Hatásos módszer a mikrohibák leküzdésére
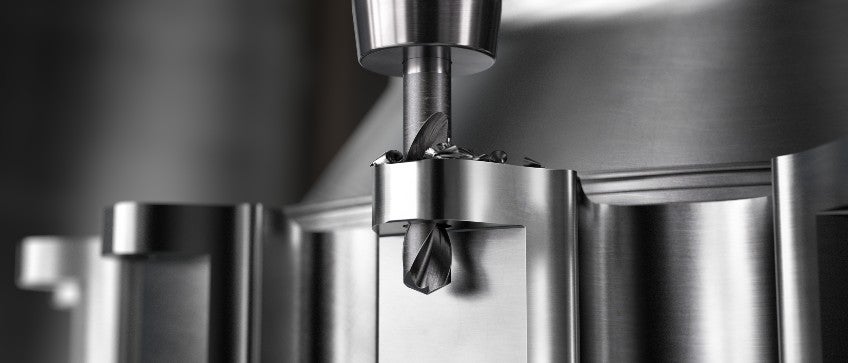
A továbbfejlesztett kialakítású keményfém fúróval végzett tesztek új lehetőségeket nyitnak a furatminőség terén.
A „mérj kétszer, vágj egyszer” a gyártásban elterjedt kifejezés, de ezt könnyebb mondani, mint megtenni a kihívást jelentő anyagok megmunkálásakor. Ezért fordult egy vezető globális repülőgépgyártó a fémforgácsolás globális piacvezető vállalatához, amikor a fúrási folyamatokból egy teljes második fázis kiiktatására törekedett, a furatok minőségének javítása mellett a repülőgép-alkatrészekben. Itt James Thorpe, a Sandvik Coromant globális termékmenedzsere, elmagyarázza, hogy a fúró kialakítása miért kifejezetten fontos a jobb minőségű furatok létrehozásában.
A megmunkálási folyamatok közül a legelterjedtebb a furatkészítés, és ezt veszik a leggyakrabban magától értetődőnek. Sok műhely kevés okot lát a meglévő furatkészítési beállítások megváltoztatására vagy frissítésére, és évek óta ugyanazokat a szerszámokat és forgácsolási paramétereket használja. A COVID-19 világjárvány kiszámíthatatlan hatásaival kezdődően azonban mindez megváltozott. A gyártók kiszámíthatatlan és tartós változásokkal szembesültek a vásárlói piacokon, és most úgy látják, hogy szükség van a gyártás adaptálására.
A legtöbb gyártó például új szállítói bázisokat és termékeket keres. Tehát azok a műhelyek, amelyek valamikor a gyártás egy bizonyos területére szakosodtak, CNC-esztergákat és -marókat nyitnak meg a szívós és kihívást jelentő anyagok szélesebb választéka előtt. Ugyanakkor a gyártóknak új utakat kell keresniük a nyereség növelésére és a ciklusidő csökkentésére, a termékminőség feláldozása nélkül.
Más szóval itt az ideje, hogy a gyártók átgondolják, hogyan készítenek furatokat.
A fehér réteg
A furatfelület integritása valódi aggodalomra adhat okot a repülőgépipari gyártók vagy azon általános gépészeti vállalatok számára, akik szeretnének diverzifikálódni a repülőgépipar felé. A jobb furatminőség létfontosságú az alkatrészek meghibásodásának megelőzésében, és ezt nagyban meghatározzák a furatok megmunkálásához vagy simításához használt gyártási folyamatok.
A szerszámmegoldások és a fúrók forgácsolóél-geometriája folyamatosan fejlődnek, hogy megfeleljenek a legmagasabb gyártási és alkatrész-minőségi követelményeknek. A hűtőközeg használata szintén segít csökkenteni a hőfelhalmozódást a szerszámon. És a tesztek szerint ezek a tényezők mindegyike képes szabályozni az úgynevezett „fehér réteg” hatást a munkadarabanyagban.
A fehér réteg kifejezést a világ egyik vezető repülőgépipari gyártója találta ki, amely egyben a Sandvik Coromant ügyfele is. Olyan vékony, rendkívül finom szemcseszerkezetre utal, amely az alkatrészfúrás után figyelhető meg, és amelyet a fúró hője okoz. A fehér réteg nem csak megváltoztathatja az anyag felületi tulajdonságait, hanem elfogadhatatlannak ítélték az ügyfél minőségirányítási folyamataiban.
A gyártó szigorú furatsimítási eljárást alkalmaz a repülőgépipari alkatrészek – beleértve a turbinatárcsákat, kompresszorokat, dobokat és tengelyeket – furatainál. Ezért választotta a Sandvik Coromant vállalatot partneréül, hogy kivizsgálja, miért képződik a fehér réteg, és hogyan lehet ezt szabályozni.
