วิธีเลือกสปินเดิลของเครื่องจักร
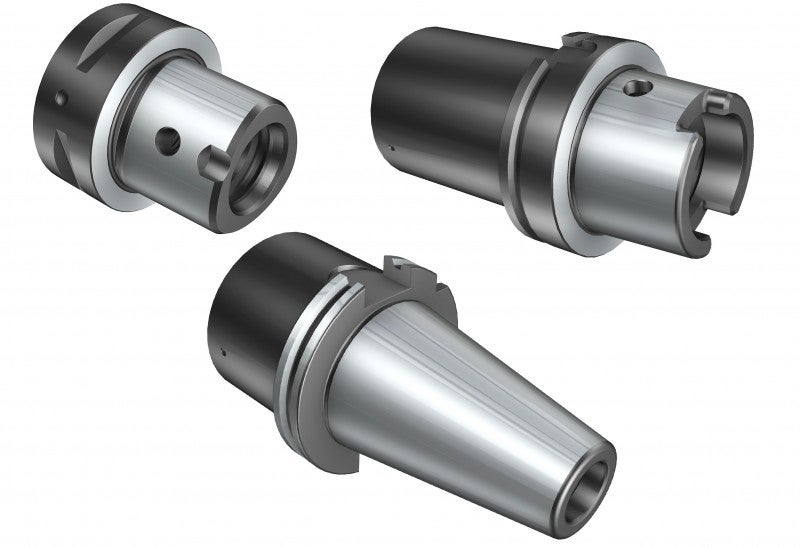
วิธีเลือกระบบเชื่อมต่อสปินเดลของเครื่องจักรถือเป็นการตัดสินใจที่มีความสำคัญ เนื่องจากเป็นตัวกำหนดข้อจำกัดด้านประสิทธิภาพการตัดเฉือนโลหะ แต่ไม่มีคำตอบที่สามารถอธิบายให้เข้าใจได้ง่ายว่าระบบเชื่อมต่อใดดีที่สุด เนื่องจากขึ้นอยู่กับชิ้นงานที่จะตัดเฉือนและการทำงานเป็นหลัก ดังนั้นจึงไม่ควรด่วนสรุปว่าตัวเลือกสปินเดลมาตรฐานที่มาพร้อมกับเครื่องจักรรุ่นนั้นเป็นตัวเลือกของระบบเชื่อมต่อที่ดีที่สุดอย่างหลีกเลี่ยงไม่ได้
ข้อกำหนดเกี่ยวกับสปินเดลของเครื่องจักร
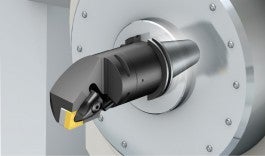
ในกรณีที่ไม่มีการตัดเฉือน ระบบเชื่อมต่อสปินเดลของเครื่องจักรต้องทำการสับเปลี่ยนได้รวดเร็ว แต่เมื่อมีการตัดเฉือน ข้อต่อระหว่างสปินเดลของเครื่องจักรกับระบบจับยึดที่มีความแข็งถือเป็นสิ่งสำคัญ แม้ว่าแรงตัดจะมีประสิทธิภาพสูงจนทำให้ระบบเชื่อมต่อหยุดชะงัก ระบบเชื่อมต่อจึงต้องมีความต้านทานการโก่งตัวและแรงบิดที่เต็มประสิทธิภาพ
- ความต้านทานการโก่งตัว: เมื่อต้องการให้กระบวนการตัดมีความมั่นคงเมื่อเครื่องมือมีระยะยื่นยาวหรือมีโหลดการตัดที่มีน้ำหนักมาก
- การส่งถ่ายแรงบิด: การทำงานกับเส้นผ่านศูนย์กลางขนาดใหญ่เป็นเรื่องที่ต้องให้ความใส่ใจเป็นพิเศษ เนื่องจากปริมาณโหลดที่ใช้ในระยะที่ห่างจากแนวศูนย์กลางของสปินเดล (แรงบิด = แรง × รัศมี) จะถูกต้านจากพื้นที่หน้าสัมผัสในการหมุนที่ใหญ่กว่า
- ตำแหน่งศูนย์กลางของเครื่องมือที่แม่นยำ: เพื่อให้มีความสามารถในการทำงานซ้ำและการผลิตที่มีมั่นคงและปลอดภัย ซึ่งเป็นสิ่งสำคัญอย่างยิ่งสำหรับการกลึง
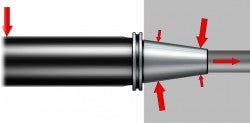
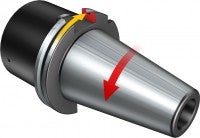
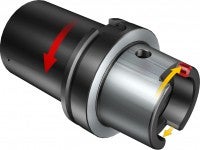
ระบบจับยึดที่ทนต่อการโก่งตัวสูงหรือแรงตัดในแนวรัศมีประกอบด้วยลักษณะเฉพาะดังต่อไปนี้:
- เส้นผ่านศูนย์กลางหน้าสัมผัสของหน้าแปลน: หน้าสัมผัสของหน้าแปลนช่วยเพิ่มฐานแพลตฟอร์มและลดการใช้แรงตัด
