穴あけ加工のヒント
給油のヒントとこつ
適切な給油は、穴あけを成功させるためにきわめて重要です。給油は以下に影響を及ぼします。
- 切りくず排出
- 穴品質
- 工具寿命
クーラントタンクの容積は、ポンプの1分間当たりの供給量の5~10倍が必要です。クーラントの流量が十分であることが重要です。
ストップウォッチと適当な大きさのバケツを使用して、容量をチェックすることができます。
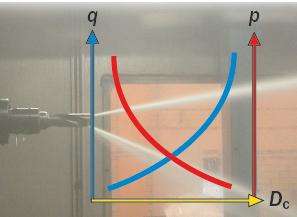
給油における圧力と径の関係
(圧力:赤、径:黄、油量:青)
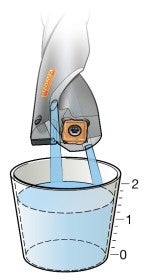
ドリルから吐出される量をチェックします
- 水溶性オイル (エマルジョン) は必ずEP (極圧) 添加剤と併用してください。オイルと水を混合する場合は、オイルを5~12%混合することで最適な工具寿命を実現します (ステンレス鋼と耐熱合金材の場合: 10~15%)。切削油のオイル混合率を高くするときは、推奨値を超えないように、必ず切削油分配装置で確認します
- 可能である場合には、内部給油は常に外部給油より好ましいものです
- ニートオイル (純油) は給油を改善するため、ステンレス鋼の穴あけ加工に有効です。常にEP添加剤を併用してください。ニートオイルは、超硬ソリッドドリルと刃先交換式ドリルの両方に適しています。
- 圧縮エア、ミストまたは最小限の給油は、特にいくつかの鋳鉄およびアルミ合金などの被削材で使用することができます。温度が上がって工具寿命に好ましくない影響を及ぼしますので切削速度を下げることを推奨します
内部給油
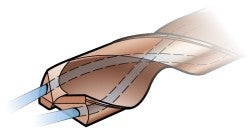
特に長い切りくずが生成される被削材の場合や深穴 (>3 x DC) 加工の場合、切りくずの詰まりを避けるために、内部給油が常に推奨されます。
水平ドリルでは、クーラントがドリルから少なくとも30 cm (11.81 inch) は下に垂れずに吐出されている必要があります。
外部給油
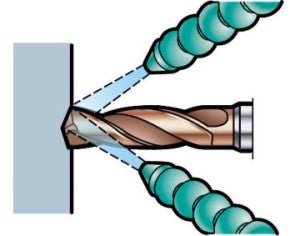
切りくず生成が良好で、加工穴深さが浅い場合は、外部給油が使用できます。切りくず排出を改善するために、少なくとも1本 (固定ドリルの場合は2本) のクーラントノズルを刃先に向ける必要があります。
クーラントを使用しないドライ穴あけ加工のヒント
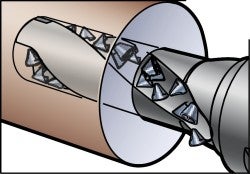
ドライ穴あけ加工は一般には推奨されません。
- 切りくずが短い被削材で、加工穴深さが加工径の3倍以下の場合は使用可能です
- 横穴加工に使用
- 低い切削速度を推奨
- 工具寿命が短くなります
以下の場合、ドライ穴あけ加工は決して推奨しません。
- ステンレス鋼の被削材 (ISOステンレス鋼(M)および耐熱合金(S) )
- ヘッド交換式ドリル
高圧クーラント (HPC) (~70 bar)
高圧クーラントの使用には以下の利点があります。
- 冷却効果の向上により工具寿命が伸びる
- ステンレス鋼などの切りくずが長い被削材の切りくず排出の改善および工具寿命の向上
- 良好な切りくず排出による安全性の向上
- 安定した加工を維持する所定圧力および穴サイズに対する十分な流量の供給
切りくず処理のヒント
切りくず生成と切りくず排出は穴あけ加工にとって非常に重要な事項で、被削材、選択したドリル/チップブレーカ、クーラント圧/量、切削条件などによって決まります。
切りくずが詰まると、ドリルが径方向に振れて、その結果穴の品質やドリルの寿命、信頼性に影響が出たり、ドリルやチップが破損する原因となることがあります。
