旋削加工
製品概要
ボーリングバイトの選定は、生産コストに大きな影響を及ぼします。サンドビック・コロマントの工具は広範をカバーしており、24時間以内に納品される標準在庫工具として、φ10 ~100 mm(φ0.40~9.84inch)までのソリューションをご用意しています。上記の寸法範囲を超える場合は、最大600 mm径(φ23.6inch)までの特注工具をご注文いただけます。
突出し量が3-14 x BDのバイトをご注文いただけます。 コロマントキャプトの場合は、φ16~100 mm(φ0.63~3.94inch)までのサイズになります。
短い突出し量で高い生産性
突出し量が4 x BD以下の場合、一般的に鋼または超硬のボーリングバイトを使用することができます。ただし、この範囲内でも、サイレントツールのバイトは生産性を高めるための非常に有利な効果を発揮します。突出し量が最大10 x BDまでの場合に十分な効果を得るには、通常、鋼防振ボーリングバイトを使用することで問題が解決されます。突出し量が10 x BDを超える場合は、超硬補強防振ボーリングバイトで径方向のたわみとびびりに対応する必要があります。
ボーリングバイト径、DMM | ||||
inch | ||||
![]() | ![]() ![]() | |||
最大突出し量 | ||||
鋼防振型 ボーリングバイト | 超硬補強 防振ボーリングバイト |
![]() | 特注品 | |
![]() | コロターンSL – QC | |
![]() | コロターンSL | |
![]() | 一体型 |
カッティングヘッドとサイレントツールの防振ボーリングバイトの組み付けは、チップシートに損傷があれば、ヘッドだけを簡単に交換することができます。
一般旋削加工、突切り加工、溝入れ、ねじ切りに使用できる約500種類のカッティングヘッドを総合的に取り揃えています。これには、φ32~80 mm(φ1.26~3.15icnh)のクイックチェンジQSが含まれています。また、コロターンHPカッティングヘッドも用意しています。
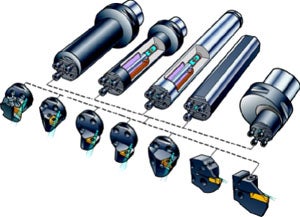
カッティングヘッドとサイレントツールの防振ボーリングバイトを組み合わせることにより、カッティングヘッドがさまざまな加工に柔軟に対応できるようになるため、優れた効果を発揮します。
大径の円筒シャンクタイプのボーリングバイトは、コロマントキャプトおよびクイックチェンジカップリングユニットなどの複数の異なるカップリングに入ります。
コロターンSL
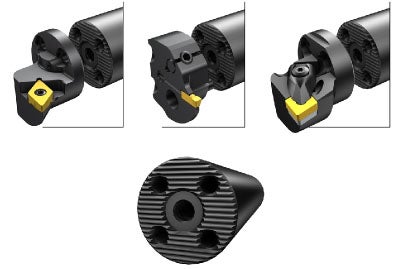
クイックチェンジQS
![]() | ![]() |
![]() | |
![]() |
バイトタイプ
内径旋削加工はびびりに非常に敏感です。工具突出し量をできるだけ小さくし、できるだけ大きな工具サイズを選択し、最適な剛性と精度を実現してください。鋼防振ボーリングバイトで内径旋削加工を行う場合の第一推奨は、570-3Cタイプのバイトです。
送り分力が旋削加工より大きい場合の溝入れおよび荒ねじ切り用の推奨バイトタイプは570-4Cです。
下表には、異なるバイトタイプの最大推奨突出し量が掲載してあります。
超硬補強バイトの静的剛性は、同じ突出し量の鋼バイトより約2.5倍アップしています。
異なる突出し長さに対応したさまざまな防振機構があります。
バイトタイプ | 旋削加工 | 溝入れ加工 | ねじ切り加工 | |
鋼ボーリングバイト | 4 x BD | 3 x BD | 3 x BD | |
超硬ボーリングバイト | 6 x BD | 5 x BD | 5 x BD | |
鋼防振 ボーリングバイト | ![]() | 10 x BD | 5 x BD | 5 x BD* |
超硬補強 防振ボーリングバイト | ![]() | 14 x BD | 7 x BD | 7 x BD |
______________________________________________________________
* 570-4Cバイト
