İnce talaş delik işleme
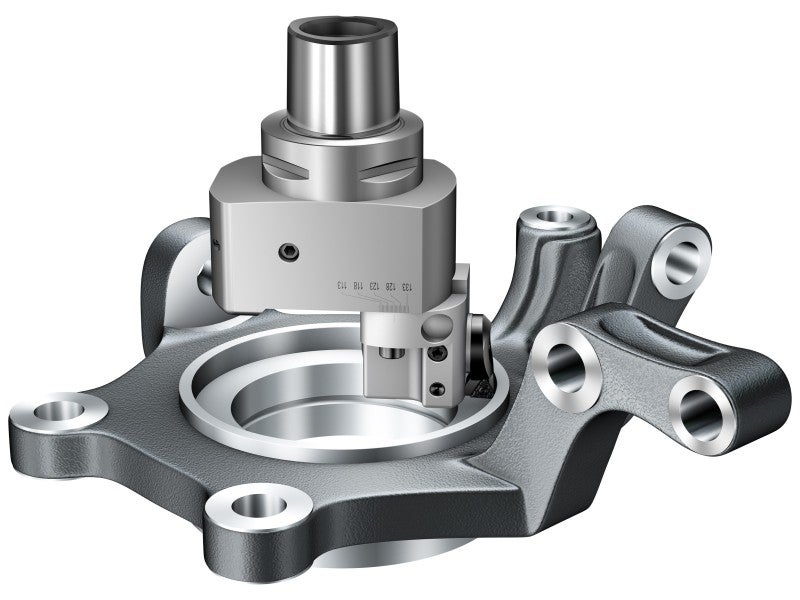
Hassas delik işleme çalışmaları, mevcut bir deliği tamamlamak ve dar bir delik toleransı, doğru konumlandırma ve yüksek yüzey kalitesi elde etmek amacıyla gerçekleştirilir. İşleme küçük kesme derinlikleriyle gerçekleştirilir, değerler genel olarak 0,5 mm (0,020 inç) altındadır.
Tek kenarlı delik işleme, dar tolerans (IT6 ile IT8 arası) veya yüksek yüzey kalitesi elde edilmesi gerektiğinde, küçük kesme derinlikli ile gerçekleştirilen ince talaş işleme çalışmaları için kullanılır. Hassas delik işleme takımının çapı, çok yüksek hassasiyetli bir mekanizma sayesinde mikron olarak ayarlanabilir. Tek kenarlı delik işleme, T9 veya daha yüksek toleranslara sahip deliklerdeki ince talaş işleme için bir kaba delik işleme takımı ile uygulanabilir.
Geriye delik işleme
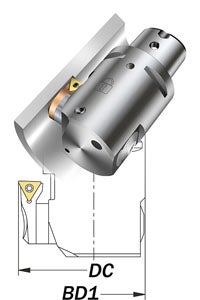
Geriye doğru delik işleme, ters taraftan ulaşılamayan bir kenara sahip deliklerin işlenmesine olanak sağlamak için kullanılır. Geriye doğru delik işleme ayrıca, deliğin tamamı tek bir konumdan işlendiği için kenarlı bir deliğin eşmerkezliliğini optimize etmek için de kullanılabilir.
Not: Delik işleme takımının kenarlı delikten boylu boyunca geçeceğinden ve delik işleme takımının parça ile çarpışmayacağından emin olun. Geriye delik işleme sırasında, delik işleme takımı minimum DC/2 + BD1/2 çapa sahip bir deliği boylu boyunca geçecek şekilde konfigüre edilir.
Geriye doğru delik işleme için takım ayarı:
- Başsız cıvatayı üst kesme sıvısı çıkışından çıkartın ve alt kesme sıvısı çıkışına takın
- Doğru soğutma sıvısı pozisyonu elde etmek için kesme sıvısı çıkışına takın (en küçük boyutlu takımlarda başsız cıvata alt kesme sıvısı çıkışına takılamaz)
- Kartuşu 180° döndürün
- Gerekiyorsa kızak uzantısı kullanın
- Dönüş yönünü tersine çevirin
Dış delik işleme
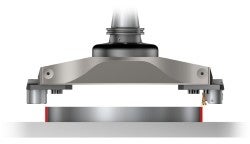
Daha dar bir çap toleransı elde etmek için dıştan gerçekleştirilen ince talaş işleme işlemleri bir hassas delik işleme takımı ile yapılabilir.
Dış delik işleme için takım ayarı:
- Dönüş yönünü tersine çevirin
- Kafayı 180° çevirin
- Çarpışmayı önlemek için mümkün olan en yüksek l3 işleme uzunluğunu l3 ve en büyük takım dış çapını seçin
Dış çap işleme için kızak ve hassas delik işleme kafasının kütlesi iş parçasının etrafında dönecek ve yüksek merkezkaç kuvvetlerine neden olacaktır. Bu nedenle dıştan gerçekleştirilecek bir uygulama için maksimum kesme hızı, kafa 180° döndürülmüş (takım hassas delik işleme için konfigüre edilmiş) durumdayken çap için maksimum kesme hızı dikkate alınarak hesaplanmalıdır.
