Sådan opnår du god emnekvalitet i drejning
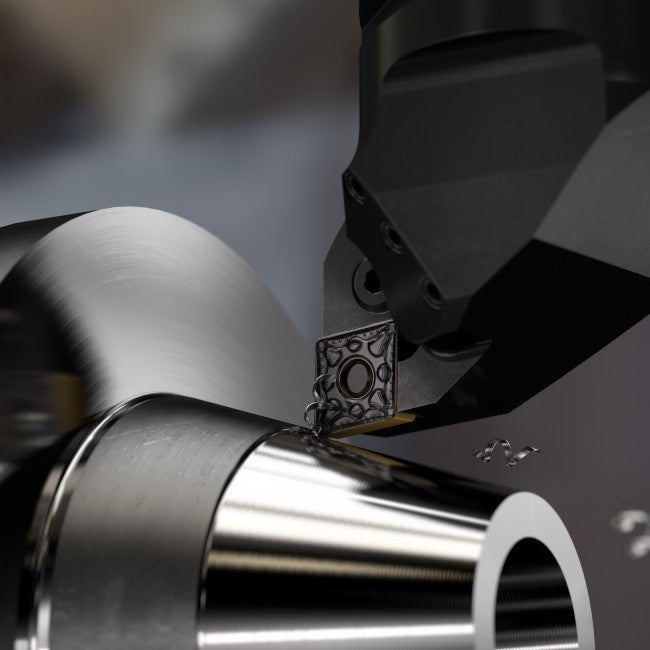
Spånkontrol er en af de vigtigste faktorer for at fremstille drejede emner af høj kvalitet. Vælg de korrekte skæredata, og følg vores applikationstips for god emnekvalitet.
Vellykket spånkontrol
Spånkontrol er en af de vigtigste faktorer inden for drejning, og der findes tre grundlæggende alternativer:
- Selvbrydende (f.eks. gråt støbejern)
- Brydning mod værktøjet
- Brydning mod emnet
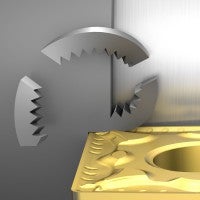
Selvbrydende
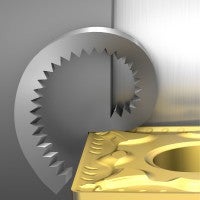
Brydning mod værktøjet
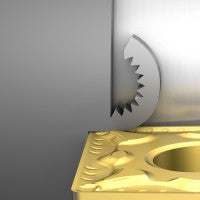
Brydning mod emnet
Faktorer, der påvirker spånbrydningen
- Skærgeometri: På basis af bredden af spånformeren og designet af mikro- og makrogeometri vil spånen være åben eller mere sammenpresset
- Næseradius: Mindre næseradius kontrollerer spånen bedre end en større næseradius
- Indgrebs- (hoved)vinkel: Afhængig af vinklen dirigeres spånen på forskellige måder: mod emnet eller væk fra emnet
- Spåndybde: Afhængig af emnematerialet vil en større spåndybde påvirke spånbrydningen, hvilket medfører større kræfter til at bryde og fjerne spånen
- Tilspænding: Højere tilspænding vil generelt skabe kraftigere spåner. Kan i nogle tilfælde hjælpe med spånbrydningen og spånkontrollen
- Skærehastighed: Ændring af skærehastigheden kan påvirke spånbrydningen
- Materiale: Et kortspånet materiale (f.eks. støbejern) er generelt let at bearbejde. Ved materialer med fremragende mekanisk styrke og modstandsdygtighed over for krybning
(solide materialers tendens til langsomt at bevæge sig eller blive deformeret under påvirkning, f. eks. Inconel) er spånbrydningen et større problem
Skæredata for drejning
Overvej altid maskine, værktøj, skær, og materiale, når du skal vælge den korrekte hastighed og tilspænding til drejning.