太くて硬い切りくず | ||
切削速度 | ![]() | 低摩擦のため、開きが大きい |
送り |
切りくずがドリルから詰まることなく排出されるときは、切りくず生成は許容範囲内です。これを確認する最適な方法は、穴あけ時に加工音を聞くことです。連続音が聞こえる場合は、切りくず排出は良好ですが、断続音は切りくずの詰まりを示しています。送り分力や動力モニタをチェックしてください。異常音がする場合は、切りくずの詰まりが原因の可能性があります。切りくずをチェックしてください。切りくずが長く、渦巻状ではなく曲がっている場合、切りくずの詰まりが発生しています。穴をチェックしてください。切りくずの詰まりが発生している場合は、凹凸面が見られます。
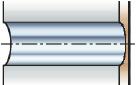
切りくず排出の良好な穴
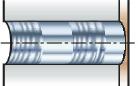
切りくず詰まりの影響を受けた穴
切りくずの詰まりを避けるためのヒント:
- 切削条件が正しいか、適切なドリル/チップブレーカが使用されているかを確認する
- 切りくず生成の確認– 送りと速度を調整する
- クーラントの量と圧力をチェックする
- 切刃を確認するチップブレーカ全体が食いついていない場合には、切刃の損傷/チッピングにより切りくずが長くなることがある
- 新しいロットのワークにより被削性が変化していないか確認する。変化がある場合は切削条件を調整する
良好、許容範囲、不可の切りくず状態
刃先交換式ドリル
中心刃は容易に確認できる円錐状の切りくずを生成します。外周刃は旋削加工の際にできる切りくず形状に似た切りくずを生成します。
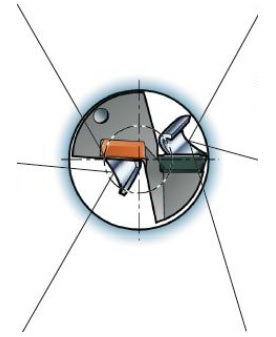
中心刃 | 外周刃 |
![]() 良好 | ![]() 良好 |
![]() 許容範囲 | ![]() 許容範囲 |
![]() 切りくず詰まり | ![]() 切りくず詰まり |
超硬ソリッドドリル
刃の中心から外周にかけて1つの切りくずを生成します。
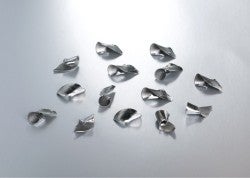
良好
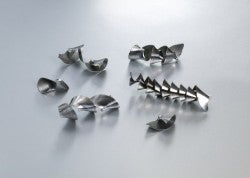
許容範囲
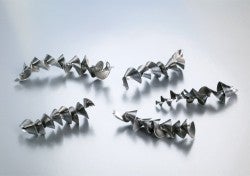
切りくず詰まり
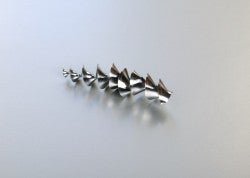
初期切りくず
注意:ワークに完全に食いつくまでの初期切りくずは常に長くなりますが、問題にはなりません。
ヘッド交換式ドリル
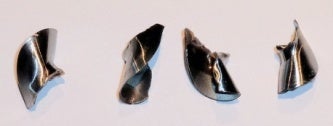
良好
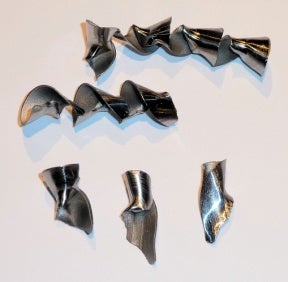
許容範囲
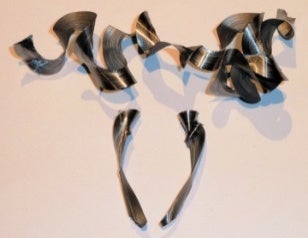
不可、切りくずが詰まる危険性
送りと速度のヒントとこつ
vc (m/min)
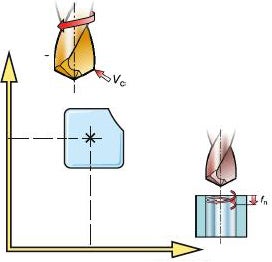
fn (mm/r)
切削速度の影響 – vc (m/min(ft/min))
切削速度は、被削材の硬度と同様に、工具寿命と消費動力に影響を及ぼす主な要因です。
- 切削速度は工具寿命を決定する最大の要因
- 切削速度は動力Pc (kW) とトルクMc (Nm) に影響を及ぼす
- 高い切削速度は高温を発生させ、特に外周コーナ部の逃げ面の摩耗が増える
