Turbine housing
Machining benefits for power casings
Creating value that benefits machine shops has been the focus for the development of modern milling cutters in the CoroMill family. The established values of the tooling have come to characterize machining capability and set benchmarks for tooling.
- milling cutter concepts to cover the absolute majority of requirements, as regards type, size and other application targeting,
- high performance through light cutting action to maximize utilization of all types of machine tools and provide stability at varying tool overhang,
- latest tool design and tool manufacturing technology, including hardened cutter bodies, improved cutter precision as well as secure, advanced insert location and clamping,
- cutter and insert geometries optimized for component materials and features, as well as providing strength, sharpness and feed rate optimization,
- continual introduction of new generations of insert grades giving real improvements in cutting data, tool life, machining security and finishing capability,
- extended range of tooth-pitches, sizes and tool-holding for cutters to optimize productivity and stability, utilize machine and provide best chip evacuation.
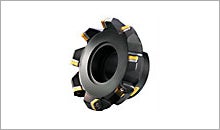
Face milling
CoroMill® 345 is excellent for most face milling operations.
- Good face milling performance
- CoroMill 345
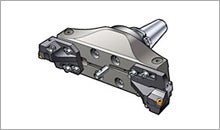
Hole making
The new rigid CoroBore® XL is an excellent choice both for roughing and finishing of large diameter bores.
- Boring tools
- Boring casings efficiently
- Component solution example (eng)
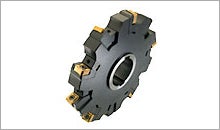
Slot milling
Machining of grooves or slots often involve milling for the roughing and semi-finishing operations. CoroMill® 331 is the first choice.
- CoroMill 331
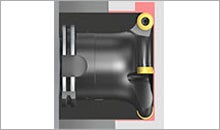
Slot milling
Turn-milling can be a productive alternative when the machine tool can rotate the work piece, see component solution example.
- Turn milling
- Component solution example (eng)
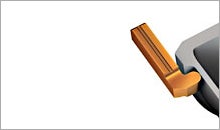
Grooving
CoroCut in combination with SL-adaptors and angle inserts makes it possible to machine complex grooving profiles.
- Parting and grooving
Good face milling performance
Good face milling performance is crucial to achieve efficient production. Milling the huge casings and housings that are part of power equipment is an area where best practice machining makes a prominent difference to through-put and manufacturing costs.
CoroMill® 345
For medium to light, general face milling of most materials, CoroMill 345 has since its introduction become a benchmark. A large programme of cutters and inserts provides it with a very broad range for optimizing operations. It has been developed for maximized use of the power and torque capability of any machine for small to medium depths of cut. Soft cutting action makes possible very high feed rates for short cutting times and eight edges per insert combines advantageous geometries for good tool economy.
The cutter body design, with unique fixed pocket and shim technology, combined with the insert grade and geometry dedication for materials, provides the possibility to apply larger feed per insert values and high cutting speeds. The extended choice of tooth pitch alternatives in the cutter makes the cutter broadly versatile in the application to various workpiece features.
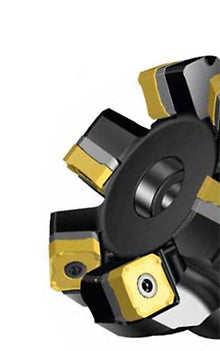
Heavy face milling
Heavy face milling operations can be divided into different categories and often a general 45-degree entering-angle cutter or even a round-insert cutter is fine for the job. But for one category of milling – typically involving large, often uneven surfaces of metal – a really rugged cutter is needed when a combination of efficient, secure machining is a priority.
CoroMill® 360
The new CoroMill 360 face mill is based on the classic 60-degree entering angle for heavy duty milling: As such it provides scope for large depths of cut, high feed capability, reasonable surface finish and balanced cutting forces. The new 360 cutter builds on decades of experience, years of development and testing in the most gruelling conditions.
The capacity for large axial depths of cut is vital to productivity in that a large, sometimes uneven mass of metal can be removed in just one pass. The chip-thinning effect of the 60-degree angle brings with it the capability of applying high feed rates, and thus shorter machining times. Inserts are seated in cassettes, that are clamped on serrated seats in the cutter, allowing quick and easy indexing in the machine. Cutter setting is unnecessary and the replaceable cassettes save the cutter body from wear or damage. The advantage of using a relatively large entering angle also allows the use of generously wide parallel lands on inserts without compromising too much on cutting depth capacity.
The advantageous distribution radially and axially of cutting forces is another feature of the 60-degree entering angle, giving stability and thus security in this category of heavy-duty machining, combined with high metal removal capability at lower power consumption.
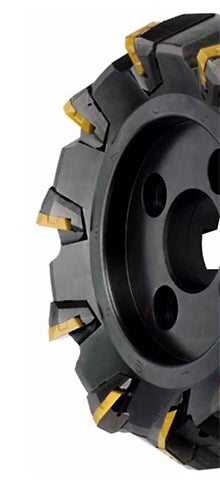
Turn milling
Turn milling of casings takes advantage of the component only needing to rotate very slowly while the milling cutter can work at maximum cutting speed. The turn milling process has enabled the efficient manufacturing of many components which would otherwise have been difficult to make and needed a number of different machining operations, in different set-ups, in different machines. The process excels when components have unsymmetrical forms and with surfaces less than 360 degrees round the part surface because of flats, cavities and obstacles.