- แรงจับยึด: ยิ่งใช้แรงจับยึดในการต้านระบบจับยึดมาก ก็ยิ่งต้องใช้แรงตัดในการ "ผลัก" ระบบจับยึดมากขึ้นตาม
- ส่วนหน้าตัด: การลดขนาดเส้นผ่านศูนย์กลางเครื่องมือที่เกี่ยวข้องกับเส้นผ่านศูนย์กลางหน้าสัมผัสของหน้าแปลนจะทำให้ความต้านทานของเครื่องมือลดลง
- การส่งถ่ายแรงบิด: สิ่งที่ปรากฏชัดเจนเมื่อทำการกลึงและเครื่องมือมีเส้นผ่านศูนย์กลางขนาดใหญ่โดยมากคือ ไม่สามารถทนต่อแรงบิดได้และทำให้ความสูงที่ศูนย์กลางผิดพลาดและสูญเสียความเที่ยงตรงทันที
ความเป็นมาเกี่ยวกับระบบเชื่อมต่อสปินเดลของเครื่องจักร
ระบบเชื่อมต่อสปินเดลของเครื่องจักรเป็นวิวัฒนาการของเครื่องจักร เหตุการณ์สำคัญส่วนหนึ่งที่เราเห็นว่ามีอิทธิพลต่อการเปลี่ยนแปลงคือ
- ระบบควบคุม NC ที่นำไปสู่ระบบเปลี่ยนเครื่องมืออัตโนมัติและการจัดเก็บเครื่องมือ เหตุการณ์ดังกล่าวทำให้เกิดสเต็ปเทเปอร์แบบใช้สลักดึงและรองยึด
- รอบสปินเดลสูงขึ้น
- การตัดเฉือน การกลึง การกัด และการเจาะแบบมัลติฟังก์ชันด้วยระบบเชื่อมต่อเดียวกัน
ย้อนกลับไปเมื่อปี 1868 ระบบเชื่อมต่อระบบแรกและเป็นที่รู้จักกันดีคือ Morse Taper ซึ่งพัฒนาขึ้นสำหรับการเจาะ หลังจากนั้นมีการใช้สเต็ปเทเปอร์ 7/24 หรือเรียกว่าเทเปอร์ ISO เป็นครั้งแรกเมื่อปี 1927 รองยึดและสลักดึงเพิ่มเป็นส่วนหนึ่งของระบบเปลี่ยนเครื่องมือในช่วงทศวรรษที่ 60 โดยมีความแตกต่างกันตามภูมิภาคต่างๆ 3 ภูมิภาค ได้แก่ MAS-BT ในทวีปเอเชีย, ISO/DIN ในทวีปยุโรป และ CAT-V ในทวีปอเมริกา
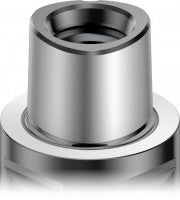
ข้อเสียของสเต็ปเทเปอร์คือความต้านทานการโก่งตัวและความเร็วรอบต่อนาทีจากแรงจับยึดที่ต่ำและไม่มีหน้าสัมผัสกับปลายสปินเดล ข้อเสียดังกล่าวทำให้มีการพัฒนาขึ้นในช่วงทศวรรษที่ 90 อันได้แก่ BIG-PLUS® (พัฒนาโดย BIG Daishowa ในประเทศญี่ปุ่น), HSK (Germany พัฒนาโดยคณะกรรมการของ DIN ในประเทศเยอรมนี) และ Coromant Capto® (เปิดตัวครั้งแรกในปี 1990 และเป็นระบบเดียวที่พัฒนาขึ้นสำหรับการใช้งานทุกรูปแบบนับตั้งแต่วันแรก ไม่ว่าจะเป็นการกลึง การกัด และการเจาะ)