- 高い切削速度は、特に低炭素鋼などの柔らかく、切りくずが長くなる被削材の切りくず生成に有効
- 切削速度が高すぎる場合:
- 急速な逃げ面摩耗
- 塑性変形
- 穴品質の低下および穴公差の悪化 - 切削速度が低すぎる場合:
- 構成刃先
- 切りくず排出の悪化
- 加工時間が長くなる
送りによる影響 – fn (mm/r(in/r))
- 切りくず生成、加工面品質、穴品質に影響を与える
- 動力Pc(kW)とトルクMc(Nm)に影響を及ぼす
- 高送りは送り分力Ff (N) に影響を及ぼすため、条件が不安定な場合に検討
- 機械的および熱的応力の要因となることがある
- 高い送り速度:
- 切りくず処理が困難になる
- 加工時間が短くなる
- 工具の摩耗が減るが、ドリルが破損する危険性が増す
- 穴品質の低下 - 低い送り速度:
- 切りくずが長く薄くなる
- 品質の向上
- 工具の摩耗が加速する
- 加工時間が長くなる
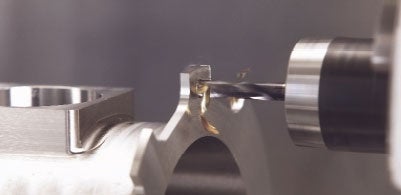
薄肉/弱いワークの穴あけ加工を行う場合は、送り速度が低い状態で加工すること。
良好な穴品質を達成するためのヒント
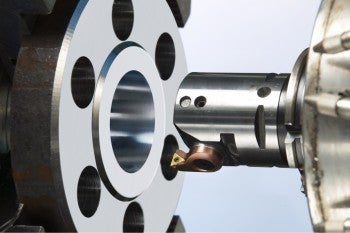
切りくず排出
切りくず排出が十分であることを確認します。切りくずが詰まると、穴の品質と信頼性/工具寿命に影響が出ます。ドリル/チップブレーカと切削条件はきわめて重要です。
安定性、工具の段取り
できるだけ短いドリルを使用します。振れの少ない堅固で確実なツールホルダを使用します。マシンのスピンドルが良好な状態で、芯が正しく合っていることを確認します。ワークが固定され、安定していることを確認します。凹凸面、傾斜面および交差穴に対して正しい送り速度を設定します。
工具寿命
チップの摩耗をチェックし、規定の工具寿命プログラムを設定します。穴あけ加工を管理する最も効率的な方法は、送り分力モニタを使用することです。
メンテナンス
チップクランプスクリューは定期的に交換してください。チップ交換の前にチップシートを清掃し、必ずトルクレンチを使用してください。超硬ソリッドドリルを再研磨する前に摩耗限度を超えてはなりません。
種々の被削材に対する穴あけ加工のヒントとテクニック
- 低炭素鋼
- オーステナイト・二相ステンレス鋼
- CGI (コンパクト黒鉛鋳鉄)
- アルミ合金
- チタン合金、耐熱合金 (HRSA)
- 高硬度鋼
低炭素鋼の穴あけ加工のヒント

問題点: 低炭素鋼は溶接部品に使用されることが多く、切りくず生成が難しい問題になる可能性があります。低い硬度、炭素含有量、そして硫黄含有量により、長い切りくずが生成されます。
推奨: 切りくず生成に関する問題が発生する場合は、切削速度 vcを上げて、 送りfnを下げます (通常の鋼では送りは上げるべきであることに注意してください) 。
その他:高圧内部給油を使用します。
オーステナイトおよび二相ステンレス鋼の穴あけ加工のヒント

問題点: オーステナイト、二相およびスーパー二相ステンレス鋼の被削材は、切りくず生成が問題になることがあります。
推奨: 切りくずを適切に形成しその排出を助けるので、正しいチップブレーカを選定することがきわめて重要です。一般的に、シャープな刃先が望ましいものです。切りくず生成に問題が発生した場合、送り fn を増やすと切りくず破断がより容易になります。
その他:内部給油、高圧。
CGI (コンパクト黒鉛鋳鉄) の穴あけ加工のヒント

問題点: CGIは、基本的に、特別な注意は必要ありません。ねずみ鋳鉄よりは大きな切りくずを生成しますが、破断しやすい切りくずです。切削抵抗は高いので、工具寿命が影響を受けます。特別な耐摩耗材種が必要です。コーナ摩耗はあらゆる鋳鉄に特有の現象です。
