Hogyan kell optimalizálni alumíniummegmunkálást a járműipar számára
Mivel a járműiparban egyre több alumíniumból készült motor, hajtáslánc, vízpumpa és fékrendszeri alkatrész kerül felhasználásra, az OEM-gyártók és beszállítópartnereik számára a kihívás a termelékenyebb marási műveletek biztosítása. A szerszámválaszték a valódi piaci kitűnés kulcsa ebben a szegmensben, ahol az optimalizált marók megfelelő alkalmazása a motoralkatrész-megmunkálási műveletek teljes skáláján jelentős előnyökkel járhat.
A hagyományos és hibrid személygépkocsikhoz gyártott alumínium motorok száma évről évre növekszik. Valójában ma már évente közel 100 millió darabot gyártanak. Ezek a motorok gyakran összetett alakú alkatrészeket tartalmaznak, amelyek az öntés után változatos, de elengedhetetlen marási műveletek sorozatát igénylik.
A Sandvik Coromant mostantól teljes kínálattal rendelkezik a járműiparban alkalmazott alumíniummegmunkáláshoz, az első fázisú lapkialakítástól kezdve a nagyolásig, elősimításig és simításig. Minden egyedi marót úgy terveztek, hogy optimális minőséget és alkatrészenkénti költséget biztosítson. Az utóbbi elérése érdekében a termékcsalád egyes szerszámai többféle feladatot is ellátnak, például a ciklusidő csökkentése érdekében egyetlen műveletben elvégzik a nagyolást és a simítást.
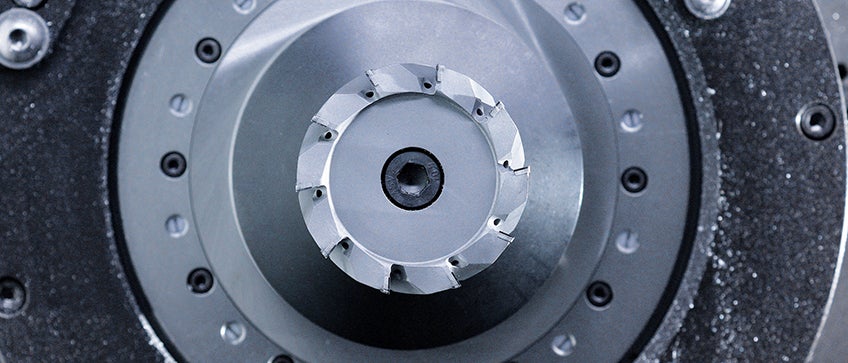
Ilyen például az M5C90, egy innovatív maró, amely a nagyolást és az elősimítást kombinálja egyetlen szerszámban. Az M5C90 egy nagy sebességű homlokmaró, amely egyedi kialakítású, hogy kiküszöbölje a hosszadalmas összeállítási időt az ügyfél létesítményében. Az M5C90 a hagyományos marókhoz képest kevesebb foggal dolgozik, ami elsősorban az egyedi radiális és axiális lapkaelhelyezésnek köszönhető a simítósoron/belső átmérőn (nincs szükség lapkabeállításra). Ez a pozicionálás biztosítja a sorjamentes marást és az optimális felületi minőséget a hengerfejeken, hengerblokkokon, fékrendszeri alkatrészeken és minden olyan alumínium alkatrészen, ahol széles fogásvétel érhető el (nem alkalmazható vékony falú alkatrészeken).
Az M5C90 alkalmazásával elérhető potenciális előnyök példájaként tekintsünk meg egy folyamatban lévő ügyfélesetet, amelyben egy AlSi12Cu1-ből készült fékrendszeri szeleptest érintett. A külső átmérőn 10 keményfém lapkából és a belső átmérőn 4 lapkából (plusz egy wiper lapka) álló elrendezésű szerszámot 8000 fordulat/perc orsófordulatszámon, 4021 m/perc (13 192 láb/perc) forgácsolási sebességgel és 0,25 mm/fog (0,009 col/fog) előtolással használják. Ezenkívül az axiális fogásmélység 2 mm (0,078 col), a radiális fogásmélység 140 mm (5,51 col), ami 5600 cm3/perc (342 col3/perc) fémeltávolítási sebességet eredményez. Bár a teljes éltartamot még meg kell határozni, 18 hónapos használat után is még mindig ugyanaz a szerszám van a gépben.
