Was ist Profilfräsen?
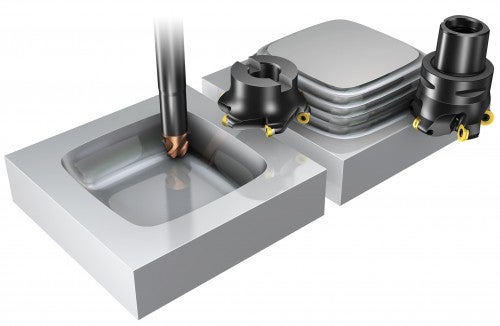
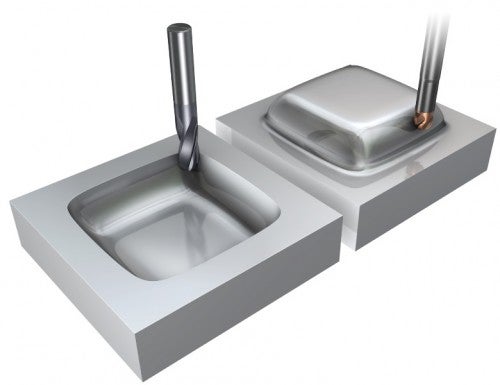
Profilfräsen ist eine gängige Fräsbearbeitung. Fräskonzepte mit runden und Radius-Wendeschneidplatten sind Fräser, die zum Schruppen und Vorschruppen eingesetzt werden, während Konzepte mit Kugelschaftfräsern zum Schlichten und Feinstschlichten verwendet werden.
Profilfräsen
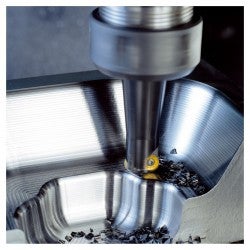
Profilfräsen deckt mehrachsige Fräsbearbeitungen konvexer und konkaver Formen in zwei und drei Richtungen ab. Je größer ein Werkstück und je komplizierter die zu bearbeitenden Konturen, desto wichtiger wird der Planungsprozess.
Der Bearbeitungsprozess sollte in mindestens drei Bearbeitungstypen unterteilt werden:
- Schruppen/Vorschruppen
- Vorschlichten
- Schlichten
Feinstschlichten, häufig durch Hochgeschwindigkeitsbearbeitung, ist in manchen Fällen erforderlich. Das Fräsen von verbleibendem Werkstückstoff, die sogenannte Restmaterialbearbeitung, fällt unter Vorschlichten und Schlichten. Um die bestmögliche Genauigkeit und Produktivität zu erzielen, empfiehlt es sich, die Schrupp- und Schlichtbearbeitung in getrennten Maschinen durchzuführen und Zerspanungswerkzeuge optimiert für jede Anwendung zu verwenden.
Die Schlichtbearbeitung sollte auf einer 4/5-achsigen Werkzeugmaschine mit moderner Software und modernen Programmiertechniken durchgeführt werden. Dadurch kann eine zeitaufwändige manuelle Endbearbeitung deutlich verkürzt werden oder in manchen Fällen sogar gänzlich entfallen. Das Endergebnis ist ein Produkt mit besserer Form- und Maßgenauigkeit und höherer Oberflächengüte.
Wahl der Werkzeuge
Optimierte Zerspanungswerkzeuge zum Schruppen und Vorschruppen:
Konzepte mit runden und Radius-Wendeschneidplatten.
Optimierte Zerspanungswerkzeuge zum Schlichten und Vorschlichten:
Kugelschaftfräser und Konzepte mit Radius.
