Turbine blade
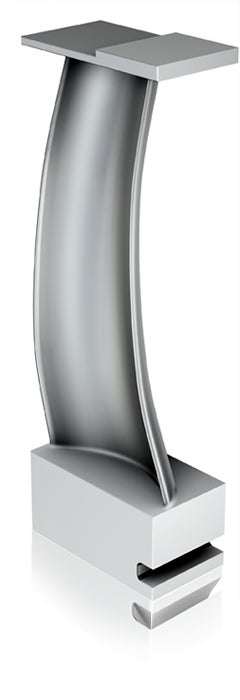
Blade machining moves to a new level
Competitive manufacturing blades for steam and gas turbines is challenging with machining containing most of the demanding factors in metal cutting:
- part materials have varying machinability (some of them poor, needing dedicated inserts),
- considerable amounts of material have to be removed and good surface finish has to be achieved (without affecting the blade negatively, for example in terms of residual stress),
- component form is complex (some needing advanced CAM-programmes with the best methods),
- blades are prone to vibration during machining (long, slender, thin parts that need light-cutting tools and dampening abilities),
- production efficiency is important (large volumes are made),
- several different tools have to be used and applied correctly (straightforward face milling to 4- to 5-axis profiling).
Well-worked out machining strategy with continuous improvements is crucial to productivity and subsequent processes. Innovative tooling and qualified application is the only way to meet the challenges involved especially the rotating blades.
Roughing the blade rhombus and aerofoil, of especially medium-sized blades, from blanks, to achieve the basic blade form is often at the centre of attention as it represents the bulk of machining. Many of these are made in martensitic stainless steel but blades are also made in Duplex, HRSA and Titanium. This operation has seen a number of different solutions through the years but round-insert milling cutters and ball-nose end mills have become the main direction through their ability to generate profiles with a secure and strong cutting edge and also their cutter-to-part clearance.
When one milling cutter is used for the rhombus-roughing, a large amount of cutter engagement with the part is an important success factor, with 60 to 80% being the target. This has to be achieved by applying the most suitable cutter diameter in combination with the most advantageous tool path. Also the best balance between feed, depth of cut, size of insert, geometry and grade of insert, pitch of inserts as well as the cutting forces generated should be established to achieve optimized performance, security and results.
Roughing the roots of the blade, especially the transition between head and foot, (hub and shroud) is an important follow-up operation to get right as this also represents considerable amounts of material but is not suitable for the round-insert cutter of the rhombus because of the corner and shoulder involved. This needs a special solution to achieve high efficiency.
Semi-finishing and finishing of the blade also requires the best tool and method solutions to achieve quality at high efficiency. A complimentary round-insert milling cutter, solid carbide end mills and a modern, suitable face mill applied with advanced methods, to suit the blade size and form as well as the machine and programme possibilities involved, will complete the set-up.
Roughing rhombus
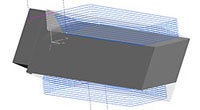
An often-used method for roughing of the rhombus is to enter the cutter straight into the component. This method will not optimize tool life and productivity. Our recommended method is to roll into cut in a down milling direction and to keep the cutter constantly engaged. This way the feed rate is increased and longer tool life possible.
CoroMill 600 is your ideal cutter for profile roughing and semi-finishing operations. Optimized cutter body design, dedicated grades and geometry, and the patented iLock™ system make it ultimate for aerofoil and rhombus machining.
New blade milling concept
Aerofoil
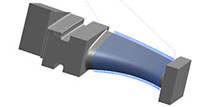
Modern design of turbine blades maximizes efficiency through complicated surface geometries. Machining these surfaces therefore requires a careful machining strategy.
Sandvik Coromant provides know-how and high-quality cutters for roughing, semi-finishing and finishing of the aerofoil, including CoroMill 600, CoroMill 300, CoroMill 316 and CoroMill Plura.
Shroud and hub
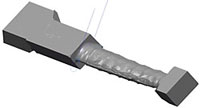
Roughing of the transitional radii between the head/foot and the aerofoil of the blade has always been a demanding and time-consuming operation, involving a number of dedicated tools.