ประเภทของระบบเชื่อมต่อสปินเดลของเครื่องจักร
ตารางด้านล่างแสดงระบบจับยึดหลักทั้งสี่ประเภทและวิวัฒนาการทีละขั้นนับตั้งแต่สเต็ปเทเปอร์แบบดั้งเดิมไปจนถึง Coromant Capto® ระบบเชื่อมต่อทุกประเภท ยกเว้น BIG-PLUS® ได้รับมาตรฐาน DIN, ISO หรือ ANSI
มุมเทเปอร์ | หน้าสัมผัสของหน้าแปลน | วิธ๊การจับยึด | การส่งถ่ายแรงบด | |
สตีปเทเปอร์ | 16.26° | ไม่มี | สลักดึง | ลมลอคที่หน้าสัมผัสของหน้าแปลน |
BIG-PLUS® | 16.26° | มี | สลักดึง | ลมลอคที่หน้าสัมผัสของหน้าแปลน |
HSK-A | 5.7° | มี | ชุดจับยึดแบบแยกส่วนภายใน | ลมล็อคที่เทเปอร์ |
Coromant Capto® | 2.88° | มี | ชุดจับยึดแบบแยกส่วนภายใน | ทรงเหลี่ยม |
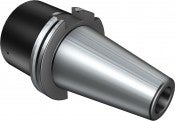
สตีปเทเปอร์
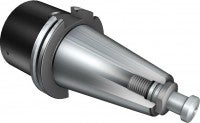
BIG-PLUS®
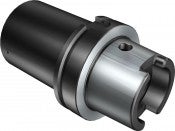
HSK-A
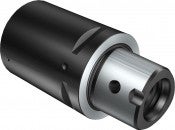
Coromant Capto®
สตีปเทเปอร์ 7/24
สำหรบสตปเทเปอร มมเทเปอรตองเทากน รองยดและเกลยวสำหรบสลกดงอาจแตกตางกนได พรอมรองรบมาตรฐาน CAT, ISO, DIN และ MAS BT
BIG-PLUS®
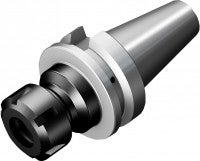
BIG-PLUS® ไดรบการพฒนาสำหรบการใชงานเครองแมชชนนงเซนเตอร เทเปอรและรองยดมคณสมบตเหมอนกบสตปเทเปอรแบบดงเดม แตหนาสมผสทมพกดความเผอตำทำใหมความตานทานการโกงตวสงขน ถงแมวาตวจบยดสตปเทเปอรแบบมาตรฐานสามารถตดตงในสปนเดล a BIG-PLUS® ไดพอด แตไมแนะนำใหใชรวมกน พรอมรองรบมาตรฐาน CAT, ISO, DIN และ MAS BT
HSK
HSK (DIN 69893) ไดรบการพฒนาสำหรบเครองแมชชนนงเซนเตอร ซงมหนาสมผสของหนาแปลนและชดจบยดเทเปอรกลวงแบบแยกสวนทไมจำเปนตองใชสลกดง ลมลอคมรปรางแตกตางกนขนอยกบตวเลอกแตละรน แตในกรณทมการใชงานดวยความเรวสงจะมรปรางไมตางกน
- แบบ A: การตดเฉอนทวไป โหลดทมการโกงตวสงและแรงบดปานกลาง ระบบเปลยนเครองมออตโนมต