![]() | ![]() | ![]() | ![]() | |
Rundplattenfräser | Kugelschaftfräser mit Wendeschneidplatten | Austauschbarer Kugelschaftfräskopf | Vollhartmetall-Kugelschaftfräser | |
Maschine/Spindelgröße | ISO 40, 50 | ISO 40, 50 | ISO 30, 40 | ISO 30, 40 |
Stabilitätsanforderungen | Hoch | Mittel | Mittel | Gering |
Schruppen | Sehr gut | Gut | Akzeptabel | Akzeptabel |
Schlichten | Akzeptabel | Akzeptabel | Sehr gut | Sehr gut |
Schnitttiefe ap | Mittel | Mittel | Gering | Gering |
Vielseitigkeit | Sehr gut | Sehr gut | Sehr gut | Sehr gut |
Produktivität | Sehr gut | Gut | Gut | Gut |
Checkliste für das Profilfräsen
Zur Auswahl der korrekten Werkzeuge und Bestimmung der bestgeeigneten Methode ist das Profil des Werkstücks sorgfältig zu analysieren:
- Mindestradius und maximale Kavitätentiefe bestimmen
- Zu zerspanende Werkstückmenge abschätzen
- Zur Vermeidung von Vibrationen Werkzeug- und Werkstückspannung beachten. Sämtliche Anwendungen sind auf einsatzbezogenen Maschinen durchzuführen, um eine hohe Form- und Maßgenauigkeit zu erzielen
- Durch den separaten Einsatz von präzisen, zum Schlichten bzw. Feinstschlichten ausgelegten Werkzeugmaschinen, kann ein zeitaufwändiges manuelles Polieren verkürzt werden oder in manchen Fällen sogar gänzlich entfallen
- Eine moderne Programmierung kann erforderlich sein, um große Einsparungen zu erzielen. Für eine optimale Oberflächengüte und endkonturnahe Bearbeitung empfiehlt sich der Einsatz von Vollhartmetallschaftfräsern mit Hochgeschwindigkeitskapazität
- Das Schruppen und Vorschlichten großer Bauteile erfolgt auf produktivste Weise in der Regel mit konventionellen Methoden und Werkzeugen. Eine Ausnahme bildet Aluminium, bei dem auch beim Schruppen hohe Schnittgeschwindigkeiten verwendet werden.
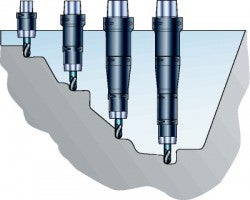
Methoden zur Reduzierung von Vibrationen
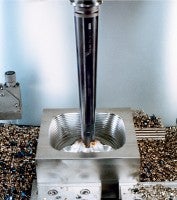
Bei der Fräsbearbeitung tiefer Profile mit langen Überhängen stellen Vibrationen ein Hindernis dar. Typische Methoden zur Bewältigung dieses Problems sind die Reduzierung von Schnitttiefe, Schnittgeschwindigkeit oder Vorschub.
- Modulare Werkzeuge mit hoher Stabilität und Rundlaufgenauigkeit verwenden
- Modulare Werkzeuge verbessern die Flexibilität und erhöhen die Anzahl möglicher Kombinationen
- Schwingungsgedämpfte Werkzeuge bzw. Verlängerungen verwenden, wenn die Gesamtwerkzeuglänge von der Spindelplanfläche bis zur Schneidkante 4- bis 5-mal größer als der Durchmesser an der Spindelplanfläche ist
- Verlängerung aus Schwermetall verwenden, wenn die Biegesteifigket drastisch erhöht werden muss
- Für Spindeldrehzahlen über 20.000 U/min gewuchtete Zerspanungswerkzeuge und Werkzeugadapter wählen
- Verlängerungen und Aufnahmen mit größtmöglichem Durchmesser in Relation zum Fräserdurchmesser wählen
- Eine radiale Differenz von 1 mm zwischen Halter und Zerspanungswerkzeug reicht aus. Fräser mit Übermaß verwenden
- Tauchfräsen ist eine alternative Methode beim Fräsen mit extrem langen Werkzeugen
Suchen Sie Werkzeugempfehlungen?
Hier finden Sie unsere Zerspanungswerkzeuge chevron_right
Brauchen Sie Beratung?
Stellen Sie uns eine Frage chevron_right
Was es sonst noch über die Grundlagen unserer Metallzerspanung zu lernen gibt?