The Indexable Conical Ball Nose end mill (engineered solution) combines the best of CoroMill technology into one dedicated cutter solution, delivering a surface readyshaped for finishing operations. Use CoroMill Plura cutters for finishing. The productivity improvements are considerable.
Head and foot
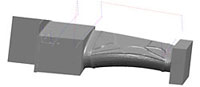
When face milling head and foot, enter the component with the roll into cut method. Position the cutter off centre to produce the thinnest chip at exit. This will result in less vibrations and enable higher feed rates.
CoroMill 490 is a new state of the art milling solution with a unique design based on a large axial rake angle in combination with a positive sharp cutting edge. CoroMill 490 offers superior surface finish of the head and foot.
Mounting slot
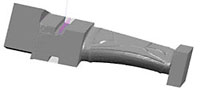
The blade’s size and the slot’s position and form determine the machining strategy. A method using a high-feed cutter is often efficient when opening a slot.
First choice for roughing the slot is CoroMill 316 high-feed cutter with a ramping tool path. CoroMill Plura provides a versatile solution for slot finishing, with a cutting edge length covering the various depths of the slot.
New blade milling concept
CoroMill 600 is a modern innovative milling cutter – a completely new design based on a unique state-of-the-art platform of tool elements. Developed for roughing and semi-finshing of turbine blades for the power industry, this is a round-insert cutter enabling a completely new approach to meet the challenges of blade machining.
There are four new elements to the new concept:
- insert-seat interface; this factor has recently taken on a new, broader importance because of its broader effect on the possibilities made available. The iLock concept was introduced to indexable insert cutting tools to ensure absolute positioning of the insert in the toolholder/cutter body. The insert is easier to rotate into position at indexing or replacing by operators with gloves on. The carefully developed design of accurately matching rails and grooves having the best form and sizes has had a far-reaching effect on cutting edge stability, accuracy, security and tool-handling. The implications of this is that the inserts of the CoroMill 600 cutter is no longer dependent upon support from the sides of the insert seats for locking insert and indexation/fixation of insert, leaving the field free to provide inserts with completely new optimized geometries, that were previously impossible to consider. New visions are possible with regard to cutting action, cutting-geometry variations along the edgeline, feed-rate optimizations, etc.
- the cutter body of CoroMill 600 is of a completely new design, optimized for curvature milling such as involved in 4- and 5-axis milling of turbine blades. The form and clearance of the cutter body means optimization of tool path possibilities, higher machining security and improved chip evacuation. A differential insert-pitch minimizes vibration tendencies.
- new insert-geometries are evolving for the CoroMill 600 ranging from light-cutting to medium-duty machining capabilities. Inserts are direct pressed through the latest insert-manufacturing processes. The light-cutting insert has as good as or often better performance than available ground inserts with a similar geometry. This insert has a sharp, positive, but strong cutting edge with optimized micro geometry for various blade materials.
- a new insert grade development has been completed for the CoroMill 600 tools. A brand new CVD-coated grade, especially developed and optimized for turbine-blade milling has enabled performance to be improved for the wide range of martensitic stainless steel blades. The grade represents a new combination of insert substrate, coating and manufacturing processes. Complimentary, modern CVDand PVD-coated insert grades for other occurring blade materials have been proven and are established solutions.
- high pressure coolant, air or minimal lubrication facilities are part of the CoroMill 600 cutter. The standard HP concept has been prepared for at each insert seat, with the optional jet directed for improved chip formation. This is to create a hydraulic wedge of coolant for the more demanding materials or for compressed air to improve chip flow and evacuation – a key factor in milling blades, when cutting speeds are relatively low.