加工に適した長さ・径のボーリングバイトを選定します。超硬バイトの静的剛性は鋼バイトより高いため、大きな突出し量での加工が可能です。
図のように、適切な長さ・径の以下のボーリングバイトを選択することができます。
ねじ切りと溝入れは、旋削加工より大きな背分力が発生します。このため推奨最大突出し量が限定されます。防振機構は動的剛性を高め、大きな突出し量での加工を可能にします。
1 = 鋼ボーリングバイト | |
2 = 超硬ボーリングバイト | |
3 = 鋼防振ボーリングバイト、 ショートタイプ(4–7 x BD) | |
4 = 鋼防振ボーリングバイト、 ロングタイプ(7-10 x BD) | |
5 = 超硬補強防振 ボーリングバイト (10–12 x BD、12–14 x BD) |
加工概要
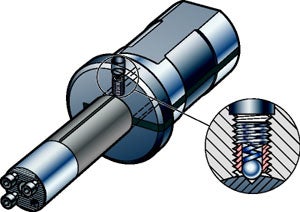
安定したクランプ方法と適切な心高という2つの要素は、適切な寸法公差と加工面品質を得るために重要です。円筒シャンクボーリングバイトをスプリットスリーブホルダでクランプして、接触面積を最大にします。イージーフィックススリーブは、最も安定したクランプ方法と最も正確な心高の位置決めを実現することができます。心高は、工具のすくい角と切削抵抗の両方に影響を及ぼします。
推奨クランプ公差はISO H7です。また、45 HRC以上のスプリットブッシュ材を使用して変形を長期的に回避することも推奨します。絶対にスクリューでバイトシャンクを直接押さえた状態では使用しないでください。スクリューでバイトが損傷することがあります。
突出し量が長い加工では、適切なクランプはあまり期待できません。
ボーリングバイト – 概要
- 十分なクランプ接触を実現するには、約 1 µmまでの加工面品質が必要になります。
- 推奨クランプ長さは4 × BDです。ボーリングバイトが200 mm(7.87inch)を超える場合は、できるだけ6 × BDのクランプ長さを使用することを推奨します。
- 円筒シャンクボーリングバイトはスプリットスリーブに取り付けます。推奨クランプ公差はISO H7です。
- スプリットブッシュ材は、変形を長期的に回避するために、45 HRC以上の硬度が必要です。
- 大きなバイトの場合、ダブルベアリングキャップを使用します。
- 安定した最適なクランプ方法を実現するには、スプリットボーリングバイトホルダを使用します。
部品の構造と寸法に基づいて、ボーリングバイトの径と長さを決定します。安定した最適なクランプ方法を実現するための第一推奨は、コロマントキャプトカップリングかスプリットスリーブです。加工径と、底面までの長さによって、使用するべきボーリングバイトのタイプが決まります。
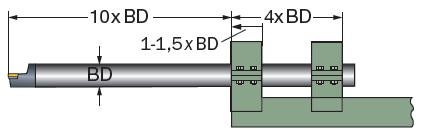
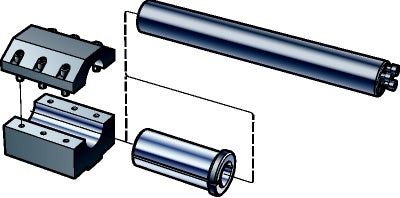
サイレントツールのクランプ方法
タレット構造であるCNC旋盤や、さまざまな加工に柔軟性のある複合加工機は、通常は剛性が低くなります。タレット幅が小さいと、クランプ長さと大きな円筒シャンクボーリングバイトのバイト径との比率が下がり、その結果としてセットアップ剛性が低下します。
また、コロマントキャプトカップリングは、タレット旋盤のソリューションにもなります。これにより、スリーブの長さが最短になり、クイックチェンジの利点と相まって安定したセットアップを実現します。
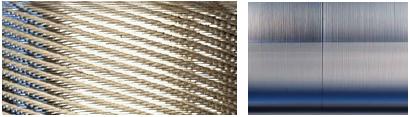
適切に工具をクランプすることは非常に重要です。写真は、
1) クランプ方法が適切でなかったときの加工面と、2) スプリットホルダによるクランプ方法を使用したときの加工面を示しています。
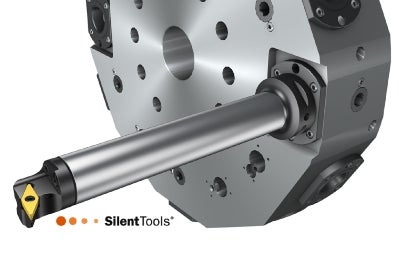
平ベッド旋盤
ツールポスト付きの平ベッド旋盤は、タレット旋盤より頑丈で、安定していることが多く、長くて大きなボーリングバイトを固定することができます。この場合の機械の限界はツールポスト、機械の寸法、構造上の剛性になります。