Although this is the main advantage, other turn-mill advantages include improving chip control, lowering cutting forces, higher capability for demanding workpiece materials and coping better with interrupted cuts. Both machinery, programming and cutting tools have undergone development to make turn milling a very viable and advantageous process.
CoroMill® 345
Many of today’s standard CoroMill cutters – such as the CoroMill 345 – are ideal for turn milling and can be equipped with dedicated wiper inserts. There are tools suitable for optimizing the different configurations that keep arising as suitable for turn milling.
Sandvik Coromant has developed tools and methods to take proper control of the process parameters and thereby lift turn milling to broader use, to new levels of efficiency and to achieve better quality results. Process development and application have provided a full understanding of how the various parameters affect performance and results, providing a key to this interesting potential in manufacturing.
Turn milling rarely requires dedicated tools for roughing operations. But for optimizing finishing operations, dedicated, standard wiper indexable inserts for the CoroMill 345 should be used. A straight wiper cutting edge, as opposed to the conventional cambered one for general milling, is needed to smooth the slight surface form deviations. Round insert cutters like the CoroMill 200/300 offer the best productivity when surface flatness is not paramount, such as when roughing casings.
Application technology is needed because factors such as the positioning of the milling cutter in relation to the workpiece is critical as regards radial form accuracy, pressure on workpiece and security as well as productivity of the operation.
Optimized turn milling
The positive effects of optimized turn milling is illustrated by the method applied to machining the grooves for vane rings in turbine casing-halves at one of the world’s largest gas turbine makers. Questioning the conventional use of disc-type, side-and-face milling cutter, individual grooves were machined through face turn-milling instead. Each of the milling cutters used can be adjusted to suit each application and are simpler to use than the disc-type cutters as well as being more flexible in the machine. The method also produces grooves to better precision.
The application of turn milling was part of a productivity improvement programme with Sandvik Coromant as the process optimizer in the company’s rotor and housing machine shops. The alternative, fine-tuned process could be applied that improved productivity by 40%.

Turn milling principle
Boring casings efficiently
When machining large diameter holes in casings, tool strength for roughing and tool rigidity for finishing can be said to be two of the main attributes. These are necessary to achieve good productivity, predictable tool life and consistency within the required component tolerances and surface finish levels. In the latest boring tools these properties are combined with the flexibility to easily adapt tools to the type of operation and demands at hand.
CoroBore® XL
A new benchmark in large-diameter boring has been established by the CoroBore XL system thanks to a number of tool developments: very rigid interfaces between tool-assembly items, high-rigidity bridges with large support areas, new features for efficient setting, internal coolant supply, extended ranges of adjustability and units being of light-weight.
Rigid and reliable with versatility and straightforward setting, the modern, large boring tools for roughing and finishing have been designed to provide more consistent results at high machining rates.
The new system can be used with existing, well-proven boring concepts but also has new cutting tool units such as fine boring heads with high precision and simplified setting. Generally, inserts for fine boring should be positive and have sharp cutting edges and small nose radii to minimize cutting forces and this is fulfilled by the latest CoroTurn 107 inserts. When stability allows, Wiper inserts can optimize the relationship between surface finish and feed rate.
CoroBore® 820 XL
For rough machining, CoroBore 820 XL with adjustable cartridges ensure close axial positioning of the two cutting edges to promote a good balance in twin-edge boring or for adjustment to step-boring. Good radial adjustability is covered by slides. The most secure insert-clamping in the form of Rigid Clamping is an option for when roughing demands are high.
A range of tool bridges and extensions cover a large diameter area, where new tool holders and new Coromant Capto C10 spindle interface as well as a large cross-section of the tool bridge, make it possible to achieve high-performance machining at very large diameters.
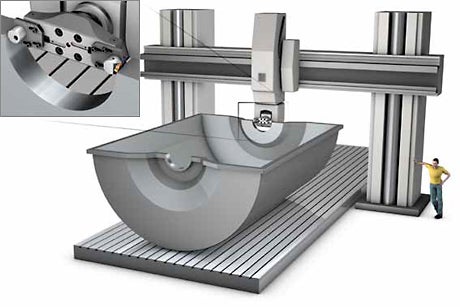
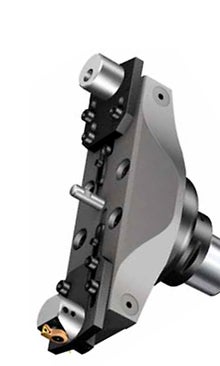
Turbine housing
Machining benefits for power casings Creating value that benefits machine shops... keyboard_arrow_right
CoroMill 345
CoroMill 345 is a cost-efficient face mill for high productivity in terms of feed... keyboard_arrow_right
Turbine blade
Blade machining moves to a new level Competitive manufacturing blades for steam... keyboard_arrow_right
Turbine blade
Blade machining moves to a new level Competitive manufacturing blades for steam... keyboard_arrow_right