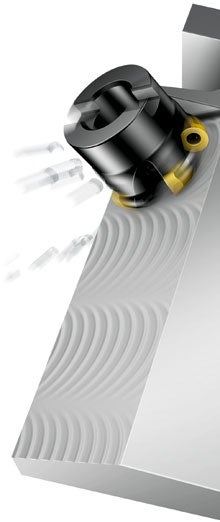
Rough machining
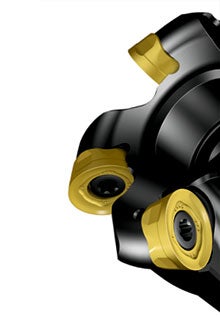
Unique insert seat technology
Aerofoil machining
Involves selecting tools for the semifinishing and finishing of the blade contour. These are based on blade-size, machinery and methods. To achieve optimum results, the choice of tool needs to be in relation to the amount of material and the sculptured surface. The CoroMill 300 round insert cutter is an excellent profiling cutter for five-axis machining, with good clearance, light cutting action and a broad range for semi-finishing. It is capable of high-feed semi-finishing with an extra-close pitch version with, if any, only minimal vibration tendencies. The 12 and 8 mm IC inserts, in different geometries, can be selected along with diameter and pitch for optimum performance.
Semi-finishing and finishing the aerofoil is profiling passes with CoroMill Plura solid carbide end mills or with exchangeable heads in CoroMill 316. The semi-finishing operation will influence the surface finish achieved in the final finishing operation. The aim should be to generate a very regular, uniform level of residue material, if necessary through two semi-finish operations. Vibration tendencies are another factor that affects the quality result which can be affected by the cutter engagement, feed, approach and cutting action of the tool employed.
The CoroMill Plura programme is a modern development of solid carbide end mills in advanced grades for all component materials. The geometry development has taken the demands of milling in today’s machines. Flute depth is varied and has been adapted to suit cuts providing best core stiffness and space for efficient chip evacuation in blade machining.
End milling operations have been largely dominated by two somewhat overlapping application areas as regards tool types – indexable insert cutters and solid carbide cutters. These areas have been segregated mainly by tool-diameter, operation type and the component finish required. Indexable insert end mills have no upper diameter limit but, for practical reasons, have a lower diameter limit – often 12 or 16 mm. Solid carbide end mills, on the other hand, can be of diameters down to tenths of a mm but usually have an economical upper diamater-limit around 25 mm.
As regards type of operations and finish, indexable insert cutters are flexible, high metal removal rate tools, well suited for most operations while solid carbide cutters have close tool-tolerances and can provide high finishes and accuracy, especially at large axial depth of cut thanks to long radial cutting edges.
While a solid carbide tool is one, complete precision tool, integrated from shank to cutting edge, an indexable insert tool is made up of two tool elements which means broad variation and optimization possibilities. In between the two areas provided by the indexable insert and solid carbide tools, there is a potential area for an alternative tool solution which overlaps both. One that provides both cutting edge indexability and the benefits of solid carbide tooling for small to medium size end mill diameters.
The CoroMill 316 exchangeable head milling system has the sophistication of Plura solid carbide cutting edges combined with an advanced coupling between head and tool shank. It offers very extensive capability with a programme of Plura heads where the range of shanks provide broad machine tool suitability. The CoroMill 316 tooling is balanced by design and so capable of relatively high spindle speed. It combines the advantages of tool-cost efficiency with tool-handling efficiency. The combination of high speeds and multi-tooth head options provide the capability of very high feed rates as well as high cutting speed. The exchangeable-head concept also makes it easier to adapt the cutter geometry to various workpiece materials and conditions. The design of heads provides good machining stability and minimized tool deflection tendencies through helix and differential pitches.
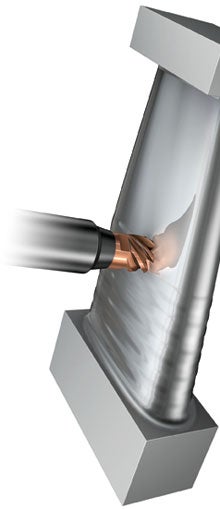
Advanced coupling

The shroud and hub area of the blade
Involving surfaces leading up to and at the transitional radii between the root and the head of the blade, is usually seen as a stand-alone operation, involving dedicated tools. The rest-milling necessary in the roughing is quite a demanding operation which needs a cutter capable of high material removal rate during flank and point engagement.