- Start med lav tilspænding for at sikre skærsikkerhed og overfladekvalitet, øg tilspændingen for at forbedre spånbrydningen
- Kør med en spåndybde, der er større end næseradiusen. Dette minimerer skærets radiale afbøjning, noget der er vigtigt ved indvendig bearbejdning
- For lavt indstillet skærehastighed medfører for kort værktøjslevetid. Brug altid den anbefalede skærehastighed, vc m/min. (ft/min.)
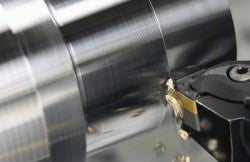
Sådan forbedres det drejede emnes kvalitet med brug af køling
Med korrekt køling øges processikkerheden og forbedres værktøjets performance og emnets kvalitet. Overvej følgende ved brug af køling:
- Det anbefales kraftigt at anvende værktøjer med præcisionskøling til sletbearbejdning
- Det nødvendige kølevæsketryk til at bryde spånen afhænger af dysediameter (udgang), materialet der bearbejdes, spåndybde og tilspænding
- Det nødvendige kølevæskeflow afhænger af trykket og af kølevæskehullernes samlede størrelse/areal
- I medium- og skrubdrejningsapplikationer anbefales det at bruge underkøling
- Til sletdrejning anbefales det at bruge både præcisionskøling og underkøling
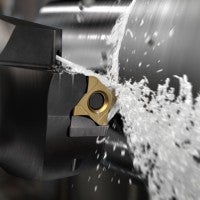
Løs udfordringer med korrekt anvendt køling
- Problemer med spånkontrol: Brug overkøling
- Problemer med dimensioner: Forårsages normalt af for høj temperatur – brug både over- og underkøling og så meget tryk som muligt
- Dårlig overfladekvalitet: Brug overkøling, hvis defekten forårsages af spåner
- Uforudsigelig værktøjslevetid i skrubdrejning: Brug kun underkøling
- Uforudsigelig værktøjslevetid i sletdrejning: Brug både over- og underkøling
- Dårlig spånafgang ved indvendige operationer: Brug både over- og underkøling, og så højt tryk som muligt
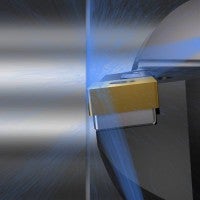
Sådan anvender du kølevæske og skærevæske ved drejning
Sådan opnår du en god overfladekvalitet på drejede emner
Generelle regler for overfladekvalitet:
- Overfladekvaliteten kan ofte forbedres ved at bruge en højere skærehastighed
- Skærgeometrien (neutrale, positive og negative spånvinkler samt positive frigangsvinkler) har indflydelse på overfladekvaliteten
- Valget af skærkvalitet påvirker i nogen grad overfladekvaliteten
- Vælg en mindre næseradius, hvis der er tendens til vibrationer
Wiperskær
Wiperskær kan udføre drejning af emner ved høje tilspændingshastigheder – uden at miste evnen til at frembringe en god overfladekvalitet eller spånbrydningsevnen.
En generel vejledning er: Fordobling af tilspænding = samme overfladekvalitet. Samme tilspændingshastighed – dobbelt så god overfladekvalitet.
Wiperskær er designet til ved tilspændingen at udglatte den bearbejdede overflade og derfor er effekten primært til længde- og plandrejning.
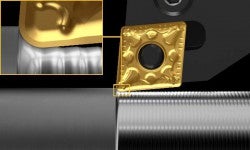
Standardradius
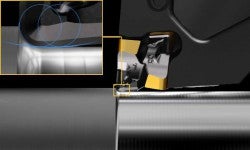
Wiper-radius
Sammenligning, standardskær versus wiperskær baseret på tilspændingshastighed
Bemærk! Alle værdierne for standardradius er teoretisk set beregnet. Værdierne for wiperradier tager udgangspunkt i eksperimentelle værdier i lavtlegeret stål.
