Jak zoptymalizować obróbkę aluminium w przemyśle motoryzacyjnym
Wraz ze wzrostem zainteresowania branży motoryzacyjnej aluminium jako surowcem do produkcji części silników, układów przeniesienia napędu, pomp wody i układów hamulcowych, producenci sprzętu oryginalnego i ich dostawcy stanęli przed wyzwaniem dostarczania bardziej produktywnych rozwiązań do frezowania. Kluczem do zdobycia autentycznej przewagi na rynku w tym segmencie jest wybór narzędzi, gdyż prawidłowe zastosowanie zoptymalizowanych frezów do obróbki całego asortymentu podzespołów silnika może przynieść znaczne korzyści.
Każdego roku rośnie liczba wyprodukowanych silników wykonanych z aluminium, zarówno w tradycyjnych, jak i hybrydowych samochodach pasażerskich. W istocie co roku wytwarza się prawie 100 milionów egzemplarzy. W silnikach tych zabudowane są często przedmioty o skomplikowanych kształtach, które po odlaniu wymagają wykonania szeregu zróżnicowanych i zarazem istotnych operacji frezowania.
Sandvik Coromant dysponuje obecnie kompletnym asortymentem do obróbki aluminium w branży motoryzacyjnej: od pierwszej obróbki powierzchni czołowych, poprzez obróbkę zgrubną i półwykończeniową po obróbkę wykończeniową. Każde z niestandardowych narzędzi frezarskich, których jest w sumie pięć typów, ma na celu optymalizację jakości i kosztu jednostkowego obróbki. Aby umożliwić osiągnięcie tego drugiego celu, niektóre narzędzia z asortymentu łączą różne zadania, np. wykonują obróbkę zgrubną i wykończeniową w jednym ustawieniu, aby skracać czasy cyklu.
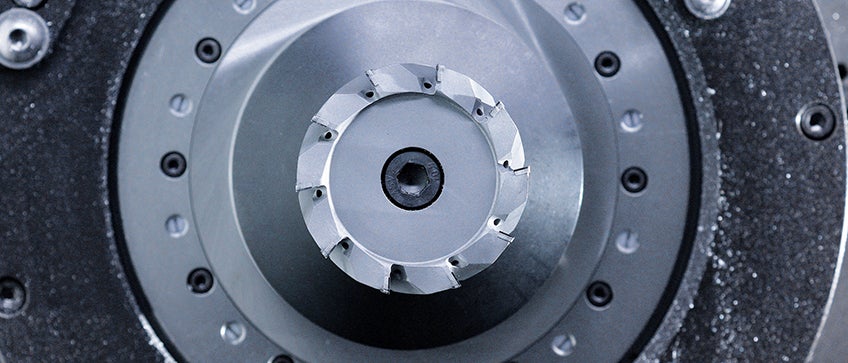
Przykładem jest frez M5C90, innowacyjne narzędzie umożliwiające wykonywanie zarówno obróbki zgrubnej, jak i półwykończeniowej. M5C90 służy do wykonywania z dużą prędkością frezowania czołowego i jest narzędziem dopasowywanym do potrzeb konkretnego klienta, eliminującym czasochłonny proces ustawiania w obiekcie klienta. M5C90 potrzebuje mniejszej liczby ostrzy niż porównywalne frezy tradycyjne, głównie dzięki niepowtarzalnemu osiowemu i promieniowemu ustawieniu płytek w rzędzie wykończeniowym / na średnicy wewnętrznej (bez potrzeby regulacji płytek). Takie ustawienie zapewnia frezowanie bez zadziorów i optymalne wykończenie powierzchni głowic cylindrowych, bloków silnika, części układu hamulcowego i wszystkich podzespołów aluminiowych, w przypadku których można osiągnąć dużą promieniową głębokość skrawania (nie dotyczy przedmiotów cienkościennych).
Przykładem potencjalnych korzyści płynących z zastosowania M5C90 jest trwający właśnie u klienta okres próbny produkcji korpusu zaworu w układzie hamulcowym, wykonanego z AlSi12Cu1. Narzędzie, posiadające 10 płytek węglikowych na średnicy zewnętrznej oraz cztery płytki na średnicy wewnętrznej (plus jedna płytka wiper), pracuje z prędkością wrzeciona wynoszącą 8000 obr./min, prędkością skrawania 4021 m/min (13,192 ft/min) oraz posuwem 0.25 mm/ostrze (0.009 cala/ostrze). Ponadto głębokość osiowa skrawania wynosi 2 mm (0.078 cala) przy głębokości promieniowej wynoszącej 140 mm (5.51 cala), co w efekcie daje wydajność skrawania metalu równą 5600 cm3/min (342 cala3/min). Choć całkowita trwałość narzędzia pozostaje jeszcze do ustalenia, samo narzędzie nadal pozostaje w obrabiarce po upływie 18 miesięcy eksploatacji.