Registrieren Sie sich für unser kostenloses E-Learning Programm chevron_right
Schrittweise Vergrößerung der Werkzeuglänge
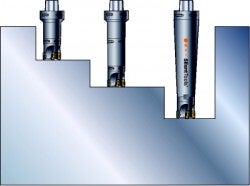

Um eine maximal Produktivität bei Schruppbearbeitungen zu bewahren, bei denen der letzte Arbeitsgang tief im Werkstück erfolgt, ist es wichtig, mit unterschiedlichen Fräserverlängerungen zu arbeiten.
- Mit der kürzesten Verlängerung beginnen, da längere die Produktivität beschränken und Vibrationen verursachen
- Zu einem vorab festgelegten Zeitpunkt im Programm auf ein längeres Werkzeug wechseln. Die Taschengeometrie bestimmt den Zeitpunkt für den Wechsel.
- Schnittdaten an die jeweilige Werkzeuglänge anpassen, um maximale Produktivität zu erhalten
Ist-Schnittgeschwindigkeit
Wenn ein Nenndurchmesser des Werkzeugs bei der Berechnung der Schnittgeschwindigkeit eines Kugelschaftfräsers oder eines Fräsers mit runden Wendeschneidplatten zugrunde gelegt wird, ist die tatsächliche Schnittgeschwindigkeit vc, viel niedriger, wenn die Schnitttiefe, ap, gering ist. Dadurch wird der Tischvorschub und die Produktivität erheblich beeinträchtigt.
Grundberechnungen der Schnittgeschwindigkeit, basierend auf dem Ist-Durchmesser bzw. effektiven Durchmesser, Dcap.
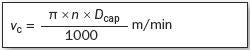
Eck-/Schaftfräser
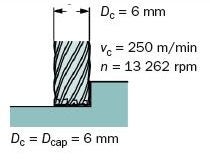
Kugelschaftfräser
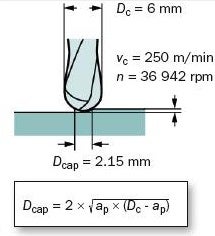
Fräser mit runden Wendeschneidplatten
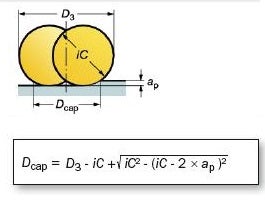
Pointmilling – geneigter Fräser
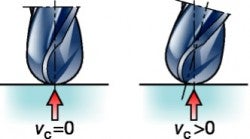
Beim Einsatz eines Kugelschaftfräsers ist die kritischste Stelle das Werkzeugzentrum, wo die Schnittgeschwindigkeit gegen Null geht, was sich unvorteilhaft auf den Zerspanungsprozess auswirkt. Die Spanabfuhr im Werkzeugzentrum ist aufgrund des geringen Platzes an der Werkzeugspitze problematisch.
Daher empfiehlt es sich, die Spindel oder das Werkstück um 10 bis 15 Grad zu neigen, wodurch die Schneidzone aus diesem Bereich heraus verlagert wird.
- Größere minimale Schnittgeschwindigkeit
- Verlängerte Standzeit und verbesserte Spanbildung
- Bessere Oberflächengüte
Zentrum-schneidende Fräser (bohrend einsetzbar)
Zentrumsbereich, z = 2
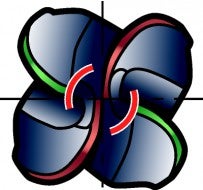
Außenbereich, z = 4
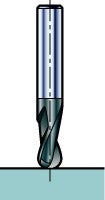
Z = 2
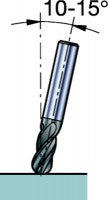
Z = 4
Flacher Schnitt
Wird ein Fräser mit runden Wendeschneidplatten oder ein Kugelschaftfräser bei geringer Schnitttiefe verwendet, kann die Schnittgeschwindigkeit, vc, aufgrund der kurzen Eingriffszeit der Schneidkante erhöht werden. Der Zeitraum der Wärmeentwicklung im Schnittbereich verkürzt sich, wodurch die Temperatur an Schneidkante und Werkstück gering bleibt. Außerdem kann der Vorschub/Zahn, fz, aufgrund der abnehmenden Spandicke erhöht werden.