Azok számára, akiknek olyan maróra van szükségük, amely vékony falú alumínium alkatrészek, például sebességváltóházak és burkolatok simítására is alkalmas, a Sandvik Coromant kínál egy másik, ugyanilyen hatékony marót, az M5F90-et. Az M5F90 egy másik egy lépésben nagyoló és simító szerszám. A vékony falú alumínium alkatrészek megmunkálásához és süllyesztési műveletekhez készített marótest (25–80 mm, 0,98–3,15 col átmérőjű) keményforrasztott PCD-csúcsokat tartalmaz. Mindegyik csúcs tartalmaz egy nagyoló- és egy simítóélt. A nagyolási terület hagyományos marószerszámként működik, ahol minden forgácsolóél azonos átmérőjű és magasságú, míg a simítási terület radiálisan és axiálisan lépcsős forgácsolóélekből áll. Ez a koncepció lehetővé teszi a sűrű fogosztást, ami sorjamentes megmunkálást és kiváló felületi minőséget biztosít.
Lenyűgöző időmegtakarítás érhető el, amint azt egy ügyfél esete is mutatja, amely egy alumínium (magas Si-tartalmú) hengerfej homlokmarását tartalmazta. Itt az M5F90 használata egy versenytárs által gyártott speciális PCD-maróval szemben nemcsak 150%-os ciklusidő-megtakarítást eredményezett, hanem megszüntette a sorjaképződést is. Forgácsolási adatok: 15 915 fordulat/perc orsósebesség; 2000 m/perc (6562 láb/perc) forgácsolási sebesség; 0,16 mm/fog (0,006 col/fog) előtolási sebesség; és 1,5 mm (0,06 col) fogásmélység.
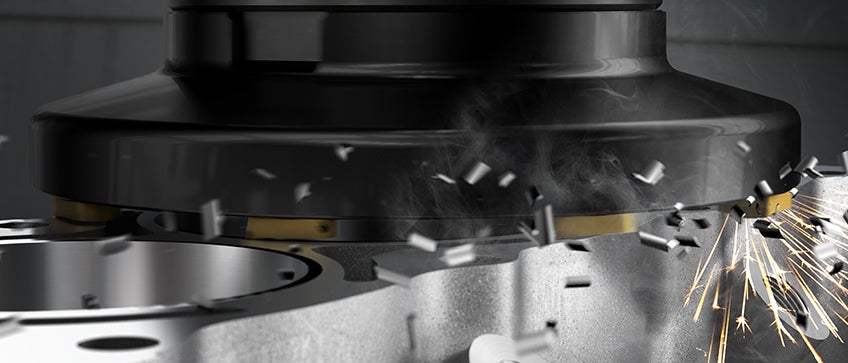
Egy másik M5F90-es példában 44%-os ciklusidő-csökkenést értek el egy alumínium lánchüvelyen egy versenytárs 63 mm (2,48 col) átmérőjű, hat PCD-lapkát tartalmazó, váltólapkás marójával összehasonlítva. Ráadásul a megoldás kiküszöbölte a korábban szükséges, kefével végzett sorjázási műveletet.
Egy másik új fejlesztésű szerszám az M610, amelyet a bimetál – jellemzően alumínium és szürkeöntvény – csatlakozásokkal rendelkező motorhengerblokkok illesztőfelületének/tetejének marására fejlesztettek ki.
A különböző termikus és mechanikai tulajdonságok kihívást jelentenek a bimetál anyagok megmunkálásában. A meglévő marók ehhez az alkalmazáshoz bonyolultak és beállításra szorulnak, ami a gyártási teljesítmény csökkenését eredményezi. Ezenkívül az ilyen szerszámok gyakran okoznak kitöredezést az alkatrész szürkeöntvény részein.