- แบบ B: การใชงานแบบอยกบท โหลดทมการโกงตวปานกลาง แรงบดสง การใชงานทมรปแบบพเศษ ระบบเปลยนเครองมออตโนมต
- แบบ C: การตดเฉอนทวไป โหลดทมการโกงตวสงและแรงบดปานกลาง ระบบเปลยนเครองมอดวยตนเอง (อางอง แบบ A)
- แบบ D: การใชงานแบบอยกบท โหลดทมการโกงตวปานกลาง แรงบดสง การใชงานทมรปแบบพเศษ ระบบเปลยนเครองมอดวยตนเอง (อางอง แบบ B)
- แบบ E: การใชงานดวยความเรวสง สปนเดลนำหนกเบาและเรว โมเมนตการโกงตวและแรงบดตำ ระบบเปลยนเครองมออตโนมต การสรางสมดลทงาย
- แบบ F: การใชงานดวยความเรวปานกลาง การตดเฉอนวสดเนอออน โมเมนตการโกงตวและแรงบดปานกลาง ระบบเปลยนเครองมออตโนมต การสรางสมดลทงาย
- แบบ T: การใชงานแบบหมนเครองมอและแบบหมนชนงานโดยมพกดความเผอตำลงในรองขบ (สำหรบการกำหนดตำแหนงเครองมอ) ไมจำเปนตองใช "สวนคอ" จงทำใหโมเมนตการโกงตวดขน
หมายเหต! เครองจกรโดยมากทใชระบบเชอมตอสปนเดล HSK-T ยงคงตองใชสวนคอสำหรบระบบเปลยนเครองมออตโนมตและแมกกาซน กลาวคอยงจำเปนตองใชเครองมอ HSK A/C/T
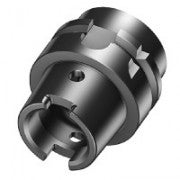
A
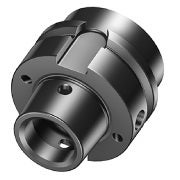
B
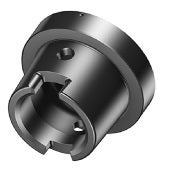
C
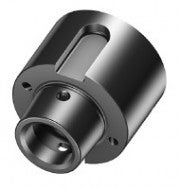
D
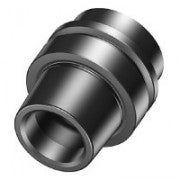
E
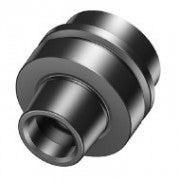
F
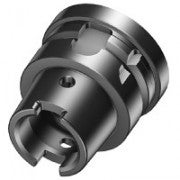
T
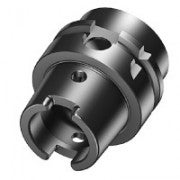
A/C/T
Coromant Capto®
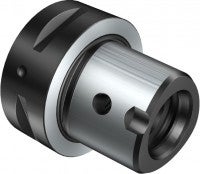
Coromant Capto® (ISO 26623) มีจุดเด่นครอบคลุมข้อดีทั้งของ HSK และของ BIG-PLUS® แต่ทำงานผ่านชิ้นงานทรงเหลี่ยมแบบเทเปอร์ที่มีหน้าสัมผัสได้โดยไม่ต้องใช้ลมล็อค ส่วนหน้าตัดระบบจับยึดที่แข็งแกร่งมีพื้นที่สำหรับชุดจับยึดแบบแยกส่วนพร้อมทั้งแรงจับยึดในระดับสูงสุด จึงมีความต้านทานการโก่งตัว การส่งถ่ายแรงบิด และความแม่นยำของตำแหน่งศูนย์กลางที่เหนือกว่า