Tilspænding mm (tommer) | Standard RE 0,4 mm (0,016 tommer) Ra µm (µtomme) | Wiper (-WF/-WM) RE 0,4 mm (0,016 tommer) Ra µm (µtomme) | Standard RE 0,8 mm (0,031 tommer) Ra µm (µtomme) | Wiper (-WMX) RE 0,8 mm (0,031 tommer) Ra µm (µtomme) |
0,07 (0,003) | 0,31 (12,4) | 0,30 (12,0) | - | - |
0,10 (0,004) | 0,63 (25,2) | 0,32 (12,8) | 0,31 (12,4) | - |
0,12 (0,005) | 0,90 (36,0) | 0,45 (18,0) | 0,45 (18,0) | - |
0,15 (0,006) | 1,41 (56,4) | 0,70 (28,0) | 0,70 (28,0) | 0,25 (10,0) |
0,18 (0,007) | 2,03 (80,8) | 1,00 (40,0) | 1,00 (40,4) | 0,30 (12,0) |
0,20 (0,008) | 2,50 (100,0) | 1,25 (50,0) | 1,25 (50,0) | 0,35 (14,0) |
0,22 (0,009) | 3,48 (139,2) | 1,74 (69,6) | 1,74 (69,6) | 0,40 (16,0) |
0,25 (0,010) | - | - | 2,25 (90,0) | 0,45 (18,0) |
0,28 (0,011) | - | - | 2,82 (112,8) | 0,50 (20,0) |
0,30 (0,012) | - | - | 3,23 (129,2) | 0,55 (22,0) |
0,35 (0,014) | - | - | 4,40 (176,0) | 0,60 (24,0) |
0,40 (0,016) | - | - | 5,75 (230,0) | 0,70 (28,0) |
0,45 (0,018) | - | - | 8,54 (341,6) | 1,1 (44,0) |
0,50 (0,020) | - | - | 10,55 (422,0) | 1,3 (51,0) |
Tilspænding mm (tommer) | Standard RE 1,2 mm (0,047 tommer) Ra µm (µtomme) | Wiper (-WMX) RE 1,2 mm (0,047 tommer) Ra µm (µtomme) | Standard RE 1,6 mm (0,063 tommer) Ra µm (µtomme) | Wiper (-WMX) RE 1,6 mm 1) (0,063 tommer) Ra µm (µtomme) |
0,15 (0,006) | 0,47 (18,8) | - | - | - |
0,18 (0,007) | 0,68 (27,2) | - | - | - |
0,20 (0,008) | 0,83 (33,3) | 0,3 (12,0) | 0,63 (25,2) | - |
0,22 (0,009) | 1,16 (46,4) | 0,3 (12,0) | 0,87 (34,8) | - |
0,25 (0,010) | 1,50 (60,0) | 0,4 (16,0) | 1,12 (44,8) | 0,3 (12,0) |
0,28 (0,011) | 1,88 (75,2) | 0,4 (16,0) | 1,41 (56,4) | 0,35 (14,0) |
0,30 (0,012) | 2,16 (86,4) | 0,4 (16,0) | 1,62 (64,8) | 0,4 (16,0) |
0,35 (0,014) | 2,93 (117,2) | 0,5 (20,0) | 2,20 (88,0) | 0,4 (16,0) |
0,40 (0,016) | 3,83 (153,2) | 0,65 (26,0) | 2,88 (115,2) | 0,4 (16,0) |
0,45 (0,018) | 5,70 (228,0) | 0,85 (34,0) | 4,27 (170,8) | 0,5 (20,0) |
0,50 (0,020) | 7,03 (281,2) | 1,15 (46,0) | 5,27 (210,8) | 0,7 (28,0) |
0,55 (0,022) | 8,51 (340,4) | 1,2 (48,0) | 6,38 (255,2) | 0,9 (36,0) |
0,60 (0,024) | 10,13 (405,2) | 1,3 (52,0) | 7,59 (303,6) | 1,05 (42,0) |
0,65 (0,026) | - | - | 8,91 (356,4) | 1,25 (50,0) |
0,70 (0,028) | - | - | 10,31 (413,6) | 1,3 (52,0) |
0,85 (0,033) | - | - | 15,24 (609,6) | 1,9 (76,0) |
0,90 (0,035) | - | - | 17,09 (683,0) | 2,1 (84,0) |
- Værdierne for 1,6 mm (0,06 tommer) radius tager udgangspunkt i et DNMX-skær
Applikationstips til udvendig drejning
Emner med tendens til vibration
Bearbejd i ét overløb ( for eksempel et rør)
Det anbefales at udføre bearbejdningen med ét overløb for at rette kraften ind i spændeenheden/spindlen.