Fontos megjegyezni, hogy a teszteket nem csak a minőségirányítás motiválta. A felső vezetés szintjén az ügyfél csökkenteni kívánta a teljes üzemeltetési időt, illetve növelni a nyereséget úgy, hogy kiiktat egy teljes másodlagos megmunkálási folyamatot.
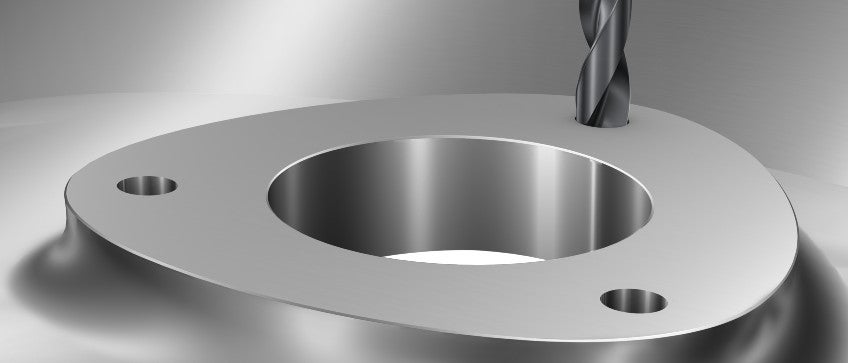
A furatfelület integritása valódi aggodalomra adhat okot a repülőgépipari gyártók vagy azon általános gépészeti vállalatok számára, akik szeretnének diverzifikálódni a repülőgépipar felé. Itt egy HRSA ház kiálló részének fúrása látható a CoroDrill 860 -SM geometriával.
Második felvonás
A másodlagos folyamat azután következik, hogy a keményfém fúróval furatot készítettek, és tartalmazhat dörzsárazást, süllyesztő vagy szármarást az alkatrész simításához. A másodlagos szakasz elsősorban a felületi integritási követelmények kielégítésére szolgál – csökkentve a fehér réteghez hasonló problémákat –, és nem a méretpontosságot szolgálja, kivéve a szoros tűrésű furatok megmunkálásakor.
Az átfogó költségek szempontjából a másodlagos folyamat még drágább is, mint az alacsony forgácsolási adatok fenntartása, ami a felületintegritás megőrzésének másik módja. Ezért akarta a Sandvik Coromant ügyfele megvizsgálni, hogy ki lehet-e iktatni a teljes folyamatot. Ha a termék beszállítója a méretnek megfelelő furatot gyárt, másodlagos folyamatok nélkül, az erős üzleti helyzetbe juttatja az alkatrészenkénti költség csökkenésének köszönhetően.
A fehér réteg okainak és lehetséges megelőzési módjainak vizsgálata négy tesztből állt, amelyek során a repülőgépiparban népszerű, nagy szilárdságú, nikkel-króm anyagban, az Inconel 718-ban végeztek fúrásokat. Az ügyfél először végzett ilyen vizsgálatot.
A tesztek során a Sandvik Coromant, a CoroDrill® R840 és a CoroDrill® R846 tömör keményfém fúrójával végzett fúrásokat értékelték ki. Mindegyikhez a forgácsolási paraméterek különböző készleteit alkalmazták: rendre 58 mm/perc, illetve 98 mm/perc, és 829 ford/perc, illetve 757 ford/perc. A forgácsolóerőt, a nyomatékot és a fehér réteg vastagságát végig mérték a tesztek során.
E tesztek óta a CoroDrill R840 helyébe a -GM geometriájú CoroDrill® 860, a CoroDrill R846 helyébe pedig az -SM geometriájú CoroDrill® 860 lépett. Ezen következő generációs szerszámok mindegyike úgy lett kialakítva, hogy tovább növelje a szerszám éltartamát, anélkül, hogy rontaná a furatminőséget.
Az eredmények értékes betekintést nyújtottak a fehér réteg vastagságának okaiba. Különösen figyelemre méltó volt, hogy a CoroDrill R846 kevesebb fehér réteget hozott létre, ami az íves és radiális vágóélek előkészítésének köszönhető. A CoroDrill R840 forgácsolóélének egyenes élei és élletörései pedig vélhetően összefüggenek a forgácsolóerő, a forgatónyomaték és a fehér réteg vastagságának növekedésével. Tehát a fúró kialakítása határozza meg, hogy elérhető-e magas furatminőség, csökkentett fehér réteggel, a forgácsolási adatok feláldozása nélkül.
A globális repülőgépgyártó Sandvik Coromanttal együtt végzett tesztjei nemcsak feltártak egy-két dolgot a fehér rétegről, de a vállalat néhány másodlagos folyamatot is ki tudott iktatni, mint például a dörzsárazás és a süllyesztőmarás, ami idő- és költségelőnyökkel járt. Sőt, az eredmények a Sandvik Coromant CoroDrill 860 keményfém fúró kialakítását is igazolták.