ความเที่ยงตรงในแนวรัศมีและการส่งถ่ายแรงบิดที่มีประสิทธิภาพดียิ่งขึ้นเป็นสิ่งสำคัญเพื่อตอบสนองความต้องการและครอบคลุมการใช้งานทั้งสามรูปแบบ ดังนี้:
- ระบบเชื่อมต่อสปินเดลของเครื่องจักร – เครื่องแมชชินนิ่งเซนเตอร์และเครื่องกลึงแนวตั้ง
- ระบบจับยึดแบบถอดเปลี่ยนชิ้นส่วนได้ – เครื่องแมชชินนิ่งเซนเตอร์
- ระบบเครื่องมือแบบเปลี่ยนเร็วด้วยตนเอง – เครื่องกลึง
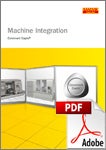
Coromant Capto® เป็นระบบเชื่อมต่อที่ใช้งานได้หลากหลายที่สุดสำหรับเครื่องกลึงกัดหลายแกน และสามารถรับมือกับการทำงานได้ทั้งแบบหมุนชิ้นงาน (การกลึง) และแบบหมุนเครื่องมือ (การกัด/การเจาะ)
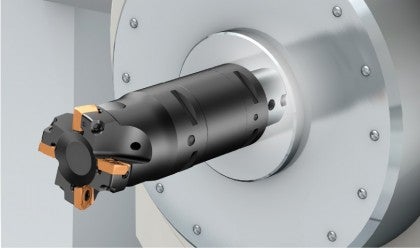
คำแนะนำเกี่ยวกับสปินเดลของเครื่องจักรสำหรับเครื่องจักรประเภทต่างๆ
เครื่องแมชชีนนิ่งเซ็นเตอร์ (เฉพาะแบบหมุน)
ขอแนะนำให้ใช้ระบบเชื่อมต่อสปินเดลที่มีหน้าสัมผัส BIG-PLUS® และ HSK-A มีความมั่นคงดีพอสำหรับการใช้งานแบบหมุนเครื่องมือในเครื่องแมชชีนนิ่งเซ็นเตอร์โดยส่วนใหญ่ สำหรับงานหนัก ควรพิจารณาใช้ Coromant Capto® C10 ก่อนที่จะใช้ระบบจับยึดที่มีขนาดใหญ่กว่า เช่น HSK-A 125 หรือ SK60 สำหรับการใช้งานที่มีความเร็วรอบต่อนาทีสูง ควรพิจารณาใช้ HSK-E หรือ F
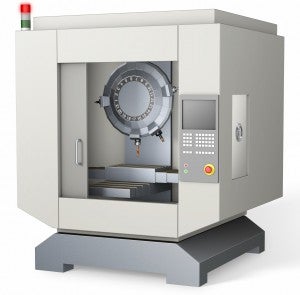
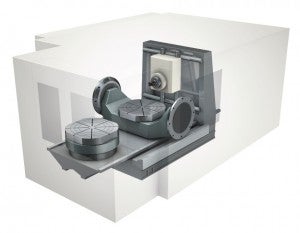
เครื่องจักรแบบมัลติฟังก์ชัน (แบบหมุนชิ้นงานและแบบหมุนเครื่องมือ)
Coromant Capto® เป็นระบบจับยึดเดียวที่สามารถตอบโจทย์ความต้องการด้านแรงบิดและความต้านทานการโก่งตัวสำหรับการทำงานแบบหมุนชิ้นงานและการทำงานแบบหมุนเครื่องมือ
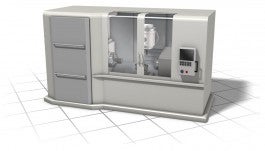
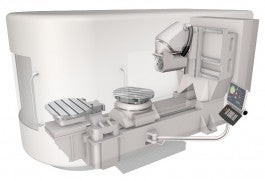
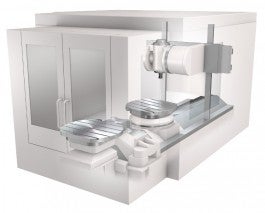
ระบบกลไกของชุดจับยึดสปินเดลและการผลิตระบบเชื่อมต่อสปินเดลมีแตกต่างกัน Sandvik Coromant ทำงานร่วมกับผู้ผลิตเครื่องจักรอย่างต่อเนื่องเพื่อรองรับการผสานรวมระบบ Coromant Capto® เข้ากับเครื่องจักร โดยให้ความสำคัญสูงสุดกับรูปแบบของเครื่องจักรและระบบเชื่อมต่อด้านล่าง ซึ่งระบบจับยึด Coromant Capto® ทำงานได้มีประสิทธิภาพดีที่สุด