突出し量の長いサイレントツール(防振ボーリングバイト)で良い加工結果を得るには、機械のスライドとジブの剛性が重要な要素です。最高の結果を得るには、ツールポストのクランプを、クロスジブが大きく広がった構造の大型ジブで行う必要があります。クランプ長さは4 x BD以上です。バイトサイズが大きくなると、重量が著しく増えることにご留意ください。。
- φ100 mm(3.94 inch) = 88 kg(194.0lb)
- φ120 mm(4.72 inch) = 140 kg(308.7lb)
最適なツールポストの構造は、バイトを機械のスライドすぐかつスライド間に取り付けられるA型フレームです。 | ![]() |
ボーリングバイトの最適な性能を引き出すには、工具とツールホルダとの接触状態、構造、および寸法公差が重要な要素です。バイトが完全に包み込まれるようクランプされるホルダを使用することで、最高の剛性が得られます。スクリュー付きのV型バイトホルダとスクリュー付きの円筒シャンクホルダは推奨しません。
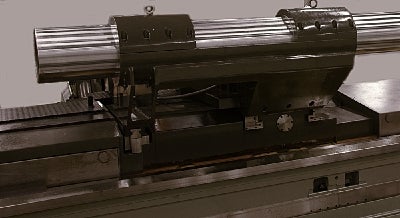
バイト径300 mm(11.81インチ)用のスプリットホルダです。クロススライド間の距離は1,200 mm(47.24インチ)(4 x BD)です。
心高調整用ツール すべてのコロターンSL円筒シャンクバイトについては、心高を正確に素早く調整できるシンプルな方法があります。
バイトが加工中に中心から下に少しずれても、バイトの適切な取付位置は中心線上にあります。 別の調整ツールとしては、ハイトゲージとクロステストレバーがあります。 | ![]() | |
![]() | ||
![]() |
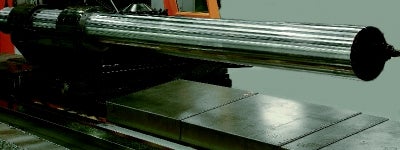
突出し量10 x BDの、防振型300 mmコロターンSLクイックチェンジ式ボーリングバイト
圧力と方向
最高の工具寿命と加工安定性を実現するには、刃先に吐出されるクーラントが有効です。SLクイックチェンジ式ヘッドが装備された工具の場合は、クーラントを確実に刃先に当てるために、クーラントノズルを手動調整する必要があります。最高の結果を得るためには、複数のノズルを持つ内部給油工具を使用します。突出し量の長い内径旋削加工の場合にもこれは重要です。クーラントのオン/オフは、六角レンチを使用して行います。
ボーリングバイトから穴の内側までのクリアランスは、切りくずの排出と径方向のたわみを回避するために極めて重要です。加工径が100 mm(3.94 inch)の場合、使用可能なバイトは80 mm(3.15 inch)です。これで切りくず排出に十分なクリアランスが確保できるため、工具と部品の損傷を防ぐことができます。
クーラントは、英国パイプ(BSP)規格準拠の取付ねじ付きの、市販サイズのコネクタを使用して、ボーリングバイトの先端から噴射することができます。サンドビック・コロマントの防振ボーリングバイトには、クーラント穴が装備されています。
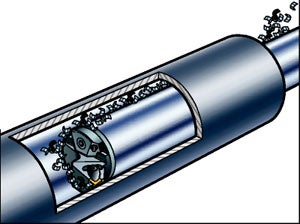
びびりに影響する要素
びびり傾向を最小限に抑える方法:
- 大きな切込角とポジティブなすくい角を使用します。
- 小さなノーズRと刃先角を使用します。
- ポジティブな工具形状を使用します。
- 刃先形状の摩耗パターンとホーニング処理を管理します。
- 切込みはノーズRより大きくする必要があります。
送り分力が小さいほど、径方向のたわみが少なくなり、びびりによる不具合も少なくなります。最高の結果を得るには、90°の切込角(リード角: 0°)を使用する場合は、ノーズRより大きな径方向切込みを使用します。径方向切込みが小さい場合は、45°の切込角でも同様の結果が得られます。
![]() | びびり傾向 |
切込角 | |
リードアングル | |
ノーズRと刃先角 mm(inch) | |
工具形状 | |
刃先形状 | |
ノーズRに対する切込み |
切削抵抗の方向を変えることでたわみを軽減できることを忘れないでください。
