Steam turbine shaft
Turbine shafts are mainly machined through turning and groove-cutting operations with some amounts of drilling. Large amounts of metal are removed and demanding grooves have to be cut.

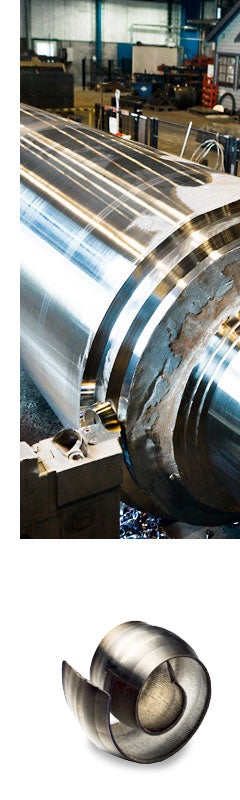
There is a range of typical turning operations used for turbine shafts that have undergone real continuous improvements. Heavy roughing of large forgings, long, with uneven surfaces but stable conditions are followed by extensive finishing of bearing surfaces. The turning operations performed on power components lend themselves well to improvements through the advances in tool technology.
A check-list of factors that directly affect the level of performance, security and results should include the following. They represent the established set of application parameters that make a lot of difference to the success in turning:
- incorporating the latest insert-grade generation, using allround and dedicated grades to optimize individual operations,
- best insert geometry for rough turning operations giving even higher levels of metal removal rates,
- best Wiper insert technology for even better finish-turning performance and results.
- having a choice of good insert-clamping in toolholder to maximizise stability and security,
- incorporating the best modular toolholding available for turning operations, for best stability and quick tool changes.
The possibility to apply the best insert shape to maximize strength and to apply the most suitable entering angle is dependant on how extensive a turning tool programme is. The necessary cutting edge also has to be available in the right insert form and size to both optimize the operation and to provide good tool economy. The choice between round insert and square insert with a specific geometry and nose radius can be decisive in optimizing operations – in both rough and finish turning operations.
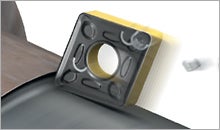
Rough turning
For rough turning of steel, insert geometry HM represents the latest tooldevelopment.
- Rough turning
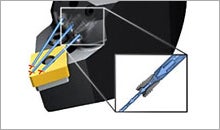
High-pressure coolant
CoroTurn® HP offer secure trouble-free production. Improved chip control in finishing of all materials and increased cutting speed and tool life in difficult materials.
- CoroTurn HP
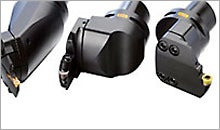
The modular SL-adapter system
With the flexible SL-system you can build your own optimized product from standard cutting units.
- CoroTurn SL modular system
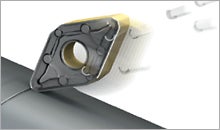
Finish turning
For finish turning, the Wiper insert technology has evolved considerably since its introduction a decade ago.
- Finish turning
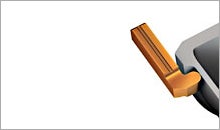
CoroCut® angled inserts
Perfectly formed for those difficult to access grooves, 90 degree angled inserts come in a variety of shapes all as standard.
No need for special tools. Blanks even available for dedicated 90, 45 degree and T-profiles.
- Parting and grooving
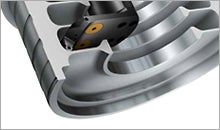
Engineered solutions
Engineered solutions can reduce the number of operations and the cutting time of power components.
- Engineered solutions
Rough turning
For rough turning of steel, insert geometry HM represents the latest tooldevelopment. It is a new design for heavy-duty double-sided inserts. HM is available to maximize strength in S-shaped inserts and to add versatility as C-shape inserts. Specifically developed for large cutting depths in steel forgings, it has very strong cutting edges and a wide chipbreaking area. As such, it can withstand the heavy variations throughout large feed-ranges of these inserts while providing durability and edge security.
When the new HM-geometry is combined with the right insert-grade of the GC4000 series, performance can be optimized to new, higher levels. Particular threats to the cutting edge, such as plastic deformation and crater wear, can be contained throughout a longer tool life. New generation steel-turning grades such as the allrounder GC4325, provides high metal removal rates through its balance of durability, predictablity and durability. GC4235 is the toughest alternative with maximum cutting edge security for the toughest conditions.
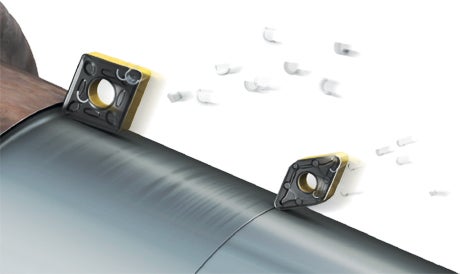
Finish turning
For finish turning, the Wiper insert technology has evolved considerably since its introduction a decade ago. This modern way of designing the insert nose-radius did away with the conventional problemratio of nose-radius-size to feed-per-revolution and its effect on surface finish. With Wiper inserts, feeds could be doubled while maintaining the same surface finish.
Wiper insert WMX is the new generation that can achieve the required finish much faster than inserts with a conventional nose radius. The main radius with multiple complimentary radii has been designed as part of a new chipbreaking geometry that has provided the insert with a much larger feed range. The WMX wiper insert can also be applied to medium roughing operations.
Compared to the previous generation of wipers, the insert also gives even better surface finish, is less prone to vibration tendencies, provides better chip control and smoother cutting action. The large central application range of WMX is complimented by a range of additional wiper geometries which can be used for optimization at very low feed/depth-of-cut values or for even larger depths of cut.
Engineered solutions
Engineered solutions can reduce the number of operations and the cutting time of power components. To machine deeper, internal chambers you need state-of-theart tooling solutions – such as those developed through Silent Tool concepts. Dampened tool blades are crucial to maintaining satisfactory performance without limitations from vibration tendencies and chip congestion. Blades longer than four times the width of the blade are designed with a patented dampened device and this allows the depth of cut to be four times greater than without dampening.
Having built-in dampening for ensuring performance at extended tool reach, these blades turn features in deep grooves often at some 20% higher cutting speeds with tool life being 50% longer.
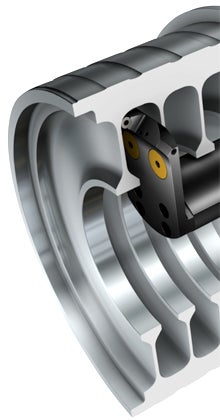