Ezzel szemben az M610 nem igényel összeállítást és beállítást, és nagy előtolási sebességet tesz lehetővé az alkatrészeken kialakuló kitöredezés, sorják vagy karcolások nélkül. Ez a képesség fontos, mivel a felületi tökéletlenségek szivárgást okozhatnak a hengerblokk és a hengerfej között, ami viszont csökkenti a teljesítményt. Néhány globális járműipari OEM máris profitál az M610 bevezetéséből.
Egy konkrét ügyfélre hivatkozva, óriási versenyelőnyt értek el a bimetál motorblokkok égéstéri felületének simításakor. Egy versenytárs betétes, állítható marójával szemben az M610 833%-os éltartamjavulást ért el, több mint 4000 alkatrész elkészítésével, szemben a versenytárs 480 darabos marójával. Ráadásul az M610 10-szer nagyobb sebességgel dolgozott. A 15 lapkás M610 forgácsolási adatai: 3000 m/perc (9843 láb/perc) forgácsolási sebesség 5720 mm/perc (225 col/perc) előtolási sebesség 3820 ford/perc orsófordulatszám 0,15 mm/fog (0,006 col/fog) előtolási sebesség és 0,5 mm (0,02 col) fogásmélység az alumíniumon és 0,05 mm (0,002 col) az öntöttvason
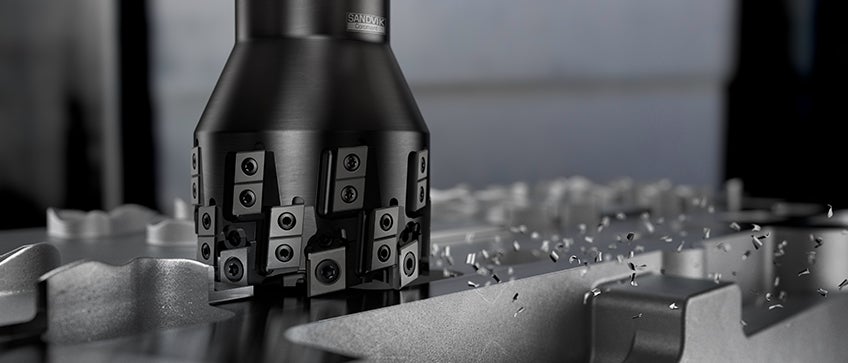
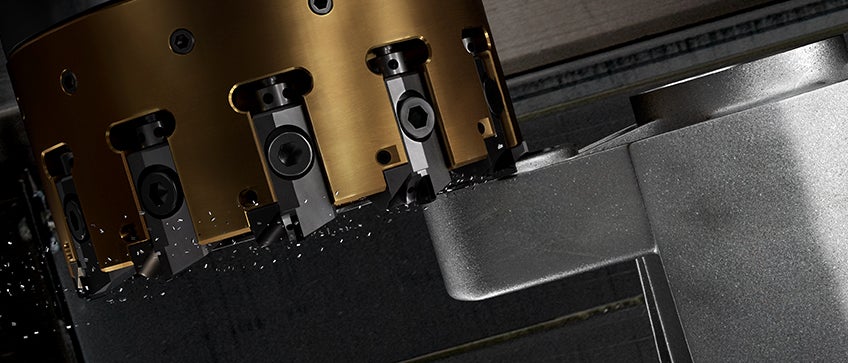
A termékcsalád további szerszámai közé tartozik az M5Q90 tangenciális nagyolómaró, amely az első lapkialakítást (az oldalak első megmunkálása az öntés után) egyetlen műveletben, sorja nélkül végzi el. A szerszám tangenciális PCD-lapkákkal rendelkezik, amelyek sima és stabil forgácsolási műveletet biztosítanak az energiafogyasztás csökkentése és a rezgések kiküszöbölése érdekében.
