVD-belagte skær er mere modstandsdygtige over for stråleslid på hovedskærkanten, mens CVD-belagte skær er mere modstandsdygtige over for stråleslid på bagkantmekanismen. Ved sletbearbejdning kan stråleslid på bagkanten forringe overfladekvaliteten.
Sammenfatning
Effektiv bearbejdning af motorkomponenter i HRSA-materialer kræver en velafbalanceret samlet løsning, der især tager hensyn til faktorer som emnets tilstand, værktøjsmateriale og de dermed forbundne skæredataanbefalinger, brug af køling og optimale bearbejdningsstrategier.
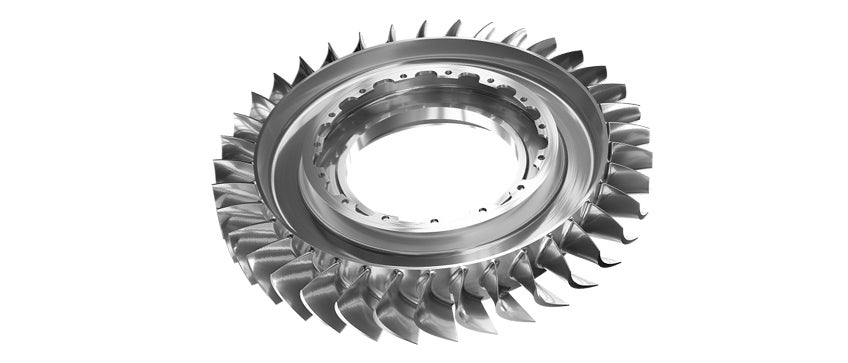
Værktøjer til andet (ISM) og sidste (LSM) trin i bearbejdningen af HRSA-materialer har meget skarpe, positive geometrier til slet- og mediumbearbejdning samt geometrier til operationer, der kræver større sejhed.