Udvendig sporstikning
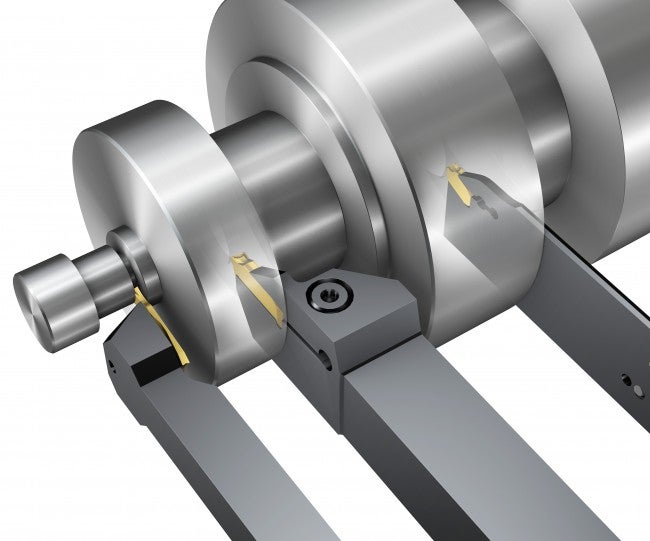
Målsætningen ved sporstikning er høj produktivitet. Udvendig sporstikning er generelt mindre krævende end afstikning, og derfor er det lettere at opnå processikkerhed. Derfor kan man i stedet fokusere på at forbedre produktiviteten, især ved bearbejdning af brede spor, da de tager længere tid og påvirker komponentens samlede bearbejdningstid mere end små spor.
Metoder til udvendig sporstikning
Ved dybe spor kan processikkerhed være en udfordring som følge af de lange udhæng der kræves, vanskeligheder med spånafgang og vanskeligheder med at sikre kølevæsken adgang til skærkanten. Enkeltsporsstikning er den mest økonomiske og produktive metode at lave spor. Men hvis sporets dybde er større end skærets bredde kan der bruges flersporsstikning, indstikning, ramping eller profildrejning til at lave sporet. Til udvendig sporstikning er et værktøj med præcisionskølevæske førstevalg.
Applikationstips: sådan anvender du udvendig sporstikning
Enkeltsporsstikning
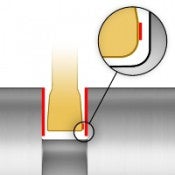
Enkeltsporsstikning er en økonomisk og produktiv metode at lave spor. Ved enkeloperation skal der tages højde for følgende:
- Hvis overfladekvaliteten er meget vigtig, skal der bruges skærgeometri med Wiperteknologi
- Sørg for at bruge skær med snævre tolerancer, de rette hjørneradier og den rette bredde. Det anbefales at bruge slebne skær (f.eks. -GF)
- Brug et skær med korrekt profil og fas til masseproduktion. Hvis skæret ikke er en del af standardsortimentet, er det værd at investere i applikationstilpassede skær
Skrubbearbejdning af brede spor
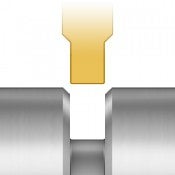
De mest almindelige metoder til fremstilling af brede spor eller drejning mellem hjørner er:
- Flersporsstikning
- Indstikning
- Ramping
Alle tre metoder er skrubbearbejdningsoperationer, der skal efterfølges af en separat sletbearbejdningsoperation.
Tommelfingerregel: Hvis sporets bredde er mindre end dybden, skal du bruge flersporsstikningsmetoden. I modsat fald skal du bruge indstikning. Til slanke komponenter kan der bruges metoden ramping.