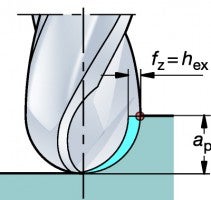
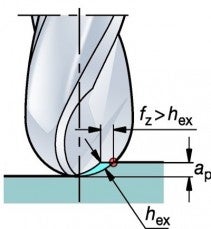
Flacher Schnitt
Beispiel: flacher Schnitt, nicht geneigter Fräser im Vergleich zu geneigtem Fräser
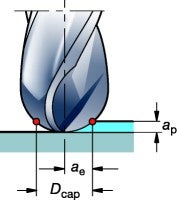
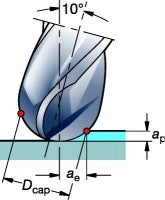
Dieses Beispiel zeigt die Möglichkeiten der Steigerung der Schnittgeschwindigkeit, wenn ae/ap gering ist, und die Vorteile des Einsatzes eines geneigten Fräsers.
Vollhartmetall-Kugelschaftfräser
Dc = 10 mm, Sorte GC 1610.
Werkstoff: Stahl, 400HB
Schnittdatenempfehlungen für einen tiefen Schnitt ap - Dc/2:
vc = 170 m/min
fz = 0.08 mm/U = hex
Bearbeitung | Nicht geneigter Fräser | Geneigter Fräser (10°) |
Vorschlichten ap - 2 mm (0.079 Zoll)
vc - 300 m/min (984 Fuß/min)
Der Vorschub pro Zahn, fz, ist derselbe für geneigte und nicht geneigte | Dc = 10 mm (0.394 Zoll)
vc = 300 m/min (984 Fuß/min)
hex = 0.08 mm (0.003 Zoll)
vf = 2 860 mm/min (113 Zoll/min) | Dc = 10 mm (0.394 Zoll)
vc = 300 m/min (984 Fuß/min)
hex = 0.08 mm (0.003 Zoll)
vf =5 100 mm/min (201 Zoll/min) |
Feinstschlichten ae - 0.1 mm
vc - 5 * 170 - 850 m/min (557–2789 Fuß/min)
Hinweis: Beim Feinstschlichten sollte ein zweischneidiger Fräser zn = 2, eingesetzt werden,
fz - 0.12 mm/z (0.005 Zoll/z) | Ein nicht geneigter Fräser ist zum Feinstschlichten ungeeignet | Dc = 10 mm (0.394 Zoll)
vc = 850 m/min (2789 Fuß/min)
hex = 0.02 mm (0.0008 Zoll)
vf =14 600 mm/min (575 Zoll/min) |
Produktivität beim Profilfräsen: Konstantes Aufmaß
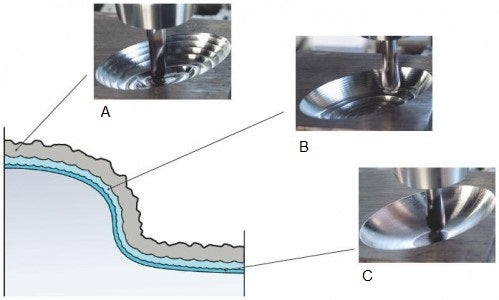
A: Schruppen
B: Vorschlichten
C: Schlichten und Feinstschlichten
Ein konstantes Aufmaß ist eines der wirklichen Hauptkriterien für eine konstant hohe Produktivität, insbesondere bei Einsatz hoher Schnittgeschwindigkeiten.
- Um maximale Produktivität bei diesen insbesondere im Formen- und Gesenkbau auftretenden Bearbeitungen zu erreichen, ist es wichtig, die Größe der Fräser den spezifischen Anwendungen anzupassen
- Das primäre Ziel ist es, eine gleichmäßige Fertigungstoleranz bzw. ein gleichmäßiges Aufmaß zu erzielen, damit das jeweils eingesetzte Werkzeug möglichst wenigen Belastungs- oder Richtungsänderungen ausgesetzt wird
Vor allem beim leichten Schruppen und Vorschlichten kann es häufig von Vorteil sein, unterschiedliche Fräser mit abnehmenden Durchmessern anstatt eines einzigen Durchmessers für die gesamte Anwendung einzusetzen.