Dla klientów potrzebujących frezu, za pomocą którego można także dokonywać obróbki cienkościennych przedmiotów aluminiowych, takich jak obudowy skrzyń biegów lub silnika, Sandvik Coromant posiada w swojej ofercie równie efektywny frez: M5F90. M5F90 to kolejne narzędzie do wykonywania obróbki zgrubnej i wykończeniowej w jednym przejściu. Korpus tego frezu (25-80 mm, 0.98-3.15 cala średnicy), przeznaczonego do obróbki cienkościennych przedmiotów aluminiowych i punktowej obróbki powierzchni czołowych, posiada wlutowane końcówki z PCD. Każda końcówka posiada krawędź zarówno do obróbki zgrubnej, jak i wykończeniowej. W zakresie obróbki zgrubnej frez działa jak konwencjonalne narzędzie frezarskie, w którym wszystkie krawędzie skrawające umieszczone są na tej samej średnicy i wysokości, natomiast obszar do obróbki wykończeniowej składa się ze stopniowanych promieniowo i osiowo krawędzi skrawających. Koncepcja ta umożliwia zastosowanie gęstej podziałki do obróbki bez zadziorów i bardzo niską chropowatość obrobionej powierzchni.
Możliwe są imponujące oszczędności czasu, o czym świadczy przeprowadzona u klienta próba, polegająca na frezowaniu czołowym aluminiowej głowicy cylindrowej (o dużej zawartości krzemu). W tym przypadku zastosowanie M5F90 w porównaniu ze specjalnym frezem z PCD z oferty konkurencyjnego producenta nie tylko zaowocowało zaoszczędzeniem 150% czasu realizacji, ale także umożliwiło eliminację zadziorów. Zastosowane parametry skrawania: prędkość obrotowa wrzeciona 15 915 obr./min; prędkość skrawania 2000 m/min (6562 stopy/min); posuw 0.16 mm/ostrze (0.006 cala/ostrze); oraz głębokość skrawania 1.5 mm (0.06 cala).
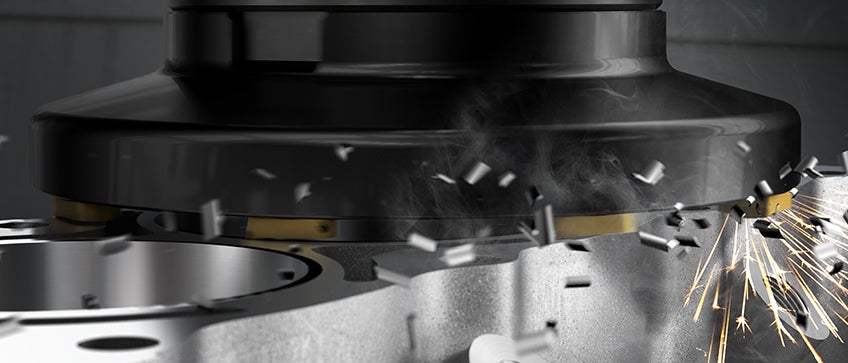
W kolejnym przykładzie zastosowania M5F90 udało się osiągnąć redukcję czasu cyklu o 44% podczas obróbki aluminiowej osłony łańcucha w porównaniu z dostarczanym przez konkurencję frezem o średnicy 63 mm (2.48 cala) z sześcioma płytkami wymiennymi z PCD. Co więcej, rozwiązanie to wyeliminowało wcześniejszą konieczność usuwania zadziorów.
Kolejne nowe narzędzie niestandardowe to frez M610, zaprojektowany z myślą o frezowaniu powierzchni bloków cylindrów ze złączami bimetalowymi, zazwyczaj wykonanymi z aluminium i żeliwa szarego (GCI).