Eksempel:
Udvendig diameter (OD) på 25 mm (0,984 tommer)
Indvendig diameter (ID) på 15 mm (0,590 tommer)
Spåndybde, ap = 4,3 mm (0,169 tommer)
Det resulterer i en godstykkelse = 0,7 mm (0,028 tommer)
OD = 25 mm (0,984 tommer) | ap 4,3 mm (0,169 tommer) |
![]() | ID = 15 mm (0,590 tommer) |
En indgrebsvinkel på 90° (hovedvinkel 0°) kan bruges til at rette skærekræfterne i aksial retning. Det medfører en minimal bøjningskraft på emnet.
Bearbejdning i to overløb
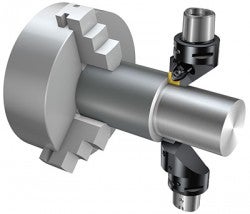
Synkroniseret bearbejdning med øverste og nederste revolver vil udligne de radiale skærekræfter og forhindre vibration og bøjning af emnet.
Slanke/tyndvæggede emner
Når du drejer slanke/tyndvæggede emner, skal du overveje følgende:
- Brug en indgrebsvinkel tæt på 90° (hovedvinkel 0°). Selv en lille ændring (fra en 91/-1 til en 95/-5 graders vinkel) vil påvirke skærekraftens retning under bearbejdningen
- Spåndybden,ap, bør være større næseradiussen, RE. Stor ap øger de aksiale kræfter, Fz, og reducerer de radiale skærekræfter, Fx, der medfører vibration
- Brug et skær med skarp skærkant og lille næseradius, RE, der vil generere lave skærekræfter
- Overvej at bruge Cermet eller PVD-kvalitet for at opnå slidstyrke og en skarp skærkant, hvilket er at foretrække i denne type operation
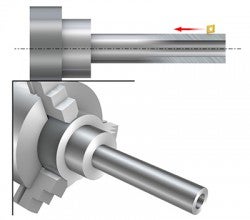
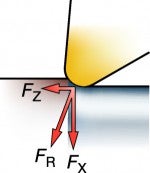
Hjørnedrejning/drejning mod ansats
Følg trin 1-5 for at undgå at beskadige skærkanten. Denne metode meget god til CVD-belagte skær og kan reducere antallet af brud betydeligt.
Trin 1-4:
Hold afstanden for hvert trin (1-4), så den er den samme som tilspændingsværdien for at undgå spånhamring.
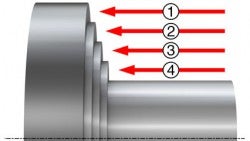
Trin 5:
Bearbejd den sidste spån i et vertikalt overløb, der starter fra den udvendige diameter mod den indvendige diameter.
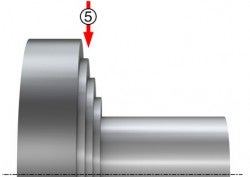
Der kan også opstå problemer med wrap around-spåner ved bearbejdning fra den indvendige diameter til den udvendige diameter, når du plandrejer. En ændring af værktøjsbanen kan vende spånretningen og løse problemet.
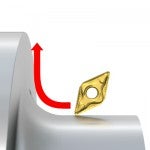
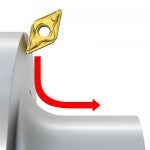
Plandrejning
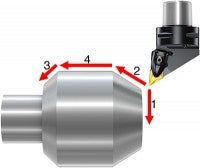
Start med plandrejningen (1) og fasen (2). Hvis det er muligt, og hvis de geometriske forhold på emnet tillader det, skal du bearbejde fasen (3). Længdedrejningen (4) er den sidste operation, og skæret vil få en blød indkøring og udkøring under bearbejdningen.