推奨: 切りくず生成に関する問題が発生する場合は、切削速度vcを上げて、送りfnを下げます。
その他:内部給油。
アルミ合金の穴あけ加工のヒント

問題点: バリの発生と切りくず排出が問題になる可能性があります。溶着による工具寿命の悪化することがあります。
推奨: 最適な切りくず生成には、低送り、高切削速度を適用してください。
工具寿命の悪化を避けるため、溶着をできるだけ低減するよう種々のコーティングをテストする必要があるかもしれません。テストすべきコーティングにはダイヤモンドコーティングが含まれますが、いくつかのケース (母材による) ではコーティングはまったく使用しないこともあります。
その他:高圧エマルジョンまたは高圧ミストクーラントを使用してください。
チタン合金および耐熱合金の穴あけ加工のヒント

問題点: 穴表面の加工硬化が次の操作に影響を及ぼします。良好な切りくず排出が得られなくなることがあります。
推奨: チタン合金用チップブレーカの選定においては、シャープな刃差先が望ましいものです。ニッケルベース合金に対しては、剛性の高いチップブレーカであることがきわめて重要です。加工軟化が問題になる場合は、送り速度を上げることを試みてください。
その他:高圧クーラント (70 bar以下) の使用によりパフォーマンスが向上します。
高硬度鋼の穴あけ加工のヒント

問題点:許容できる工具寿命の達成に難点があります。
推奨: 熱を下げるため切削速度を下げます。径くずを許容できる排出の容易なものとするため、送り速度を調整します。
その他:エマルジョンの混合比を高くします。
穴公差のヒント
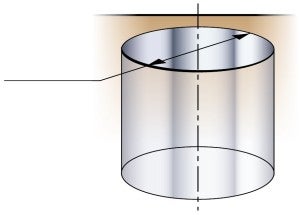
穴の寸法は3つのパラメータに分けて表すことができます。
- 呼び径 (実際の径寸法)
- 公差幅 (ISO準拠 IT)
- 公差の位置 (ISO準拠 アルファベット大文字)
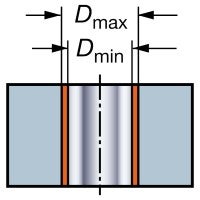
DmaxとDminの差がはめあい公差で、ITとも呼ばれています。
径範囲、D (mm)
工具幅 | D>3-6 | D>6-10 | D>10-18 | D>18-30 | D>30-50 | D>50-80 | D>80-120 | D>120-180 | D>180-250 |
IT5 | 0.005 | 0.006 | 0.008 | 0.009 | 0.011 | 0.013 | 0.015 | 0.018 | 0.020 |
IT6 | 0.008 | 0.009 | 0.011 | 0.013 | 0.016 | 0.019 | 0.022 | 0.025 | 0.029 |
IT7 | 0.012 | 0.015 | 0.018 | 0.021 | 0.025 | 0.030 | 0.035 | 0.040 | 0.046 |
IT8 | 0.018 | 0.022 | 0.027 | 0.033 | 0.039 | 0.046 | 0.054 | 0.063 | 0.072 |
IT9 | 0.030 | 0.036 | 0.043 | 0.052 | 0.062 | 0.074 | 0.087 | 0.100 | 0.115 |
IT10 | 0.048 | 0.058 | 0.070 | 0.084 | 0.100 | 0.120 | 0.140 | 0.160 | 0.185 |