- Die beste Qualität beim Schlichten wird erreicht, wenn das durch vorangegangene Bearbeitungen erzeugte Aufmaß so gering und gleichmäßig wie möglich ist
- Ziel ist stets eine möglichst endkonturnahe Bearbeitung
- Sicherer Zerspanungsvorgang
Vorteile von konstantem Aufmaß
- Einige Vorschlichtbearbeitungen und praktisch alle Schlichtbearbeitungen können teilweise bzw. in manchen Fällen sogar komplett automatisiert erfolgen
- Geringere negative Auswirkungen auf Werkzeugmaschinenführung, Kugelrollspindel und Spindellager
Öffnen eines Werkstücks aus Vollmaterial
- Beim Öffnen einer Tasche ist es wichtig, eine Bearbeitungsmethode zu wählen, welche die Schnitttiefe, ap, minimiert und ein konstantes Aufmaß für die anschließende Profilfräsbearbeitung hinterlässt.
- Bei Plan- und Eckfräsern/Schaftfräsern oder Walzenstirnfräsern verbleibt ein stufenförmiges Materialaufmaß, welches entfernt werden muss. Dieses führt zu variierenden Schnittkräften und Werkzeugablenkung. Folge ist, dass ein ungleichmäßiges Aufmaß für die Schlichtbearbeitung zurück bleibt, welche die Maßgenauigkeit der Endform beeinflusst.
- Durch den Einsatz von Rundplattenfräsern werden sanftere Übergänge zwischen den Durchgängen erzielt.Dadurch bleibt ein geringeres, gleichmäßigeres Aufmaß für die Schlichtbearbeitung zurück, wodurch eine höhere Bauteilqualität erzielt wird.
- Eine dritte Alternative zum Öffnen einer Tasche ist der Einsatz eines Hochvorschubfräsers. Auch hier verbleibt aufgrund der niedrigen Schnitttiefe ein geringerer und gleichmäßigerer bzw. gering stufenförmiger Materialabtrag.
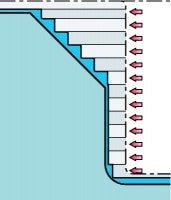
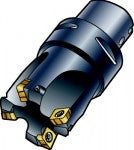
Eckfräser
Ergibt ein größeres ungleichmäßiges Aufmaß
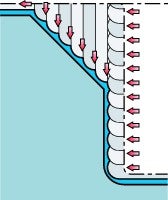
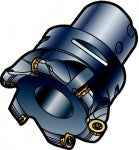
Rundplattenfräser
Ergibt ein geringeres Aufmaß
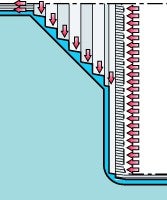
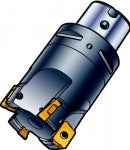
Hochvorschubfräser
Ergibt ein geringeres Aufmaß
Suchen Sie Werkzeugempfehlungen?
Hier finden Sie unsere Zerspanungswerkzeuge chevron_right
Brauchen Sie Beratung?
Stellen Sie uns eine Frage chevron_right
Was es sonst noch über die Grundlagen unserer Metallzerspanung zu lernen gibt?
Registrieren Sie sich für unser kostenloses E-Learning Programm chevron_right
Kopierfräsen
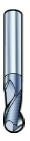
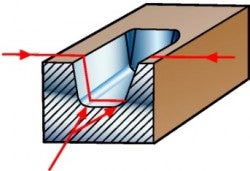
Die herkömmliche und einfachste Methode der Programmierung eines Werkzeugwegs zur Bearbeitung einer Tasche ist, eine normale Kopierfräsmethode mit vielen Ein- und Austritten in das Werkstück anzuwenden. Das bedeutet jedoch, dass leistungsstarke Softwareprogramme, Maschinen und Zerspanungswerkzeuge nur stark eingeschränkt genutzt werden. Es ist empfehlenswert, eine Maschinensoftware mit Look-Ahead-Funktion zu verwenden, um Abweichungen vom Werkzeugweg zu vermeiden.