A conical end mill is ideal and depending upon the blade size, either as an indexable cutter or solid carbide end mill, of which CoroMill Plura offers a good choice. When it comes to optimizing productivity in this operation when there is plenty of material, a dedicated indexable insert cutter is usually the best solution. A ballnose cutter in combination with a longedge cutter will do the job in subsequent operations – CoroMill 216 and CoroMill 390 being the optimum choices.
However, this is an operation begging for a dedicated-cutter solution. This has been answered by the design of a special conical ballnose end mill which combines the best of CoroMill technology in one. This tool provides the means with which to rough-mill the shroud and hub fillets after the rhombus has been roughed and before the finishing operations commence. In one operation – or at the very least fewer passes than many existing solutions – the transitional area is shaped ready for a semi-finishing operation. This cutter can be adapted to suit various sizes of blades using standard indexable inserts proven for each cut. This state-of-the-art special tool design offers a new solution to a demanding, often time and tool consuming operation where productivity improvements are considerable.
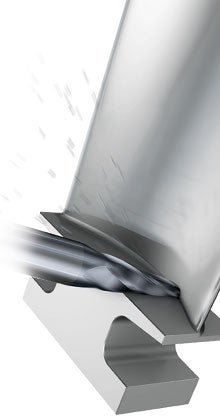
New developments for roughing and finishing with conical ballnose end mills
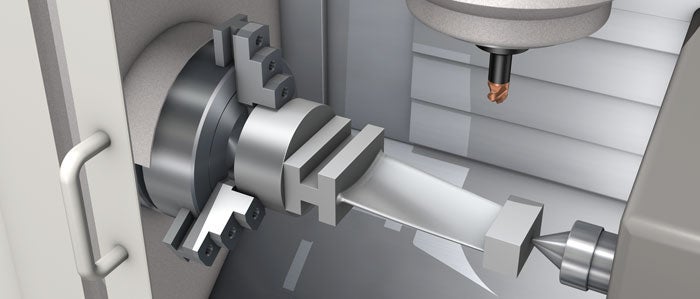
タービンブレード
ブレード加工の新たなレベルへ スチームおよびガスタービンのブレード製造には、金属切削における最も要求の高い課題が含まれます: 使用される材料の被削性が多岐に渡る(特別なチップを必要とするものを含む) 削る量がかなり多く、また高品質の加工面が求められる(残留応力等でブレードにダメージを残さない) 形状が複雑(高度なCAMプログラミングが求められる場合がある) 長く薄い部品のためびびりやすく、防振機能のある軽切削工具を必要とする 生産効率が重要(個数が多いため) 多くの種類の工具が必要を正しく使用しなければならない(正面フライス工具および4-5軸の倣い加工) 高い生産性とスムーズな加工プロセスのためには、計画的な加工戦略と継続した改善が不可欠です。革新的な工具と適切な使用こそが、ブレード加工の課題を解決するための唯一の道です。 Roughing... chevron_right
Generator shaft
There is a range of typical turning operations used for shafts that have undergone... chevron_right
Steam turbine shaft
タービンシャフトは主に旋削加工、溝加工、穴あけ加工によって加工されます。たくさんの加工が必要で、溝は高い精度が求められます。 タービン シャフト に使用される典型的な旋削加工には、継続的な改善が実施されているものがあります 。 安定した状態 との長くでこぼこした 大型 鍛造品 の 重い 荒加工 は、 軸受面 の 広範囲な 仕上げ が続いています 。 電源コンポーネント 上で実行 旋削 はよく ツール 技術の進歩 を通じて 改善 に役立ちます 。 Heavy... chevron_right
耐熱合金 (ISO S) の倣い加工用CoroMill® Pluraボールエンドミル
用途 ブリスクやブレードなどのワークの倣い加工 (中仕上げ加工仕上げ加工) 製品ラインナップ 標準ラインナップ 追加情報 倣いフライス加工 シャンク 円筒 正面刃形状 材種 T2CH R2AH ISO被削材... chevron_right