Hesaplama örneği:
- İşlenecek olan dış çap: 80 mm (3,15 inç)
- (Bu kızak ve kafa pozisyonu ile) işlenebilecek iç çap: 210 mm (8,27 inç)
Not: Maksimum devrin hesaplanması amacıyla çap değerini elde etmek için işlenmesi gereken çap değerine her zaman 130 mm (5,12 inç) daha ekleyin - Delik işleme temel alındığında maksimum kesme hızı (bu örnekte CoroBore® 825 için): 1200 m/dak (3937 ft/dak)
- 210 mm (8,27 inç) çap için 1200 m/dak (3937 ft/dak), 1820 dev/dak değerine eşittir. Bu; bu kızak ve kafa pozisyonu için kullanılabilecek maksimum devrin 1820 olduğu anlamına gelir
- Dış delik işleme için 1820 devir, 80 mm (3,150 inç) çap için 460 m/dak (1509 ft/dak) kesme hızına karşılık gelir
İnce talaş işleme işlemi için kesici uç seçimi
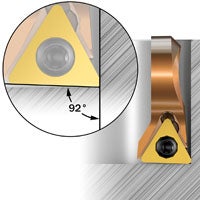
Pozitif uçlar, negatif uçlara göre daha düşük kesme kuvvetleri sağladığından hassas delik işleme uygulamalarında ilk tercihtir. Ayrıca geniş yelpazede uç geometrileri de mevcuttur.
Radyal kesme kuvvetlerini en aza indirmek ve titreşimleri önlemek amacıyla hassas delik işleme için giriş açısı en az 90° (0° boşluk açısı) olmalıdır.
Birçok Sandvik Coromant hassas delik işleme takımı, kenarların ve kör deliklerin tüm kesme kenarı kavranmadan işlenebilmesi için 92° (-2° boşluk açısı) giriş açısına sahiptir.
Doğru tornalama kesici ucu seçimi hakkında daha fazla bilgi alın.
İnce talaş delik işlemede kesme kuvvetleri
Takım kesme halindeyken, kesme kuvvetinin teğetsel ve radyal bir parçası takımı iş parçasından saptırmaya çalışacaktır. Kuvvetin teğetsel parçası, takımı aşağıya ve merkez hattından dışarıya doğru zorlayacaktır. Bu nedenle de takımın boşluk açısı azalacaktır.
Radyal sapma, kesme derinliğinin ve talaş kalınlığının azalması sonucu titreşim eğilimlerinin oluşabileceği anlamına gelir.
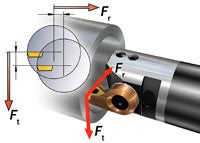
İnce talaş delik işlemede dengeleme
Simetrik olmayan bir takım veya büyük bir salgı nedeniyle oluşan dengesizlik, delik işleme takımına etki eden bir kuvvet oluşturur. Birçok uygulamada, dengesizlik nedeniyle oluşan kuvvet kesme kuvvetleri ile karşılaştırıldığında göz ardı edilebilir.
Dengesizlik, yüksek hızlarda ve özellikle de uzun kullanma mesafelerinde titreşimlere neden olarak delik kalitesini etkileyebilir.
Takım sapması
Kesme derinliği, köşe radyüsü ve giriş açısı, kesme kuvvetindeki teğetsel ve radyal parçaların boyutunu etkiler.
Radyal yönde sapma, işlenmiş delik çapını etkiler. Teğetsel sapma, kesici uç kenarını aşağıya, merkez hattından dışarıya doğru saptırarak etkiler. Radyal sapmaları dengelemek için önerilerimizi takip edin. Sandvik Coromant hassas delik işleme takımları, çapın 2 μm (0,0787 μinç) dahilinde ayarlanabilmesine olanak sağlayan bir ayar mekanizmasına sahiptir.