Jobbnak tervezett
A termékcsalád magában foglalja a már említett -GM geometriájú CoroDrill 860-at, amelyet úgy terveztek, hogy jó általános teljesítményt nyújtson kihívást jelentő ISO P-, M-, K- és H-anyagok fúrásában minden ipari ágazatban. Az -SM geometriájú CoroDrill 860 optimalizálva van az ISO S minőségek, például a hőálló szuperötvözetek (HRSA), a titán és az Inconel megmunkálására. Ez utóbbi fúró különösen népszerűnek bizonyult a repülőgépiparban.
A -GM geometriájú CoroDrill 860 és az -SM geometriájú CoroDrill 860 esetében a Sandvik Coromant mérnökei azt az elvet alkalmazták, hogy a hosszabb éltartam és a jobb furatminőség a fúró kialakításán múlik. A -GM geometriájú CoroDrill 860 innovatív, polírozott horonykialakítással rendelkezik, amely javítja a forgácselvezetést, és nagy magszilárdságot és csökkentett forgácsolóerőket eredményez fúrás közben.
Az -SM geometriájú CoroDrill 860 pedig új minőséggel, optimalizált és finomított csúcsgeometriával rendelkezik, ami tovább növeli a szerszám éltartamát, ha nehezen megmunkálható HRSA-anyagokkal dolgozik. Az eredmény jobb furatminőség.
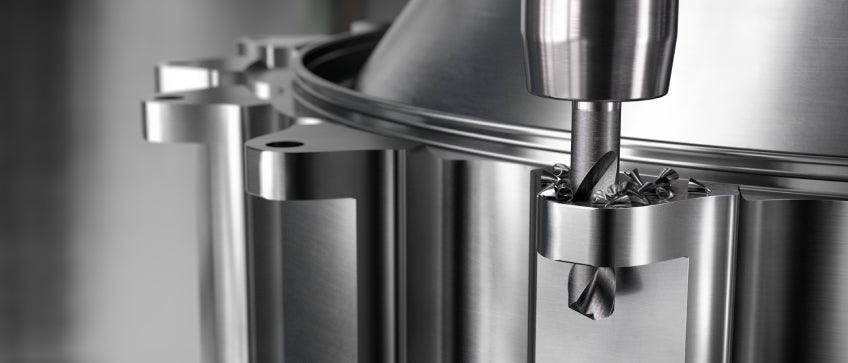
Az -SM geometriájú CoroDrill® 860 kialakítása hosszabb éltartamot és jobb furatminőséget kínál.
A CoroDrill 860 már a piacot megelőző tesztek során bizonyított számos ágazatban. Egy franciaországi gépipari vállalat a -GM geometriájú CoroDrill 860-at AISI 4140 szerkezeti acélon alkalmazta. A fúró konkáv és konvex belépéssel egyaránt képes volt minőségi fúrást biztosítani, jó egyenességgel és tűréssel. A társaság azóta új üzleti kapcsolatot létesített a Sandvik Coromanttal.
Egy másik Sandvik Coromant-ügyfél, egy olasz általános gépgyártó több mint 45%-os termelékenységnövekedést ért el a -GM geometriájú CoroDrill 860 használatával az erős, 34CrNiMo6 acélötvözet megmunkálásakor, szemben egy versenytárs fúrójával. Emellett 100%-kal hosszabb éltartamot ért el. Máshol a -GM geometriájú CoroDrill 860 lenyűgöző eredményeket ért el az Inconel 718 megmunkálásában. A lengyelországi Katowicében végzett tesztek során az -SM geometriájú CoroDrill 860 szerszámmal 180%-kal jobb élettartamot sikerült elérni a CoroDrill R840 szerszámmal szemben.
Az iparágtól függetlenül – legyen az repülőgépipar, általános gépészet vagy egyéb terület – magas szerszámteljesítmény érhető el, ha a fúrót megfelelően az adott célra tervezték. Eközben a további online eszközök, például a Sandvik Coromant CoroPlus® Tool Guide további segítséget nyújthatnak. Az internetes böngészőn keresztüli online alkalmazáshoz, valamint a munkadarab anyagának, a furatátmérőnek és -mélységnek a meghatározásával a felhasználók megtalálhatják az igényeiknek megfelelő legjobb kerek tömör körszerszámokat és forgácsolási adatokat.
Bár a „mérj kétszer, vágj egyszer” fúrás még nem valósult meg, a -GM geometriával és az -SM geometriával rendelkező CoroDrill 860 teljesítménye segít a gyártóknak újragondolni a furatok készítésének módját.