Wiele szczególnych właściwości cieplnych i mechanicznych sprawia, że jednoczesna obróbka materiałów bimetalicznych jest dużym wyzwaniem. Istniejące frezy do tego zastosowania to narzędzia o złożonej konstrukcji, które wymagają ustawiania, co ma negatywny wpływ na wydajność. Ponadto narzędzia takie powodują wykruszanie się części przedmiotu wykonanych z żeliwa szarego.
W przeciwieństwie do nich M610 nie wymaga ustawiania ani regulacji i ma możliwość wykonywania obróbki z wysokimi posuwami bez wykruszania, tworzenia zadziorów i zarysowań na obrabianych przedmiotach. Potencjał ten jest istotny, ponieważ ewentualne niedoskonałości powierzchni mogą być przyczyną nieszczelności między blokiem i głowicą cylindrową, co z kolei ma negatywny wpływ na moc i wydajność. Niektórzy globalni producenci samochodów już odnoszą korzyści dzięki wdrożeniu M610.
Chcąc podać konkretny przykład, można wspomnieć klienta, który zdobył znaczną przewagę nad konkurencją w dziedzinie obróbki wykończeniowej powierzchni po stronie spalania w bimetalicznych blokach silnika. W porównaniu z frezem konkurencyjnego producenta wyposażonym we wkładki, M610 pomógł w zwiększeniu trwałości narzędzia o 833%, gdyż obrobił ponad 4000 przedmiotów, a frez konkurencji jedynie 480. Ponadto M610 pracował z ponad 10-krotnie większą prędkością. Parametry skrawania dla frezu M610 z 15 płytkami: prędkość skrawania 3000 m/min (9843 stopy/min); prędkość posuwu 5720 mm/ostrze (225 cali/ostrze); prędkość obrotowa wrzeciona 3820 obr./min; posuw 0.15 mm/ostrze (0.006 cala/ostrze); oraz głębokość skrawania aluminium wynosząca 0.5 mm (0.02 cala) i głębokość skrawania żeliwa wynosząca 0.05 mm (0.002 cala).
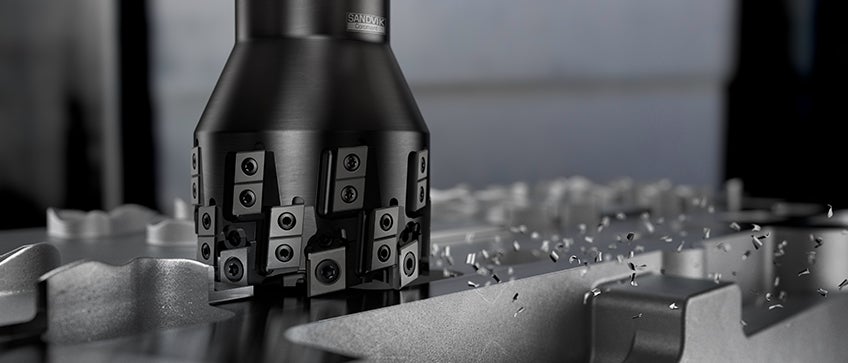
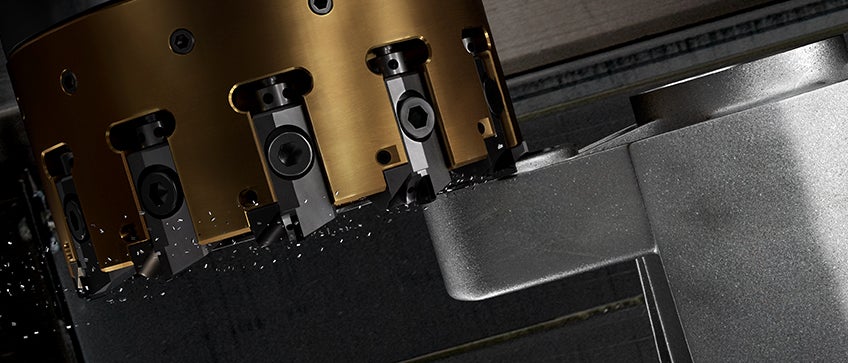
Inne narzędzia w tej rodzinie to np. frez M5Q90 do stycznej obróbki zgrubnej, który wykonuje obróbkę powierzchni czołowych pierwszego stopnia (pierwszy etap obróbki powierzchni czołowych po odlaniu) w jednym przejściu bez powstawania zadziorów. Narzędzie jest wyposażone w płytki styczne z PCD, które zapewniają płynny i stabilny przebieg obróbki, co przekłada sie na niższe zużycie energii i eliminację drgań.