- 切込角をできるだけ90°(リード角: 0°)に近づけると、ワークからの軸方向送り分力の部分が最大になります。軸方向の力の方が、径方向にかかる力と比べると、工具たわみに与える影響が少ないです。
- 内径旋削の場合は、絶対に切込角を75°(リード角: 15°)より小さくしないでください。
- すくい角をよりポジティブにすると、加工の切削抵抗は小さくなります。切削抵抗が小さいということは、たわみが少ないことを意味します。
- 径方向の抵抗が小さいと、径方向のたわみも少なくなります。
![]() | ![]() | |
![]() | ![]() | |
力の作用方向:主に軸方向 | 力の作用方向:軸方向と径方向の両方 | |
![]() | ![]() | |
ネガティブなすくい角: 切削抵抗が大きくなる | ポジティブなすくい角: 切削抵抗が小さくなる |
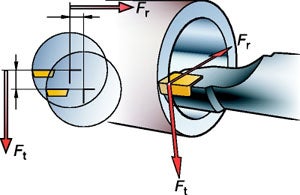
F
t
= 接線分力(主分力)、Fr = 送り分力
刃先角
チップ形状は、工具の切込角と近接性の条件に応じて選択します。1つの目安は、びびり傾向を抑えるために、常にできるだけ小さなノーズRを選定することです。刃先角に関しては、2つの選択肢があります。
- チップの刃先角が小さいと、工具の剛性がアップします。工具が径方向に振動し始めても、加工面とのクリアランスは十分に確保され、切りくず断面積の変化は小さくて済みます。
- チップの刃先角が大きいと、切刃の強度と信頼性が生まれます。ただし、大きな切刃をワークにかけると、その分大きな切削動力が必要になります。
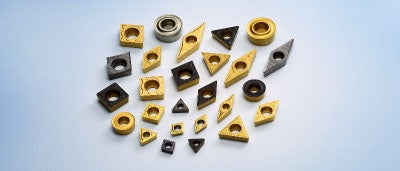
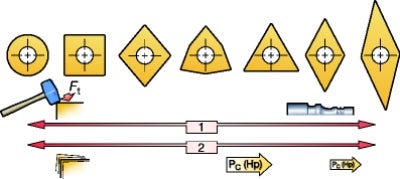
ポジブレーカ
ポジブレーカとポジティブなすくい角によって、切削抵抗を小さくして、工具のたわみを軽減します。したがって、使用する切削条件に適したチップブレーカと一緒に、できるだけ最もポジティブな形状を選択します。このため、耐摩耗性と刃先強度が弱くなるだけでなく、切りくず処理能力も低下することがあります。びびりは常にバランス良く管理されます。
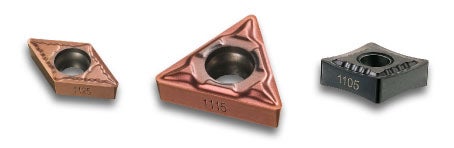
ワイパーチップ
びびりの回避という点では、基本的にワイパーチップは第一推奨ではありません。切削抵抗と径方向のたわみが大きくなるためです。ただし、非常に安定した条件の場合は、ワイパーチップが加工面品質で大きな利点を発揮し、高い切削条件での加工が可能です。
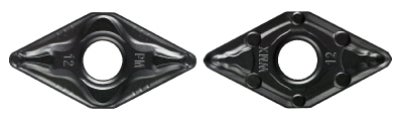
ホーニング ホーニング(ER)が小さいと、あらゆる方向の切削抵抗が小さくなります。つまり、切削アクションが容易になり、工具のたわみが小さくなります。研磨チップのホーニングはダイレクトプレスチップより小さくなっています。同様にノンコートチップまたは薄膜コーティングチップもホーニングが小さくなります。 | ![]() |
![]() | ![]() | ![]() | ||
M = ダイレクトプレスチップ | G = 研磨チップ、通常はホーニング(ER)が小さい | E = 公差の厳しい、シャープエッジ用の研磨チップ |
切削条件
逃げ面摩耗などの過度のチップ摩耗は、絶対に回避しなければなりません。工具とワーク加工面とのクリアランスが変化し、びびりによる不具合が発生する可能性があるからです。
![]() | ![]() |
![]() |
切削速度(vc)
切削速度が適切な場合は、加工面品質、切削抵抗、および工具寿命に影響を及ぼす構成刃先が回避されます。
- 切削速度が早すぎると、逃げ面摩耗を発生させることがあります。逃げ面摩耗は、特に深穴加工で、切りくずの詰まり、不十分な切りくず排出、チップの欠損を発生させ、安定性や信頼性を低下させます。
- 切削速度が遅すぎると、構成刃先が発生します。
- 摩耗パターンが均一でない場合は、工具寿命と加工面品質が低下しますので、摩耗パターンには十分にご注意ください。
- ワーク被削材は切削速度と大きな関連性があります。
切込み(ap)と送り(fn)