C3 | C4 | C5 | C6 | C8 | C10 | |
เครื่องกลึง | * | * | ||||
เครื่องกลึงสำหรับงานหนัก | ||||||
เครื่องกลึงแนวตั้ง | ||||||
เครื่องกลึงกัดหลายแกน | ||||||
เครื่องแมชชีนนิ่งเซ็นเตอร์ที่ทำงานได้ลงตัว | ||||||
เครื่องแมชชีนนิ่งเซ็นเตอร์สำหรับงานหนัก |
* ดามกลึงคว้านขนาดยาวบนเครื่องกลึงขนาดใหญ่
การเปรียบเทียบแรงจับยึด
ชุดจับยึดแบบแยกส่วนภายในที่ใช้กับเทเปอร์กลวง (HSK และ Coromant Capto®) จะมีแรงจับยึดได้สูงกว่าสลักดึงบนสเตปเทเปอร์ ตารางแสดงข้อมูลแรงจับยึดที่ใช้กับระบบเชื่อมต่อประเภทต่างๆ ส่วนหน้าตัดที่เพิ่มขึ้นและความยาวในการจับยึดของ Coromant Capto® จะให้แรงจับยึดที่สูงกว่ามากเมื่อเทียบกับ HSK-A
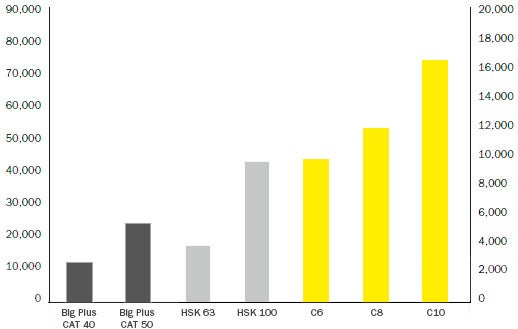
ที่มา: คู่มือ HSK, ลิขสิทธิ์ 1999
Big Daishowa (ระบบสปินเดล Big plus)
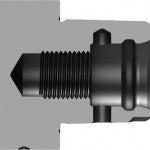
Coromant Capto®
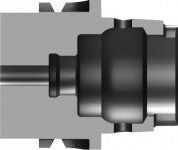
HSK-A
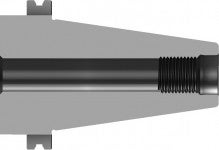
สเตปเทเปอร์ (SK)
การส่งถ่ายแรงบิดและความต้านทานการโก่งตัว
สเตปเทเปอร์ – ล็อคบนรัศมีกว้างช่วยให้เกิดการขับเคลื่อนได้ดีสำหรับการใช้งานแบบหมุนเครื่องมือ
HSK-A – พื้นที่หน้าสัมผัสขนาดเล็กและมีร่องบนเทเปอร์มากกว่าเส้นผ่านศูนย์กลางหน้าแปลน (รัศมีแคบ) จึงไม่แนะนำสำหรับการใช้งานที่มีแรงบิดสูง
Coromant Capto® – สำหรับการกลึงที่จำเป็นต้องมีความแม่นยำในการวางตำแหน่งศูนย์กลางในกรณีที่ตัวขับทรงเหลี่ยมมีประสิทธิภาพดีที่สุด
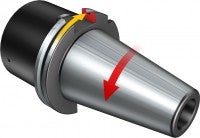
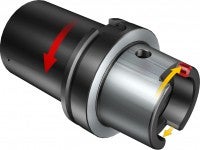
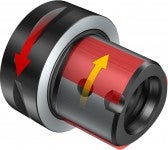
ขนาดของระบบจับยึดจะเป็นปัจจัยที่จำกัดความต้านทานการโก่งตัวและความเร็วรอบสูงสุดต่อนาที ระบบจับยึดขนาดใหญ่จะมีความทานทานดีเยี่ยมแต่ความเร็วรอบต่อนาทีต่ำกว่า ขณะที่ระบบจับยึดขนาดเล็กมีความเร็วรอบต่อนาทีสูงกว่าแต่มีความต้านทานการโก่งตัวที่ต่ำกว่า