Az alumínium hengerfejek és -blokkok az M5Q90 előnyeit élvező alkatrészek közé tartoznak. Egy öntött hengerfejen végzett lapolási művelet például jellemzően a vezérműtengelyi felület, a bemeneti/kimeneti felület és az égéstéri felület megmunkálását foglalja magában. Egy ügyfél esettanulmánya szerint az AS-9 alumíniumötvözetből öntött hengerfejek nagyoló homlokmarása egy vízszintes megmunkálóközponton rendkívül lenyűgöző éltartameredményeket hozott. 3000 m/perc (9843 col/perc) forgácsolási sebességgel, 0,2 mm (0,008 col) fogankénti előtolással és 2,0 mm (0,079 col) axiális fogásmélységgel (40 mm-ig (1,57 col) teljesen fogásban) több mint 10 000 alkatrész készült el.
Az M5R90 egy további szerszám a második fázisú nagyoláshoz/elősimításhoz. Ez a standard maró állítható betétekkel működik, és a használt betéttől függően 0,4 vagy 0,8 mm-es (0,016 vagy 0,031 col) sugárral akár 8 mm-es (0,315 col) fogásmélységet is támogat. A könnyen beállítható betétek számos járműipari alkalmazásban előnyösek, amint azt egy nemrég elvégzett ügyfélkísérlet is mutatja, amely egy motorburkolat homlokmarását foglalta magában. Az MRHB Si12 alumíniumötvözetből öntött M5R90 rendkívül kedvezően teljesített a versenytársakkal szemben. Azonos forgácsolási adatok alapján az M5R90 a szerszám éltartamát 8000-ről 10 000 munkadarabra növelte. Ráadásul a versenytárs marót 1000 darab után be kellett állítani a betét mozgása miatt, ami veszélyeztette a felületi minőséget. Ezzel szemben az M5R90 8000 darabot gyártott, mielőtt a betét bármilyen beállítására szükség lett volna.
A termékcsaládhoz tartozik az M5B90 szupersimító homlokmaró is, amely a lapkák egyedülálló axiális és radiális elhelyezésével rendelkezik. Ez a konfiguráció a wiper lapkákkal együtt kiváló felületi minőséget és sorjamentes forgácsolást biztosít, ahogy a személygépkocsik hengerfejének gyártásával foglalkozó egyik gyártó is megtapasztalta. A vállalat folyamatinstabilitást és marással kapcsolatos problémákat tapasztalt, míg egy másik probléma a lapkák kiszámíthatatlan éltartama volt, amely a patron beállításától függött, ami összeállításonként eltérő volt. Az M5B90 maróra való átállás zökkenőmentes, kiszámítható kopással és sorjamentességgel járó simítási műveletet biztosított. A szerszám csak nagyon vékony forgácsot képez, amely a forgácsolási folyamat során könnyen eltávolítható, így elkerülhető az alkatrész felületének sérülése. Ezenkívül az M5B90-re való áttérés átlagosan 30 000-ről 45 000 darabra növelte az éltartamot.
A CoroDrill® és a CoroTap® család fúró és menetfúró szerszámai, valamint a standard CoroMill® Century 590 simító homlokmaró ugyanezen megoldáscsalád részeként kínálhatók az ügyfeleknek az alumínium járműipari alkatrészek megmunkálásához.
A ciklusidő és az alkatrészenkénti költségek csökkentésének lehetősége minden esetben nagyon is valós, miközben a szerszámok éltartama és az alkatrész minősége javul, amint azt a leírt ügyfélesetek is mutatják. A járműiparban, ahol a nagy tételszámú gyártás jellemző, már egy kis ciklusidő-megtakarítás is jelentős pénzügyi megtérüléssel járhat. Ezt a gondolatot szem előtt tartva, nem igazán lehet figyelmen kívül hagyni egyetlen olyan technológiát sem, amely bizonyítani tudja, hogy képes nagyobb nyereséget kínálni.