Aluminiowe głowice cylindrowe i bloki należą do podzespołów, w przypadku których zastosowanie M5Q90 przynosi korzyści. Przykładowo cubing odlewanej głowicy cylindrowej polegałby zazwyczaj na obróbce płaszczyzn z okolic osadzenia wałka rozrządu, kanałów dolotowych i wylotowych oraz komór spalania. W przypadku analizowanym u klienta, polegającym na frezowaniu zgrubnym głowic cylindrowych odlanych ze stopu aluminium AS-9 na poziomym centrum obróbkowym, osiągnięto imponujące wyniki w zakresie trwałości narzędzia. Przy prędkości skrawania 3000 m/min (9843 cale/min), posuwie na ostrze 0.2 mm (0.008 cala) oraz osiowej głębokości skrawania 2.0 mm (0.079 cala) (pełne zagłębienie na 40 mm (1.57 cala) wykonano ponad 10 tys. podzespołów.
Kolejne narzędzie to M5R90 do drugiego stopnia obróbki zgrubnej i półwykończeniowej. Wkładki do tego standardowego frezu mają możliwość regulacji, a maksymalna głębokość skrawania wynosi 8 mm (0.315 cala) przy promieniu 0.4 lub 0.8 mm (0.016 lub 0.031 cala) zależnym od zastosowanej wkładki. Możliwość łatwej regulacji płytek przynosi korzyści w wielu zastosowaniach w branży motoryzacyjnej, co zaobserwowano podczas niedawnej próby u klienta, polegającej na frezowaniu czołowym osłony silnika. Frez M5R90, odlany ze stopu aluminium MRHB Si12, zaprezentował się bardzo korzystnie w porównaniu ze stosowanym dotychczas narzędziem konkurencji. Pracując z identycznymi parametrami skrawania, M5R90 uzyskał wzrost trwałości narzędzia z 8 do 10 tys. przedmiotów obrabianych. Ponadto konkurencyjny frez wymagał regulacji po każdych 1000 obrobionych przedmiotach z powodu przemieszczenia się płytki, co zagrażało jakości wykończenia powierzchni. W odróżnieniu od konkurenta regulacja wkładki M5R90 była konieczna dopiero po wykończeniu 8000 przedmiotów.
Do rodziny tej należy także frez czołowy M5B90 do obróbki superwykończeniowej, odznaczający się wyjątkowym ustawieniem osiowym i promieniowym płytek. Konfiguracja ta, a także zastosowanie płytki wiper zapobiega powstawaniu zadziorów i umożliwia uzyskanie doskonałej jakości powierzchni, o czym przekonał się niedawno producent głowic cylindrowych do samochodów pasażerskich. Firma ta zmagała się z problemem niestabilności procesów i powstawania zadziorów, a kolejną trudność sprawiała też nieprzewidywalna trwałość płytek, która zależała od ustawienia wkładek, odmiennego po każdym przezbrojeniu. Przejście na frez M5B90 umożliwiło obróbkę wykończeniową bez zakłóceń, z przewidywalnym przebiegiem zużycia ostrzy i bez formowania zadziorów. Narzędzie wytwarza wyłącznie bardzo cienkie wióry, które można w prosty sposób usuwać podczas obróbki, unikając uszkodzenia powierzchni przedmiotu. Ponadto zmiana na M5B90 zwiększyła średnią trwałość narzędzia z 30 tys. do 45 tys. przedmiotów.
Narzędzia do wiercenia i gwintowania z rodzin CoroDrill® i CoroTap® można również oferować klientom w ramach tej samej rodziny rozwiązań przeznaczonych do obróbki podzespołów aluminiowych dla branży motoryzacyjnej, czego przykładem jest standardowy frez czołowy CoroMill® Century 590 do obróbki wykończeniowej.
We wszystkich przypadkach potencjał skrócenia czasów realizacji i obniżenia kosztu jednostkowego detalu, przy jednoczesnej poprawie trwałości narzędzia i jakości wyrobu, jest bardzo realny, o czym świadczą opisane przypadki zastosowania u klienta. W przemyśle motoryzacyjnym, w którym przeważa produkcja dużych partii, nawet niewielka oszczędność na czasie wykonania może generować znaczące zyski finansowe. Mając to na uwadze, nie sposób zignorować jakiejkolwiek technologii, które może przynieść tak duże korzyści.