Plandrejning skal være den første operation for at indstille referencepunktet på emnet til næste overløb.
Gratdannelse er ofte et problem mod slutningen af bearbejdningen (når du går ud af emnet). Hvis du går ud af en fas eller en radius (tilkørsel med radius over et hjørne) vil det kunne minimere eller forhindre gratdannelse.
En fas på emnet giver skærkanten en blødere indgang (både ved plandrejning og længdedrejning).
Afbrudt spån

Bearbejdning med afbrudt spån:
- Brug en PVD-kvalitet til at give skærkantsejhed i applikationer med hurtige afbrydelser, f.eks. sekskantede stænger
- Brug en sej CVD-kvalitet til at give substratsejhed i applikationer med store emner og kraftige afbrydelser
- Overvej at bruge en stærk spånbryder for at tilføje tilstrækkelig modstandsdygtighed over for udflisning
- Det kan være en fordel at slukke for kølevæsken for at undgå termiske sprækker
Sletdrejning af emner med frigang (slibefrigang)

Brug den størst mulige næseradius, RE til længde- og plandrejning, det giver:
- En stærk skærkant og større pålidelighed
- God overfladekvalitet
- Mulighed for at bruge høj tilspændingshastighed
Overstig ikke frigangens bredde og foretag drejning af frigangen til sidst for at fjerne grater.
Applikationstips til indvendig drejning
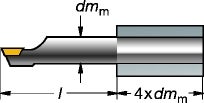
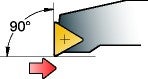

- Vælg den størst mulige stangdiameter, men sørg samtidig for, at der er tilstrækkelig plads til spånafgang mellem borestangen og hullet
- Sørg for, at der er tilstrækkelig spånafgang i forhold til de anvendte skæredata og den korrekte type spåner, der produceres
- Vælg det mindst mulige udhæng, men sørg samtidig for, at udborestangens længde gør det muligt at opnå de anbefalede fastspændingslængder. Fastspændingslængden bør aldrig være mindre end 3 gange stangens diameter
- Brug vibrationsdæmpede udborestænger, hvis der fremstilles vibrationsfølsomme dele
- Vælg en indgrebsvinkel så tæt på 90° (0° hovedvinkel) som muligt, således at skærekræfterne dirigeres langs udborestangen. Indgrebsvinklen bør aldrig være mindre end 75° (-15° hovedvinkel)
- Som førsteprioritet bør vendeskæret være et positivt skær og have en positiv skærgeometri for at minimere værktøjets nedbøjning
- Vælg en næseradius på skæret, som er mindre end spåndybden
- Et utilstrækkeligt skærkantindgreb kan øge vibrationerne som følge af friktion under bearbejdningen. Vælg et skærkantindgreb, der er større end næseradiusen for at få et godt skæreforløb
- Hvis skærkanten går for kraftigt i indgreb (stor spåndybde og/eller tilspænding) kan øge vibrationer på grund af værktøjets nedbøjning
- Skær med tynd belægning eller uden belægning giver normalt lavere skærekræfter end skær med tyk belægning. Dette er især vigtigt, når der er stor forskel på værktøjslængde og værktøjsdiameter. En skarp skærkant forbedrer normalt hulkvaliteten ved at minimere tendens til vibrationer
- En geometri med en åben spånbryder kan ofte være en større fordel ved indvendig drejning
