Zöldebb jövő a repülőgépipar számára
Az OEM-gyártóknak holisztikusan kell megközelíteniük a holnap repülőgépeit.
A globális CO2-kibocsátás egyik legnagyobb okozójaként a repülőgépiparra sürgető nyomás nehezedik, hogy környezetbarátabb, könnyebb és nagyobb távolságokat megtenni képes repülőgépeket állítson elő. Ennek eléréséhez azonban nehezen megmunkálható alumínium- és hőálló szuperötvözetekkel (HRSA) kell dolgozni. Sébastien Jaeger, a Sandvik Coromant repüléstechnikai iparági megoldásokért felelős vezetője elmagyarázza, hogyan alkalmazhatnak a repülőgépgyártók fejlett szerszámmegoldásokat e szívós alkatrészek fenntartható megmunkálásához.
A Világgazdasági Fórum (WEF) szerint „a nettó nulla CO2-kibocsátás elérése 2050-ig nemcsak a környezeti szempontból fenntartható jövő megteremtéséhez járul hozzá, hanem egy pénzügyileg rugalmas és versenyképes légiközlekedési ágazat egészének biztosításához is”. Míg azonban az autóiparban az e-mobilitás egyre inkább teret nyer – és 2021 augusztusában az elektromos járművek eladásai az Egyesült Királyságban megelőzték a dízelüzemű járművek eladásait –, addig a repülőgépiparban ezek a fejlesztések csak később fognak megvalósulni.
Általában véve az elektromos meghajtású repülőgépek várhatóan csak 2035-ben fognak széles körben elterjedni. A Lonely Planet beszámolója szerint – bár az easyJet 2030-ra elektromos repülőgépeket kíván üzemeltetni a 311 mérföld (500 km) alatti útvonalakon, Norvégia pedig 2040-re minden rövid távú járatot elektromos meghajtásúvá kíván tenni – „a közeljövőben nem fogunk újratölthető Jumbókkal hosszú távú járatokat teljesíteni: az akkumulátorok egyszerűen túl nehezek.”
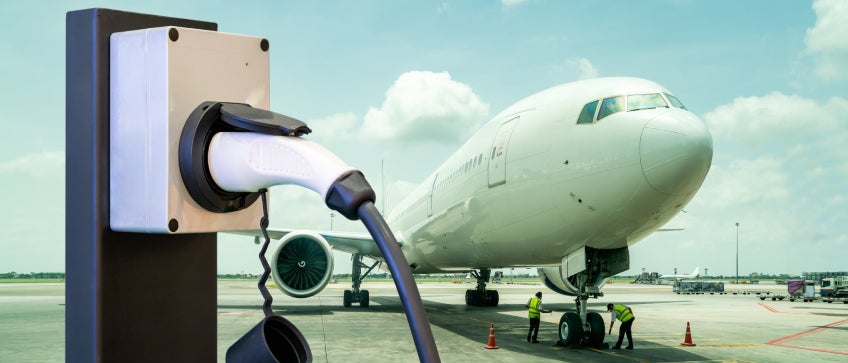
A villamosított repülőgépek várhatóan 2035-ben válnak széles körben elterjedtté.
Tehát, bár az akkumulátoroknak könnyebbé kell válniuk ahhoz, hogy hihető legyen, az eredeti berendezésgyártókra (OEM) is egyre nagyobb nyomás nehezedik, hogy könnyebb alkatrészeket gyártsanak a probléma ellensúlyozására. Biztosak lehetünk abban, hogy az alumíniumot – pontosabban a nagyobb szilárdsággal, fáradásállósággal és egyéb tulajdonságokkal rendelkező új alumíniumtípusokat – fogják felhasználni ahhoz, hogy ezek a rendszerek könnyebbek legyenek.
Az új hőálló szuperötvözetek (HRSA-k) felhasználásának növekedését is tapasztaljuk. A HRSA-kat már használják olyan repülőgép-alkatrészekben, amelyek extrém teljesítményigényűek, mivel intenzív hőhatás esetén is megőrzik keménységüket. Ezek az anyagtulajdonságok alapvető fontosságúnak bizonyulnak, mivel a fenntarthatóbb légi közlekedés egyik megközelítése az lesz, hogy a motorokat keményebben és forróbban égetik majd.
Az alkatrészeket szigorúbb tűréshatárok és változatosabb kialakítások mellett kell gyártani. Az e-autókhoz hasonlóan a holnapi elektromos repülőgépek tervei – beleértve a repülőgépvázakat és a motorokat is – gyártónként jobban fognak különbözni, mint a jelenlegi belső égésű motorral hajtott repülőgépeké. A repülőgép vázát illetően egyes OEM-gyártók a delta alakú, kevert szárnytestű és merevítőrácsos szárnykoncepciókat vizsgálják. Más OEM-gyártók ragaszkodnak a hagyományos „nagy henger, szárnyak és motor” kialakításhoz.