แผนภาพด้านล่างแสดงข้อจำกัดการทำงานสำหรับระบบจับยึดโดยเฉพาะจากการคำนวณตามหลักทฤษฎี (FEA) เมื่อมีการสูญเสียหน้าสัมผัส (ความต้านทานการโก่งตัว) และเมื่อถึงจุดที่มีความทนทานต่อการล้า (แรงบิดสูงสุด)
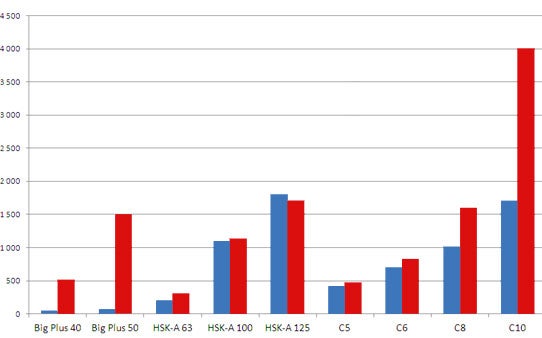
สีฟ้า: โมเมนต์การโก่งตัวสูงสุด (นิวตัน-เมตร)
สีแดง: แรงบิดสูงสุด (นิวตัน-เมตร) ในช่วงที่มีความทนทานต่อการล้า
BIG-PLUS® และ HSK มีความมั่นคงดีพอสำหรับการใช้งานแบบหมุนเครื่องมือ แต่สำหรับเครื่องกลึงกัดหลายแกน Coromant Capto® เป็นระบบจับยึดหนึ่งเดียวที่สามารถตอบโจทย์ความต้องการด้านแรงบิดและความต้านทานการโก่งตัว
คลัป | ขนาดและประเภทการจับยึด | แรงหนีบ (ดึงสตั๊ดหรือแถบดึง) | รอบต่อนาทีสูงสุด (ขึ้นอยู่กับแกนหมุนและแบริ่ง) | |
N | ปอนด์ | |||
BIG-PLUS® ISO/CAT/BT 7/24 เรียว | เทเปอร์ 40 | 12000 | 2703 | 16000 |
เทเปอร์ 50 | 24000 | 5405 | 12000 | |
เอชเอสเค-เอ | เอชเอสเค-เอ 63 | 18000 | 4054 | 20500 |
เอชเอสเค-เอ 100 | 45000 | 10135 | 12500 | |
เอชเอสเค-เอ 125 | 70000 | 15766 | 9500 | |
Coromant Capto® | ซี 5 | 32000 | 7207 | 28000 |
ซี 6 | 41000 | 9234 | 20000 | |
ซี 8 | 50000 | 11261 | 14000 | |
ซี 10 | 70000 | 15766 | 10000 |
การทดสอบแบบคงที่สำหรับเปรียบเทียบความต้านทานการโก่งตัวและความต้านทานแรงบิด
มหาวิทยาลัย RWTH Aachen ที่มีชื่อเสียงในประเทศเยอรมนีได้ทำการทดสอบแบบคงที่อย่างต่อเนื่องในห้องปฏิบัติการด้านเครื่องจักร (WZL) เพื่อเปรียบเทียบความต้านทานการโก่งตัวและความต้านทานแรงบิดของระบบเชื่อมต่อสปินเดลแต่ละประเภท
และทำการวัด Coromant Capto® โดยใช้แรงจับยึดสองค่า: เท่ากับ HSK-A, (22 kN สำหรับ C6 และ 50 kN สำหรับ C10) จากนั้นใช้แรงจับยึดมาตรฐานสูงขึ้น (45 kN สำหรับ C6 และ 80 kN สำหรับ C10)
ความมั่นคงต่อการโก่งตัว
การเบี่ยงเบน [มม./ม.]