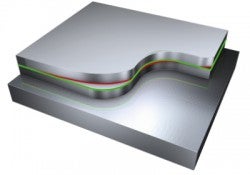
Eine unvoreingenommene Vorgehensweise bei der Wahl der Methoden, Werkzeugwege, Fräswerkzeuge und Werkzeughalter ist ganz entscheidend.
− Hohe Belastung der Schneidenspitze
− Reduzierte Vorschubraten
− Reduzierte Standzeit
− Mechanischer Einfluss
− Formenungenauigkeiten
− Längere Programmierungs- und Bearbeitungszeit
Ein Werkzeugweg zum Kopierfräsen ist häufig eine Kombination aus Gleichlauf- und Gegenlauffräsen und erfordert eine Vielzahl von Ein- und Austritten in das Werkstück. Bei jedem Ein- und Austritt wird das Werkzeug abgelenkt und hinterlässt Spuren auf der Oberfläche. Die Schnittkräfte und die Verformung des Werkzeugs nehmen zu, und im Austrittsbereich wird das Werkstück leicht unterschnitten.
Schlussfolgerungen
- Kopierfräsen entlang steiler Wände sollte so gut wie möglich vermieden werden. Beim Tauchfräsen ist die Spandicke groß, die Schnittgeschwindigkeit sollte gering sein.
- Besonders wenn der Fräser auf dem Grund auftritt, besteht die Gefahr von Schneidenausbrüchen in der Mitte des Werkzeugs.
- Steuerung der Vorschubgeschwindigkeit mit Look-Ahead-Funktion einsetzen. Andernfalls erfolgt die Vorschubreduzierung zu spät, um Schäden im Bereich der Werkzeugmitte zu verhindern.
- Die Kontaktlänge beim Auftreffen des Fräsers auf die Wand ist groß. Dadurch besteht die Gefahr von Vibrationen, Werkzeugablenkung oder sogar Werkzeugbruch.
- Bei Kugelschaftfräsern befindet sich der kritischste Bereich im Werkzeugzentrum, da dort die Schnittgeschwindigkeit Null beträgt. Daher empfiehlt es sich, die Schneidzone aus diesem Bereich durch Neigung der Spindel oder des Werkstücks herauszubewegen und Pointmilling anzuwenden.
- Es wirkt sich oftmals etwas günstiger auf den Zerspanungsprozess aus, wenn beim Aufwärtskopieren entlang steiler Wände Gegenlauffräsen angewandt wird, da die Spandicke ihr Maximum bei einer günstigeren Schnittgeschwindigkeit erreicht
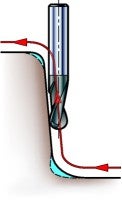
Gefahr von Riefen
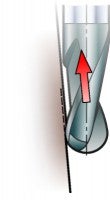
Kopierfräsen, aufwärts:
Maximale Spandicke bei empfohlener vc.
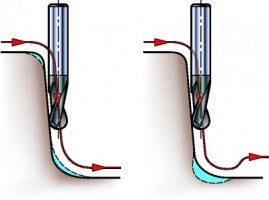
Am Taschengrund:
Gefahr von Abplatzungen in der Werkzeugmitte.
Formenfehler treten häufig auf, insbesondere bei der Hochgeschwindigkeitsbearbeitung.
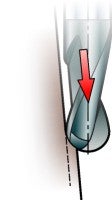
Kopierfräsen, abwärts:
Große Spandicke bei sehr geringer vc.