A motorok felépítésének különböző formái is léteznek majd, mint például a villamosított, akkumulátoros vagy elektromágneses, illetve a hibrid motorok, ahol a jelenlegi motorokat elektromos motorok segítik. Az OEM-gyártóknak egyre többféle alkatrészt kell majd gyártaniuk szigorú tűréshatárok között, miközben új módszereket kell találniuk a zaj, a tömeg és a károsanyag-kibocsátás csökkentésére – ezek mind olyan tényezők, amelyek befolyásolják az elektromos rendszerek teljesítményét. Az alumínium és a HRSA alkatrészek azonban nehezen megmunkálhatók, így ennek fenntartható és költséghatékony megvalósítása kihívást jelent.
Gyors fejlődés
A könnyebb és üzemanyag-hatékonyabb repülőgépek gyártásának egyik módja az additív gyártási (AM) technológia. Az AM lehetővé teszi nagyon összetett alakú, egyedi alkatrészek és funkcionális termékek kifejlesztését szoros tűrésekkel, így a nehezen megmunkálható alkatrészek, például rácsok könnyebben megmunkálhatók. A Dassault Systemes szoftvercég megállapításai szerint „a repülőgépiparban az AM-eljárásokból származó súlycsökkentés akár 25 százalékos energiamegtakarítást is eredményezhet”, míg „minden egyes kilogrammnyi (2,2 láb) súlycsökkenés egy repülés során évente akár 3000 dollárnyi üzemanyagot is megtakaríthat”.
De fenntartható-e maga az AM-gyártás? A romániai Kolozsvári Műszaki Egyetem Gyártástechnika Tanszékének közreműködésével készült tanulmány szerint az AM „nagyszerű alternatívája a hagyományos gyártási (TM) módszereknek, mint például az öntés, a fröccsöntés vagy a megmunkálás”. Így folytatódik: „Az AM csökkentheti a költségeket és energiahatékonyabb lehet, mint a hagyományos eljárások.”
Az AM döntő hatással lesz a termékek előállításának módjára és sokféleségére is. Az előnyök közé tartozhat a csökkentett szén-dioxid-kibocsátás, a kevesebb anyagfelhasználás és a kevesebb szállítás, mivel az alkatrészek import helyett házon belül készülhetnek.
A gyártók a gyors prototípusgyártás révén összetettebb, kompaktabb és innovatívabb repülőgép-alkatrészeket is előállíthatnak. A gyors prototípusgyártás több különböző technikára utal, de a cél egy kézzelfogható 3D prototípus gyors előállítása egy számítógéppel segített tervezési (CAD) fájlból. Ezekkel a prototípusokkal az új anyagok kis sorozatban történő kipróbálását lehet elvégezni a teljes körű gyártás előtt, hogy az alkatrészek a lehető legnagyobb innovációval, minőséggel és pontossággal készüljenek.
Megvizsgáltuk, hogy a repülőgépipari OEM-ek hogyan alkalmazhatnak új módszereket a bonyolultabb alkatrészek gyártásánál. De mi a helyzet a megfelelő szerszámokkal a munkához – különösen a szívós alumínium és a HRSA megmunkálásakor?
Ezek az anyagok nagyobb kopásállóságú és hosszabb élettartamú szerszámok használatát teszik szükségessé. Ezért fejlesztette ki a Sandvik Coromant az S205-ös minőséget az esztergáláshoz használt acéllapkákhoz. Az S205 fémszerkezetében egy Inveio® réteg szorosan egymáshoz illesztett, egyirányú kristályokból áll. Ez egy erős védőgátat hoz létre a lapka körül, amely megerősíti a szerszámot és javítja annak mechanikai tulajdonságait. A lapka már bizonyítottan hasznosnak bizonyult számos repülőgép-alkatrész, többek között hajtóművek turbinatárcsáinak, gyűrűinek és tengelyeinek gyártásánál. A Sandvik Coromant ügyfelei már beszámoltak arról, hogy a konkurens HRSA esztergagépekhez képest 30–50%-kal nagyobb vágási sebességet értek el az S205-tel.