IT11 | 0.075 | 0.090 | 0.110 | 0.130 | 0.160 | 0.190 | 0.220 | 0.250 | 0.290 |
IT12 | 0.120 | 0.150 | 0.180 | 0.210 | 0.250 | 0.300 | 0.350 | 0.400 | 0.460 |
IT13 | 0.180 | 0.220 | 0.270 | 0.330 | 0.390 | 0.460 | 0.540 | 0.630 | 0.720 |
径範囲、D (inch)
工具幅 | D>0.118-0.236 | D>0.236-0.394 | D>0.394-0.709 | D>0.709-1.181 | D>1.181-1.969 | D>1.969-3.150 | D>3.150-4.724 | D>4.724-7.087 | D>7.0879.843 |
IT5 | 0.0005 | 0.0002 | 0.0003 | 0.0004 | 0.0004 | 0.0005 | 0.0006 | 0.0007 | 0.0008 |
IT6 | 0.0003 | 0.0004 | 0.0004 | 0.0005 | 0.0006 | 0.0007 | 0.0009 | 0.0010 | 0.0011 |
IT7 | 0.0005 | 0.0006 | 0.0007 | 0.0008 | 0.0010 | 0.0012 | 0.0014 | 0.0016 | 0.0018 |
IT8 | 0.0007 | 0.0009 | 0.0011 | 0.0013 | 0.0015 | 0.0018 | 0.0021 | 0.0025 | 0.0028 |
IT9 | 0.0012 | 0.0014 | 0.0017 | 0.0020 | 0.0024 | 0.0029 | 0.0034 | 0.0039 | 0.0045 |
IT10 | 0.0019 | 0.0023 | 0.0028 | 0.0033 | 0.0039 | 0.0047 | 0.0055 | 0.0063 | 0.0073 |
IT11 | 0.0030 | 0.0035 | 0.0043 | 0.0051 | 0.0063 | 0.0075 | 0.0087 | 0.0098 | 0.0114 |
IT12 | 0.0047 | 0.0059 | 0.0071 | 0.0083 | 0.0098 | 0.0118 | 0.0138 | 0.0157 | 0.0181 |
IT13 | 0.0071 | 0.0087 | 0.0106 | 0.0129 | 0.0154 | 0.0181 | 0.0213 | 0.0248 | 0.0283 |
- IT番号が小さくなるほど公差も小さくなります
- 同じIT等級でも、穴径が大きくなると公差も大きくなります
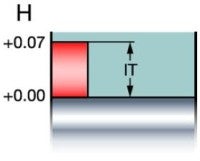
例:
公称値:15.00 mm
公差幅:0.07 mm (ISO準拠のIT 10)
位置:0からプラス (ISOのH)
穴と軸の公差
多くの場合、穴公差は穴とはまり合う軸の公差と関係があります。
例:
軸 ø20 mm (0.787 inch) h7
穴 ø20 mm (0.787 inch) h7
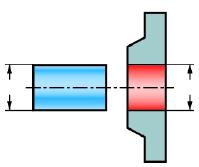
軸公差位置は、穴の公差位置と同じ文字の小文字で表されます。以下の図は、全体図です。
最も一般的 | ||
軸よりも 穴の方が大きい | ![]() | 穴よりも 軸の方が大きい |
中間ばめ | しまりばめ | | 干渉 |
遊びあり (ベアリング) | ![]() | 遊びなし (=軸が穴より大きい) |