Vorschubreduzierung zur Vermeidung verkürzter Standzeit
Bei Wechsel von Gegen- und Gleichlauffräsen ist das Werkzeug einer wechselnden Ablenkung und variierenden Schnittkräften ausgesetzt. Durch die Reduzierung der Vorschubgeschwindigkeit in den kritischen Bereichen des Werkzeugwegs kann die Gefahr von Abplatzungen an der Schneide vermindert und die Bearbeitungssicherheit und Standzeit gesteigert werden.
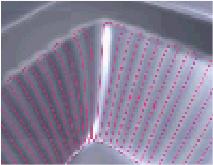
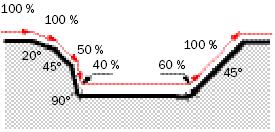
Konturfräsen
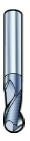
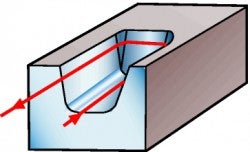
Anstatt Programmiertechniken anzuwenden, die auf das „Abtragen“ von Werkstoffstoff bei konstantem Z-Wert beschränkt sind, sollte die wesentlich vorteilhaftere Konturfräsbearbeitung im Gleichlaufmodus gewählt werden. Die Vorteile:
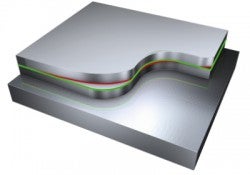
+ Eine deutlich verkürzte Bearbeitungszeit
+ Bessere Maschinen- und Werkzeugauslastung
+ Höhere Maßgenauigkeit der bearbeiteten Kontur
+ Weniger zeitintensives Schlichten und manuelles Polieren
+ Schnittgeschwindigkeitskontrolle - ve
+ Erlaubt HSM
+ Hohe Vorschübe
+ Lange Standzeit
+ Sicherheit
Die anfängliche Programmierung ist schwieriger und etwas zeitaufwändiger. Dies wird jedoch im Regelfall sehr schnell kompensiert, da die Maschinenkosten pro Stunde normalerweise die einer Workstation um das Dreifache übertreffen.. Es ist empfehlenswert, eine Maschinensoftware mit Look-Ahead-Funktion zu verwenden, um Abweichungen vom Werkzeugweg zu vermeiden.Schlussfolgerungen
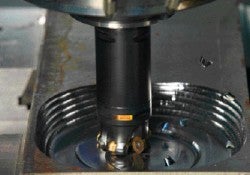
- Beim Konturfräsen sollte die „Waterline Milling Strategie" als beste Methode zum Gleichlauffräsen eingesetzt werden.
- Konturfräsen mit dem Außenbereich des Fräsers führt in vielen Fällen zu einer höheren Produktivität, da bei größeren Werkzeugdurchmessern mehr Schneiden effektiv eingreifen
- Ist die Spindeldrehzahl der Maschine begrenzt, kann durch Konturfräsen die Schnittgeschwindigkeit gehalten und gesteuert werden
- Schnelle Belastungs- und Richtungsänderungen sind beim Konturfräsen außerdem weniger häufig. Beim Fräsen mit hohen Schnittgeschwindigkeiten und Vorschüben ebenso wie bei gehärteten Werkstückstoffen ist dies besonders wichtig, da die Schneidkante und der Prozess empfindlicher auf jegliche Veränderungen reagiert, die zu Ablenkung (variierender Werkzeugablenkung) oder Vibrationen führen können
- Für eine gute Standzeit ist der Fräser so lange wie möglich konstant im Eingriff zu halten
Hinweis! Wenn die Werkzeugmitte schneidet, ist die Schnittgeschwindigkeit Null.