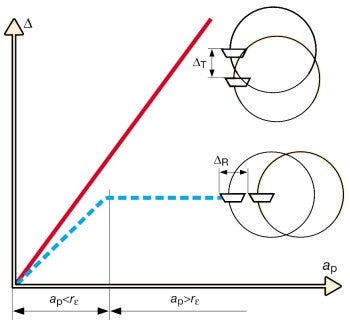
X ekseni: Kesme derinliği
Y ekseni: Sapma
Kırmızı hat: Teğetsel sapma
Mavi hat: Radyal sapma
Hassas delik işleme için uygulama kontrol listesi
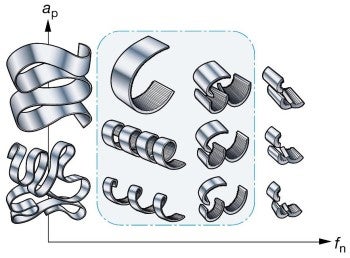
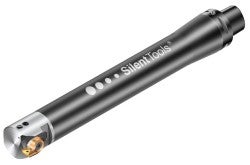
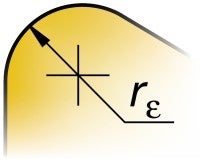
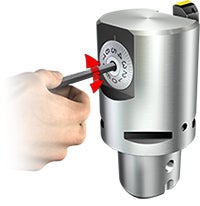
- Mümkün olan en büyük bağlama boyutunu veya bara çapını seçin
- Talaş kontrolünün düzgün olduğundan emin olun. Kısa/sert talaşlar titreşimlere neden olabilir, uzun talaşlar ise yüzey kalitesini bozabilir veya uç kırılmasına yol açabilir
- Mümkün olan en kısa kullanma mesafesini seçin, bağlama boyutundan dört kat daha uzun olan kullanma mesafeleri için sönümlemeli delik işleme baraları kullanın
- Büyük bir uç köşe radyüsü (RE) daha yüksek proses güvenliği ve yüzey kalitesi sağlar ancak titreşimlere neden olabilir. 0,4 mm (0,016 inç) üzerindeki köşe radyüsleri tavsiye edilmez. Küçük çaplar için delik işleme baralarını kullanırken 0,2 mm (0,008 inç) köşe radyüsü tavsiye edilir
- İnce kaplamalı uçlar veya kaplamasız uçlar, kalın kaplı olanlara göre genellikle daha düşük kesme kuvvetleri sağlar. Bu özellikle, takım uzunluğu/çap arasındaki oran yüksekse önemlidir.
- Keskin bir kesme kenarı genellikle titreşim eğilimini en aza indirerek delik kalitesini yükseltir
- Açık talaş kırıcılı bir geometri, genellikle daha avantajlı olabilir
- İyi bir yüzey kalitesi elde etmek için hafif bir kesici uç seçin (kararsız koşullar veya uzun kullanma mesafeleri için kullanılması tavsiye edilmez)
- Yetersiz kesme kenarı kavraması, kesme sırasında sürtünme kaynaklı titreşimleri çoğaltabilir
- Aşırı kesme kenarı kavraması (büyük kesme derinliği ve/veya ilerleme), takım sapması nedeniyle titreşimi artırabilir
- Talaş sıkışması veya titreşim eğilimi riskiyle başa çıkabilmek için bazı işlemlerde yüksek dayanıklılık seviyesine sahip bir uç kalitesinin kullanılması düşünülebilir
- Dar delik toleransı oluştururken, son ayarlamanın delik çapı ölçüldükten sonra takım hala tezgah mili üzerindeyken gerçekleştirildiğinden her zaman emin olun. Bu sayede, ön ayar düzeneği ile takım tezgahı arasındaki olası hatalı hizalamalar, radyal sapmalar veya uç aşınması dengelenmiş olur
- Delik işleme takımını ve iş parçasını düzgün bir şekilde bağladığınızdan emin olun
- Talaş tahliyesini, takım ömrünü ve delik geometrisini iyileştirmek için kesme sıvısı kullanın
- Küçük çaplar için modüler sistem Konik bir sap, kullanılan aynadan bağımsız olarak uzun kullanma mesafelerinde daha düz bir delik sunar. 6xD değerine kadar olan kullanma mesafeleri için konik yekpare karbür bir sap tercih edilmelidirSilindirik bir sap için en iyi düzlük, genellikle kısa kullanma mesafeleri ile sağlanırEn iyi stabilite ve kısa kullanma mesafelerinde azaltılmış titreşim yatkınlığı için ağır metal takım sapları seçinEn iyi stabilite ve üretim güvenliği için yüksek hassasiyetli hidrolik tutucuları tercih edin
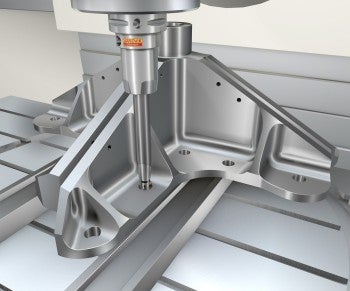
Ayrıca genel öneriler için bkz, Delik işleme nasıl uygulanır.
Tavsiye edilen sıkma torkunu görmek için aşağıdaki kullanım talimatına bakın.
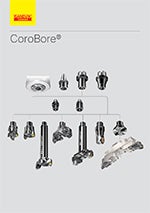
Kaba delik işleme
Kaba delik işleme temel olarak talaş kaldırmaya odaklıdır ve deliği ince talaş işleme... keyboard_arrow_right
Delik işleme
Delik işleme mevcut bir deliği genişletmek veya kalitesini artırmak için kullanılan... keyboard_arrow_right
Dişli üretimi
Dişliler nasıl üretilir? Değişen dişli üretimi ortamında, en verimli ve hassas işleme... keyboard_arrow_right
Dilimleme
Dilimleme ipuçları: dilimleme takımları nasıl seçilir İşlem güvenliği yüksek önem... keyboard_arrow_right