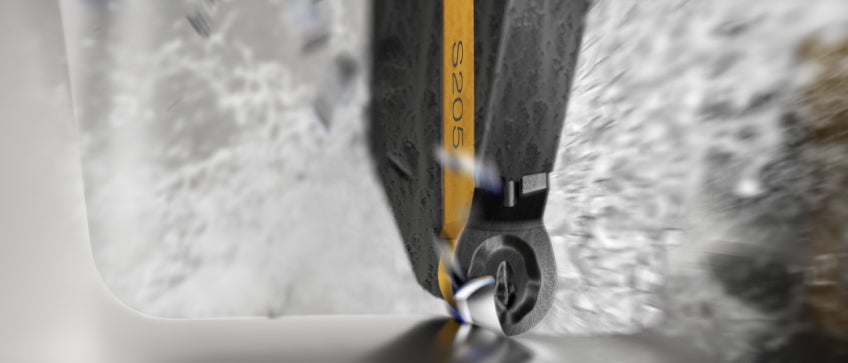
Holisztikus megközelítés
Átgondoltuk a gyártási folyamatokat és az eszközöket, de hogyan lehet a legjobban kombinálni a kettőt? Végül is, egy teljesen integrált megoldás összeállítása időveszteséggel járhat, ha a rendszereket nem úgy tervezték, hogy jól működjenek együtt.
Ennek érdekében a Sandvik Coromant az úgynevezett komponensmegoldással támogatja ügyfeleit a repülőgépiparban. A megoldás több szakaszból áll, beleértve a gépigény és az alkatrészenkénti költséget vizsgáló idővizsgálatokat. Továbbá, a gyártási módszerek elemzése a kifutásnál, mind a Módszerek-idő méréssel (MTM), mind a végfelhasználói folyamatokkal kapcsolatban. Az alkatrészmegoldás magában foglalja a számítógéppel támogatott gyártás (CAM) programozását és a helyi vagy határokon átnyúló projektek menedzsmentjét is.
A Sandvik Coromant egyik ügyfelének, akinek a gyártása során forgácstörési problémákkal kellett szembenéznie, az alkatrészmegoldás lehetővé tette számunkra, hogy felismerjük az okot és megoldást találjunk. Az ügyfél számára a Sandvik Coromant szakemberei új stratégiát dolgoztak ki dinamikus hajtási görbékkel, amelyek lehetővé tették, hogy minden pillanatban szabályozzuk a forgácstörést. Ezt az új megközelítést „tölcséresztergálásnak” neveztük el, és most szabadalmat is kaptunk rá. A tölcséresztergálással az ügyfél 80%-os ciklusidő-csökkenést ért el, nagyszerű forgácskezeléssel és megduplázott szerszáméltartammal.
Ráadásul az ügyfél négy gép használatát egy gépre tudta csökkenteni, csökkentve a multitasking szükségességét, biztonságosabb megmunkálási folyamatokkal és folyamatos termeléssel. A fenntarthatóbb repülőgépgyártás kulcsa a csökkentett géphasználat és a kevesebb szerszámcserével történő gyártás lesz, köszönhetően az olyan szívósabb megmunkálási minőségeknek, mint az S205.
A szoftverek is fontos szerepet játszanak majd, mint például a CoroPlus® Tool Guide, amely a Sandvik Coromant digitális portfóliójának része. Az ügyfelek már a gyártás megkezdése előtt fontos döntéseket hozhatnak a szerszám és a vágási paraméterek kiválasztásáról.
A kör bezárul
A szerszámok és a gyártás új megközelítései mellett a repülőgépipari OEM-ek a gyártáshoz is fordulhatnak. Az Air Transport Action Group (ATAG) jelentése szerint a Kaiser, amely a Boeing alumíniumot szállító vállalata, ma már zártkörű újrahasznosítási rendszert alkalmaz – ez az egyik legnagyobb ilyen jellegű program az iparágban. A Kaiser becslései szerint a rendszer révén évente mintegy tízmillió kilogramm selejtet és fémhulladékot hasznosít újra az ipar.
A Sandvik Coromantnál saját körkörös rendszert indítottunk a keményfém szerszámok újrahasznosítására, amelynek keretében visszavásároljuk az ügyfelek elhasználódott keményfém szerszámait, és újra felhasználjuk őket vadonatúj szerszámok készítéséhez. Ennek eredményeként a Sandvik Coromant cementkarbid szerszámaihoz használt nyersanyagok többsége hulladékból származik. Fenntartható üzleti tevékenységet folytatunk a korlátozott erőforrásokkal rendelkező környezetben, és minimalizáljuk a túlzott hulladék mennyiségét. Ennek során azt tapasztaltuk, hogy az újrahasznosított anyagból készült szerszámok előállításához 70%-kal kevesebb energiára van szükség, miközben 40%-kal kevesebb szén-dioxidot bocsátunk ki.
A repülőgépiparra egyre nagyobb nyomás nehezedik, hogy környezetbarátabb, könnyebb és nagyobb távolságokat megtenni képes repülőgépeket gyártson. A megfelelő folyamatokkal és eszközökkel azonban – nem is beszélve a gyártás holisztikusabb megközelítéséről – a repülőgépgyártó OEM-ek is hozzájárulhatnak a repülőgépipar környezetbarátabb jövőjének megteremtéséhez.