- En skærkvalitet med en højere grad af sejhed kan være værd at overveje ved visse operationer, hvis der er risiko for spånhamring og/eller tendenser til vibration
- Overvej alternative værktøjsbaner, hvis spåndannelsen skal forbedres
Applikationstips til drejning i hårde materialer
Ud over de generelle anbefalinger for drejning er der nogle afgørende faktorer, der skal overvejes for drejning i hårde materialer (hvis produktionsprocessen omfatter egen forberedelse af emnet før hærdning):
- Undgå grater
- Bevar snævre måltolerancer
- Lav affasninger og fremstil radier i den bløde tilstand
- Lad ikke skæret gå pludseligt ind i eller ud af indgreb
- Ind- eller udkørsel ved at foretage til- og udkørsel med radius
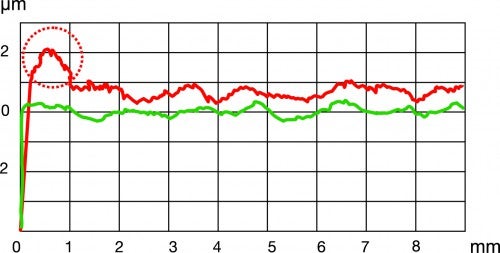
Overflademålinger
X-akse: Dellængde
Y-akse: Diameterafvigelse
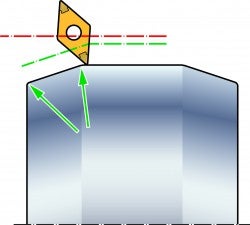
Kritisk overflade
Opspænding
- God maskinstabilitet, fastspænding og justering af emne er afgørende
- Som en tommelfingerregel er det normalt acceptabelt, hvis et emnes længde/diameter-forhold er op til 2:1 for emner, der kun understøttes i den ene ende. Hvis der er ekstra pinoldokunderstøttelse, kan dette forhold øges
- Bemærk, at et termisk symmetrisk design af spindeldok og pinoldok vil tilføre ekstra dimensionsstabilitet
- Brug Coromant Capto®-systemet
- Minimer alle udhæng for at maksimere systemets stivhed
- Overvej at bruge udborestænger med hårdmetalskaft og Silent Tools til indvendig drejning
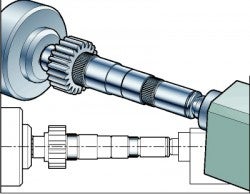
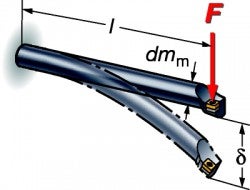
Skærs mikrogeometri
To typiske kvaliteter af CBN-skær er S-skær og T-skær.
- S-skær: Har den bedste skærkantstyrke. Modstandsdygtig over for mikroudflisning og sikrer en ensartet overfladekvalitet.
- T-skær: Til den bedste overfladekvalitet ved kontinuerlig spåntagning og minimal gratdannelse ved afbrudt spån. Lavere skærekræfter.
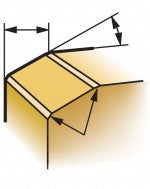
S-skær
Fas med ER behandling
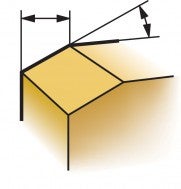
T-skær
Fas uden ER behandling honing
Skærs hjørnegeometri
- Under stabile betingelser skal der altid anvendes wipergeometri for at opnå den bedste overfladekvalitet.
- Brug skær med lille indgrebsvinkel, når der stilles høje krav til produktiviteten.
- Brug kun et skær med normal radius, hvis stabiliteten er dårlig (slankt emne osv.).
Våd eller tør bearbejdning
Drejning i hårde/hærdede materialer uden kølemiddel er den ideelle metode og kan anbefales. Både CBN-skær og keramiske skær tåler høje skæretemperaturer, som eliminerer omkostningerne og besværet ved at skulle bruge kølevæsker.
Nogle applikationer kræver dog kølevæske, f.eks. for at kontrollere emnets termiske stabilitet. Sørg i disse tilfælde for at der er et kontinuerligt kølevæskeflow under hele drejeoperationen.
Generelt fordeles varmen, der opstår ved bearbejdning, i spånerne (80 %), emnet (10 %) og skæret (10 %). Det viser betydningen af at fjerne spånerne fra skærkantzonen.