Strategie des Werkzeugwegs
Z – konstantes Konturfräsen, zwei Achsen. Schruppen bis Schlichten
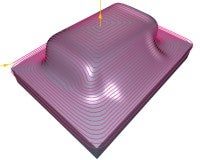
Waterline Fräsen Z - konstantes Konturfräsen
- Üblich, wenn eine CAM-unterstützte max. Scallop-Funktion verfügbar ist
- Sanfter Eintritt und Rückzug
- Einfache Programmierung
- Breite Werkzeugauswahl
Helixförmiges Konturfräsen, 3-5 Achsen. Schlichten
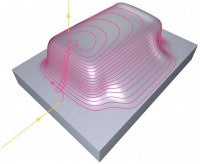
Konturfräsen auf schrägeintauchendem Werkzeugweg
- Reibungslose Richtungswechsel
- Hohe Maßgenauigkeit und Oberflächengüte
- Kontrollierte Wellenprofilhöhe
- Konstanter Eingriff
- Kurze Programme
- Kurzes Werkzeug
Herstellung von Freiformflächen
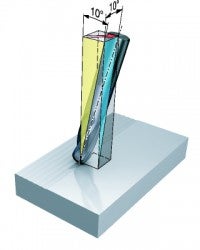
Gleichlauffräsen mit einem circa 10° geneigten Fräser in zwei Richtungen gewährleistet hohe Oberflächengüte und zuverlässige Leistung. Ein Kugelschaftfräser oder ein Fräser mit runden Wendeschneidplatten erzeugt eine Oberfläche mit einer bestimmten Rautiefe, h, in Abhängigkeit von:
- Schnittbreite, ae
- Vorschub pro Zahn, fz
Weitere wichtige Faktoren sind die Schnitttiefe, ap, welche die Schnittkräfte und den Rundlauffehler (TIR) beeinflusst. Für optimale Ergebnisse:
- Hochpräzisions-Hydraulikspannfutter mit Coromant Capto® verwenden
- Werkzeugüberhang minimieren
Schruppen und Vorschruppen
Ist der Vorschub pro Zahn wesentlich kleiner als die Schnitttiefe und -breite, wird die erzeugte Oberfläche eine deutlich geringere Rautiefe in Vorschubrichtung aufweisen.
Schlichten und Feinstschlichten
Es ist von Vorteil, eine gleichmäßige, glatte Oberfläche zu erzielen, die anschließend, unabhängig der Methode, auf einfache Weise poliert werden kann.
Dies wird erreicht, wenn fz ≈ ae.
Stets einen geneigten zweischneidigen Fräser zum Feinstschlichten verwenden, um eine optimale Oberflächengüte zu erzielen.
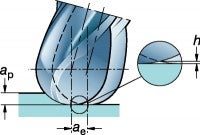
Vorschruppen mit einem fz-Wert, der viel kleiner ist als der ae
-Wert
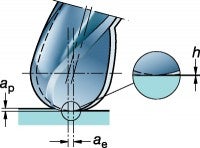
Feinstschlichten mit einem geneigten Fräser und einem fz-Wert, der gleich dem ae
-Wert ist
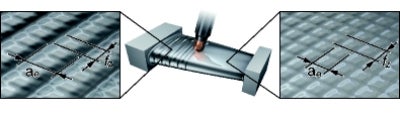
Suchen Sie Werkzeugempfehlungen?
Hier finden Sie unsere Zerspanungswerkzeuge chevron_right
Brauchen Sie Beratung?
Stellen Sie uns eine Frage chevron_right
Was es sonst noch über die Grundlagen unserer Metallzerspanung zu lernen gibt?
Registrieren Sie sich für unser kostenloses E-Learning Programm chevron_right
CoroMill® Plura Kugelschaftfräser für das ISO S-Profilfräsen
Einsatzbereich Profilfräsen (Vorschlichten bis Fertigbearbeitung) von Bauteilen... chevron_right
CoroMill® Plura Kugelschaftfräser für das ISO S-Profilfräsen
Einsatzbereich Profilfräsen (Vorschlichten bis Fertigbearbeitung) von Bauteilen... chevron_right
CoroMill® Plura Kugelschaftfräser für das Profilfräsen in ISO S Werkstoffen
Entdecken Sie die konischen CoroMill® Plura Kugelschaftfräser, die für das Profilfräsen... chevron_right
CoroMill® Plura Lollipop für das ISO S Profilfräsen
lollipop Anwendung Optimiert für das Profilfräsen von schwer zugänglichen Werkstückgeometrien,... chevron_right