切込み(ap)と送り(fn)の組み合わせは最善の切りくず断面積のための大切な要素です。2つの目安:
- ノーズRより大きな切込み(ap)を設定します。
- 求められる加工面品質によって異なりますが、ノーズRの最低25%以上の送り(fn)をプログラムします。
突出し量の長い加工でびびりが発生したとき最初に検討すべきポイントは、送りを上げることです。次に、切削速度を変更することです。通常は切削速度を上げることで、良好な結果が得られます。
切りくず断面積
- 切りくず断面積が大きすぎる場合は、切削抵抗が大きすぎます。
- 切りくず断面積が小さすぎる場合は、工具とワークとの摩擦が非常に大きくなり、摩擦の影響が発生する可能性があります。
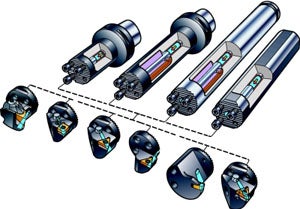
加工のヒント
できるだけ大きなバイト径で、できだけ小さな突出し量の工具を選定することによって、びびり発生リスクを低減します。推奨クランプ長さ=4 x BD以上を守って使用してください。
突出し量10 x BDを超えて防振CRボーリングバイトを突切り加工に使用することはできません。570-4Cバイトの場合は、防振機構の上をクランプすることができますが、3Cバイトの場合はできません。570-3Cショートタイプボーリングバイトを最小長さに切断する場合、防振機構の上でクランプすることを避けるために、3 x BDを超える長さをクランプしないでください。径が100 mm(3.94インチ)を超える570-3Cバイトは決して切断しないでください。
標準バイトの修正
バイト径 | L、切断後の最小長さ | |
BD | ショートタイプ 4–7 × BD | ロングタイプ 7–10 × BD |
mm | mm | mm |
16 | 100 | 155 |
20 | 125 | 200 |
25 | 155 | 255 |
32 | 190 | 320 |
40 | 240 | 410 |
50 | 305 | 520 |
60 | 380 | 630 |
80 | 630 | 630 |
100 | 770 | 770 |
推奨最小クランプ長さ: 4 × BD
バイト径 | L、切断後の最小長さ | |
BD | ショートタイプ 4–7 × BD | ロングタイプ 7–10 × BD |
inch | inch | inch |
0.625 | 4 | 7 |
0.750 | 5 | 8 |
1.000 | 7 | 11 |
1.250 | 8 | 13 |
1.500 | 10 | 17 |
1.750 | 10.4 | 18 |
2.000 | 12 | 21 |
2.500 | 15 | 25 |
3.000 | 20 | 20 |
4.000 | 30.3 | 30.3 |
推奨最小クランプ長さ: 4 × BD
ボーリングバイトに記載されている2行は、最小および最大突出し量を示しています。突出し量がその範囲内に入っていることを確認してください。この範囲から外れている場合は、防振機能は保証されません。
切りくず排出
最適な切りくず排出を実現するには、内部給油付きのツールホルダとチップブレーカを使用して、短い螺旋状の切りくずを発生させます。切りくず排出が不十分な場合は、クーラントの流量を上げる、チップブレーカを交換する、あるいは切削速度を上げるなどの方法で、短い切りくずが出るように試してください。
もう1つのオプションは、別のツールパスを検討することです。逆向きに
切削することで、実際に切りくず排出を改善することができます。
バイトと穴のあいだに切りくずが排出できる余裕が十分にあることを確認してください。クリアランスが不十分な場合は、切りくずが工具によって加工面に押し付けられ、工具本体も損傷する可能性があります。
![]() | ![]() |
ノズルの調整
クーラントフローのオン/オフは、六角レンチを使用して行います。SLクイックチェンジヘッドの場合、同じ六角レンチを使用してノズルの方向も調整します。
ワイパーチップ
加工面品質と生産性を向上させるとき、非常に安定した条件の場合は、ワイパーチップが最適チップになる可能性があります。ワイパーチップを使用する場合の一般的な推奨事項は、送りを上げて、小さなノーズRを選択することです。