穴とキャビティ/ポケットのフライス加工
2軸ランピング加工 ヘリカル加工 コンタリング加工 外径ヘリカル加工またはランピング加工 プランジ加工 ペックドリリング加工 スライス加工法 閉鎖ポケットまたは閉鎖角 穴のフライス加工:開口部の作成 中実ワークでの開口部の作成 穴またはキャビティの拡張 キャビティまたはポケットの加工/拡張 中実ワークでの開口部の作成 ランピング加工 ペックドリリング加工 溝の作製 穴のフライス加工時には常に、ペックドリリング加工よりランピング加工... chevron_right
ねじ切り加工
このセクションでは、ねじ切り旋削加工、スレッドミリング加工あるいはタップ加工に対する切削速度、送り速度あるいはその他のパラメータを計算するためのねじ切り加工の公式と定義を説明しています。国際的な基準による種々のねじ形状の表記についても確認できます。 ねじ切り旋削加工の公式と定義 切込み 総切込み量を小さな切込みに分割することにより、チップの切刃のノーズR部分に過負荷がかからないようにします。 例: パスごとの切込み(ラジアルインフィード)の0.23–0.10... chevron_right
正しいタイプのタップの選定方法
適切なタップを選ぶ際に、考慮すべきいくつかの要素があります。以下の手順に従って、お客様の用途に最適なタップタイプを見つけてください。 さまざまなタップ工具タイプ どのタップ工具を使用するかは、どんなタイプの穴のねじ切りをしたいかによります。 ねじ形状タイプと被削材(ISO加工領域) 正しいねじ形状タイプとねじ切りする被削材を見つけてください。 ねじ切り工具食いつき部タイプ タップ加工する穴のタイプにより、どの食いつき部タイプを使用するのが適切であるかが決まります。 さまざまなタップ工具タイプ タップ工具には以下の4種類があります。ストレートフルートタップ、スパイラルポイントタップ、スパイラルヒューズタップ、転造タップ。どのタイプを使うかは、ねじ切り加工する穴の種類(止まり穴または貫通穴)と加工部品の材質によります。 ストレートフルートタップ スパイラルポイントタップ スパイラルヒューズタップ 転造タップ 切削タップ 切削タップでは、タップが被削材を切削して切りくずが発生します。 転造タップ 切削タップに比べて優位な点: 転造は通常のねじ切り加工よりも一般的に短時間で加工できます 径の3.5倍までの最大深さが可能で、切りくず除去の問題が発生しません 多くの場合、転造タップの方が長寿命です 1種類の工具をさまざまな被削材に使用でき、貫通穴と止まり穴の両方に適合します 安定したデザインにより破損の危険性が少なくなっています 正確な公差のねじ山が保証されます 切りくずは生じません 剥離強度に優れ、ねじ山の強度が最大100%高くなります ねじ山の表面粗さが低くなります 効果的な使用のための前提条件: ある程度の延性が必要なためすべての被削材には適合しません。 推奨引っ張り強度限界:1200... chevron_right
スライス加工方法
スライスおよびトロコイド加工方法は、当初、高硬度鋼 (ISO H)、耐熱合金 (HRSA, ISO S) といった難削材の荒加工および中荒加工用に開発されましたが、その他の被削材に使用することもでき、特にびびりやすい加工に使用されています。 トロコイド加工は、主に穴加工に使用されます。 スライス加工は、通常コーナの中荒加工に使用されます。 いずれの加工方法も、非常に安定して生産性が高いことが証明されています。 スライス加工およびトロコイド加工の技術は、小さな径方向切込み... chevron_right