Flersporsstikning
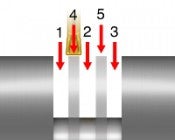
- Til dybe, brede spor (dybden større end bredden)
- Flangerne der efterlades til afsluttende overløb (4 og 5) skal være tyndere end skærbredden (CW -2 x hjørneradier)
- Øg tilspændingen med 30-50 %, når du bearbejder flanger
- Førstevalgsgeometrien er -GM
Indstikning
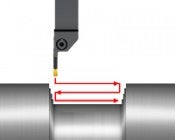
- Til bredere og fladere spor (bredden større end dybden)
- Tilspænd ikke mod hjørnet
- Førstevalgsgeometrier er -TF og -TM
Ramping (drejning/profildrejning)
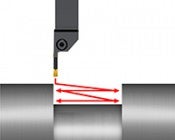
- Optimal spånkontrol
- Minimer radial skærekraft og stråleslid
- Førstevalgsgeometrier er -RO og -RM
Sletdrejning af et spor
- Mulighed 1: Brug en drejegeometri
- Mulighed 2: Brug en profildrejningsgeometri, f.eks. til spor med store radier
- Anbefalet aksial og radial spåndybde 0,5-1,0 mm (0,02-0,04 tomme)
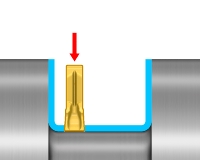
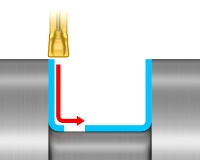
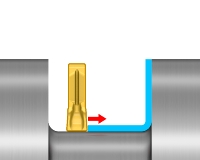
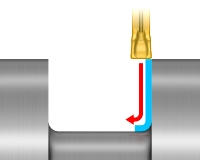
Drejning og udvendig sporstikning
Drejning med af- og sporstikningsskær
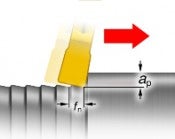
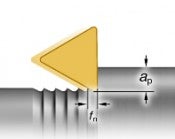
- Brug en spåndybde (ap), der er større end skærets hjørneradier, til kantdrejning
- Wipereffekt − tilspændingshastighed pr. spåndybde (fn/ap) skal være relativ høj for at sikre en let nedbøjning af værktøj og skær. Det skaber frigang mellem skærkanten og den bearbejdede overflade
- For lav fn/ap medfører værktøjsgnidning, vibration og dårlig overfladekvalitet
- Maks. ap = 75 % af skærbredden
Overfladekvalitet | |||||
Ra µm | |||||
![]() | |||||
Tilspænding, fn mm/o. tommer/o. |
![]() | TNMG 160404 |
![]() | TNMG 160408 |
![]() | P&G-skær -5 mm -RM |
![]() | P&G-skær -4 mm -TF |
![]() | P&G-skær -6 mm -TM |
Diagrammet viser overfladekvaliteten for af- og sporstikningsskær sammenlignet med et TNMG-skær med en 04- eller 08-hjørneradius.
Drejning af et spor
Ved sidedrejning skal værktøj og skær afbøje lidt. Men for meget bøjning kan forårsage vibrationer og brud:
- Et tykkere blad nedsætter bøjningen
- Et kortere udhæng (OH) nedsætter bøjningen (δ)
- Undgå drejeoperationer med lange og/eller tynde værktøjer
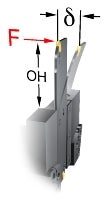
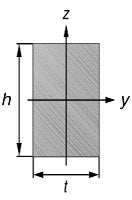
Et kortere udhæng nedsætter bøjningen sideværts
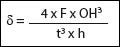
Fridrejning og udvendig sporstikning
Mange komponenter kræver slibning eller gevinddrejning. Der er brug for frigang for at kunne slibe eller skære gevind ind i et hjørne. Vi anbefaler derfor at bruge skær, der er beregnet til fridrejning. Eksempel: T-Max Q-Cut® og CoroCut® 1-2
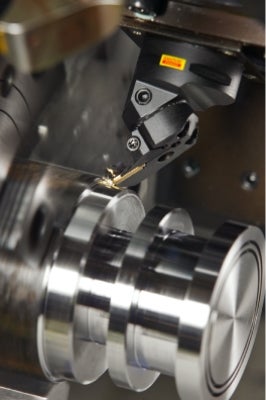
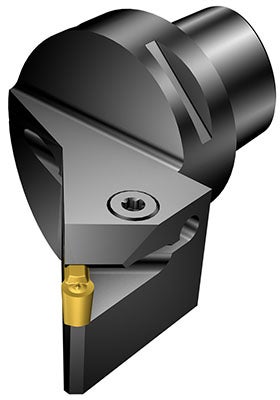
Af- og sporstikning
I af- og sporstikning er processikkerhed og produktivitet to vigtige aspekter. Med... chevron_right
Indvendig sporstikning
Lange udhæng og dårlig spånafgang er to udfordringer ved indvendig sporstikning.... chevron_right
Sporstikning af profiler
Sporstikning af profiler anvendes til at fremstille komplekse spor. Adgangen til... chevron_right
Aksialsporstikning
Ved bearbejdning af et aksialspor på enden af en komponent er det vigtigt at vælge... chevron_right