内径ねじ切り加工
びびりの発生リスクを下げるには、以下のヒントを活用してください。
- 修正逃げ面送りを使用する。
- パス当りの切込みは0.06 mm(0.0024inch)~0.2 mm(0.0078inch)の値にする。
- 最終パスは、常に低い切込み速度で行う。
- シャープなチップブレーカを使用して、できるだけ切削抵抗を小さくする。
最高の切りくず排出のためには:
- 修正逃げ面送りを使用して、螺旋状の切りくずを穴の開口部に送ります。
- 安定した条件では内から外への送り方向を使用します。左または右の逃げ面を選択して、切りくずの流れを進めます。
- クーラントを使用して、最高の切りくず排出を実現します。
切りくず方向 | 送り方向 | ||
![]() | ![]() | ||
内から外への送り方向 | 修正逃げ面送りにより、切りくずは穴から外側に向かいます。 |
内径溝入れ・倣い加工
びびりの発生リスクを下げるには、以下のヒントを活用してください。
- セットアップの際は突出し量をできるだけ短くして、なるべく軽切削ブレーカを使用する。
- 小さなチップを使用し、1パスで切削する代わりに複数回に分けて切削を行う。
- 最高の切りくず排出を得るには、外側から始めて、内側に向かって重複して切削を行う。
- 仕上げ加工は側面旋削加工になる可能性がある。内側から開始して、
外側に向かって切削する。 - ランピング加工/旋削加工は切りくず処理を改善するが、同時にびびりを軽減させることがある。
- 荒加工の場合に、勝手付きチップを使用して切りくずを移動させる。
一般的なセットアップ
一般的にバイトを回転させると、切削抵抗が発生して、チップを下方向に押し付けます。
その他のセットアップ
バイトを上下逆さに取りつけると、切削抵抗の方向が変わり、剛性がアップします。また、切りくず排出も改善されます。この方法は、小径加工の場合でも慎重に検討する必要があります。断続切削によって切削抵抗が0まで下がった場合、バイトは加工方向に跳ね返り大きな切削抵抗を受けるため、工具も部品も損傷する可能性があります。
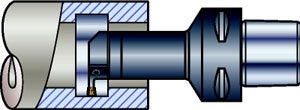
管理
最高の性能を得るために、少なくとも年に1回はすべての部品を洗浄して、オイルを塗布します。また、必要に応じてスクリューにも潤滑油を塗布する必要があります。摩耗または疲弊したスクリューやワッシャーは交換します。
防振バイトは薄肉のため、変形することがあります。組み付ける場合は、バイトが正しく固定されていることを確認します。サイレントツール製品を併用する場合は、必ずクランプ状態をチェックします。トルクレンチを使用して、適切にスクリューを締め付けます。
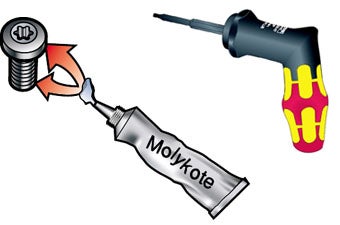
まとめ:びびりの回避方法
静的剛性を上げる
- クランプ状態とセットアップ状態をチェックする
- コロマントキャプト、またはスプリットホルダを使用する
- 工具の突出し量をできるだけ小さくして、径をできるだけ大きくする
- 材料の補強(ボーリングバイト)
動的剛性を上げる
- 小さなチップノーズRを選択する
- 防振工具を使用する
- 切削工具の重量をできるだけ軽くする
切削速度を下げる
- ポジティブな切れ刃を使用する
- ホーニングが小さくて、ポジティブなチップブレーカを使用する
たわみを回避する
- 切削抵抗の方向を径方向から軸方向に変える
- 切込角を90°(リード角: 0°)に近づける
- 切込みをノーズRより大きくする
切りくずを処理する
- クーラントの流量を増やす
- 工具とワークとのクリアランスが十分あるか確認する
- 切りくずがすべて排出されていることを確認する
注意!
防振ボーリングバイトに荷重をかけ過ぎないように注意してください。最大荷重は製品に表示されています。また、www.sandvik.coromant.com/calculatorsから利用できる計算機を使用して、最大荷重を求めることも可能です。