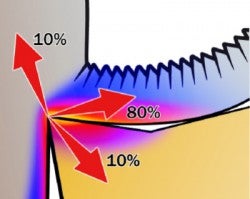
Skæredata og slid
Stor varme i skærekantzonen reducer skærekræfterne. Derfor genererer en skærehastighed der er for lav mindre varme og kan forårsage brud på skæret.
Grubeslid påvirker gradvist skærstyrken, men påvirker ikke overfladekvaliteten nær så meget. I modsætning hertil påvirker flankeslid gradvist emnetolerancen.
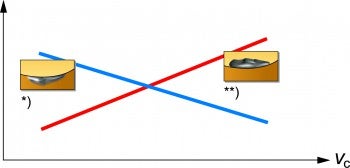
Andel af værktøjslevetiden ved bestemmelse af slid
*) Fasslid **) Grubeslid
Kriterier for skift af skær
En foruddefineret overfladekvalitet (B) er et hyppigt og praktisk kriterium for skærskift. Overfladekvaliteten måles automatisk i en separat station og en værdi tildeles en specificeret overfladekvalitet.
Indstil et foruddefineret antal emner (A) som kriterium for skærskift for at opnå en optimeret og mere stabil proces. Denne værdi skal være 10–20 % mindre end den foruddefinerede overfladekvalitet, og det præcise tal fastlægges fra tilfælde til tilfælde.
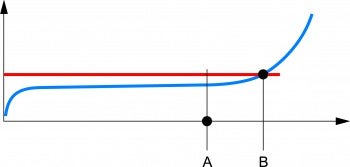
A: Forudbestemt antal emner
B: Foruddefineret overfladekvalitet
X-akse: Antal emner
Y-akse: Overfladekvalitet
Blå linje: Skærslid
Rød linje: Maks. Ra/Rz værdi
Strategi med et overløb
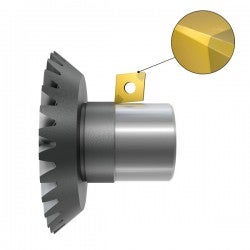
En "spånvolumen"-strategi med ét overløb kan gennemføres for både udvendige og indvendige operationer. En stabil opspænding er vigtig, og værktøjsudhænget skal ikke være mere end en gang stangdiameteren ved indvendig drejning (1×D). For at opnå en god bearbejdning anbefaler vi rejfede skær med ER behandling (S-type) og moderat hastighed og tilspænding.
Fordele
- Kortest mulige bearbejdningstid
- Én værktøjsposition
Ulemper
- Problemer med at overholde strenge måltolerancer
- Kortere værktøjslevetid (end to overløb)
- Toleranceafvigelser pga. relativt hurtigt slid
Strategi med to overløb
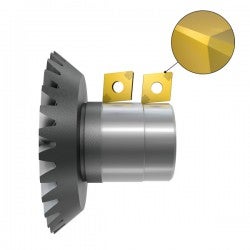
En strategi med to overløb giver mulighed for ikke-overvåget bearbejdning af overflader med høj kvalitet. Vi anbefaler skrubbearbejdningsskær med en radius på 1,2 mm (0,047 tommer) og sletbearbejdningsskær kun med fas uden ER behandling (T-type). Begge skær skal have wipergeometri.
Fordele
- Værktøj optimeret til skrub- og sletbearbejdning
- Større sikkerhed, snævrere tolerancer og potentielt længere driftsperioder mellem værktøjsskift
Ulemper
- Der kræves to skær
- To værktøjspositioner
- Ét ekstra værktøjsskift
Sådan anvender du kølevæske ved drejning
Skærevæskens primære funktioner er spånafgang, køling og smøring mellem værktøjet... chevron_right
Opboring – sådan gør du
Der er flere faktorer, der skal overvejes for at få en optimeret opboreproces. Korrekt... chevron_right
Sådan vælger du korrekt drejeskær
Der er mange parametre at tage højde for ved valg af drejeskær. Vælg omhyggeligt... chevron_right
Drejning
Produkt oversigt Valget af udborestang har stor indflydelse på produktionsøkonomien.... chevron_right