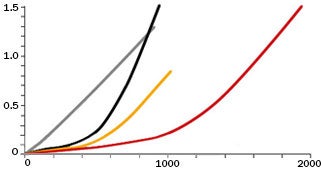
โมเมนต์การโก่งตัว [นิวตัน-เมตร]




C6- 45kN
C6- 22kN
HSK-A 63- 22kN
เทเปอร์ 7/24, ขนาด 40-15kN
ความมั่นคงต่อการโก่งตัว
การเบี่ยงเบน [มม./ม.]
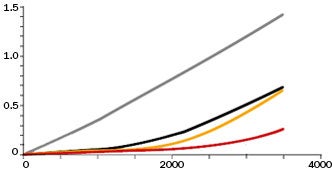
โมเมนต์การโก่งตัว [นิวตัน-เมตร]




C10- 80kN
C10- 50kN
HSK-A 100- 50kN
เทเปอร์ 7/24, ขนาด 50-25kN
ผลการทดสอบแสดงให้เห็นว่าเมื่อมีแรงจับยึดเท่ากับ HSK-A ระบบจับยึดที่แข็งแรงกว่าจะช่วยให้ความต้านทานการโก่งตัวดีขึ้น แต่เมื่อมีแรงจับยึดสูงขึ้น ระบบจับยึด C6 จะมีแรงผลักดีกว่า 2.88 เท่าเมื่อเทียบกับ HSK-A 63 และระบบจับยึด C10 ดีกว่า 2.15 เท่าเมื่อเทียบกับ HSK-A 100
ความมั่นคงต่อแรงบิด
การเบี่ยงเบน [มม./ม.]
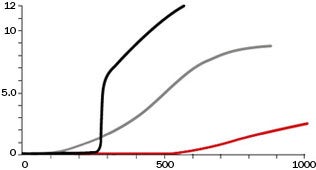
โมเมนต์การบิดตัว [นิวตัน-เมตร]



C6- 46kN
HSK-A 63- 22kN
เทเปอร์ 7/24, ขนาด 40-15kN
ความมั่นคงต่อแรงบิด
การเบี่ยงเบน [มม./ม.]
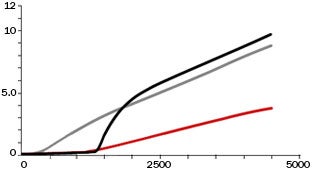
โมเมนต์การบิดตัว [นิวตัน-เมตร]



C10- 50kN
HSK-A 100- 50kN
เทเปอร์ 7/24, ขนาด 50-25kN
กราฟด้านบนแสดงให้เห็นว่าระบบ Coromant Capto C6 มีความต้านทานแรงบิดสูงกว่าระบบ HSK-A 63 ถึง 2.29 เท่า โดยมีองศาที่ต้านการบิดตัวดีกว่าถึง 7.1 เท่า และเมื่อเปรียบเทียบโดยใช้ C10 ความต้านทานแรงบิดจะดีกว่า 1.85 เท่า และมีองศาที่ต้านการบิดตัวดีกว่า HSK-A 100 4.0 เท่า
ระบบเครื่องมือแบบถอดเปลี่ยนชิ้นส่วนได้
ระบบเครองมอแบบถอดเปลยนชนสวนไดชวยใหสามารถประกอบเครองมอไดตามตองการสำหรบการทำงานในรปแบบตางๆ... keyboard_arrow_right
CoroBore® BC
เลอกการทำงานไดมากถง 4 รปแบบในอปกรณชนเดยวทออกแบบมาโดยเฉพาะ ใชคมตดไดสงสดสองชดตอขนตอนการทำงาน ชวงเสนผานศนยกลาง: 25‒200... keyboard_arrow_right
การกัดบ่าฉาก
การปฏบตงานกดบาฉากประกอบไปดวย: การกดบาฉาก/ กดปาดหนา การกดขอบขาง การกดบาฉากผนงเบยงแบบบาง การกดบาฉาก/... keyboard_arrow_right
CoroDrill® DS20
ทำการตดเฉอนไดอยางมนใจและเชอถอไดดวยประสทธภาพการผลตระดบสงและเสนผานศนยกลางทสมำเสมอ ดอกสวานทดเยยมพรอมใหการรองรบชวงของคาการตดไดอยางครอบคลม... keyboard_arrow_right